Articles
Name | Author | |
---|---|---|
EASA crackdown on Aviation IT Systems | Sander de Bree, CEO, EXSYN Aviation Solutions | View article |
Aircraft IT Survey: The Current and Future Aircraft Maintenance Software Market | John Hancock, Editor, Aircraft IT | View article |
Case Study: TechOps Mexico implements paperless engineering management | Juan Ignacio Lopez, Planning and Productivity Manager, TechOps Mexico and Dr. Hugh Revie, Vice President, EmpowerMX | View article |
Case Study: TechOps Mexico implements paperless engineering management
Author: Juan Ignacio Lopez, Planning and Productivity Manager, TechOps Mexico and Dr. Hugh Revie, Vice President, EmpowerMX
Subscribe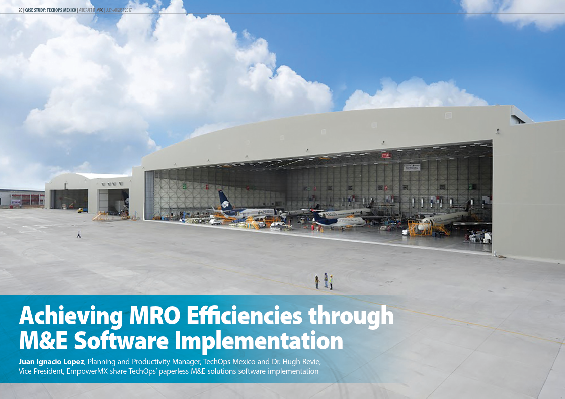
More information makes a better business
Juan Ignacio Lopez, Planning and Productivity Manager, TechOps Mexico and Dr. Hugh Revie, Vice President, EmpowerMX share TechOps’ paperless M&E solutions software implementation
INTRODUCTION
In an industry where the average margins are less than three (3)%, labor costs are crucial to the bottom line of any MRO. An MRO spends approximately $5-10 million USD per bay, per year on labor costs (IATA.org, 2013). If an MRO can reduce labor costs by even five (5)% those savings translate into significantly increased margins.
TECHOPS MEXICO
TechOps Mexico strives to be a world class MRO and the leading MRO in Latin America. Their facility, one of the largest aircraft MRO centers in Latin America, has a total surface area measuring over 100,000 square meters, or over one (1) million square feet. Its three (3) hangars can accommodate over twelve (12) aircraft simultaneously, and each aircraft is serviced using the latest technology and to the highest quality and safety standards.
The company, located at Queretaro International Airport, Mexico was launched as a joint venture between Delta Air Lines and Grupo Aeromexico in 2012. There are more than 1,600 staff in the facility, 16% of which are female, far above industry average. In 2016, TechOps Mexico completed 1.6 million labor hours of work on a 24/7 basis. Currently, the facility has twelve (12) continuous maintenance lines, which they expect to increase. TechOps Mexico is very proud of its environmentally conscious facility, with a hangar designed to collect rainwater, a reverse osmosis water purification system and solar panels that generate 30% of all energy used in the facility.
With a plan to improve labor costs, TechOps Mexico set goals to achieve between five (5) and twenty (20) percent labor efficiencies. When multiplied across the number of bays for an MRO such as TechOps Mexico, profit margins increase dramatically. To gain these benefits, TechOps Mexico selected EmpowerMX’s FleetCycle® software.
EMPOWERMX
EmpowerMX is a world leader in providing intelligent innovative maintenance solutions for today’s aircraft. Formed in 1999, EmpowerMX is headquartered in Dallas, Texas with offices in Europe and the Southeast Asia. EmpowerMX focuses on aircraft maintenance with a full MRO suite of products managed by aviation maintenance experts. The EmpowerMX solution enables MROs or airlines to plan checks more effectively, in part through processing historical data from similar checks or tasks. EmpowerMX then uses that historical data to ensure an incremental improvement in the overall work for every future check performed. More than 4,000 aircraft are managed using the EmpowerMX FleetCycle® software. The software supports all aircraft types and models. With EmpowerMX, many customers have realized similar results to those achieved by TechOps Mexico.
THE ORIGINS OF THE PROJECT
TechOps Mexico provides heavy maintenance services, as well as modifications for Boeing and Embraer aircraft, currently servicing fleets for Delta, AeroMexico and AeroMexico Connect (see figure 1.) With more challenging TAT (Turn Around Time), commitment to satisfy its current customers and growth plans for future customers, TechOps Mexico embarked on a series of dramatic changes related to planning, execution and tracking of aircraft maintenance.
