Articles
Name | Author | |
---|---|---|
The Next Big Shift in Airline MRO Analytics | Baiju Jacob, Director and Global Head of MRO Practice, and Manuel Fernandes, Digital Subject Matter Expert & Senior Consultant, MRO Practice, Hexaware Technologies | View article |
Case Study: Making everything work better | John Hancock, Editor, Aircraft IT | View article |
Case Study: Controlling Aircraft Tooling using RFID Technology | Jakob Heegaard, Director IT, Jet Time | View article |
Case Study: Innovations in Aircraft Maintenance at easyJet | Gareth Thomas, Application Manager, easyJet | View article |
Case Study: Using an M&E IT solution to manage CAMO operations | Yuliya Kornyeva, Senior Project Manager, FL Technics | View article |
Case Study: Innovations in Aircraft Maintenance at easyJet
Author: Gareth Thomas, Application Manager, easyJet
SubscribeInnovations in Aircraft Maintenance at easyJet
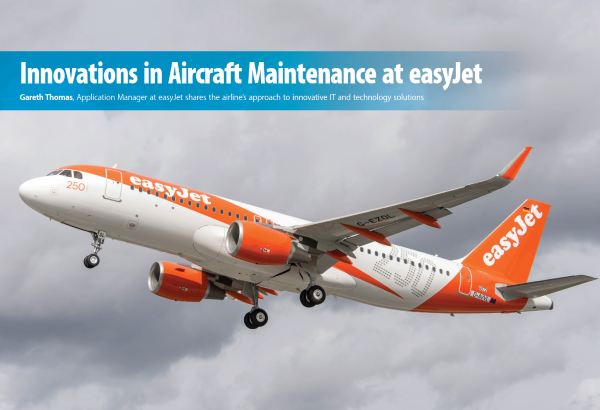
Gareth Thomas, Application Manager at easyJet shares the airline’s approach to innovative IT and technology solutions
easyJet
Before we look at innovation in aircraft maintenance, it will be useful to set the scene with a brief introduction about the airline. easyJet is a European airline with over 250 aircraft and we carry over 70 million passengers a year on more than 800 routes.
Aircraft are a key part of any airline. In 2003 we took delivery of easyJet’s first A319 aircraft with CFM 56 engines and moved to increase capacity in 2009 with the A320. By 2013, easyJet wanted better fuel efficiency so opted for A320s with Sharklets and began a retro-fit program to install them on some of the existing fleet. The recent delivery of two 186 seat configuration A320s has further increased capacity and, in 2017, the airline will take delivery of its first A320 NEO with Leap 1-A engines.
The task in engineering and maintenance is to find the most innovative way to keep the ever-growing fleet maintained whilst sustaining the same levels of overheads and headcount per aircraft. Our choice of NEO aircraft will include the Leap 1-A engines that will generate large quantities of live data; however, we do have to find the best way to collate that data and use it to our advantage.
IT SYSTEMS CURRENTLY IN USE
easyJet relies on some key IT systems to underpin the engineering and maintenance operation.
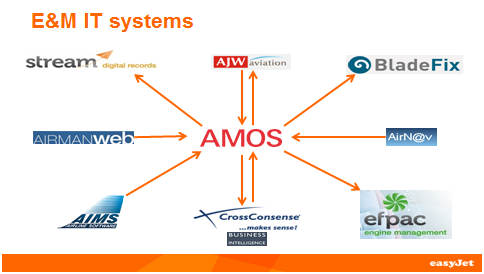
Figure 1
At the heart of the system is AMOS (figure 1). Everything we do transitions or transacts with AMOS. We use Stream as our current technical records storage system for records verification processes which has helped easyJet to move from paper records verification to digital record verification with a daily task to compare all completed paper records, work packages and tech logs with the digital form stored within AMOS. A direct link to AJ Walter, the logistics provider and their quantum system, allows full integration of logistics processes. BladeFix is another useful system and from Airbus Software easyJet has AirmanWeb for tracking defects and AirNav for maintenance manuals; they are both integrated within AMOS with quick shortcut links to work orders and task cards. EFPAC is our engine management and optimized planning tool plus AIMS for the fleet schedules and efficient maintenance planning within AMOS. In addition we use CrossConsense which also hosts easyJet’s AMOS service and provides business intelligence services.
