Articles
Name | Author | |
---|---|---|
CASE STUDY: SAS’s Journey to paperless maintenance operations | Yuliya Kornyeva, Maintenance Data Analyst, Dlovan Sandi, ELB Digital Service Owner, SAS - Scandinavian Airlines and Rob Saunders, Director of Business Development of the Electronic Log Book, Ultramain Systems | View article |
WHITE PAPER: Leveraging data for digital aviation success | Sander de Bree, Founder & CEO, EXSYN Aviation Solutions | View article |
CASE STUDY: Digital transformation at TUI | Niklas Kropp, Programme & Projects Manager E&M, TUI Airlines | View article |
CASE STUDY: Getting the best from new engines at Condor | Nicolas Schneider, AMOS Administrator, Condor and Dr. Almut von Schneidemesser, Senior Manager for Aircraft Communications IT at Condor | View article |
WHITE PAPER: Lufthansa Systems develops a digital twin concept for aviation | Priscila Monroy, Junior Consultant at Lufthansa Systems | View article |
CASE STUDY: Achieving IT process continuity in Air France Industries and KLM Engineering & Maintenance | Anne-Laure Propper, Project Manager & Olivier Demède IFS Maintenix Product Owner, both Air France Industries KLM Engineering; and Arjan Otten, Project Engineer Maintenance Programs, KLM Royal Dutch Airlines | View article |
CASE STUDY: Digital transformation at TUI
Author: Niklas Kropp, Programme & Projects Manager E&M, TUI Airlines
SubscribeNiklas Kropp, Programme & Projects Manager E&M at TUI Airline, describes their journey to a fully digital system in a data driven ecosystem
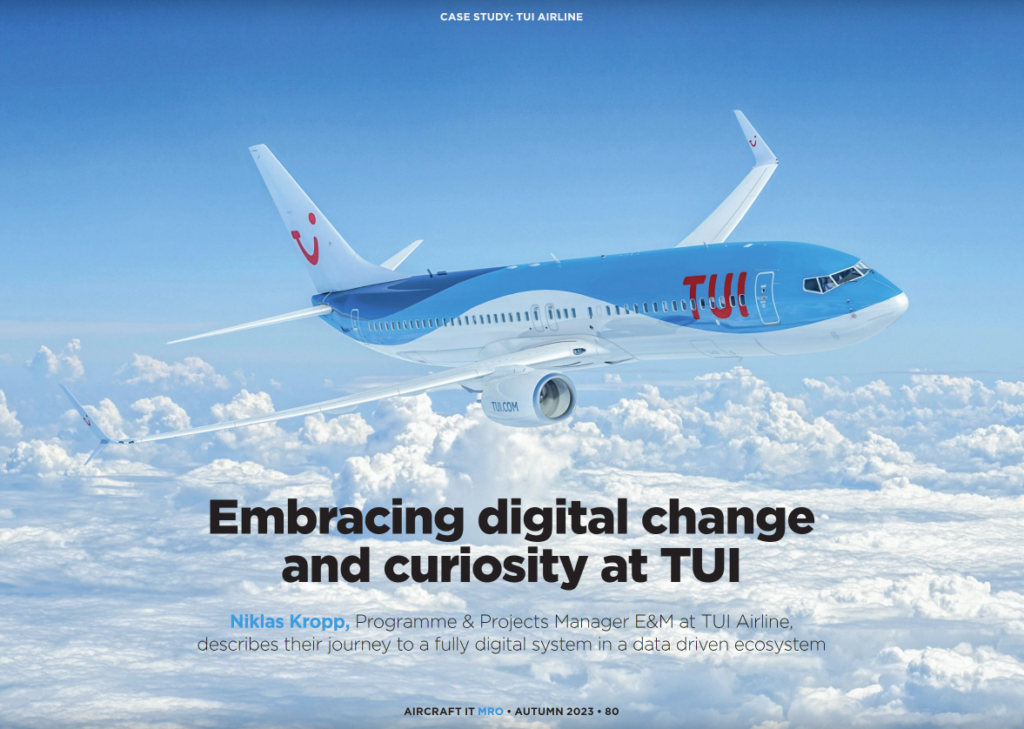
Most of this case study will be about the exciting digital transformation at TUI Airline and how we managed to partner with the right software solution provider to make that happen. But first, a look at the subject of the case study, TUI Airline.
