Articles
Name | Author | |
---|---|---|
The Smarter Supply Chain in MRO: Part 2 | Amol Salaskar, Consultant Business Analyst in Aviation and MRO, IBM Center of Competency | View article |
The towering eye wall | Gesine Varfis, Marketing & Early Adopter Program for Maintenance Consulting, APSYS | View article |
Digital Transformation — where we are today | Martin Harrison, Global Managing Director - Airlines, Aerospace and MRO, ICF | View article |
Case Study: First Air – Implementing a Mobility Suite of Apps | Gail Campbell, Manager Technical Records & Trax Administration, First Air | View article |
How I See IT – The choices paradigm | Allan Bachan, Vice President, ICF | View article |
The Smarter Supply Chain in MRO: Part 2
Author: Amol Salaskar, Consultant Business Analyst in Aviation and MRO, IBM Center of Competency
Subscribe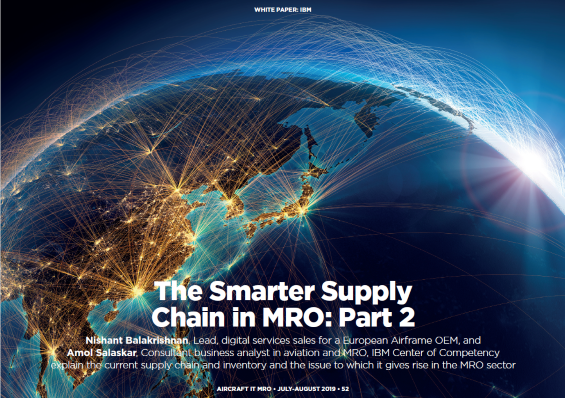
The Smarter Supply Chain in MRO: Part 2
Nishant Balakrishnan, Lead, digital services sales for a European Airframe OEM, and Amol Salaskar, Consultant business analyst in aviation and MRO, IBM Center of Competency explain the current supply chain and inventory and the issue to which it gives rise in the MRO sector
In part one of this paper, we discussed the imperative to improve the MRO supply chain in light of the growing global aircraft fleet, and the competitive pressures on MRO organizations from the need for lower costs and greater efficiency as well as growing customer expectations.
THE BUSINESS SOLUTIONS
In order to address the challenges described above, we need to bring forth technology solutions in the supply chain that will not only alleviate but also bring significant added value in terms of facilitating the evolution of the aviation MRO and its supply chain from being effective to one with a significant business edge. This will require, building on the structure of solutions in the capabilities of Analytics / Business Intelligence / Optimization, Advanced Analytics /Predictive / Simulation, and Customer Experience.
Network Integration and Connectivity
There is a need for a structure which promotes the seamless flow of across the network, making it relevant and meaningful to various stakeholders in the entire supply chain. A supply chain is mostly a collection of individual elements that work in a synchronous manner. For this the suppliers, third party vendors, the internal shops, warehouses, spares depots, logistics and the production planning and control need to work together. If we have the data foundation in place then the supply chain can evolve by using tools in a variety of ways and we will explore a few in the following sections.
Analytics / Business Intelligence / Optimization
Apart from the access to the status of day to day operations, the use of analytics (figure 1) helps to define and measure many of the common KPI (Key Performance Indicators) that govern a supply chain. KPIs such as order fulfillment, Cost to Service, Lead time, inventory carrying cost, Repair & Maintenance cycle, Fill rates, Fast Moving, Slow Moving, Non-Moving, etc. typically address the operational or service excellence drivers. But peculiar within aviation MRO, is the ability to identify parts, mainly rotables, with a higher level of NFF (No Fault Found) rates and rogue components i.e. parts whose unscheduled failures are higher than OEM (Original Equipment Manufacturer) specified standard.
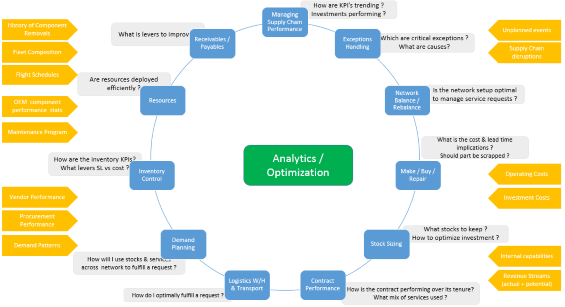
Figure 1: influence of analytics / optimization
Many airline customers prefer to enter into a parts pooling agreements, and expect that parts that are used on the own fleet are up-to a specific technical standard. This requires that the aviation MRO maintain a certain quality in the pool standard. This requires planning for investment and monitoring of the parts usage. An analytics program helps with efficient tracing of such parts to ensure, and then to schedule the parts for withdrawal from the pool.