INNOVATIONS ALREADY IN PLACE
Innovation is an endless quest and innovation is doing new things. Aviation should be in the forefront of innovation; we’re part of a dynamic industry so finding ways to work smarter will help minimize the impact when we hit highs or lows. We’re always looking for improvements in the ways we do things and, if an innovative idea can save time and money why not improve a process even where you don’t actually think you currently have a problem?
We’ve already delivered a lot of innovations at easyJet over the last few years; here are a few products and systems that are currently active in the way we work. In February 2010 we insourced our Technical Services Department and went live with version 9.10 of AMOS which was a huge step change for easyJet. We couldn’t use the whole system at once so when problems occurred we began to ‘lean-out’ our processes and integrate them more with AMOS.
A leaner modification approval process
The first step was to move the manual modification approval process (MAP). At the time, for management to approve modifications, the airline had a paper process which relied on engineering staff to print a piece of paper and walk it round every single Head within engineering to get their signature: it could take up to 180 days. The piece of paper then had to be taken to a modification approval meeting where everybody would again sit round to give their final approval. We looked at what AMOS had available and found a Cost Benefit Analysis tool which would allow us to email approval requests out to management. Now, thanks to this application and scrapping that costly meeting, we have reduced our MAP approval time to 18 days.
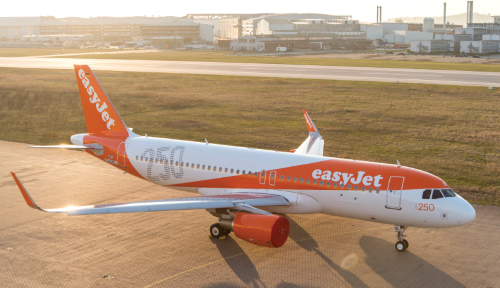
Better reliability investigations
We next looked at our reliability investigations: we used to do all correspondence by email chains. Fleet engineers had to send emails to both the reliability engineer and management separately on what was going on when, say, a pump failed. It was time consuming and it was complicated. Again, we looked to AMOS where there is a reliability investigation application called Technical Case Manager. Now, we manage all of our reliability investigations directly in AMOS for everyone to see and share the progress. We don’t have to prompt management plus they and the reliability engineers can all have the latest information on demand.
Improved shift management
There was also a problem tracking shift staff with easyJet’s HR systems and HR approached Engineering to see whether we might have something they could use. We found that AMOS had an application that could track shift patterns and, with RFID badges from ASD, we can now export that information directly to our HR systems for effective tracking.
Fan blades to balance any engine
Overall, we felt we were ‘leaning-out’ our processes and making progress and so started to look ahead, to get innovative. We realized there was a huge manual process identifying the best replacement options when a fan blade was defective. In light of that, we started working on a system that could deliver real-time solutions for fan blade replacements that kept the engine balanced; and that led us to BladeFix. It’s now possible to select any engine within the easyJet fleet and BladeFix will use data from AMOS to map the current fitments. Tell it which fan blade is defective and BladeFix will identify which fan blade within stock anywhere in the network is the optimum fit to balance that engine. This reduces the amount of time to do balance calculations for power plant engineers and it’s easy to locate and ship the required spares within AMOS.