TUI AIRLINE
TUI Airline is part of the TUI Group, one of the world’s leading tourism groups (figure 1).
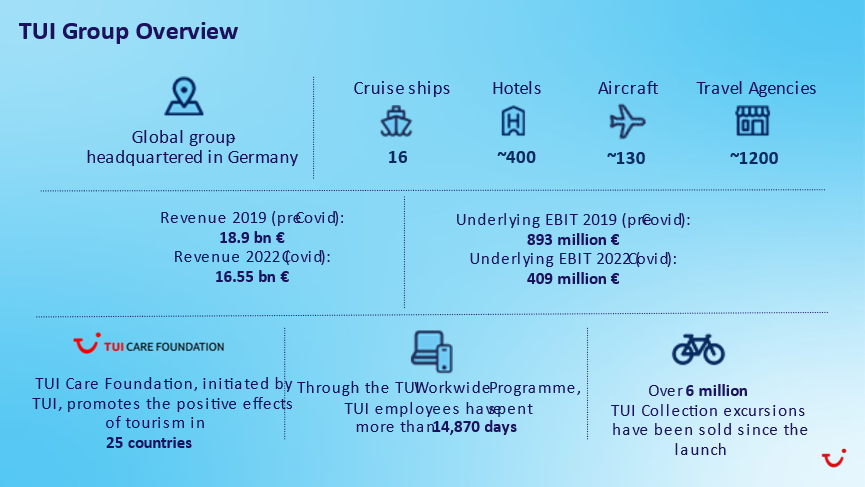
Figure 1
As the leading global tourism group, TUI is headquartered in Hannover, Germany and is much more than just an airline. As a vertically-integrated tourism business TUI focusses to deliver ‘Excellence in Leisure Experiences’ on its cruise ships, aircraft, hotels & resorts and excursions. With it’s TUI Care Foundation, TUI reinforces the positive social and economic contributions of tourism. Looking at the airline, our ambition is to ‘create happy holidays with every flight’.
The TUI Airline fleet composes of more than 130 aircraft with 19x Boeing 787, 2x 767, 3x Embraer E2 and its back-bone fleet of more than 100 Boeing 737NG/MAX. The majority of aircraft are based in the UK with further AOCs operated in Belgium, the Netherlands, Sweden as well as Germany. Being part of a tourism group, the airline serves the tour operator’s demand and operates to various favorite holidaymakers destinations across Europe. To deliver cost-efficiencies and meet our ambitious sustainability targets our fleet is undergoing a constant renewal. TUI Airline’s sustainability practices have been recognized in various rankings, including TUI Airline’s reduced environmental footprint in recent years (see figure 2).
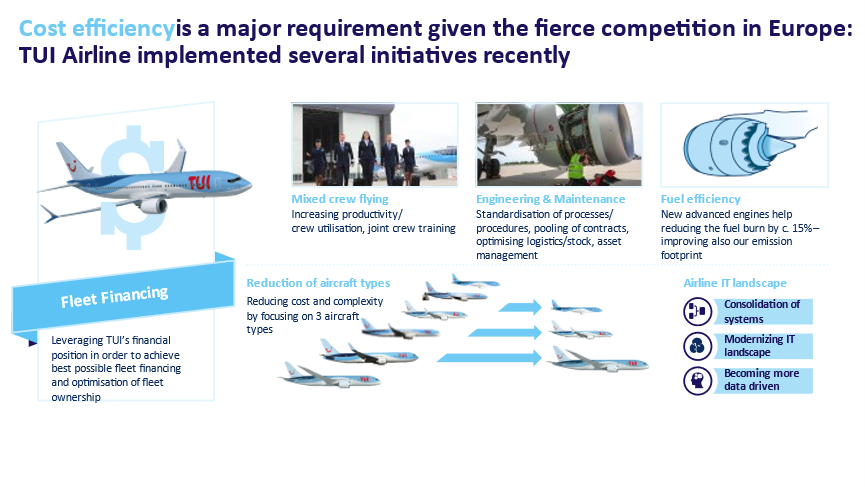
Figure 2
Looking into our strategy, it is important for TUI Airline, that, creating happy holidays with every flight remains at the heart of our business operations.To deliver smooth business operations, working together with partners, is a crucial driver to deliver operational excellence for he airline in the long-term.
