Articles
Name | Author | |
---|---|---|
CASE STUDY: SAS’s Journey to paperless maintenance operations | Yuliya Kornyeva, Maintenance Data Analyst, Dlovan Sandi, ELB Digital Service Owner, SAS - Scandinavian Airlines and Rob Saunders, Director of Business Development of the Electronic Log Book, Ultramain Systems | View article |
WHITE PAPER: Leveraging data for digital aviation success | Sander de Bree, Founder & CEO, EXSYN Aviation Solutions | View article |
CASE STUDY: Digital transformation at TUI | Niklas Kropp, Programme & Projects Manager E&M, TUI Airlines | View article |
CASE STUDY: Getting the best from new engines at Condor | Nicolas Schneider, AMOS Administrator, Condor and Dr. Almut von Schneidemesser, Senior Manager for Aircraft Communications IT at Condor | View article |
WHITE PAPER: Lufthansa Systems develops a digital twin concept for aviation | Priscila Monroy, Junior Consultant at Lufthansa Systems | View article |
CASE STUDY: Achieving IT process continuity in Air France Industries and KLM Engineering & Maintenance | Anne-Laure Propper, Project Manager & Olivier Demède IFS Maintenix Product Owner, both Air France Industries KLM Engineering; and Arjan Otten, Project Engineer Maintenance Programs, KLM Royal Dutch Airlines | View article |
WHITE PAPER: Lufthansa Systems develops a digital twin concept for aviation
Author: Priscila Monroy, Junior Consultant at Lufthansa Systems
SubscribePriscila Monroy, Junior Consultant at Lufthansa Systems shares the development process that created this exciting new technology.
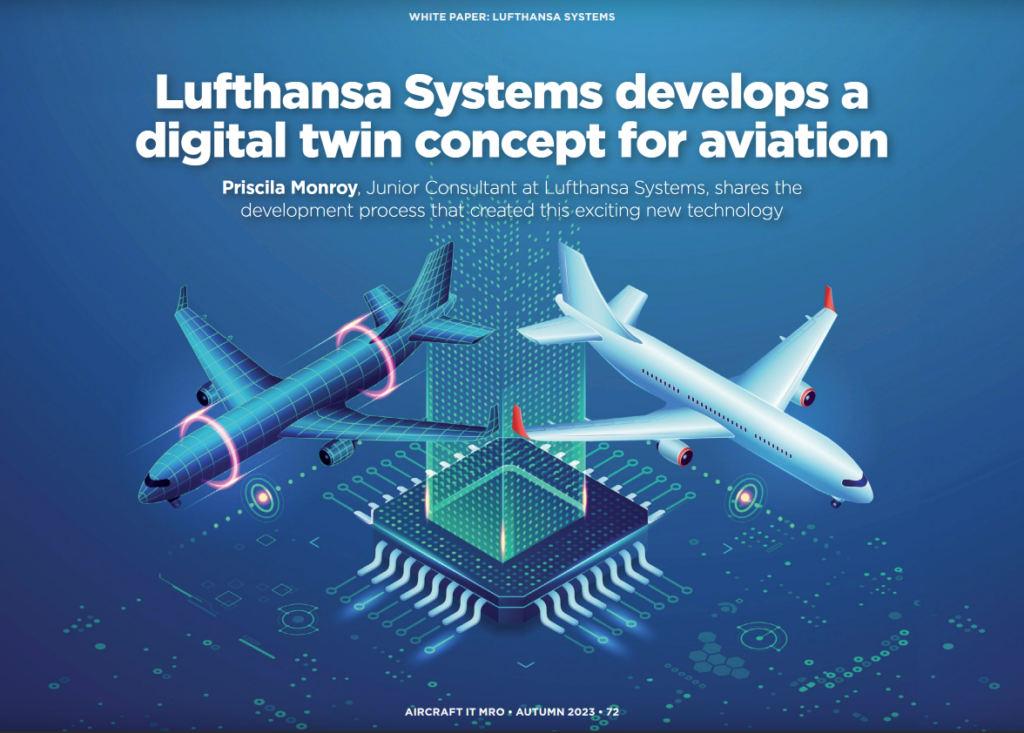
Before we dive into the details of our development, it will be useful for readers to set-out what a digital twin is and what can be done by using it.
