Articles
Name | Author | |
---|---|---|
The Smarter Supply Chain in MRO: Part 2 | Amol Salaskar, Consultant Business Analyst in Aviation and MRO, IBM Center of Competency | View article |
The towering eye wall | Gesine Varfis, Marketing & Early Adopter Program for Maintenance Consulting, APSYS | View article |
Digital Transformation — where we are today | Martin Harrison, Global Managing Director - Airlines, Aerospace and MRO, ICF | View article |
Case Study: First Air – Implementing a Mobility Suite of Apps | Gail Campbell, Manager Technical Records & Trax Administration, First Air | View article |
How I See IT – The choices paradigm | Allan Bachan, Vice President, ICF | View article |
Case Study: First Air – Implementing a Mobility Suite of Apps
Author: Gail Campbell, Manager Technical Records & Trax Administration, First Air
Subscribe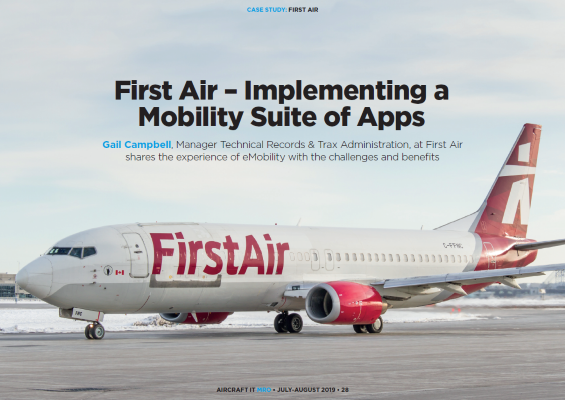
First Air – Implementing a Mobility Suite of Apps
Gail Campbell, Manager Technical Records & Trax Administration, at First Air shares the experience of eMobility with the challenges and benefits
Before we get into the meat of this subject, it might be useful to tell readers something about First Air. The airline, based in Ottawa, Canada, has been serving Arctic communities for seven decades. Being a Canadian and an Arctic airline, First Air experiences lots of snow and is an acknowledged leader in Arctic air transportation. It is a proud accomplishment built on a history of development and innovation, including the Tundra tire that made the arctic more accessible and supported the air surveying and mapping of Canada’s arctic territories. In 1971, the then Bradley Air Services opened its first High Arctic base followed by the first scheduled passenger service in 1973 under the name of First Air. More bases followed with services to Labrador and Greenland; and the airline has continued to expand its Arctic services since. In 2010, First Air used its Hercules freighter to aid in the Haiti Earthquake disaster relief. More recently, the airline carried more than 200,000 passengers and more than 17m kg of cargo in 2016. First Air operates a versatile fleet of 17 aircraft for regularly scheduled passenger and air cargo services. All aircraft are gravel and ice strip equipped for landing in remote locations, and many are combination (combi) aircraft capable of multiple passenger/cargo configurations.
CHOOSING TRAX eMOBILITY
First Air has recently implemented Trax eMobility having already been Trax users for nearly five years. eMobility started to be used in First Air in November 2018 so it’s still a fairly new process for the airline and its staff. One factor when we were considering implementing mobility was that there are a lot of older and senior people who have been in the business for many years and have become used to dealing with paper and pen. But I’m pleased to be able to say that moving them to eMobility went really well and we were impressed with how everyone made the change. First Air initially implemented four modules from Trax eMobility. These were Line Control, Production Control, TaskControl and QuickTurn. We assign the work orders at night for the engineers to work on, including defects from pilots on which Maintenance can act. As I said above, it is still fairly new for us having first gone live last November with Line Maintenance and with HMV (Heavy Maintenance Visit) scheduled for completion at the time of writing, April 2019. Fortunately, we already knew the basics of the Trax system which made moving to eMobility smooth.
