Articles
Name | Author | |
---|---|---|
CASE STUDY: SAS’s Journey to paperless maintenance operations | Yuliya Kornyeva, Maintenance Data Analyst, Dlovan Sandi, ELB Digital Service Owner, SAS - Scandinavian Airlines and Rob Saunders, Director of Business Development of the Electronic Log Book, Ultramain Systems | View article |
WHITE PAPER: Leveraging data for digital aviation success | Sander de Bree, Founder & CEO, EXSYN Aviation Solutions | View article |
CASE STUDY: Digital transformation at TUI | Niklas Kropp, Programme & Projects Manager E&M, TUI Airlines | View article |
CASE STUDY: Getting the best from new engines at Condor | Nicolas Schneider, AMOS Administrator, Condor and Dr. Almut von Schneidemesser, Senior Manager for Aircraft Communications IT at Condor | View article |
WHITE PAPER: Lufthansa Systems develops a digital twin concept for aviation | Priscila Monroy, Junior Consultant at Lufthansa Systems | View article |
CASE STUDY: Achieving IT process continuity in Air France Industries and KLM Engineering & Maintenance | Anne-Laure Propper, Project Manager & Olivier Demède IFS Maintenix Product Owner, both Air France Industries KLM Engineering; and Arjan Otten, Project Engineer Maintenance Programs, KLM Royal Dutch Airlines | View article |
CASE STUDY: Achieving IT process continuity in Air France Industries and KLM Engineering & Maintenance
Author: Anne-Laure Propper, Project Manager & Olivier Demède IFS Maintenix Product Owner, both Air France Industries KLM Engineering; and Arjan Otten, Project Engineer Maintenance Programs, KLM Royal Dutch Airlines
SubscribeAnne-Laure Propper, Olivier Demède and Arjan Otten share the experience of managing multiple maintenance organizations and strong cultures in one MRO system
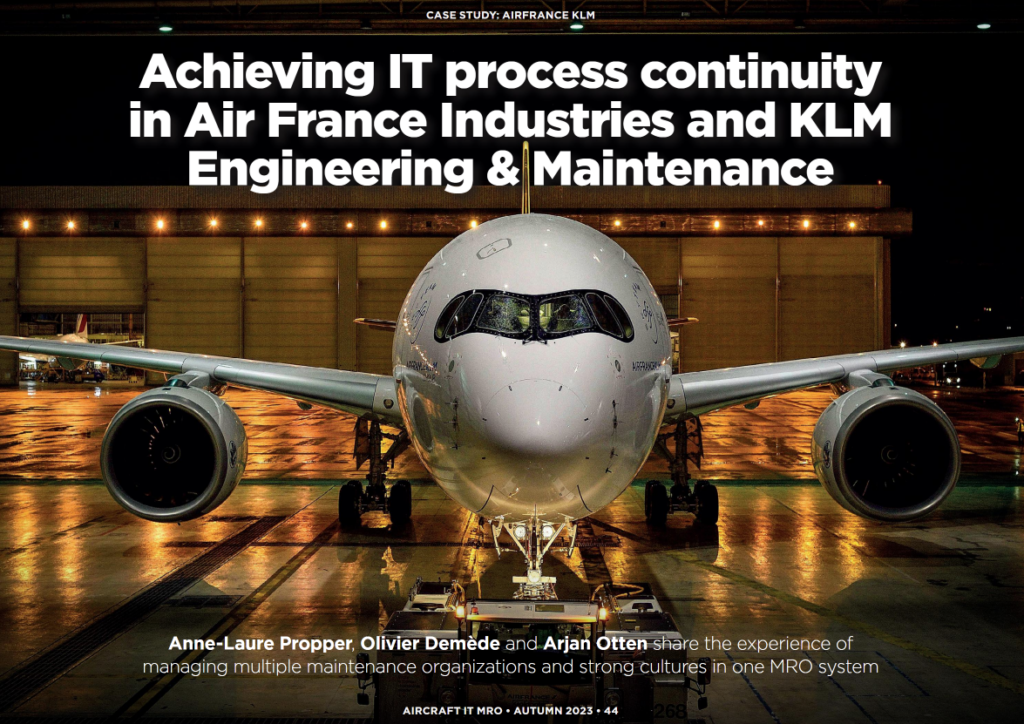
For any case study to be meaningful, readers will need to know the circumstances in which the case occurred. In this article, it was with one of the world’s great airlines, and here are few words about them.