A digital twin is a digital representation of any physical object or system using real-time data or historical data. With this data, you are able to run simulations and with these simulations, you can, for example, simulate different circumstances or environments. Based on that, you will get results either as reports or dashboards or any business organization tool and, with these results, the stakeholders are able to make informed decisions about what would be the physical performance of the physical object in a variety of circumstances or environments.
WHY A DIGITAL TWIN?
There is currently a lot of technology around with emerging IT tools that are helping to understand how different systems behave. Based on that, Lufthansa Systems had the idea to develop a study focusing on how can we, as the aviation industry, use a digital twin to enhance time management, and improve the decision-making processes within the industry. That was how the idea came about. We realized the benefit that such a tool could offer by helping to improve operations and fleet optimization, as well as helping to predict the flight routes that would to help reduce the carbon footprint of the organization. So, with this in mind, we started to form the idea and consider the challenges that might be encountered while developing this concept or system (Figure 1).
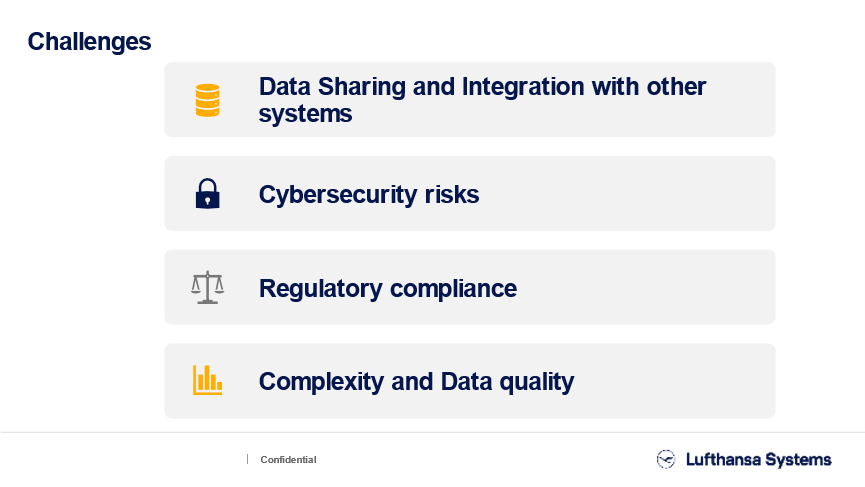
Figure 1
We realized that it would be a really complex system, therefore qualified personnel were needed to be able to develop the tool. Then there is the integration with other systems which is of great importance because the idea of this digital twin is with data transmission, being able to connect with existing software in aviation organisations: that is really important. There are also cyber-security risks to be considered and, for that, we evaluated the safety and security regulations that apply to these technologies.
We selected the digital twin tool because it works with real-time data as well as historical data. There are a lot of different tools that help predict and simulate different, for example, flight plans or flight routes, but there wasn’t a single tool that would allow us to bring all of those capabilities together or, for example, to be able to simulate theoretical things to improve the operations, not just what is happening right now but could we predict or forecast what would be the effect of different decisions and to have a better analysis.
The Lufthansa Systems Digital Twin Concept is the one that will enable us to do this; to not only work with the real-time data that is available in most organizations but also to run theoretical simulations in order to improve operations.
We started to build this study with the Digital Twins in mind, we did not consider other technologies, but during the study, we did consider different architectures until we found one that best suited the objectives that we wanted to achieve.
DEVELOPMENT HISTORY OF THE DIGITAL TWIN
At first, we did all of the background checks: plus we did research on how this tool has been used in other industries and, based on that, we built a use case specifically for the aviation industry and decided that it can be used for maintenance, for airline operations, CAMO operations, for research, design and manufacturing (figure 2).
