Articles
Name | Author | |
---|---|---|
Fair billing – realizing profits from each line maintenance job | View article | |
The World according to IT & Me! | View article | |
Case Study: Managing a Dynamic Engineering Environment in Indonesia | Ananta Widjaja, Technical Director, Sriwijaya Air | View article |
Fleet Utilization Optimization | Dr. Nima Safaei, Senior Specialist – Risk and Reliability Analysis, Bombardier Aerospace | View article |
Digital aircraft and engine lease returns | Tim Scott, Vice President Technical Services, AVITAS | View article |
Fleet Utilization Optimization
Author: Dr. Nima Safaei, Senior Specialist – Risk and Reliability Analysis, Bombardier Aerospace
SubscribeDr. Nima Safaei Senior Specialist – Risk and Reliability Analysis, Bombardier Aerospace tackles an analytical complexity; how to optimally make two interrelated decisions using one tool to improve fleet utilization.
Aircraft maintenance routing (AMR) is a challenging problem for airline operations to determine the route of individual aircraft in a sequence of revenue flight legs, so that each route will include sufficient opportunities for the required maintenance tasks to be performed. A maintenance opportunity occurs when an airplane spends a sufficiently long period at a maintenance site, whether or not any maintenance is actually performed.
In practice, AMR consists of two interrelated decisions, tail rotation (TR) and maintenance scheduling (MS), which are commonly made by two separate departments. The MS decision is to determine what maintenance should be done on which aircraft, and at which maintenance site. It also determines how to consolidate tasks as work packages and assigns them to available maintenance opportunities within the routing created by the TR decision. Airlines and aircraft operators usually use two different strategies to handle the aforementioned decisions. The first ignores the actual maintenance requirements and only considers cyclic (n-day) maintenance visits. The second schedules the maintenance tasks and plans the route of individual aircraft on a day-to-day basis, an opportunistic strategy.
Both strategies are in fact sequential approaches with a one-way interaction between the business units making TR and MS decisions separately. Such strategies cannot help the airlines to maximize their fleet utilization and to reduce operational costs; since those strategies are both favoring ‘feasibility’ over ‘optimization’. In other words, the inefficiency resulting from the lack of interaction between TR and MS decisions, along with unforeseen day-to-day events, do not allow airlines and operators to control their operations in an optimal manner. Instead, they have to just look for feasible scenarios. This shortfall results in several opportunity costs including:
- A low level of fleet utilization (staggered aircraft usage, non-revenue flights, too many maintenance visits, a lack of spare aircraft, etc.);
- A high level of fluctuation in the maintenance workload (exaggerated peaks and valleys);
- A high level of early maintenance and thereby the cost of extra maintenance activities due to lack of maintenance opportunity;
- A low level of maintenance task yield (percentage of the task interval satisfied);
- Insufficient operational buffers for aircraft swapping and resources availability for unforeseen events.
Chicken or egg dilemma
From an operational point of view, there is an inherent interrelationship between TR and MS decisions. The MS decision is a function of the aircraft’s usage dictated by the TR (especially for low-interval tasks and routine checks); while, the TR is restricted by the maintenance constraints dictated by the MS decision (especially for high-interval tasks and heavy checks). A straight solution to tackle this interrelationship is a sequential methodology which first projects the maintenance tasks due, using a baseline aircraft usage rate; secondly it schedules the tasks; and, finally, feeds them to the TR engine as maintenance constraints to create the routes. This one-way methodology does not guarantee that the created routes are always feasible for the projected maintenance demand; however, it does create a ‘chicken or egg’ dilemma: do we make MS decision first and then TR or vice versa?
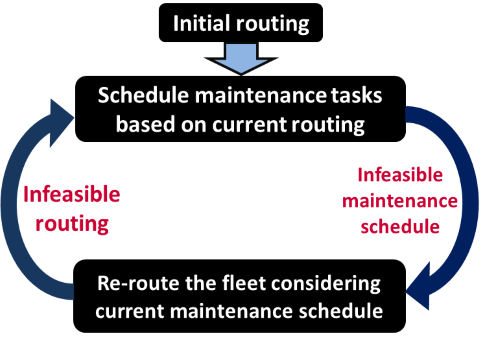
Cyclic rosters are not efficient
As a common practice, one way to tackle the above dilemma is to create cyclic maintenance rosters; that is, each aircraft should undergo maintenance every n days. However, the variety of maintenance tasks, ages and utilization rates of individual aircraft means the maintenance workload of the fleet may completely differ from one period to another. This, together with the variety of resource requirements (time, labor, tools, spares…) for different tasks, will constrain the way we build cyclic maintenance rosters.
