Articles
Name | Author | |
---|---|---|
Predictive maintenance — beyond the buzzwords | Sander de Bree, Founder & Chief Visionary, EXSYN Aviation Solutions | View article |
Digital twins: improving the way things work and wear | Nadine Etong, Director MRO Product Line, IFS | View article |
Smartwings App helps better manage parts | Petr Barton, Operational Supply Chain Manager, Smartwings | View article |
Looking for a smarter supply chain in MRO: Part 1 | Amol Salaskar, Consulting Business Analyst in Aviation and MRO, IBM | View article |
Looking for a smarter supply chain in MRO: Part 1
Author: Amol Salaskar, Consulting Business Analyst in Aviation and MRO, IBM
SubscribeLooking for a smarter supply chain in MRO: Part 1
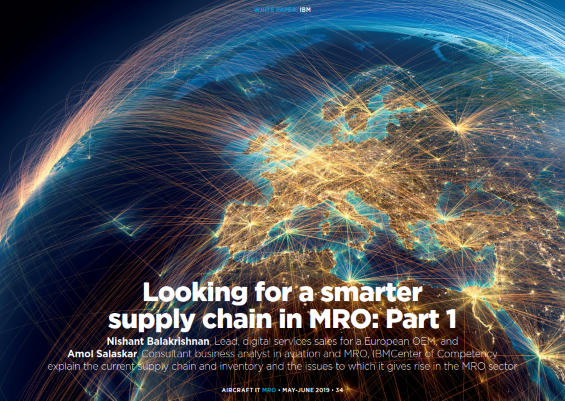
Nishant Balakrishnan [Lead, digital services sales for a European OEM], and Amol Salaskar [Travel and Transportation – Airlines & MRO, Center of Competency] explain the current supply chain and inventory and the issue to which it gives risesituation in the MRO sector
The number of airplanes is expected to double in the next 20 years to over 40,000 in-service by 2036. As a natural progression, the forecast is for an increase in the need for after-market services. In this bargain, the MRO (Maintenance Repair and Overhaul) market is expected to touch almost USD 180 billion during that same time.
In terms of services portfolio the MRO’s have progressed from just airframe based services to now servicing engines, complex assemblies, components repairs, and added spares parts supply also. This is made possible through multiple strategies, such as building in-house capabilities, or by the development of integrated supply chains with third party service providers and parts suppliers.
We will see the services portfolio is also offering a richer value added proposition because of the enablement of analytics, optimization, and predictive capabilities. The objective is to delight the customer while, at a fundamental level, recognizing the need to harness data capabilities to reveal potential service disruptions, plus performance degradation on components and assemblies, even before they occur.
In July 2017, Indigo, an airline with a world record-breaking ‘first’ in an order of 250 Airbus A320neo, underwent a severe schedule breakdown. It had to cancel over 80 flights and reschedule many more in a period of one week, because it had to ground seven aircraft from its 138 strong fleet. The reason was not just technical failures in the engine noticed over a long period of time, but also the lack of availability for spare engines, and the logistics.
This is precursor to what will be the MRO’s offering: performance based value, i.e. a guaranteed uptime for components and aircraft. In order to achieve this, MRO’s will shift from just data analytics to prescriptive analytics computing enabled by IoT devices/sensors on the aircraft that can send (near-to) real-time (or on-demand) information on the health of the components, and are capable of proposing the best possible recovery procedures. This evolution is rather well complemented by today’s technology, which allows for generation, analysis and consumption of vast amounts of structured and unstructured data, that is generated by the airplane, its installed components, the OEM (Original Equipment Manufacturer), the repair shops and the airline MIS (Maintenance Information Systems).
For an airline operation, an AOG (Aircraft on Ground) support is considered the last line of defense to overcome a service disruption, and get the aircraft back to operation and flying. The role demands technical and engineering support, yet a large part of AOG support is the organization of spare-parts. As such, we see the role of AOG support changing towards a supply chain coordinator.
A key ingredient to delivering and succeeding in such an endeavor is the performance of the MRO’s supply chain, which is the main interest of this paper. However, in order to draw some meaningful insights into the aviation MRO supply chain, we need to understand how supply chains are viewed globally. In order to do so, we draw insights from IBM’s supply chain surveys. These surveys have identified that the top drivers / criteria to successfully manage the supply chain are visibility and flexibility, a lower cost of operation, an ability to manage the business risk, and include in their scope customer satisfaction enablement / experience.