Bearing that determination for cost-efficiency in mind as an airline in a highly competitive market space, we are looking at a rationalization of aircraft types in the fleet; to go from multiple aircraft types to just three types. In a similar vein, our airline IT landscape not only in Engineering & Maintenance has seen further consolidations, but multiple operating and finance systems in TUI are subject to further consolidation and standardization, aiming to become a lot more data driven.
For the Engineering & Maintenance division this means mirroring the Digital Tech Ops Ecosystem. The business development and fleet systems team focuses on transitioning from a linear roadmap into an ecosystem approach (figure 3), based on cross-functional communication and collaboration. In order to adapt to an ever changing operating environment, we sought a partner who would be able to cope with constant change and provide short development cycles. By combining AMOS, Flydocs and Aviatar’s expertise, we aim to deliver significant, tangible digital change to TUI Airline.
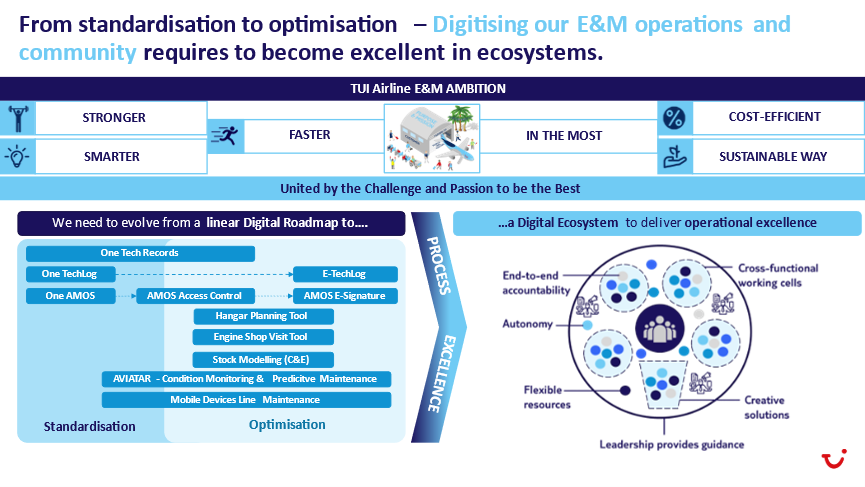
Figure 3
To realize efficient business operations, harmonizing and optimizing processes, systems and ways of working has been a key enabler. In recent years we have heavily invested into standardizing crucial business processes within TUI Airline E&M, including to implement one AMOS, one MOCC, one TechLog or one Technical Records System. Bringing systems and processes together was only possible due to one international TUI Airline E&M Team in the first place.
THE MISSION TO BECOME DIGITAL
Looking into Engineering and Maintenance in more detail, we have embedded the following ambition into our DNA: ‘Become Stronger, Smarter and Faster in the most cost-efficient and sustainable way (figure 4).
