Articles
Name | Author | |
---|---|---|
Predictive maintenance — beyond the buzzwords | Sander de Bree, Founder & Chief Visionary, EXSYN Aviation Solutions | View article |
Digital twins: improving the way things work and wear | Nadine Etong, Director MRO Product Line, IFS | View article |
Smartwings App helps better manage parts | Petr Barton, Operational Supply Chain Manager, Smartwings | View article |
Looking for a smarter supply chain in MRO: Part 1 | Amol Salaskar, Consulting Business Analyst in Aviation and MRO, IBM | View article |
Predictive maintenance — beyond the buzzwords
Author: Sander de Bree, Founder & Chief Visionary, EXSYN Aviation Solutions
SubscribePredictive maintenance – beyond the buzzwords
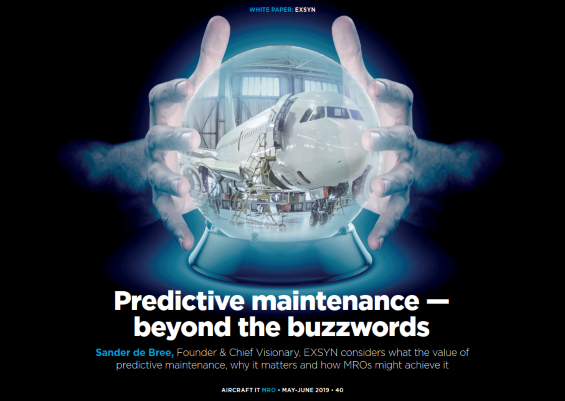
Sander de Bree, Founder & Chief Visionary, EXSYN considers what the value of predictive maintenance, why it matters and how MROs might achieve it
Sander de Bree, Founder & Chief Visionary, EXSYN Aviation Solutions
It’s a topic of increasing importance and in this article I want to share with you some thoughts and information about predictive maintenance in aviation. I’m sure that many readers will already have read plenty about the subject and its functions, using terminology such as AI (artificial intelligence), machine leaning, big data and the Internet of things (IoT) plus much besides. However, I want to offer a different perspective, not to look at the technology and what it can do: instead, we’ll put things in the context of today’s aircraft maintenance. To consider the true value of predictive analytics and predictive maintenance for the aviation industry, we’ll tackle the subject in three basic parts.
First a little about what predictive maintenance is and what it entails; we’ll then look at how it works and why that matters in aviation; finally we’ll look at some things that can be done today at airlines and MRO businesses in order to start applying predictive analytics and predictive maintenance technologies.
To start things off, some questions, which I have asked to live audiences, with their responses that offer a useful insight into current feelings about predictive maintenance:
‘Predictive maintenance for aviation: what does that mean for you?’
- Is it something to reduce cost and increase aircraft up time?
- Is it the next stage of aircraft maintenance philosophy?
- Is it completely useless?
- Is it the next hot Buzzword?
Most people in our sector would answer number 1, that it’s something to reduce cost and increase aircraft up time.
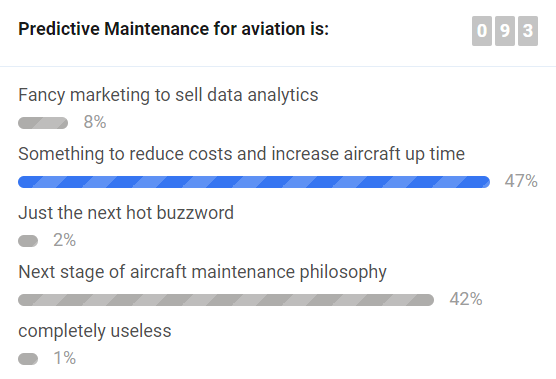
‘Which key word do you think of when you think of predictive maintenance?’
When we asked this, the sort of words that were offered included ‘big data’, ‘safety’, ‘reliability’, ‘money’, ‘machine learning’… and we’ll look back at these further on.