KLM ROYAL DUTCH AIRLINES
Founded in 1919, KLM Royal Dutch Airlines is the longest continually operating airline in the world. Part of that longevity can be ascribed to an unwavering commitment to technology, innovation and transformation. Typically, in 2003, KLM saw the potential of an organization that was itself then just seven years old, and the power of their product as a maintenance and engineering system built for the world’s top airlines. It led to the airline selecting the IFS Maintenix product to run their engineering and MRO division. Less than a year after that, in 2004, Air France, a giant of the industry with seven decades as France’s flag carrier, merged with KLM to form what was, at the time, the world’s largest airline, Air France KLM. Since then, the two airlines had come together to build a truly world-class organization.
STARTING OUT IN 2004
When Air France KLM selected IFS Maintenix in 2004, one of the main criteria was that the organization should be able to maintain multiple maintenance programs for the different operators in the group. In the period from 2004 to 2015, all of the KLM fleet was inducted and from 2009 to 2020, the Air France fleet was inducted (figure 1), including the Airbus A380 which was being introduced at the same time.
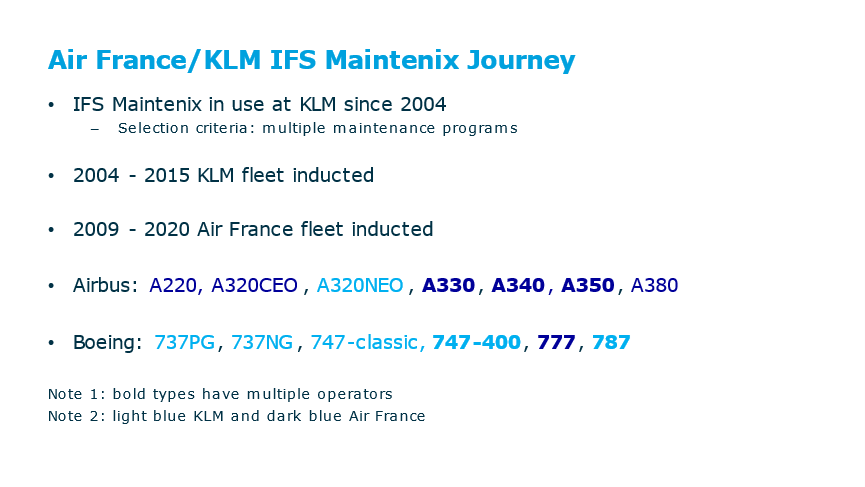
Figure 1
At first, Air France maintenance had been using a legacy system, separate from IFS Maintenix but, after 2009, moved quickly to put the Air France fleet onto the new system. The combined airline had a few criteria that they wanted to meet with the new unified maintenance program (figure 2).
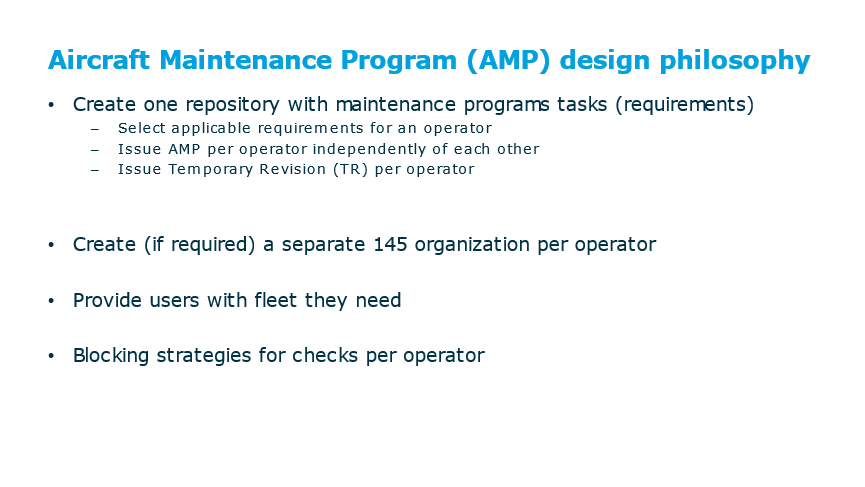
Figure 2
They wanted to create one repository with maintenance programs and tasks (requirements) applicable for different operators in the group and to be able to select applicable requirements for each operator. Also, they wanted to be able to select and issue maintenance program revisions for each individual customer, and that is possible in IFS Maintenix. Also, in the case of a temporary revision with a requirement from the authorities that it has to be implemented immediately, but where it only applies to one group of aircraft, they want to be able to implement the revision just for the group to which it applies whether that aircraft group is in one fleet or multiple fleets and that is also possible with IFS Maintenix. All of that was realized when Air France and KLM came together.