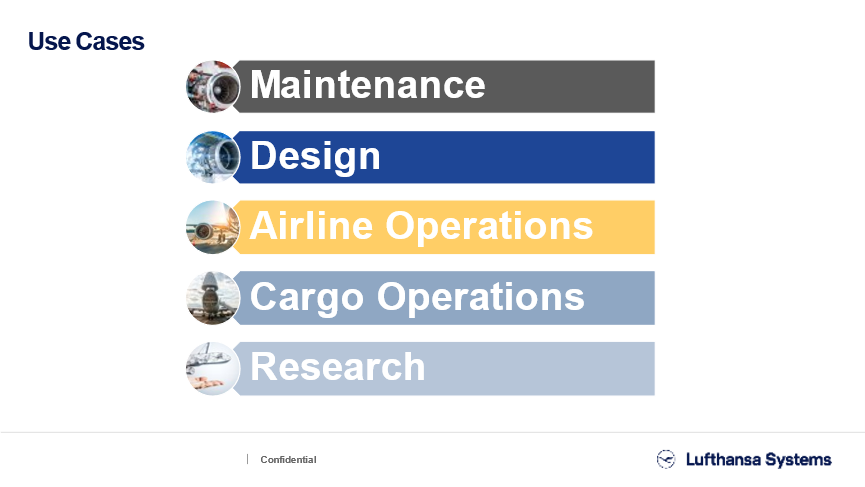
Figure 2
When we had built these use cases, we were able to select experts in the industry for maintenance, design, operations, cargo carriers and research. We got together with them and ran workshops. Also, we sent out surveys to gather from them all the information we could to be able to develop the digital twin concept and to identify potential problems. We wanted to determine what would be the right development strategy for the tool and to identify whether this tool would be something that they needed and could implement in their operations. After all of these activities, we got together to produce a summarized overview of all the information we had gathered before continuing to do the research to build the architecture, taking into account the comments that they had given us.
Our research suggested that the main areas where this would be used in aviation would be engineering, maintenance and design but this can also be implemented for management, to predict cost and another important use case we saw is for environmental sustainability. This is a great tool to apply to reducing an organization’s carbon footprint.
The digital twin that we have developed uses machine learning (ML) and algorithms and modelling tools, such as 3D models, to be able to have a digital replica of the object in question and also computer models with which to work.
HOW THE DIGITAL TWIN WORKS AND WHAT IT CAN DO
In figure 3, you can see graphically the working flow of the system.
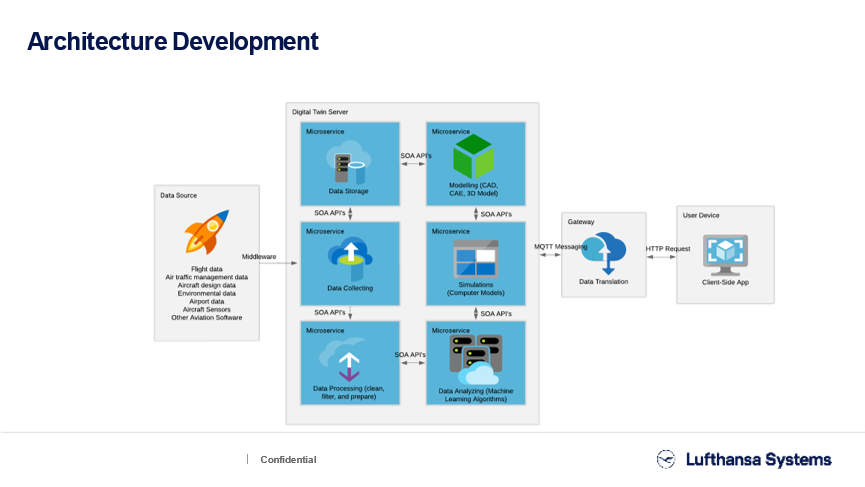
Figure 3
The idea is that we will have a Client-Side App with a user interface and which can either run on the web or as an application in the user’s computer. Through this, we will be able to send a request. For example, if we want to see how this system is going to behave in particular conditions, we can enter the inputs appropriate to what we want. And then, the information goes through the gateway because, if it’s running on the web, normally the communication protocol is through HTTP and we need the gateway which does the translation of the data to MQTT (Message Queuing Telemetry Transport) messaging.