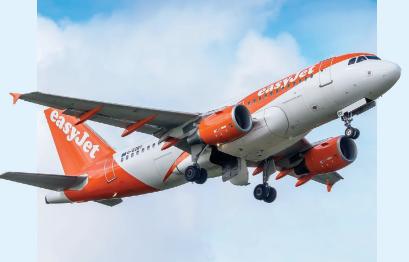
Reliable data transfer and software updates
A couple of years ago we ran into a problem when it became no longer possible to install data on our aircraft using floppy discs: that was outdated technology. With the old system, software had to be written to a disc in Luton and then sent by FedEx to the line stations. We had to hope that they would work when the engineer used them on the aircraft but, in practice, nine times out of ten there were issues. This could cause huge problems if the software was out of date. So, we looked to see what alternative was available and we found a small orange box (we didn’t pick it only for the color!), the MBS Mini portable data loader (PDL) which is now used to update all required aircraft software in a seamless manner. But we first had to remove all the floppy disc drives from the aircraft and install connector ports. That this has now been carried out across the entire fleet shows how much we believe in this product. The process now starts with the fleet engineers in Luton deciding which software to load, which is then moved to the MBS servers and downloaded onto the Mini PDLs at each line station. Using this small box, we can be in full and accurate control of our software.
Tool management… greater efficiency and enhanced safety
There is an inherent safety risk with personnel and uncontrolled tooling and the risk of a mismatch of different tooling being used on the aircraft which we always keep front of mind. To address this issue at easyJet, we found another orange box but this time a lot larger and from Snap-on (figure 2). It might look like a standard tool box with a screen fixed to the top of it but it is a lot more than that.
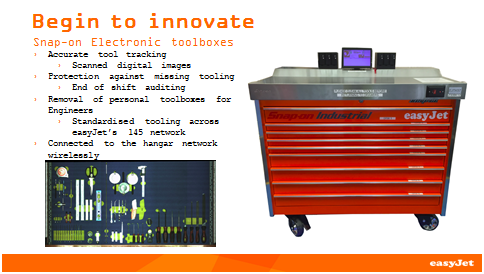
Figure 2
This toolbox scans images of every drawer and allocates the tools to the user who removed them. When the tools are replaced in the toolbox, it again scans the drawer to make sure that the correct tool has been replaced and has been replaced to the correct part of the toolbox and, where either is incorrect, it will notify the engineer. The toolbox also allows the shift supervisor to perform a full tool audit prior to the aircraft being released back into service. It will inform him who has any missing tools so they can be located and returned. The toolbox is also wireless, so can be taken to the aircraft and/or moved around the hangar while remaining connected to the easyJet network and servers.
Towards a paperless cockpit
A couple of years ago, easyJet wanted to make the cockpit as paper free as possible so decided to install Panasonic Toughpads in the cockpits as the airline’s electronic flight bags (EFBs). Whilst the main purpose is to provide the flight crew with all of the documentation and systems it also offered a great opportunity to load the entire AirNav suite. It also allows for full aircraft maintenance manuals on the aircraft during defect rectification which is a huge time saver for the engineer to not have to keep going between the aircraft and the computer back in the base office.
INNOVATIONS FOR THE FUTURE
That’s a brief overview of the type of thing that is already running in easyJet Engineering. Now, without disclosing all the details of projects on which we are currently working, here is an idea of some of the things we are working on.
Paperless and connected engineers
A major step in what we’re trying to achieve in the not too distant future is to connect engineers to the IT systems. We still rely too much on paper to carry our aircraft maintenance so when we upgrade our AMOS from version 9.80 to version 10.90, we’re also going to release electronic signatures to our scheduled work packages and the signature will be fully set up and controlled within AMOS so we won’t need any extra hardware or software. We’ve worked hard with Swiss-AS on making this a reality and it’s something of which we’re really proud. It will be a much more efficient process for engineers rather than having to enter the same information in both the paper records and the MRO systems. They’ll be able to seamlessly sign the documents within AMOS and they’ll be automatically sent to the technical records storage system. We estimate that introducing this process will save over one million pieces of paper a year.
As well as improving process efficiency, it will also deliver cost savings; not to mention the fact that we can then move to automation of records verification. We’re currently in the process of finalizing this approach and have already had discussions with the aviation authorities about using it. Once there are improved systems for our engineers to work with in the office, we then need to give them the option to take the maintenance systems to the aircraft. Having a device around the aircraft, wirelessly connected to the network will offer huge efficiencies across the board. As well as taking AMOS to the aircraft to complete their work, the engineers will be able to stay in constant contact with Maintenance Control and they can have RFID scanning capability at their fingertips. This will unlock the potential for engineers to be fully connected to easyJet networks.