Both airlines are regulated by EASA but also both have history, working in different ways in Paris and Amsterdam and there are other customers who use Air France KLM MRO services who also have their own ways of working. Now, Air France KLM is able to create, for an aircraft type, a separate set of task cards dedicated for each customer operating that aircraft type. Air France will use the card for their 145 organization and KLM for their own 145 organization.
With this program, Air France KLM is also able to provide access to the system user for only the fleet they need to see. So, a planner at KLM will see the KLM fleet whereas their colleague in Air France will only see the Air France fleet. KLM Engineering and Air France Engineering will see all the aircraft in their respective fleets. And a customer who only has two aircraft put into the system at Air France KLM engineering will only see those two aircraft in the planning module and can work with those aircraft.
The last thing that was important for the airlines was that they should be able to create a separate blocking strategy for each operator’s fleet. So, if one airline wants to have an A Check or a C Check or, over all the types, a D Check, or if a customer does not want A Checks and only wants the individual tasks but not grouped, all those things are possible within one aircraft type.
So, for the Boeing 787, it has been possible to create one set-up for KLM, a different set-up for Air France and yet a further set-up for that other customer who does not want A Checks but will select specific tasks per visit. For all of them, it is possible to create a set-up which does that. In figure 3 is a schematic of how that works.
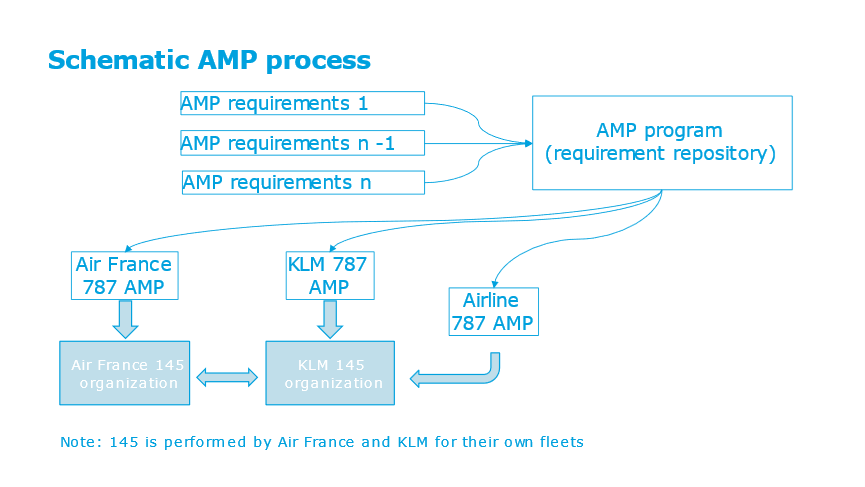
Figure 3
At the top of the figure, you can see the Aircraft Maintenance Program (AMP) requirements numbered 1 to ‘n’, ‘n’ being whatever number it runs to which is usually between two and three thousand: for the Boeing 747s, due to their history, that was often up to five thousand tasks. They’re all part of the maintenance program requirement repository and, from there, it is possible to send them to the different AMPs of the different customers. For the Boeing 787, there are two independent sets of task cards, one for each of the two 145 organizations. Even if, say, the aircraft had been inducted in the KLM 145 organization but, in the end, it was maintained partly in Paris by Air France. Because they all use the one system, even if it was not their main organization, they could still perform work on that aircraft in Paris using the KLM organization task cards.
IFS Maintenix also provides a reporting solution for AMPs; with a single button, you can issue a maintenance program for the operator that you are looking at, and there will only be task cards for that operator, which helps a lot: but you can also, build your own custom report to meet a regulator’s requirements for specific data for a particular operator.
Starting from the requirements, figure 4, moving left to right, shows aircraft and OEM requirements and alterations.