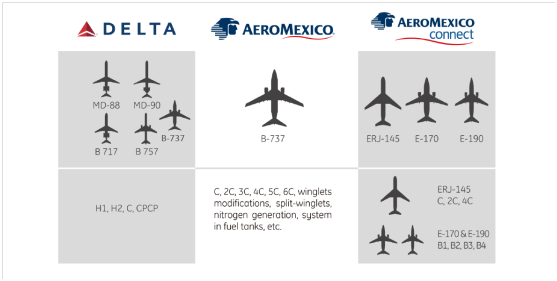
Figure 1
The business realized that achieving these goals required technological solutions that could provide access to real time information and assist to efficiently managing maintenance checks. What was needed was a software solution that could manage the maintenance program from planning to execution. The solution would need to integrate seamlessly with existing supply chain software and, in addition, the system would have to provide maintenance analysis from historical data that could be used to make future checks even more efficient. TechOps Mexico wanted a web-based solution that was easy to use and would help them control data and records more effectively. After evaluating all available MRO software, TechOps Mexico was convinced EmpowerMX FleetCycle® software satisfied all requirements.
HOW THE PAPERLESS MAINTENANCE & ENGINEERING PROGRAM STARTED WITH TECHOPS MEXICO
In 2015 TechOps Mexico was, like most other MROs, entirely paper-based. Every year the company printed 3.5 million pages of technical documentation. TechOps Mexico invested over 100,000 man hours in the tracking, auditing and record keeping of paperwork. In addition to processing time, the company had to allocate significant space for paper processing and storage.
The business had existing systems that were not integrated, causing delays in information flow. To track, report and follow its checks, TechOps Mexico had to update several stand-alone systems; such as SAP, Microsoft Access, Excel and Project. For example, if conditions warranted recommended changes to the check plan, those changes typically took two (2) or more days to be reflected in each system. By the time each system was up-to-date with recommended changes, those recommendations were often no longer relevant.
In 2015, TechOps Mexico announced a 30% increase in the number of maintenance lines by Q1 2016 and sent a team to visit Delta Airlines in order to see the EmpowerMX software in action and understand how Delta used the software to achieve results. The team evaluated Delta’s use of EmpowerMX with the following criteria:
- Real-time delivery of information
- Ease of use by mechanics;
- Management of critical MRO activities, e.g. labor-hour tracking;
- Reduction of paperwork errors.
After seeing the software at Delta Airlines, TechOps Mexico agreed that the solution offered an intuitive, easy to use interface with real-time information for improved operational visibility. The solution streamlined auditing, customer approvals and paperwork processes, while providing the ability to easily manage unique operations through configurable settings. In January 2016, TechOps Mexico selected EmpowerMX FleetCycle® for implementation.
THE IMPLEMENTATION
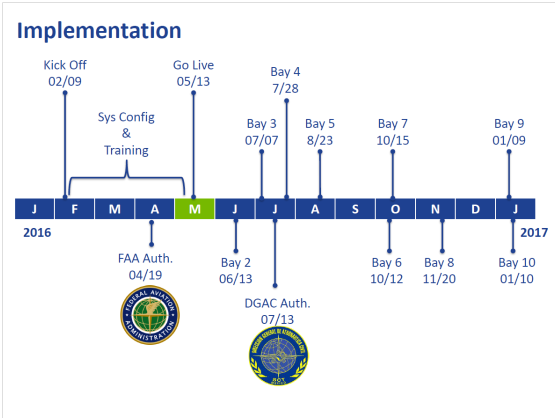
Figure 2
Starting in February 2016, the EmpowerMX team worked with TechOps Mexico to configure the FleetCycle® software to satisfy the MRO’s specific procedures. TechOps Mexico coordinated with the FAA and, in April 2016, was the first Mexican MRO to receive approval to use electronic non-routine cards. The Mexican Civil Aviation Authority (DGAC) also gave its approval to use electronic non-routine cards, making TechOps the first MRO to receive the DGAC certification as well. In mid-April, TechOps Mexico trained the first bay and went live on May 13th. After the first bay, the MRO launched its second one month later and subsequent bays even faster, reducing implementation time from three week to less than seven days per line.
TechOps Mexico summarized its successful implementation in three words: Own. Change. Act.
Own
Own the project. TechOps Mexico firmly believes employees must feel ownership in the software, the project and the implementation. The implementation team decided to rebrand the EmpowerMX system with the acronym F.A.S.T. (Facilitate Aircraft Services at TechOps) which represented the goals and philosophy of the project. The internal branding also helped all employees relate to the project, taking pride and ownership in the software as an integral part of the TechOps Mexico business process.