For decades at First Air we had been talking about moving towards electronic records, and eMobility offered us the solution with which we could achieve that. We operate in a lot of remote bases that don‘t have very good or consistent internet connectivity and eMobility allows engineers to work offline. Even in one of the smaller stations, the relevant information can still be input and will load up to the main Trax system as soon as there is Wi-Fi coverage available. It provides maintenance staff with quick access to the reference manuals and email, and the ability to order parts at the gate. Just having that ability alone, the time saving for that one task, makes a difference. In the past, when we sent a memo to maintenance staff, we had what was called the dreaded yellow book where everybody had to go and sign it and then, if they hadn’t, we had to chase people to sign it. Now it is on the iPads within Trax with the ‘read and sign’ function for employees, which means that if the airline wants to send a memo to all of Maintenance, their acknowledgement and notification that they’ve read it will be electronic.
We have already noticed an improvement in our performance on delays at the gate or even getting the aircraft out quicker from HMV. There has also been a reduction in duplication, in fact some entries were being done three times (two on paper and one electronically) whereas that has now been reduced. Plus we now need less time for personnel training with the iPads able to deliver training right to their fingertips. There has been a reduction in the paper workload for supervisors: in the past, at night, the supervisor would have a mound of paper with all the task cards and everything to be processed; then my department would send back the paperwork if the supervisor forgot to check this box or something. That is no longer a problem as the system requires each report step to be completed before moving on to the next.
Signing on is done with the LDAP (Lightweight Directory Access Protocol) and each user’s username and password is good for everything; so no need to remember five or six different passwords
EXPECTED IMPROVEMENTS
It isn’t possible yet (at the time of writing) to offer any percentages or statistics to demonstrate improvements, it is still a new system, but we do expect to see better manpower efficiency and utilization and there has already been evidence of that on the line. We also anticipate a reduction in the repetition and errors and to spend less time processing paperwork as well as being able to provide real-time information for maintenance staff, supervisors and maintenance operations – no more waiting for a piece of paper to travel from one department to another. We are also looking to get one set of accurate maintenance records and to decrease the downtime of aircraft at the bases and at HMV. Elimination of time wasted for travelling is expected. What I mean by that is the walk time from getting the card, going to the aircraft, going to stores, going back to the aircraft, etc. We also value the ability to take photos using the iPad camera. Another benefit will be the reduction in technical record audit times – there will be no more need for clerks to process the mounds of paper from supervisors (as mentioned previously) and scan each piece. That won’t be necessary with the electronic solution because it will be right in the system from the outset. There will be automation of internal processes plus improved tracking of the actual man-hours on a task. It’s very easy just to start and stop the task which will mean more accurate hours.
SETUP AND USER ACCEPTANCE
The servers recommended to First Air were Glassfish servers, which are backed up nightly. We have a load balancer, Barracuda ADC and the devices are managed using Cisco Meraki MDM (Mobile Device Management), onto which the iPads are all enrolled so that, when the devices are issued out to remote stations, they can be run and updated from Ottawa. It takes about 30 minutes for Administration to set-up an iPad and then a further 30 minutes for the user to set-up their personalizing of the device – fingerprint, manuals, etc. Also, each maintenance base is equipped with an electronic hot-spot so they can take the device out in the vehicle with them. First Air maintenance staff each has an iPad assigned to them so that there’s no longer just the one computer in the workshop with its password stuck on a Post-it note above the monitor! That means that security has also improved. Database back-ups are run hourly.
PRODCTION CONTROL (HMV), LINE CONTROL AND TASKCONTROL
The Production Control and Line Control apps are equipped with Status dashboards allowing for a review of work required and work accomplished. Instead of the supervisor having to go out to engineers to ask how the work is progressing, he can see everything right on the dashboard. It improves oversight and ease of assigning tasks and defects to the work order and automation of the process reduces paperwork, cost and is moving closer to electronic sign-off. Also reduced is walking and waiting time for the distribution of paperwork. With HMV, it also shortens the turn-times on the aircraft letting us get them out a couple of days earlier, and it’s always good to have the aircraft back out making money. Other things we can do with this is utilizing all aspects of the task cards and removing duplication.
Estimated man-hours has always been an issue with people forgetting to sign-off so that time has to be adjusted. Whereas with eMobility, it is in real time. They simply swipe and it starts to count down their time. Also, with non-routine cards, engineers can assign them to themselves with no interaction needed with Administration.