Mobile opportunities
The next step will be to give the engineers mobile optimized versions of their systems. This means AMOS Mobile which will be introduced with AMOS 11. With our electronic TechLog, this step change will make it more efficient to do data logging and will free up a lot more time for what they actually have to do – working on the aircraft. We are also analyzing a few ideas at easyJet to introduce along with our mobile engineering device.
Drones for inspection
Something cool as well as useful is drones, impressive pieces of technology that are useful to our industry. What if we can get drones to perform aircraft inspections? Not only can they get to high parts of the aircraft without lifting equipment or safety harnesses, they can also use lasers to scan the entire skin section for dent and buckle imaging which could immensely improve the recovery time for an aircraft with damage. The drone idea is still at proof of concept stage but is something that we are keen on at easyJet Engineering as part of the future of aircraft maintenance.
Predictive maintenance
The aviation industry has always waited for failures before going out to fix them. And then we’ve waited for more to occur before we analyze them and put preventative actions in place; it’s called a reliability program. But what if we could constantly monitor an entire fleet of aircraft to identify which systems or components are at risk of imminent failure and then take them off before we have a grounded aircraft at a remote station? The use of predictive systems could revolutionize the way we perform scheduled maintenance, especially when it comes to efficiencies in manpower, spares, etc. There are already systems available like trend monitoring. But trend monitoring is just a key piece of the puzzle. It’s also important to know current aircraft parameters, previous defects and scheduled maintenance history to name a few. However, predicting the future is a puzzle where you’ll never fully know all the pieces, it will just keep growing and that’s good because it means that we’ll continue to get increasingly accurate.
AND FINALLY…
To close, I’d like to return to the heart of easyJet’s engineering and maintenance systems, AMOS. After the next upgrade we will be already looking to the future with a move to AMOS 11 as early as the second quarter of 2017 as there are many improvements within that system that will help streamline and improve our processes. For instance, we’ve worked closely with Swiss-AS to help them develop a self-picking module which will deliver optimized consumption of consumable material at the aircraft with one click, a barcode scan and that’s it, the material will be booked to the aircraft.
We also plan to be using the new software management modules where, along with our MBS devices we will be able to create, organize and track aircraft software even more efficiently. It will also offer full visibility of all users of AMOS, including the pilot briefing sheets.
Finally, there are a couple of new logistics modules that, although released within version 10 of AMOS as optional, we have decided to save taking those improvements until version 11. The benefits of these modules are considerable – improved shipment tracking, better dangerous good handling and more accurate consumables tracking which will help change and improve the way we do logistics and supply chain within AMOS.
In summary, at easyJet we’re passionate about the way we perform aircraft maintenance. The important thing about innovation is… people have been talking about it for decades and will still be talking about it long into the future. That endless quest to improve is what drives us as engineers and innovators.
Contributor’s Details
Gareth Thomas
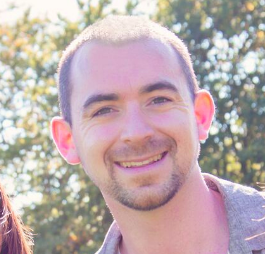
Gareth is an experienced Systems Administrator with 10 years of working within both MRO’s and Airlines. He has a broad knowledge of lean processes, Engineering & Maintenance and IT System development. Having been with easyJet for six years, he is currently working to deliver a number of innovative projects within Engineering and Maintenance, but is key to the airlines AMOS upgrade and, along with it, implementing Electronic Signatures for Aircraft Maintenance.
easyJet
As Europe’s leading airline, easyJet offers a combination of the best route network connecting Europe’s primary airports, with great value fares and friendly service. easyJet flies on more of Europe’s most popular routes than any other airline and carries over 68 million passengers annually, of which around 12 million are travelling on business. The airline flies over 240 aircraft on more than 780 routes to over 130 airports across 32 countries. More than 300 million Europeans live within one hour’s drive of an easyJet airport.
Comments (0)
There are currently no comments about this article.
To post a comment, please login or subscribe.