Change
When a project is owned by the team, change automatically follows. Using change management best practices, TechOps Mexico changed business processes, removed barriers and sustained the new processes. The implementation of F.A.S.T. shifted the culture to a data-driven culture. Instead of making decisions based on perceptions, users of FleetCycle® could now see real time status and ask specific questions based on actual data.
Act
In order to enforce change, an organization must act accordingly. An action that leads to a short-term win enables the new system to become a permanent part of the culture. For the F.A.S.T. team, that meant being on site with the users 24/7 during the rollout: the team listened to users’ requirements and questions, and, where necessary, redefined complete processes based on employee feedback. The successful implementation throughout the facility proved the time and investment of a dedicated rollout team was worthwhile. When users saw that the team acted and executed on their suggestions and questions, employees began building relationships with the implementation team and personally investing in the F.A.S.T. project.
GETTING PLANNING RIGHT
TechOps Mexico worked with EmpowerMX to introduce planning-related process changes. In 2015, the MRO was using Microsoft Project for planning, which was activity-based. While Microsoft Project is an industry standard for project management, it required extensive input by users to correlate a plan to current job card status. Revisions to the plan could take up to two (2) days and provided little support for actions and decisions. With Microsoft Project, supervisors were trying to organize work with an outdated plan for the aircraft.
When the new solution was introduced, the software significantly changed the way TechOps Mexico performed planning. With FleetCycle®, updating a revision to the plan could now be completed in a few hours, rather than days. The software enabled milestone-based planning, which updated automatically based on real-time task card completion. Now all employees worked from the same up-to-date plan by simply logging into the system. As soon as users started creating cards, those items could be evaluated. When the cards were closed, all the associated information became part of future data analytics. Users could see real-time status of each aircraft and make decisions based on facts, not feelings. With the EmpowerMX software, TechOps Mexico could check progress against milestone compliance and replicate a successful plan across different maintenance lines.
CUSTOMER REQUESTS AND OUT OF SCOPE WORK
After implementing FleetCycle®, TechOps Mexico benefited substantially from the software’s capability for managing customer requests and out of scope work. Before the new system, the MRO was using paper ‘bump sheets’, which rely on the user to define whether a customer request was part of the current scope of work. With this manual process, customer’s representatives had to be on site to give their approval. Customer request details were not readily available, creating a disconnect between the reality of the change status and reported information. For example, employees had difficulty determining which customer items were pending approval or how many hours were required to perform those changes.
The introduction of FleetCycle® eliminated these problems with the customer change process. First, based on the specific customer contract, the system automatically identifies and classifies whether a card is part of the work scope; if not, it automatically sends that to the customer for approval. The software enables real-time tracking of which cards have been accepted, hours invested in cards and remaining time on the hours proposed to the customer. The software also tracks all notes and comments the customer adds to those cards. With employees’ real-time access, now customer changes can be approved within minutes.
ELECTRONIC SIGNATURES
With the new solution, TechOps Mexico implemented the electronic signature for non-routine cards. FleetCycle® enables technicians to directly document maintenance into the system and sign digitally for work performed. When a mechanic electronically signs a non-routine, the software checks for the user’s qualifications: once validated, the software records the mechanic’s license number and date against the non-routine. The system ensures that all steps are digitally signed before a card is closed.
Once non-routine documents were electronically available, the auditing process sped up dramatically. As a result, TechOps Mexico was able to reallocate 4,000 inspection hours to maintenance activities. With the improved process, the MRO was able to audit a much larger number of documents per month, up to twelve (12) thousand.
CONTINUOUS IMPROVEMENT
EmpowerMX has given TechOps Mexico much better information about their operations. These facts are vital for the business Continuous Improvement projects. The new software makes problem-solving a fact-driven process, which helps TechOps Mexico find, implement solutions and track their effectiveness. The MRO can easily use the software and data to evaluate different pilot projects. For example, TechOps Mexico recently tested a business process change using FleetCycle® to deliver tooling directly to the aircraft or setting up new control points for budgeting.
CONTINUOUS IMPROVEMENT CASE USING FLEETCYCLE®
TechOps Mexico identified a process bottleneck that prevented quick throughput of task cards. With the legacy system, the buyback process required mechanics to record their request in a paper logbook located at the inspection area. Then all cards waited in queue for the next available inspector.
With F.A.S.T. it became possible to quantify the bottleneck: a card may queue for an entire shift, with more than 200 cards in the queue for a single bay. TechOps Mexico identified the following actions to remove the bottleneck:
- Remove inspectors from any process not related to buyback or initial inspection;
- Assign inspectors based on areas where buyback requirements were present;
- Replace the paper logbook with FleetCycle® queueing for inspection calls.