Other things allowed are for the maintenance staff to complete the task card, research manuals, order parts, and upload pictures while working on the aircraft. Mobile entries are not lost even when offline because the data will be stored and once it reconnects to Wi-Fi the information will sync with Trax. It all decreases processing times for scheduled cards by 20%, and non-routine cards by 40%.
QUICKTURN
QuickTurn is the module that covers defects and it also has a dashboard which shows the flight schedule at a glance with updates in real time, including a quick view of defects that require immediate attention, and that helps with on-time performance. This is expected to decrease maintenance downtime at the gate by 30 percent which represents a tremendous saving as you will see in the video at the end of the article. It also increases the accuracy of records and defect control by at least 40 percent. Transport Canada is always keen to look at defect control and, with Trax eMobility, we have been able to improve on the defect control process.
Another useful capability is that we can review historical troubleshooting, e.g. the captain writes up an MEL, it goes to one base, then the next base can see the troubleshooting right there so they don’t have to contact the previous base. The module includes the ability to search and order parts while at the gate, which wasn’t possible before, and to search for any planned work orders for that aircraft as well as quickly record installations and removals of components and the ability to take photographs for dent mapping, SN (Serial Number) verification or information.
SUMMARY
Although I have endeavored to do justice to the Trax solution in the article, this video will help show what I have covered above and how our old processes compare to the new processes, the time it has saved, and the degree of user acceptance.
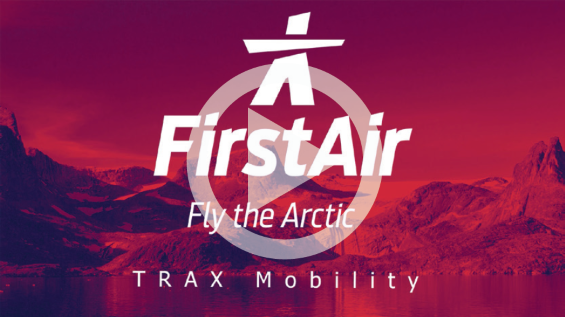
The biggest surprise from our implementation was the level of user acceptance. As an established business, First Air has a lot of older people who had become used to the pen and paper based system but they really took to the iPads. Maintenance personnel really appreciate getting their own iPads and they are now giving feedback to request further possibilities. Because a lot of people have iPhones, they caught on to the mobile system very quickly and Trax uses swipes for start and stop very much like the iPhones with which people are already familiar, so training time was minimal; probably for one mechanic for one module it would be a couple of hours, if that.
Some other Apps included in Trax eMobility include AeroDox, CabinLog, PilotLog, EzStock, VisualCheck with many more to come. Having implemented four of the Apps, we’re now looking to implement more at First Air, including PilotLog and CabinLog.
I hope that you have found our journey at First Air to a paperless environment both interesting and useful.
Contributor’s Details
Gail Campbell
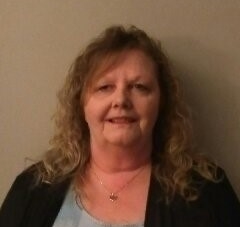
Gail has been with First Air for 25 years starting her career in the accounting department, then the Technical Operation Center and Maintenance Operations before becoming Manager of Technical Records and Trax Administration. She has also played a key role in training, setting up internal processes, getting Trax to work for First Air, and implementing Trax eMobility and the road to a paperless environment.
First Air

Trax
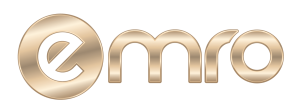
As an aviation Maintenance and Engineering software developer and vendor TRAX has been selected by over one hundred and seventy airlines and MRO operations worldwide with fleets consisting of all types of aircraft. TRAX will continue to focus its efforts in the aviation software market, concentrating on meeting customer requirements, advancing technological features such as mobile and cloud solutions, developing software with world class support and building strong customer relationships.
Comments (0)
There are currently no comments about this article.
To post a comment, please login or subscribe.