A direct benefit to a MRO supply chain is the use of forecasting & statistical analytical techniques in order to determine the parts and part quantities to procure. With aviation’s specific parameters, such as parts interchangeability and airplane or engine configurations, planning complexity can easily multiply. An analytic tool supports indecision making on the required allocation of funds to parts procurement, repair, scrap and overall supply chain costs.In the process of procurement the analytics tools play a vital role in the selection of supply vendor based on several criteria, to basically select parts, quantities and price points in order to optimize the spend and meet the business requirement.
A good analytics engine will also facilitate the parts phase in and out. As OEMs introduce new parts it’s important for the MRO to determine the total parts in the network along with the parts installed at the customer airplanes (if the customer has out-sourced MRO activities as Total care). It can then propose an organized process by which new parts can be introduced in the supply chain and the withdrawal of the obsolete parts, or parts that need an upgrade.
When we consider the use of optimization, then it is to dynamically balance the network and to re-balance it based on customer demands. This entails in determining the parts numbers and their quantities that should be maintained at the warehouses, main bases, forward deploy stores, and also at customer sites. The computation of safety stocks, minimal stock alert levels, and order quantities are criteria coupled with the other mentioned above that are used for managing the inventory in the network or the supply chain. An optimization tool can be pro-actively used for managing AOG requests. This is to use the essentiality codes for parts, in order to determine the parts that can be stocked at stock depots nearest on along the aircraft flight routes.
In the supply chain process it is not just about spares, but also the impact of tools and equipment. In the year 2012, Ryanair reported more than 20 failures on its Pitot tube heating failures causing the pilot and co-pilot disagreement on the airspeed, a severe safety issue. In such unplanned events there is an urgent need to perform inspection / replacement of Pitot tubes and two are located on the vertical stabilizer near the elevators, which could be about 20 feet above the ground. Such a task needs the right ground support equipment (GSE) e.g. maintenance stands. Therefore, one can use optimization tools for managing the GSE’s and their positioning to match fleet operations and maintenance requirements.
Managing the repair cycle is an equally critical part of the supply chain. Optimization tools facilitate in order to determine the additional serviceable parts that must reside in the supply chain in order to overcome the lead-time and cost of repairs. In this process the analytics engine can also support decision making, i.e. in determining the movement of the repair part based on the repair scope to the repair facility with the capability, capacity and resources available.
In the process of the supply chain logistics, the role of determining the least cost path (logistics route) requires warehouses that should replenish the forward deploy depots and demand fulfillment – customer requests. In the process of fulfillment is the connectivity to external systems (including social) that allow making the decision for the route the parts should take in order to reach their destination. This route selection can include the business restrictions, e.g. embargo for movement of parts, bond ware-housing requirements, peculiar government customs policies, weather, traffic conditions, transport costs and time.
The safety-risk caused by the use of Li-Ion (lithium-Ion) batteries introduced on the new generation Boeing aircrafts has also caused a disruption to the supply chain. In the year 2014 the ICAO (International Civil Aviation Organization) moved to ban the transport of Lithium metal batteries as cargo on passenger aircraft. This also introduces new regulations on documentation, packaging, palletizing, shipping, and storing of the batteries. Such events and rules disrupt the supply chain, as alternatives are required for addressing the additional constraints. Therefore we can see that technology solutions with visibility to the complete network, and optimization engines with specific objectives at various functions within the supply chain, will ensure the entire global network is optimized and re-optimized.
Advanced Analytics / Predictive / Simulations
Evolving from the use of analytics engine and optimization to manage the supply chain network efficiently, there is the need to prepare the organization for the changes in the market-place and offer customized solutions. A vital role of advanced analytics and simulations is during a disruption in the operation. In the event of disruption, is to evaluate and propose alternatives to overcome the disruption. A disruption, can originate in the changes in the demand coming from an in-operation fleet, or issues at the shop-floor, or delay in parts from suppliers.
Typically, it is considered cost-effective to run a component installed on the aircraft until its designed TOW (time on-wing). However, if the part fails earlier, then it can lead to additional costs to the operation and possibly lead to an AOG (Aircraft on Ground) situation also. Predictive analytics tools can play a role in the analysis of data received from customer fleets. In this case would be the ability of the system to use OEM provided historical performance data on the components, the in-service data arising from the components performance on the installed and operational fleets globally, description of the probability of failures, the repair turn-around-time and the lead-time for procurement. The analytical and predictive capabilities reveal the failures or potential failures of the installed components.
Predictive or simulation capabilities (figure 2) can also be used for network-balancing and inventory sizing exercise. The ability to analyze the customers (and potential customers) operations provides the in-sights and triggers to the supply chain network to build a strategy to address the growth or changes in the market changes.