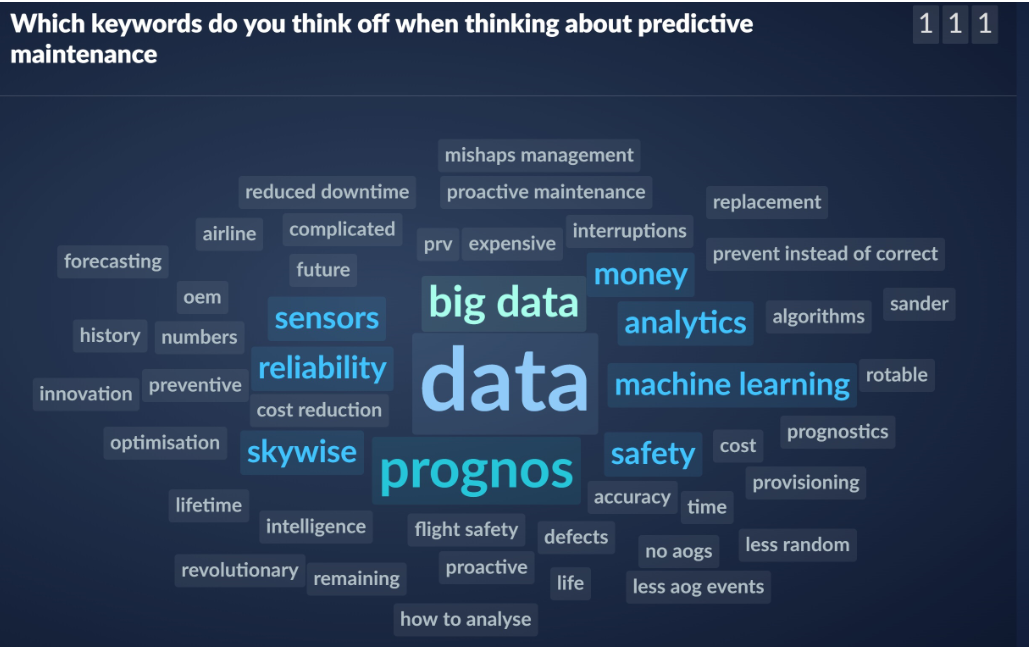
WHAT IS PREDICTIVE MAINTENANCE
Bearing that last exercise in mind and the idea that predictive maintenance is able to reduce costs and increase aircraft up time, let’s first of all look at what predictive maintenance really is in essence. If we think about predictive maintenance, it is much like a pyramid (figure 1).
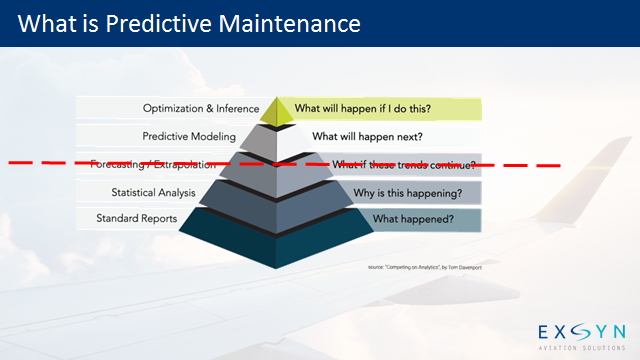
Figure 1
We are at a point, in the aviation industry where we are quite good at descriptive and analytical things such as reliability reporting… what is happening today and what happened in the past. We’re also beginning to better see what will happen if current trends continue but now we’re trying to look at what is going to happen next. If we know what happened in the past and if we know what is happening now, can we use that information to look further ahead and predict what will happen in the future?
Let’s put all that in the context of aircraft maintenance (figure 2): knowing what happened in the past, knowing what is happening today and using that in order to think about what could happen in the future.