In this paper we’ll visit these supply chain drivers and the challenges from an aviation MRO supply chain perspective. This paper is divided into two parts, i.e. the first part wherein we attempt to understand what these top supply chain drivers mean in the aviation MRO context, and the second part is to explore the role of technology solutions such as business analytics, advanced analytics and simulations, and cognitive solutions, to improving integration & visibility across the supply chain, gaining efficiency in operations, and finally aimed at building a superlative customer experience.
SUPPLY CHAIN TOP DRIVERS
When we speak about the supply chain, success is primarily about having the spare-part or service demanded by the customer, in the right quantity, at a right standard, at the right price and at a right time to the nearest point of consumption of demand.
In an aviation MRO supply chain there are complexities, which come from a multitude of dimensions namely, the part’s modification status, the part’s applicability to airplanes in the customer’s fleet, the material class, the lead time for procurement, repair turn-around-time, the probability of time to failure, and the part’s criticality to the operation of the aircraft.
In this section we visit the supply chain challenges but more from an aviation MRO supply chain perspective.
Visibility and Flexibility
Today’s MRO providers are offering a basket of services. These services have been developed by augmenting in-house capabilities and / or by the integration of the supply chains with other third-party service providers. In the latter case, an MRO may outsource certain maintenance/repair tasks to other vendors.
Apart from this, a global organization means that this supply chain may be spread across multiple locations and even geographies. The ability to view and monitor the supply chain processes end-to-end can be a serious challenge. This visibility would mean the spares at not just the main base but also the forward deployment depots, in transit, at suppliers and at customer sites. From a production perspective, it refers to the parts in process of repairs at in-house repair shops or at third-party repairs.
The flexibility of the supply chain is its ability to respond to market dynamics in the most efficient manner. For this there is a need for the supply chain planners to receive real-time or close to real-time inputs from within the supply chain processes and also the customers, social networks for market changes and competitors offerings.
In the present situation or business context supply chains are not able to offer uniform and consistent service to customers i.e. airlines. This results from a lack of seamless information flow, caused by disparate systems, ageing technologies, and not so easy to interface systems: the upshot is that supply chains have lost their effectiveness.
Supply chain users in various roles have not just been missing pieces of information, but have also been conflicting in nature. In the aviation MRO, we see inventory complexity arising out of parts serviceability status, the modification status, and traceability of technical data e.g. TSN (time since new), CSN (cycles since new), and TSO (time since over-haul), which are incidentally also mandatory regulatory requirements.
This variety in the data requirements for managing the supply chain, and on the other aspect the voluminous real-time sensor data coming from in-service airplanes (and components), are neither organized nor harmonized to integrate seamlessly in a way that can facilitate the drawing of insights or reacting to, if not to preempting, a service disruption in time. This also extends to developing business insights that will allow for organizational changes in the strategy. Most times the data received from the aircraft is deposited and analyzed in system that is separate from the supply chain and planning systems.
The business needs to manage the entire supply chain at a uniform cadence, and in harmony with its different parts, with data that is able to offer meaningful insights and is tailored to individuals along the supply chain. Where management is by exception, when there is a service disruption along the supply chain, the systems are not able to provide alternative course of action.
Reducing the Cost of Operation
In the present business environment, the costs or the efficiency of a supply chain is under pressure as customers demand better services at lower costs. This is made difficult with borders between an OEM, the supplier, and an MRO, dissolving as each tries to either scale their business by forward or backward integration. The business is now morphing into a scenario where it’s the performance of the supply chains between competing aviation MRO suppliers that is going to decide to whom the business will divert.
The challenge now lies not in the ability to provide services (inventory and technical engineering) but the ability to deliver on the goals of a supply chain (integrated or self-sustained), which is to offer the highest service level or remain within the SLA (Service Level Agreements) at optimal investments in spares and inventory, low working capital requirements, and the highest effectiveness i.e. ability or, more appropriately, the agility to respond to customers with tailored solutions.
The goals of a supply chain are made complex for the aviation MRO business, due to the spare-parts requirements. These requirements include inventory sizing to match the customer’s (i.e. airline’s) in-service fleets and new aircraft types that will come into operation, withdrawing obsolete parts, introducing programs for parts modifications / upgrades, and dynamically re-positioning spare-parts and services within the supply network from warehouses, main bases depots, forward deployment depots, or suppliers to the closest point of its use or potential use.
Also, for repairs, it’s to identify the shop that is capable of performing the repair and also route the part from the customer location to the repair facility and back to inventory (either internal or customer). At a strategic level one of the supply chain challenges are with the warehousing location, and the levels of inventory to maintain, when time to market are critical.