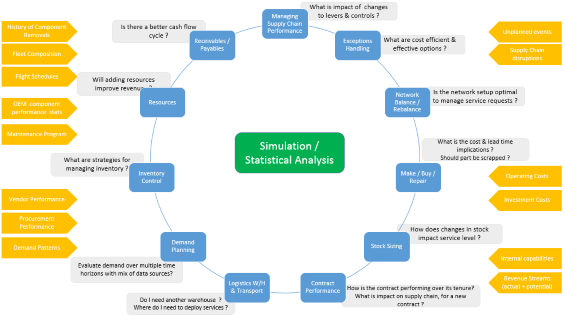
Figure 2: influence of simulation / statistical analysis
Customer operations comprise of fleet changes, and the aircraft configuration requirements, its aircraft maintenance and engineering policies, and its bases. The aircraft type and the fleet configuration influence the parts procurement, stocking and movement impact to the supply chain. New flight routes and changes in the home-base airports, i.e. night halting stations, facilitate determining the locations or warehouses and forward deploy depots that are nearest to the stations services by the airlines, and the logistics considerations.
Every aviation MRO supply chain tries to offer the highest possible service level at the optimum possible investment in parts. In this process it’s imperative to plan the investments in the inventory so that they are most applicable for the customer’s fleets. Some of the vital inputs for the simulations include the requirements of modification status of the parts, the modification status of parts installed/applicable to the customer fleets, and the customer airplane configurations.
Simulations are useful when determining the addition of new airlines to the MRO services customers’ portfolio. When a new service agreement is under consideration, the MRO will want to determine the kind of pricing to offer, and parts to support based on the investment it will likely have to make in its own parts pool or inventory. Such simulations will support the MRO in determining whether accepting a new customer (with its parts and services requirement) will continue to increase its revenues and mainly the profit margins, and the kind of impact on its supply chain performance.
A combination of statistical analytics and simulation can be used for analysis for a medium to long term strategic planning. As airplanes age the maintenance requirements increase and also the need for replacement or repaired parts. This means that shop capacities and resources need to be planned along with the spare-parts requirements. Maintenance can be both the planned and unplanned maintenance. Many larger maintenance e.g. landing gear overhaul, or engine LLP (life limited parts) replacements or repairs can be planned based on the age of the airplane and its in-service performance records. Unplanned events can come about due to in-service problems.
A hard landing or a lightning strike cannot be predicted, but can be prepared against, based on a combination of weather and airplane performance. Both these may lead to spares and maintenance requirements. A supply chain can be geared to address such requirements by a collection and analysis of customer’s in-operational airplane fleet data.
Statistical analytics in combination with simulation technique can be utilized for making supply decisions so parts with their parts quantities, modification status, and applicability can be determined along with the pricing and vendors performance. The aviation spares parts forecasting cannot be determined only by statistical technique alone as there are flight critical parts that won’t provide a stocking requirement.
Cognitive analytics are useful when evaluating warranty claims, and invoice processing: evaluating warranty claims that are within the valid conditions and detecting incorrect claims by using the operating performance of the parts, warranty conditions and design parameters. In a similar manner invoices preparations for work performed can be checked against contract conditions and work scope accomplished in order to price the invoice correctly. This would be labor, and parts price. This avoids the performance of work not approved by customer, and protects against any customer complaints due to failure to meet contract conditions.
When the MRO would like to capture additional market share, the understanding of the airlines not serviced or geographies not serviced come in the study. Cognitive solutions are the right tools for such a study. An input from social media and industry news help determine the market dynamics and industry focus areas. An example of such social media inputs would be utilized by the aviation MRO in order to address the supply chain growth, which is whether there is a need to open a warehouse or repair facility in that region in order to be in the close proximity to the growing or the changing market, and understand the kind of services that should be offered. This is again based on aircraft in operation and the age of the fleet.
Customer Experience
Using analytics and cognitive engines the supply chain performance can be improved both in terms of timeliness (speed), and cost. However, the quality of the supply chain performance is principally related to the way the customer experiences service. The way to improve the customer experience is to understand the customer’s touch-points across the supply chain, and provide a uniform and seamless Omni-channel and multi-purpose experience. An Omni-channel experience would mean that the online channel and contact center (call-center) is able to offer services with the same consistency and quality, and above all, the ability of the customer to switch between the two channels without losing continuity.
Customers in the aviation MRO industry require MRO services on a continual basis and search for new products and services, conduct transactions, and receive service. Products and services, could mean the contracts e.g. PBH (power by the hour), Total Care, or T&M (Time and Material), spare-parts that meet the airplanes configuration, engineering capability e.g. a plasma welding / NDT (Non-Destructive Testing), parts repair capabilities, technical services e.g. line maintenance / AOG services, and parts pooling services.