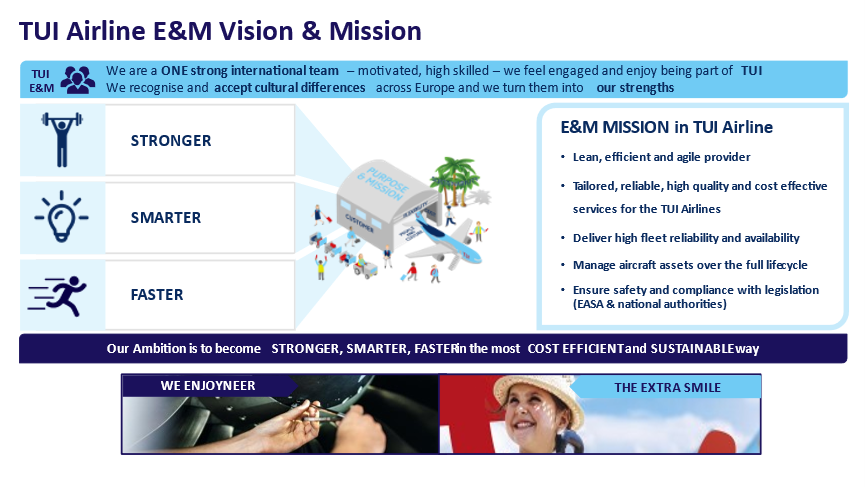
Figure 4
While we strive to deliver a reliable and safe operation, we aim to act as ‘Enjoyneers’. We want to inspire colleagues to try out new things and enjoy working within TUI Airline and its strategic partners. In the end, this is how we can contribute within Engineering & Maintenance to create happy customers with every flight. We call that ‘Enjoyneering’ – seeing the joy of customers while we work every day with the latest technology and the latest aircraft types unites us in our passion to be the best. And it is not a secret that a user friendly fleet systems’ landscape is key in creating these happy Enjoyneers in the day-to-day operation.
Looking into the TUI Airline Engineering & Maintenance footprint (figure 5) we operate over 20 Line Maintenance stations, two Base Maintenance facilities in LTN & BRU being critical to our twin-operation and five main office locations which are brought to life by over one thousand employees in Engineering and Maintenance.
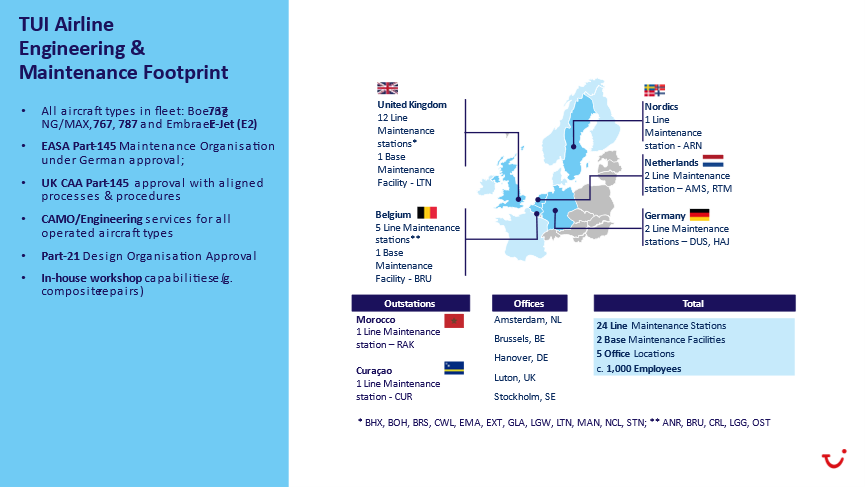
Figure 5
The dispersed landscape of the E&M operation emphasizes why the need for standardization in the last years has been crucial. Coming from five standalone airlines, it has been our objective to harmonize processes wherever possible while enabling more flexibility in deploying the fleet across the airlines to cope with changes in demand across TUI’s pan-European network. To come to one system, one process, one landscape instead of a previously highly staggered landscape, is one key factor that has driven continuous improvement in the past and continues to do so today.
Another critical success factor is the data availability and data handling, which is key to any digital transformation. How do we collect data, how do we use data in a value-adding way? As aircraft become smarter, increasing the data literacy is a core asset to remain competitve and optimize our decision-making processes. This requires investments into people skills and also to learn from industries that are more advanced in utilizing the power of data. While aiming to develop a data powerhouse it is crucial to keep the unique challenges of accessing and using aviation data (e.g. full flight data, OEM performance data). It requires the right combination of curiousity and caution to re-think how we approach our data use.