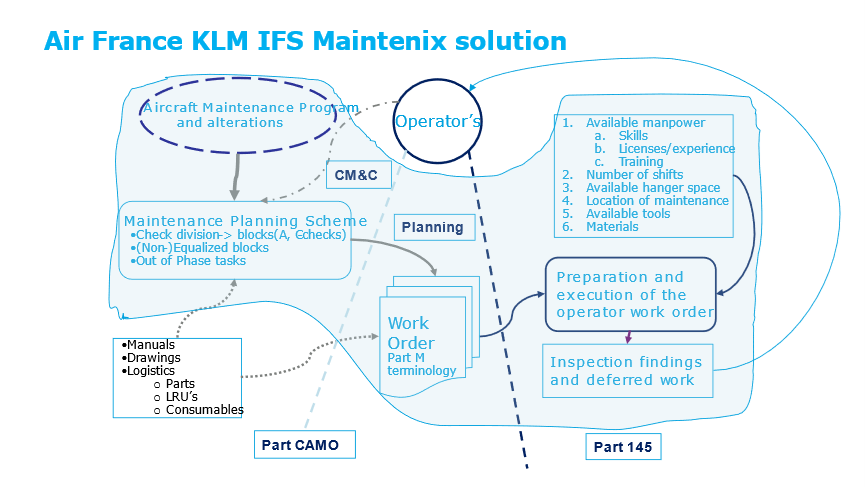
Figure 4
Everything can be set-up in Maintenix from this document. You can do a maintenance planning scheme and organize each maintenance that you want to do on the system, be that a check, item outside of maintenance phase, or equalized blocks. You can do whatever you want in a way that is suitable for the airline and its operation. Then, to do this task, you’ll need everything – manuals, parts, logistics, information – and basic information which can be set-up from the requirement, the Work Order and the work card instructions. This starts to be the transition between CAMO and Part 145. We have this set-up in the Work Order to be prepared for the mechanics in the Work Package.
Then, in the end, Part 145 gets organized with the work that the Work Package contains to make it workable, and to make sure there are enough appropriate skills and parts available. Everything can be managed internally in the IFS software as long as it receives enough data. All the preparation and execution of the work is done within IFS Maintenix and must remain in the system while all the feedback goes back to the operators through reports or through the application itself.
BENEFITS AND ACHIEVEMENTS
The benefits and achievements from having IFS software include, as already mentioned, we can generate a maintenance program and a temporary revision (TR) which is a key point for Air France KLM. Using the legacy solutions that we had previously, it was really difficult to generate a TR, it was a very complex thing; so, this represents a great benefit for us. We can also now issue AMPs and TRs for individual operators; having fleets with multiple operators, as we’ve already explained, we can now ensure individual AMPs and TRs for each operator and are now able to work continuously on maintenance program revision. We can revise requirements at any time and place them into a box, AMP, then can just release them when the operator is ready and in agreement. Another benefit is that we can create separate Part 145 organizations for each aircraft type. That helps a lot when there are different ways of doing things, especially if there are two or more organizations to work with, operating with different AOCs and different regulatory authorities.
Flexibility is another key benefit: IFS Maintenix is composed of a lot of modules, not all of which are used by Air France KLM; for example, we don’t use the Logistic module: however, users can use the modules they choose but should remember to pay attention to what they want to do and be able to run their process from end to end. There is a capability to define and to design your own reports plus there are almost paperless AMPs and task card processes: ‘almost’ because we choose to still print some work out for control purposes, but it could be paperless soon if we can devote some resource to achieving that. And, finally, new and existing fleets can be incorporated efficiently. Entering a new fleet or a new aircraft to an existing fleet in Maintenix has never been so easy compared to past experience.
CONSIDERATIONS AND LESSONS LEARNED.
IFS Maintenix is very flexible and, in leveraging that, we plan to get more guidance from IFS about what might be the consequences for what we might put in or not put in, or how it should be structured. We are aware that we have pushed the boundaries of the system and it’s logical that sometimes that can mean some trial and error which needs a good test environment. We also found that, if you issue AMP revisions to each operator at different times you need to be aware that the system’s active maintenance program view only shows you the latest released version of the task. It is possible to access older versions, but users have to bear that in mind. If not, you might think that something is missing that isn’t. In our particular solution, because of our integrated landscape, we have a challenge today around unique AMP requirement numbering for components. At the time of writing, we were discussing with IFS whether that could be remedied. Due to the fact that so many groups within Air France KLM utilize the IFS Maintenix system – Planning, Part 145, Engineering, different organizations – if we want to fully activate, or publish, the maintenance program, we’ve found it’s best to co-ordinate across all parts of the maintenance organizations.