A significant part of service delivery, yet often not considered on a par with the other criteria, is the logistics costs. There is a significant lack of systems implemented that are able to optimize the way to move parts within the network and also to customer’s locations. The logistics costs can also improve the profitability of contracts and customer retention, if it can include customer business rules, embargoes, and other geo-political specific criteria that can impact the delivery time, and cost.
Managing Risk
According to IATA, a typical airline maintains approximately USD 1.9 million of inventory per aircraft, and the study also points out that most airlines want to move a large part of their inventory to supplier owned / provided inventory. With that, the cost of owning and managing the inventory will likely rest with the aviation MRO’s or the suppliers. Along with the cost of inventory is also the associated process of managing parts upgrades, obsolescence, liquidating slow-moving / non-moving inventory, and lead time associated risk of stock-outs. The overheads required in maintaining warehouses, depots, or customer sites, add to the risk for the MRO, when considered from a global perspective. Most airline customers want to move towards parts pooling, and the risk with managing the pool quality as well as knowing the parts required for the customer’s aircraft configuration is critical to the MRO supply chain to ensure that there are no cost over-runs or inventory issues.
The costs associated especially with rotables which may have re-certification requirements, or special handlings i.e. temperature controlled or ESDS (electro-static discharge sensitive) environments will also add to the management requirements. In turn, it is also important to consider the logistics and warehouse effectiveness, which will allow parts and services to be moved across the supply chain to meet the customer’s (potential) requirements.
For many of today’s airplanes e.g. the Boeing 787 which offers over 100,000 aircraft health management parameters, there are a plethora of parameters available for monitoring. However, the maintenance information systems (MIS) of the MRO/Airline M&E are not capable of consuming, organizing and analyzing this data The heath monitoring tools provided by OEMs do provide diagnostics, however, MIS seldom consumes the output of these tools. This critically enhances the risk translated to financial metrics; if we don’t have systems to effectively manage, and monitor the entire supply chain. Part of the process of managing is the support to decision making.
Customer Satisfaction / Enablement
An efficiently managed supply chain, means that its effectiveness to meet customer requirements increases. Customers receive high levels of service and satisfaction. This is most visible in the form of the performance of the contract e.g. SLA (Service Level Agreements), and the increase in revenues.
In today’s environment customers find difficulty in their ability to receive real-time updates on the progress of their requests to the MRO. Due to disconnected systems the customer receives incomplete or erroneous updates and/or the consistency of updates varies, depending on the person handling the request.
There is a severe lack of that transparency that the customer requires regarding the status of their requests, early warning when orders are delayed or prices are revised, and the ability to intervene to decide before the invoice is prepared. This leads to misunderstanding, disputed invoices, and payments from customer being delayed or forgone. Even today, a customer might not have access to a published rate card and services catalog from which a selection is possible. Lack of visibility to inventory across the supply chain, causes the customer to move to other suppliers maybe at a higher cost.
A key differentiator yet not available as a service, is for the customers to receive recommendations on services and parts supply that is most suited and cost effective for their aircraft fleet operation. In today’s environment the systems integration, and analytical capabilities required to make value adding recommendations are dependent on the customer services department, and the process for such services are time-consuming and not precise due to the lack of business insights. What is required is an agile and customer-oriented supply chain, and one that is able to tailor and offer MRO services and solutions specific to customer requirements.
Contributor’s Details
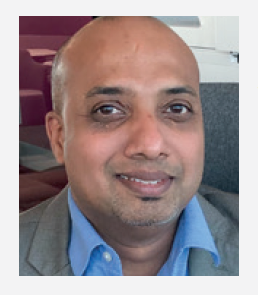
Nishant Balakrishnan is an aviation enthusiast with over 18 years of Industry experience. He has performed various roles in the industry ranging from aircraft maintenance, fleet management, inventory management, management consulting and digital transformation/sales. Currently, he leads the digital services sales for a European Airframe OEM.
Amol Salaskar is with IBM and is working as a Consultant business analyst in the aviation and MRO. Prior to that he has been a Manager Engineering IT with Jet Airways for over seven years, and for around 2 years as Business Analyst for Fleet Management Operations, with General Electric where he certified as a Six Sigma Green Belt. He holds a Bachelor’s degree in Mechanical Engineering, a Master of Science in Industrial and Systems Engineering from Auburn University, USA, and followed by a diploma in Management.
Comments (0)
There are currently no comments about this article.
To post a comment, please login or subscribe.