THE DIGITAL TECH OPS ECOSYSTEM
Keeping the challenges around the data accessibility and availability in mind, Lufthansa Technik’s approach towards a Digital Tech Ops Ecosystem inspired us to take a fresh view of our own approach.

While we continue to progress our digital roadmap, we also take onboard what we have learned in trialing an ecosystem view. When selecting our standardized solution for all of our tech records, we are currently working together with flydocs, as we aimed for a partner ensuring a seamless integration with our existent E&M core systems. Undergoing the implementation, we strongly believe it is the right decision to work with a partner that is open to change and who can quickly adapt to our needs and requirements. Looking at a future-proof system, however, comes also with its unqiue implementation challenges. As an early adopter of the Lufthansa Technik Digital Tech Ops Ecosystem, we consider ourselves as a key candidate to further optimize the integration benefits. Concerning flydocs, the further automation of previously highly manual and paper-based processes, paired with a seamless AMOS integration perfectly aligns with our ambition to work smarter and faster in the most sustainable way.
For the eTechLog, standardization also provided the foundation for digitizing ways of working. Coming from five different TechLogs, we are very pleased that we first launched a single paper TechLog across all five airlines. This enabled us to craft a common understanding. We are now in the process of moving from this single paper-based TechLog to a common eTechLog across TUI Airline. We are curious to see to what extent Lufthansa Technik can utilize the benefits of its ecosystem to deploy a future-proof solution for a highly inter-connected process and system change to satisfy the complex needs for the affected E&M, flight and cabin operations.
A constant arena of further development within the fleet systems, is AMOS. In the past, we had five different AMOS systems but have merged them into one system following extensive crossfunctional collaboration. We are very happy to have achieved that. Next in line is the AMOS eSignature. The project has already started and we are progressing well on this, which is a critical milestone on our way to paperless maintenance operations.
Next, to our core system and hardware changes. We are extending our ecosystem by in-house co-creation efforts with our data science and analytics teams. We constantly challenge ourselves to make the most of our data and develop our own tools to drive digitalization. One outcome of the collaboration with our in-house data experts is the delivery of a stock-modelling tool which has already been utilized during past seasons to optimize stock holding patterns across our bases in order to support our line and base maintenance operations.
A strategically critical project to TUI Airline has been AVIATAR’s Condition Monitoring and Predictive Health Analytics application. In this, we are coming from a very reactive way of working to a very proactive way of doing maintenance. The project’s current focus is to build more resilience into our operations and prevent operational unscheduled fleet unavailability. To effectively do this in our MOCC (Maintenance Operations Control Center), it must be done in a standardized way of working, using real-time data and effective alerting.
In a nutshell, at TUI Airline E&M we are very ambitious to craft our own digital ecosystem by strengthening our in-house capabilities on data handling. From an outside standpoint, we remain curious as to what our strategic partners and competitiors are doing (see figure 6). The recent AVIATAR Community Day in Hamburg offered us, once again, the opportunity to share knowledge and expertise with other carriers and the framwework around the Lufthansa Technik Ecosystem will ensure further open conversations in the future.
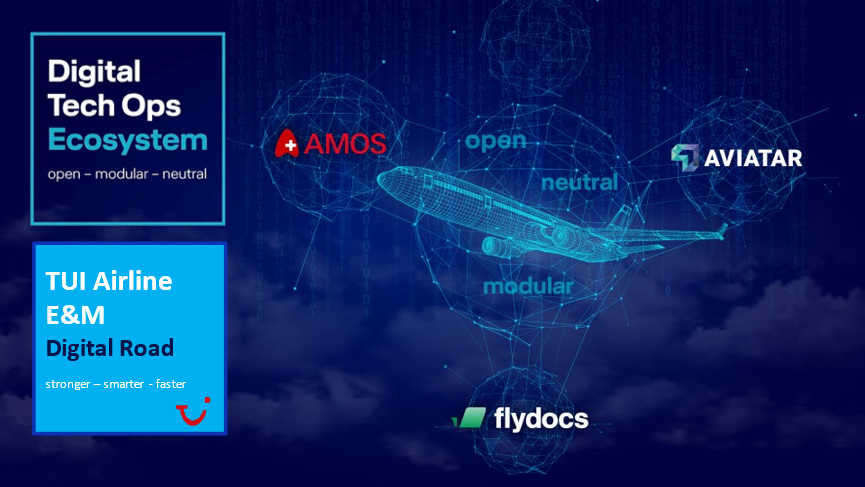
Figure 6
While the three different businesses, AMOS, AVIATAR and flydocs have three different backgrounds, the Digital Tech Ops Ecosystem philosophy should strive for further alignment from a customer and end-user perspective.