Integration with other IT programs is complex – often the case with these sorts of programs. Although the combined Air France KLM was not very old when this implementation began, and so had very little history working together, we saw that different operators had their input into the design of the system and IFS created the input fields that was usual for those operators which meant that, in the end, there were quite a few fields which not everybody had to fill. Some were mandatory, others were optional. When deploying a sophisticated maintenance system like IFS Maintenix, it is therefore critical that you are really careful as to what you decide you are going to put in the system as part of your solution, because whatever data you put in, you then have to maintain for the rest of the life of the aircraft. If you choose to put in too much optional data, you are generating more work downstream for your team, so you should only do that where it’s providing genuine value. Finally, the layout of the fields, whilst not always optimal, does have a small box where a user can put in four thousand characters. There is the ability to open the box wider but there’s no dynamic; so, if there is more going in, it can be pulled on and opened but that is not automatic.
PRESENT AND FUTURE AMP DEVELOPMENTS.
At the time of writing, we were trying to integrate IFS Maintenix with our supply chain and shop floor control. We decided to go with SAP which was already used by KLM for this because it is going to be a company-wide or group-wide software, as a result of which we are facing quite a few issues. IFS has been very helpful because most of the issues we are facing are in the integration with the current legacy systems; two different legacies, complex ones with different requirements. Integration with SAP went better than expected. Integration with legacy is a bit more complex because of Air France KLM’s landscape. So, when you start choosing your product and working with it to be aware of what you are aiming to integrate and how; it’s one of the lessons that we learned that, if you don’t define all your requirements from the start, you might face some difficulties. We’ve been on this project for quite some time and will be happy to share our experience with anyone who contacts us.
Our next step is an e-Techlog to have an interface between the cabin crew and the pilots for notifying and recording faults during the flight. We also need to integrate things with IFS Maintenix which has been a challenge given our previous IT landscape; see above. We want to use the tool to keep control of maintenance with the next step being the e-Techlog or e-Logbook to be integrated with IFS Maintenix.
We have certainly appreciated the capabilities that IFS has delivered for Air France KLM and we hope that this case study has helped readers to better understand the solution and how it has worked for us in the real world of airlines.
Contributor’s Details
Anne-Laure Propper
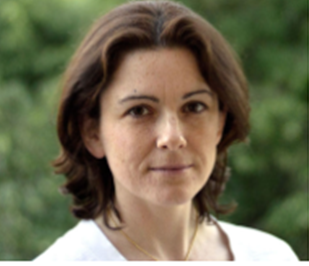
Having started in IT consulting, Anne-Laure joined AIRFRANCE KLM in 2008, occupying various positions before joining the Engineering & Maintenance teams managing projects on aircraft and cabin retrofit and modification and Airbus A380 entry into the AIRFRANCE fleet. Since January 2021, she has been in charge of the CM&C project for AIRFRANCE Engineering, transitioning from legacy systems, and integrating with supply chain and shop floor control systems for the group and its customers.
Olivier Demède
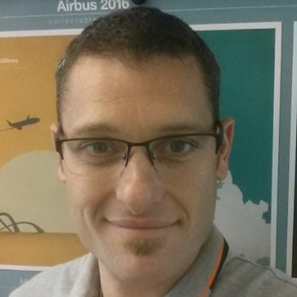
After twenty years on Part CAMO activities, Olivier was involved in Airbus A380 and Maintenix entry into service, in 2009. Then in the CM&C project to move Component Control Configuration to Maintenix. He is now in charge of improving Maintenix usage in the business and defining training material for most beneficial usage of Maintenix. This task relies on a large key user network in various skills, domains and maintenance sites within AIRFRANCE and KLM
Arjan Otten
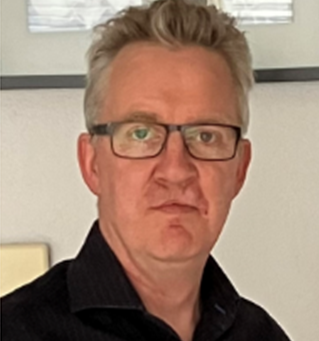
After thirty yeas of aircraft manufacturing and airline experience as structure and maintenance programs engineer at Fokker Aviation, Arjan joined KLM Engineering in 1996. Since 2001, he has occupied several functions in maintenance programs for KLM and customers. Since 2003, he has worked with Maintenix software, in the selection process for and use of Maintenix. Arjan is presently responsible for the Boeing 747-400 and 787 maintenance programs for AIRFRANCE KLM and customers
Comments (0)
There are currently no comments about this article.
To post a comment, please login or subscribe.