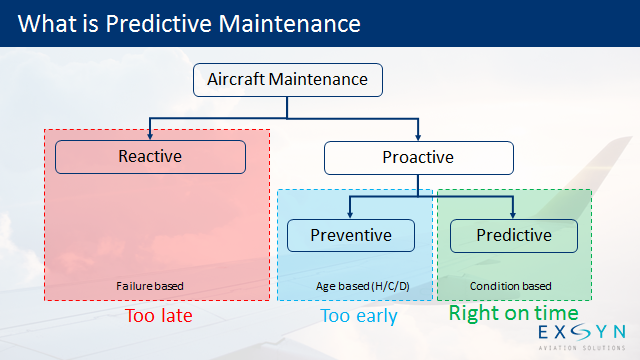
Figure 2
Not everyone will agree on this but, in this context, aircraft maintenance is, in essence, not that complicated: it’s either reactive or it’s proactive, that’s all. Reactive is failure based; something breaks down so it has to be fixed. Proactive aircraft maintenance offers two options; it can be preventive maintenance, A-Checks, C-Checks, overhaul of components, etc. or we can do predictive maintenance. The big difference between these two is that preventive maintenance, the current position of the industry, is very much age based, i.e. at certain intervals of hours, flight cycles and/or time there are checks to be performed and components to be overhauled… With predictive maintenance, the idea is to still perform maintenance but make it condition based; so rather than doing maintenance based on a certain fixed number of flight hours, flight cycles or calendar dates, we determine which condition of aircraft systems and components would justify performing maintenance actions.
In short, reactive maintenance is too late as in AOG (aircraft on ground) situations; preventive maintenance means that you’re doing some jobs too early; but predictive maintenance tries to do maintenance right on time: So there is a sound philosophy behind doing maintenance based on condition monitoring.
If condition monitoring is that important for predictive maintenance, how can we monitor and measure the condition of aircraft systems and of components installed in the aircraft to ensure that maintenance is carried out on time rather than being reactive and waiting for them to break down? This is the million dollar question of our time.
The answer is very straightforward: there are two options. The first option is to put as many sensors in an aircraft as it is possible to do, as these sensors will allow users to measure the condition of systems and components (figure 3).
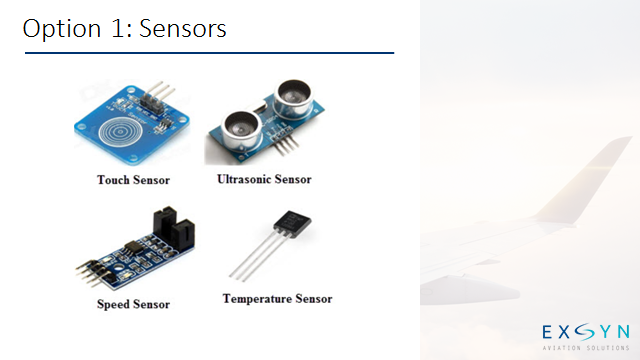
Figure 3
A temperature sensor will measure the temperatures reached by a component at various stages in the aircraft’s engine’s operation; a pressure sensor measures pressures in hydraulic systems, etc.; so as many sensors as possible should be fitted. This is what is happening with new generation aircraft: A350, B787, B737 MAX… they’re full of sensors. However, it isn’t possible to fit a sensor on everything and not everything can be measured with sensors.
For those aircraft systems and aircraft components where sensors cannot be fitted, option 2 is to use statistical modelling in order to calculate what the condition of these systems and components could be at a given moment in time. If we put a complex mathematical definition against that, it’s determining, in time, and what the deterioration percentage ‘X’ will be over time. It uses modelling mathematics in order to calculate how we expect the condition to progress. That is, in essence what we are doing with predictive maintenance.
WHY PREDICTIVE MAINTENANCE MATTERS IN AVIATION
Pretty much since the introduction of the Boeing 787, people have been talking about predictive maintenance, data collection in aviation and suchlike. The reasons that it has become such a hot topic are the arrival of next generation e-enabled aircraft, reduced costs for data storage, increased availability of data through mobile and smart devices with the tools to access this, catching-up and spill-over from the consumer market (social media developments and consumer behavior analysis), the drive to reduce maintenance costs and more efficient use of resources.