A DEEP-DIVE INTO BRINGING PREDICTIVE MAINTENANCE ALIVE WITH AVIATAR
Looking at AVIATAR, we aimed for a renewal on how we utilize aircraft health monitoring data across our fleet. Within a pilot project we strongly focused on the Boeing 787 operation. Within only six months we delivered a proof-of-concept and operationally-critically use cases were successfully implemented (figure 7).
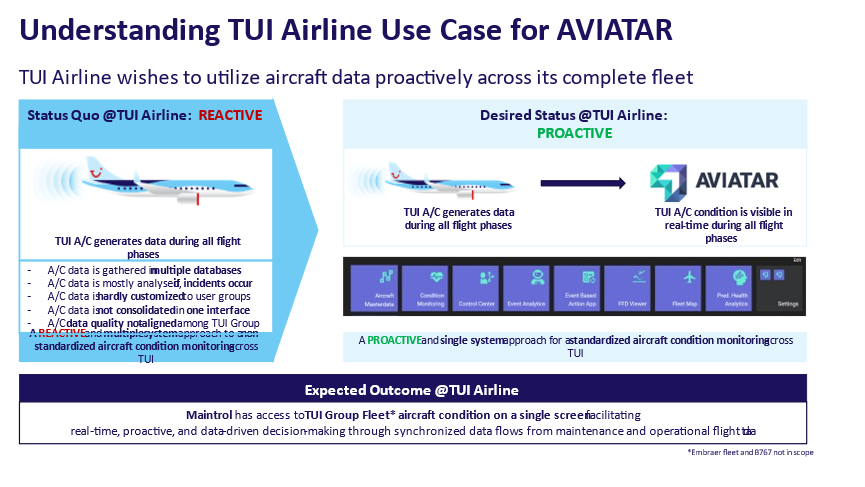
Figure 7
Looking back on the project, we saw it was a very fast implementation as the collaboration between the TUI Airline and AVIATAR teams was highly collaborative and based on co-creation. The critical success factor is that both teams had a shared vision to deliver a stable flight operation. Furthermore, the on-site implementation support from the Aviatar team was a great help in performing a credible system change within only six months. Bram D’haene, Fleet Performance Manager and a key driver of the ecosystem within TUI Airline E&M concluded that, “The co-creation we have with the Aviatar product has allowed us to see something in the operation and go after it with data to avoid repetitive issues in the operations resulting in an improved fleet performance and a happy internal as well as external customer.”
Contributor’s Details
Niklas Kropp
Niklas worked with KPMG Deutschland until May 2022 before he returned to TUI Airline as a Process Optimization Project Manager. In September 2022, he was appointed to become Programme & Projects Manager E&M, overseeing the delivery of the TUI Airline E&M Transformation Programme by driving the further strategic alignment across the five TUI Airlines and allow TUI Airline to adapt to the latest industry trends.
TUI Airline

There are currently five airlines in the TUI Group operating around 130 medium- and long-haul aircraft serving more than 180 destinations around the world. TUI is proceeding with the renewal and modernisation of its Europe-wide aircraft fleet to make flights more economical, cost-efficient and environmentally-efficient. Since 2013, TUI has ordered a total of 70 Boeing 737 MAX aircraft to replace aircraft currently in service. The first 737 MAX 8 was delivered in January 2018.