When this has been done, the request is in the system where there are different micro-services each of which will be in charge of doing a specific task as the names on each them suggest. For instance, the middle one in the left column collects data and, as already mentioned, that can be real-time data from the aircraft sensors or it can come from a database which includes all the historical data. For example, in maintenance there can be all of the records of maintenance events that an aircraft has been through. So, there can be external sources such as aircraft sensors or another system that the organization is using.
When we have this system, to be able to collect the data, because that is something external to the digital twin, the Middleware will be needed to be able to communicate with the system and, when we have all the data collected, then this microservice will send the information to the other microservices. This one is going to be in charge of processing the data. Then the information will be sent to the microservice in charge of analyzing the data; it’s mainly going to run all of the machine algorithms before the information arrives to the microservice in charge of running the simulations. There can even be the microservice where that 3D model can be made of either the aircraft or of a specific component. Then, the results will be generated and sent back to the user interface.
Basically, the idea is that there are different services because this ensures that, if something fails, it doesn’t affect the entire system, can isolated. It also allows for the system to have scalability which means that if we want to escalate any specific system, it won’t be necessary to stop the entire digital twin from working in order to make the escalation.
One way to think of this is to imagine you have gone to a restaurant where you and the waitress speak the same language. That is what is happening in the case of this architecture with the user interface and the digital twin. you make your request to the waitress; it gets sent to the kitchen and you get your food. But then there are the external sources already explained which can be likened to if you go to the restaurant but you don’t speak the same language as the waitress, in which case, you’ll need a translator. That is what the Middleware does; translates that externally sourced data so that it can be used in the digital twin.
APPLICATION OF A DIGITAL TWIN IN ENGINEERING & MAINTENANCE
In maintenance, the digital twin can be used to plan or organize preventive, predictive and scheduled maintenance. Most of all, it can be used for proactive maintenance and be applied not only to prevent problems but to be proactive and detect issues before they even happen. It does that by running the simulations of any case or scenario the user wants then put that in to the twin and the results will be available.
Imagine two aircraft, one that is mainly flying over the ocean and the other one mainly flying over the land. The components and systems, though the same in both aircraft, will react differently in the two different environments. If flying over the ocean, maybe the salt with have more impact on an engine than when flying over the desert. All of that can be simulated plus weather conditions to simulate that, if this aircraft is always over the ocean, some things will fail sooner than with the other aircraft that is not flying over the ocean. These theoretical situations can be simulated to understand how the system is going to behave. The information can come from either a data base which would just need middleware to communicate the information or it can also be instructed from real-time data from the aircraft’s sensors as already mentioned above.
We also need to mention the impact on sustainability and the flight efficiency. Nowadays, all airlines need to focus on sustainability and need to look at their impact on and how they can help to save the environment. Now the digital twin can help save on emissions and save the environment.
Standard Duty Cycles
We had a talk about standard duty cycles in the context that this tool will help predict more accurate wear times because, if one thing needs to be replaced, that could be predicted well ahead of time. The main challenge that we’re going to have in this case is for the authorities to agree that the prediction that the digital twin is making is accurate. For instance, the digital twin might say that a specific component needs to be changed in two weeks but the documentations says that it should be changed in one month. Today, replacements are based on maintenance programs that, in this case, say that it’s one month. The challenge will be to get the regulatory authorities to agree that the digital twin’s predictions are going to be valid and, instead of waiting one month to change the component, it can be changed in, say, two weeks. This will help to avoid an AOG situation.
The digital twin will always be running at the same time as the physical aircraft and will give the airline alerts. But it will also help airlines to package maintenance to not have the aircraft downtime too long. Instead, if the change can be predicted then a single maintenance package can be planned for instead of having multiple down times. The digital twin can also have a specific use case for the financial aspect of the business and supporting management in the organization.
LIFECYCLE MANAGEMENT?