Understanding the real value
In short, there are a lot of good reasons why predictive maintenance matters in aviation and, going back to the questions and answers at the top of the article, not least is reducing costs and increasing aircraft up time. So, there is a very valid use case for predictive maintenance and predictive analytics.
The History
Interestingly enough, I feel that the real value of predictive maintenance exists in something completely different which relates to our current maintenance philosophies in aviation and the ever increasing shortage of ground engineers.
In order to explain this viewpoint, we need to go back to the introduction of the Boeing 747 (figure 4).
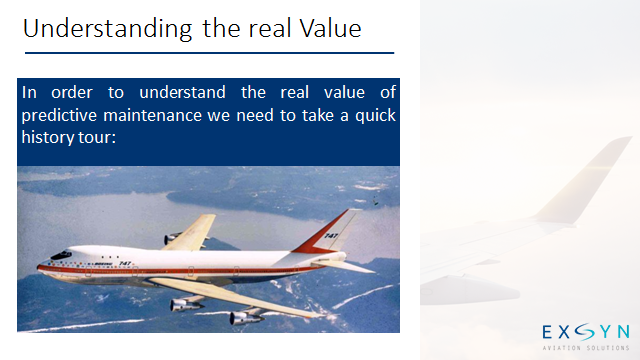
Figure 4
You might find this surprising that I’m now referring to an aircraft type that was introduced in the 1970s. But stay with me.
Age based maintenance is, in essence, a maintenance philosophy. So, when the Boeing 747 was introduced something else important happened in the aircraft MRO industry. With the 747, MSG Maintenance Programs were introduced, moving away from older to new maintenance philosophies. As a result, certain sets of aircraft components where classified as ‘On-Condition’ components and others remained age-based centric with hard-time requirements and life limits. In addition to this, airlines, under the MSG-3 philosophy, needed to monitor the performance of the ‘on-condition’ parts and the effectiveness of their maintenance. As such, modern day aircraft reliability management was born. This is actually still very relevant today as most aircraft maintenance programs are based on MSG-3 philosophy with hard-times, life-limited parts, Age-based maintenance and a number of aircraft components where there are no requirements associated with them.
The facts, the real value
In order to monitor the effectiveness of that maintenance program, it is necessary to perform reliability analyses. That’s the one thing that comes with MSG-3: if there are component that don’t have any maintenance requirements against them, it is still at least important to monitor whether maintenance is being carried out effectively. That is why ‘reliability’ was introduced. And those maintenance programs are still in the industry today: so, a significant amount of tasks in an aircraft maintenance program consist of functional checks, component replacements, etc.; all based on age-based maintenance. But what does all this have to do with the real value of predictive maintenance in aviation?
A typical maintenance planning document (MPD) would be broken down as in figure 5 with just 15 percent of work related to zonal/structural maintenance, 25 percent to components and a huge 60 percent related to systems.
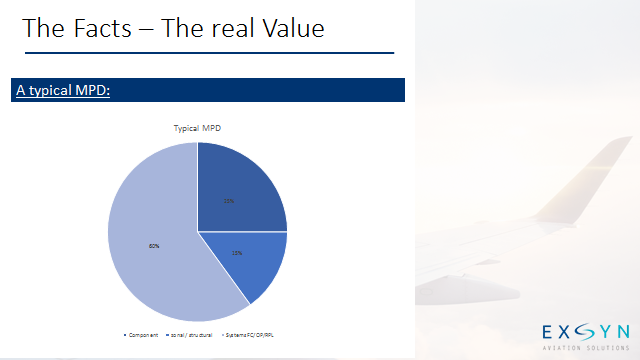
Figure 5
If readers were to look at their own maintenance program today, and run some analyses on it, they would see similar distribution.
Interestingly, for only around 18 percent of those systems and components is the age-based maintenance philosophy the right way to maintain those aircraft systems or components. For the remaining 82 percent, condition-based maintenance is much more effective. (Rio R. 2015)
In other words, there is potential to further reduce maintenance costs if we are able to monitor the condition of the 82% and only replace / repair when condition indicates that a particular component needs to be replaced. This shows us that there is quite a high level of potential value that still sits in maintenance programs today, regardless of aircraft type being operated.