Swiss-AS
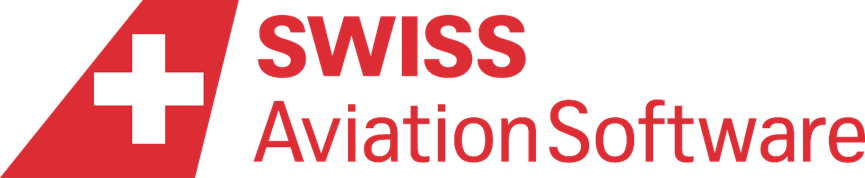
Swiss AviationSoftware unites more than 30 years of IT experience with profound MRO expertise and offers its customers a state-of-the-art maintenance system. AMOS is a comprehensive, fully-integrated software package that successfully manages the maintenance, engineering and logistics requirements of modern airlines and MRO providers by fulfilling demanding airworthiness standards. More than 220 customers around the world steer their maintenance activities with AMOS, which makes AMOS one of the industry-leading MRO software solutions worldwide.
AVIATAR
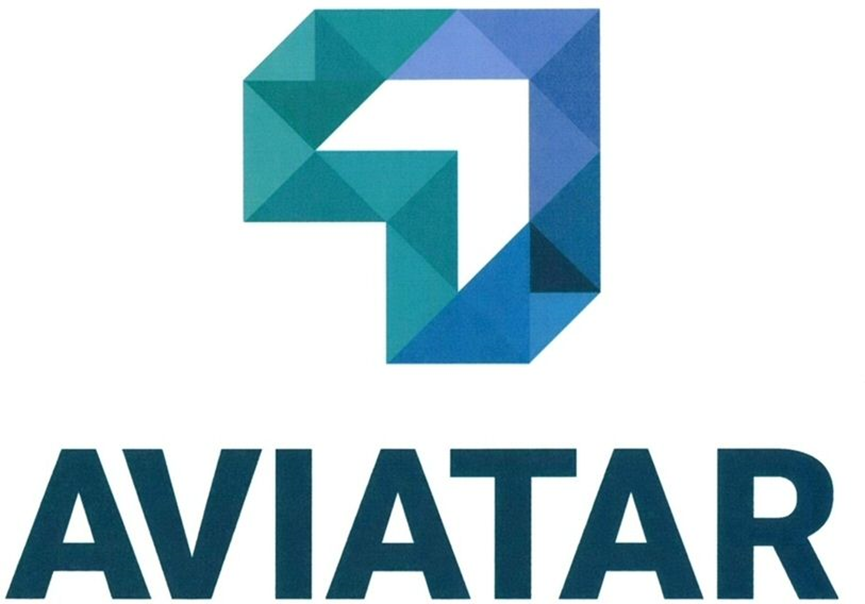
AVIATAR, the digital platform of Lufthansa Technik, combines decades of aircraft knowledge and engineering expertise with data science. Their digital solutions focus on the entire value chain, from predictive maintenance to automated fulfilment. What’s more, AVIATAR delivers full flexibility to choose which MRO provider to use. AVIATAR uses data from airline ops, aircraft, maintenance systems and other external sources. It then turns that data into actionable insights that empower usersto achieve tangible results.
flydocs
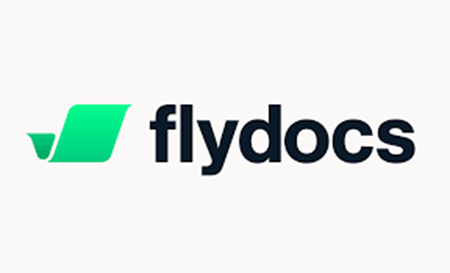
flydocs is an asset management solution provider that creates value out of aircraft maintenance data, offering tools and expertise to drive sustainable innovation to help build the future of the commercial aviation asset lifecycle. Founded in 2007, flydocs is 100% owned by Lufthansa Technik. With over 300 employees in multiple locations across the globe, and are trusted by over 78 airlines, lessors and MROs to deliver measurable long-term operational and cost efficiencies.
Comments (0)
There are currently no comments about this article.
To post a comment, please login or subscribe.