For existing customers, services could mean a dashboard for checking contract performance i.e. SLA, penalties, warranty applicability, accessing invoices, real-time monitoring of progress of work in the shops (including contracted shops), and accessing the shop reports / serviceability records of parts. Transactions are the booking of a part or service request, reserving maintenance slots, receiving documentation, invoices and paying for services rendered. It can also be as advanced as the ability to offer the customer to prepare a quotation for a service they would require.
Integration and visibility become critical parts of the supply network making the information required to support online and self-sufficiency for the customer. A digital channel e.g. portal would be an access point for the customer to perform any of the tasks. Existing customers who log-on to the MRO providers web-site will be provided with content that is most relevant to the airline operation. A cognitive assistant could interact with the customer in order to facilitate the interaction. Any services that the cognitive assistance is not able to complete, can be transferred to the agent assisted call center, which can then take over the interaction and ensure its successful completion. The call center has access to the trail of the customer’s interactions in order to understand the gaps, and is seamlessly able to take over.
Cognitive capabilities are not just about helping the customer receive a specific MRO capability but also are able to expand the need based on the historical data available. The historical data available could be in the form of the contract in-force, or repair and parts sourced, fleet in-service performance, and OEM recommendations. Using the inputs the cognitive assistant is able to provide recommendations that guide the customer leading to a satisfactory or delighting experience.
In terms of pricing, the cognitive agent is able to look at the customers ‘rating’ and profile standard in order to determine the price point that is attractive to the customer and at the same time is able to retain the profit margins determined by the MRO. This is possible through the visibility of the internal cost structure, as well as knowledge about the market or competitor offerings, and use of deep analytics (cognitive) in order to build references for use.
Similar to the MRO’s marketing team, the customer is able to perform a what-if analysis on its contract performance. The simulation capabilities will allow the customer to analyze the impact of inclusions or re-make the entire contract.
A supply chain is the back-bone that makes the digital experience a reality. Its integrated nature, and use of analytic and advanced analytics, make it agile and responsive to the customer requirements and anticipated needs.
CONCLUSION
We began with an understanding of the evolving aviation business environment, followed by the challenges that it’s going to create for the aviation MRO’s (Maintenance, Repair and Overhaul). The MRO industry is evolving in its organization into competing supply chains of suppliers, MRO and third party service providers. On the spares front the customer’s expectation is to pass a large part of the spare-parts and engineering requirements to the MRO, and measure the success based on performance impact to the commercial flight operations.
MRO’s will be compelled to improve their supply chains and also realize that there are benefits from the vast amounts of data that is generated by the airplane (and its installed components), coming from the OEM, and suppliers/repair vendors. This data could be both structured and unstructured, and can be used to simulate or predict scenarios that will allow them the ability to service the changing business and also ensure that the operations are efficiently managed.
We described the key challenges, i.e. integration and visibility, the need for reducing cost of operation and re-emphasizing customer focus, from the aviation MRO supply chain environment. These challenges are even more peculiar because of the aviation specific parts characteristics such as applicability, interchangeability and essentiality that are fundamental to business operation.
We’ve explored ways prevailing and emerging technologies can influence improvements at various key parts in the supply chain process. The ERP (Enterprise Resource Planning) systems automate many of the tasks, thereby promoting the management organization towards a MBE (management by exception). However, it is still a reactive process that looks at historical patterns, and availability of a comprehensive set of business rules.
The advent of advanced analytics, simulation, statistical analysis, optimization and lastly the cognitive systems (machine learning and artificial intelligence), will provide the next level of agility to organizations. At the end these intelligent tools are aimed to improve the supply chain’s effective-ness towards a more customer-centric experience that is capable of delighting the customer.
Contributor’s Details
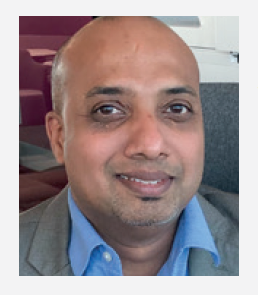
Nishant Balakrishnan is an aviation enthusiast with over 18 years of Industry experience. He has performed various roles in the industry ranging from aircraft maintenance, fleet management, inventory management, management consulting and digital transformation/sales. Currently, he leads the digital services sales for a European Airframe OEM.
Amol Salaskar is with IBM and is working as a Consultant business analyst in the aviation and MRO. Prior to that he has been a Manager Engineering IT with Jet Airways for over seven years, and for around 2 years as Business Analyst for Fleet Management Operations, with General Electric where he certified as a Six Sigma Green Belt. He holds a Bachelor’s degree in Mechanical Engineering, a Master of Science in Industrial and Systems Engineering from Auburn University, USA, and followed by a diploma in Management.
Comments (0)
There are currently no comments about this article.
To post a comment, please login or subscribe.