Why now?
Technology and computing power available today allow us to develop sensors and reliable statistical solutions for condition-based monitoring. But there’s another important reason why predictive maintenance is becoming increasingly important. That has to do with the forecast, from ICAO, for a global shortage of Aircraft Engineers. This will require us to rethink the way we do aircraft maintenance. If we are still in a situation where we are effectively applying maintenance philosophies, age based maintenance, that are, essentially, not applicable to those 82 percent of aircraft systems and components, and there is a global shortage of engineers looming, it means people are performing maintenance activities which are not the most effective to maintain that aircraft and there is a shortage of those people anyway. A combination of issues that cry out for improvements in maintenance philosophies.
This is what predictive maintenance is about, being able to get to a point where we can do condition based monitoring on that 82 percent of aircraft systems and components for which know that maintaining them based on cycles or hours or calendar dates simply doesn’t make sense. We do it today because the MPD says we have to do it, but we know it doesn’t make sense. If that is already the case today, what might we be able to do to get started on transforming to predictive maintenance philosophies in an airline?
WHAT YOU NEED TO GET STARTED WITH PREDICTIVE MAINTENANCE
We, at EXSYN, see this as three different and distinct phases from the Reportive Airline to the Monitoring Airline to the Data Driven Airline (figure 6).
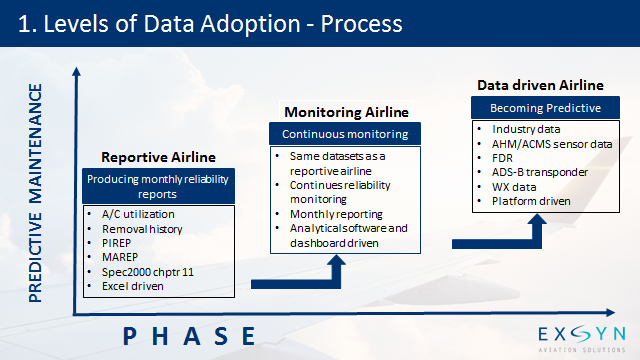
Figure 6
This diagram reflects the stages of ability of an airline to analyze what happened in the past and what is happening today; the different steps in what we might call the evolutionary ladder in order to be able to successfully adopt predictive analytical or predictive maintenance technologies. First it is necessary to look to the past and also know what is happening today, which makes up a Reportive airline. The Monitoring airline goes one step further; they know what happened in the past, they know what is happening today and they use that information to look for trends and what might happen going forward. The third step in adopting predictive maintenance or predictive analytical methodologies is to start looking beyond today. To use information from last year, yesterday; monitor what is happening today, identify trends with mathematical models and sensors in order to look beyond today and to what might happen with certain components and how their condition can deteriorate over time.
If you are interested to discover at which stage your airline stands and receive feedback what you can do next, take the free questionnaire: Are you ready for predictive maintenance https://www.exsyn.com/news/Questionnaire
This implies that data is quite important: if we’re going to monitor conditions of components in order to maintain them it’s also important to know which factors will influence that condition: which environmental conditions can influence it, which system use parameters can impact those conditions. It might be important to know several different things that an airline might not know today in order to successfully adopt predictive maintenance technologies (figure 7).
Figure 7
It’s important to know about the airline’s aircraft and fleet utilization and everything else that is needed for aircraft reliability monitoring; but it’s also necessary to have access to flight data recorder information. These are what we call ‘operational parameters’ that show how a particular aircraft has been operated or to which conditions it has been subjected. They’re the operational parameters that, in turn, influence the condition of aircraft components. That would require quite an extensive data model but, again, it’s a push towards a new maintenance philosophy. However, it comes with one big challenge and, interestingly enough, with all the different airlines with whom I’ve worked across the world, there is a common denominator which was confirmed in a recent industry survey.