The digital twin can predict the whole life of certain components (figure 4)
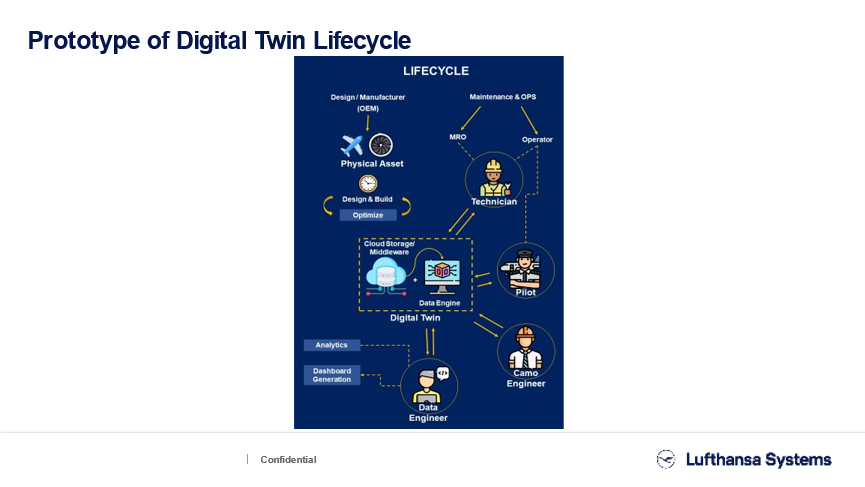
Figure 4
This will be particularly useful where an aircraft might be returned to the lessor and re-assigned to another airline or operator, to be adjusted to take account of the new conditions in which it will be working. It should even be possible to adjust charges as long as each aircraft can have its own digital twin. If the lessor is interested or a new purchaser of the aircraft is interested, they can acquire the tool with all of the information.
This is how we have developed the Digital Twin at Lufthansa Systems and we believe that it will have a huge impact on the management of, as well as the efficient planning for and operation of aircraft.
The story of how a revolutionary new technology was developed and what it will do for users.
Contributor’s Details
Priscila Monroy
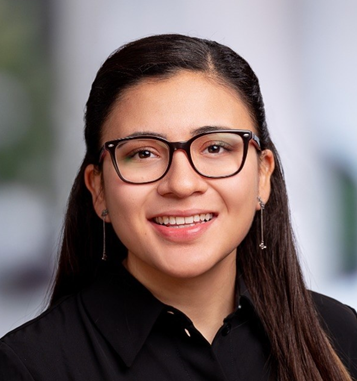
Priscila is a Junior Consultant at Lufthansa Systems with a Bachelor’s in Aeronautical Engineering, MBA studies, and a Master’s in Mechatronics Engineering. Specializing in Aircraft Maintenance, Air Traffic Management, and Aircraft Fuel Supply, her diverse skills drive innovation in the aviation industry. Priscila’s is used to collaborative working, adapting to new technologies, and problem-solving. She is committed to enhancing organizational functioning, sustainability, development, innovation and learning to create a better environment.
Lufthansa Systems
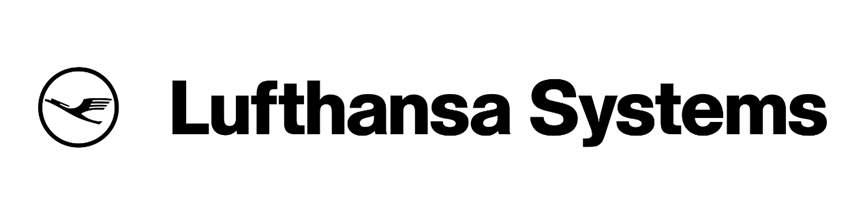
The company offers its more than 350 airline customers an extensive range of successful and in many cases market-leading products for the aviation industry. The innovative IT products and services in this portfolio offer customers a wide range of economic benefits while also contributing to improving efficiency and competitiveness. In addition, Lufthansa Systems also supports its customers both within and outside the Lufthansa Group with consulting services and the experience it has gained in projects for airlines of every size and business model.
Comments (0)
There are currently no comments about this article.
To post a comment, please login or subscribe.