Before resolving the bottleneck, TechOps Mexico inspectors were only able to handle one (1) aircraft per shift. By December inspectors were answering 48,000 calls, with the average time to completion of less than 15 minutes – a 90% reduction in the time for handling buybacks.
THE BIGGER PICTURE
The success of TechOps Mexico’s FleetCycle® implementation can be seen in the TAT and productivity results from third and fourth quarter of 2016. Of the 47 aircraft delivered after the new solution’s implementation, every aircraft serviced was delivered either on time or early. With the process improvements driven by the electronic non-routine, improved planning and proactive decision making, TechOps Mexico reduced the time to deliver an aircraft by 10% on average. FleetCycle® helped reduce mechanic time from start to completion of an activity by 30%, greatly improving productivity of the organization. The business grew, adding an additional line to the facility, without having to hire 30% of the technicians that would normally be required for a new line.
THE CURRENT POSITION
TechOps Mexico now runs twelve (12) maintenance lines, all using FleetCycle® and continuously trains its people to ensure maximum benefits from the new software. The company also meets regularly with EmpowerMX customers to share best practices. Customer requests are managed more effectively and efficiently. The software has created labor capacity, allowing the business to focus on more continuous improvement projects. Most importantly, the people of TechOps Mexico embrace the change, through ownership and action, enabling the company to achieve its goal of being a world class MRO.
Contributor’s Details
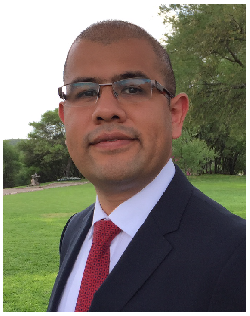
Juan Ignacio has more than ten (10) years of experience working in commercial aviation maintenance. He worked for Aeromexico as Planning and Productivity Manager where he conducted projects to optimize the operation of the airline’s main MRO unit in the city of Guadalajara. More recently, in TechOps Mexico, he led projects to increase new maintenance lines and cost saving initiatives which have increased revenue and saved millions of dollars. Juan Ignacio has his MBA and a degree in Mechanic Engineering.
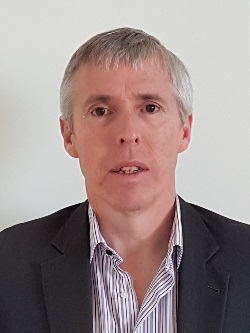
Hugh has been with EmpowerMX for almost two years and prior to joining had worked within Commercial Aviation for almost 30 years. After graduating with a doctorate in Engineering from Strathclyde University in Glasgow, Scotland, he worked for British Aerospace and then, around 16 years ago, he created his own company, CoreData Limited, which focused on providing airlines, MROs, OEMS and aircraft supply chain companies with solutions that could help them drive value from the large amounts of data they were accumulating.
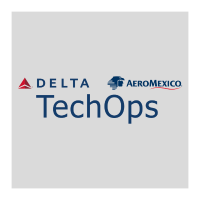
TechOps Mexico
TechOps Mexico’s facility is one of the largest aircraft maintenance, repair and overhaul centers in Latin America. It is a joint venture between Delta Air Lines and Grupo Aeromexico launched in 2012. Its facility is located at the Queretaro International Airport and can accommodate over twelve (12) aircraft simultaneously. It provides airframe and overhaul services to Boeing and Embraer aircraft, including modifications such as Wifi and Cabin upgrade projects. The company also provides advanced Engineering services. TechOps Mexico is certified by the FAA, Mexican DGAC and Brasilian ANAC Authority. Current customers include the regional and narrow body fleets of Delta, Aeromexico and Aeromexico Connect. Aircraft are serviced with cutting-edge technology plus the highest quality and safety standards.
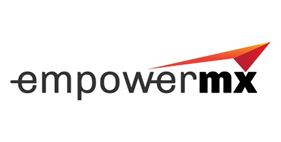
EmpowerMX
EmpowerMX is a world leader in providing intelligent maintenance solutions for today’s aircraft. EmpowerMX’s FleetCycle® Software Suite has been designed to assist Airlines, MROs, OEMs, and the Defense industry in the management of their assets through its four solutions – FleetCycle® AERO, FleetCycle® MRO, FleetCycle® OEM and FleetCycle® DEF. Each solution is built on a modular basis. Since its inception, EmpowerMX has focused on the aviation sector with most of the major US airlines now using the FleetCycle® solution.
Comments (0)
There are currently no comments about this article.
To post a comment, please login or subscribe.