For most airlines, if a technical director or head of maintenance and engineering is asked, they’ll tell you that their number one focus is predictive maintenance and that they’re putting a lot of resource, time and attention into that. Asked what is the biggest issue that respondents face and the largest response is ‘data accuracy’, the data is not that good. So, on the one hand, predictive maintenance is the highest priority while, on the other hand, data accuracy is the biggest issue that airlines face. That’s ironic in its own right; trying to use a lot of analytical, condition based monitoring technologies based on data that users don’t think is wholly reliable which, in turn, might influence the accuracy of some of these analytical models.
Of course, businesses will want to know when they might see a return on the investment into predictive maintenance and early evidence suggests that benefits of improved aircraft uptime and reduced maintenance costs, especially for unscheduled maintenance events are the early wins. The bigger benefits come when the airline is able to look at that 82 percent of maintenance programs and to improve those items which will deliver significant cost savings but that are hard to quantify as the change will be to a completely new situation in terms of aircraft maintenance philosophies.
There are some early win advantages but the main driver for those who are really serious about adopting predictive maintenance technologies is start with data accuracy today to have early-win advantages, focus on the accuracy and availability of data. That will be the foundation of being able to do successful predictive analytical modelling to get to the point where maintenance on the aircraft can be done based on the monitored condition of those aircraft and systems.
The biggest challenge is not so much data sharing, because that is just a matter of time and the removal of barriers that constrain data sharing in the industry. It will be the change that has to take place in the industry that will bring the greatest challenge. We’re accustomed to doing maintenance too early in the preventive mode and will be moving to condition monitored maintenance which means we’ll need to rely on and trust the systems and algorithms that monitor the actual condition of aircraft systems and components. That might feel like giving up a bit of security, so we need to be one hundred percent sure that the outputs and conditions monitored are accurate.
TAKE-AWAYS
So, what can I offer you to take away from this article? There are five important things that I hope you have gained.
- Sensors and statistical modelling are the core essence for condition monitoring or for condition-based maintenance.
- A looming shortage of aircraft engineers will push MRO / M&E functions to rethink how aircraft maintenance is done.
- Technology allows us to only perform maintenance when condition indicates the necessity to do so. In essence, what we are talking about is a push of the industry towards a completely new maintenance philosophy: a move towards condition-based maintenance.
- The data required to be able to properly use such models within an airline might be of questionable quality and is scattered amongst multiple different stakeholders (OEM / Airline / MRO) so, if this is to be done properly by the industry then information needs to be shared with each other: otherwise, any initiative that might be embarked upon in the area of predictive maintenance, will be destined to fail from the outset.
I hope that this has managed to clarify a few issues around predictive maintenance and how readers might begin to go about implementing it in their own businesses.

Contributor’s Details
Sander de Bree
Sander de Bree is founder of EXSYN Aviation Solutions. As founder of EXSYN he is heavily involved in business development and R&D projects, utilizing his years in the field to further drive innovation. Sander holds a degree in aeronautical engineering with specialization in human factors, airworthiness, business administration and IT.
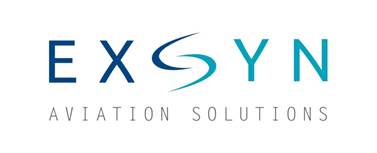
EXSYN Aviation Solutions
EXSYN Aviation Solutions is an industry recognized partner for engineering & data solutions for the aviation industry. Driven by the purpose of supporting airlines ad MRO’s to adapting to an increasingly digital aviation world, EXSYN’s capabilities have grown from a sole consulting firm to an aviation IT and managed service provider. EXSYN’s offering of applications and services is specialized for the fields of aircraft data management, data analytics & aircraft data processing.
EXSYN’s solutions are driven out of real airline use-cases and focus on aircraft reliability management, predictive maintenance, data processing and managed services for data migration, aircraft data optimization, and robotic process automation.
Comments (0)
There are currently no comments about this article.
To post a comment, please login or subscribe.