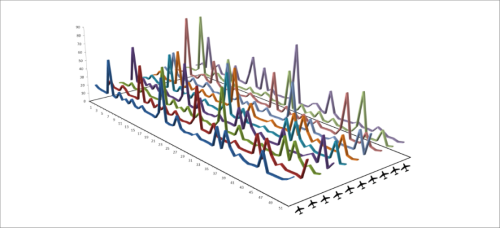
Computational complexity
The ideal methodology to cope with the above dilemma would be to make both TR and MS decisions at the same time. To this end, we would need to create and track the route of each individual aircraft concurrently for different maintenance tasks using various flight attributes (e.g., flight hours, flight cycles, time–calendar, etc.), resulting in a very complicated mathematical problem.
Proposed methodology
Within Bombardier Aerospace we have tackled the above complexity by proposing a new decision model to integrate the TR and MS decisions using an interactive optimization mechanism. The decision process is prompted by an initial Maintenance Workload Due (MWD) projected assuming the Equalized Fleet Utilization (EFU) scenario. The EFU refers to the scenario in which all tail numbers have the same usage rate over the planning horizon. Then, the TR is solved to generate the aircraft routes, providing sufficient maintenance opportunities to satisfy MWD as much as possible. If there is still a maintenance misalignment meaning that the MWD cannot be fully covered by the TR’s solution, the MWD is re-generated using the most recent routing solution and the process iterates until no further reduction in maintenance misalignment is possible.
The MS decision is then solved to schedule the individual due tasks into the maintenance opportunities provided by the TR decision. In the case of a lack of feasible schedule, the model tries to minimize the overflow; a part of MWD which cannot be performed over the planning horizon due to maintenance misalignment. The overflow is moved back to the previous periods as premature maintenance. Otherwise, the TR will be solved again by penalizing the routing solution on-hand. The penalization avoids the TR model to generate the same routing solution as the previous one. The proposed model uses state-of-the-art analytical methodologies and powerful algorithms behind the scenes to run the decision process.
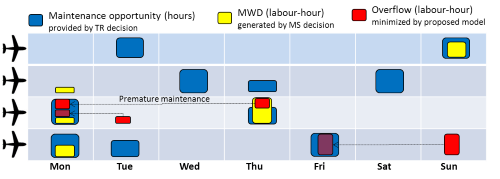
Benefits
The implementation of the proposed methodology through Monte-Carlo simulation on three fleets and associated flight schedules related to various airlines reveals significant efficiency and positive financial impacts:
- The number of non-revenue flights reduced by about 50%.
- An increased yield of line maintenance checks by 15%; resulting in respectively 70 lesser routine checks per year. This is equivalent to 100 hours more annual uptime per tail number.
- The opportunity to insert potential revenue flight legs to the current schedule considering the current fleet; resulting in a 20% potential increase in the net revenue and 22% increase in the block time per tail number.
- The capability for swift re-planning in the presence of unexpected events.
- Automated data integration with a high visibility for management (aircraft routing, scheduled checks, unscheduled maintenance, delays, cancellations, diversions, non-revenue flights…)
- Capability for learning from historical observations to forecast the future for strategic-level decisions.
Monte Carlo method
Monte Carlo methods are a broad class of computational algorithms that rely on repeated random sampling to obtain numerical results. They are… most useful when it is difficult or impossible to use other mathematical methods. Monte Carlo methods are mainly used in three distinct problem classes: optimization, numerical integration, and generating draws from a probability distribution.
The above mentioned financial impacts are in addition to the time savings resulting from the reduction in manual planning, paper work, quality control, and entering/reviewing data. Obviously, a greater level of cost saving is achievable for the larger fleets.
The proposed model tries to minimize the overflow by ensuring that the right aircraft is in the right place at the right time to undergo maintenance with the least operational costs. This provides for greater fleet availability and less aircraft grounding over the long-term through the reduction of maintenance visits and the efficient usage of maintenance opportunities. During the course of heavy checks, the proposed methodology can be also used to stagger fleet utilization with the aim of covering the master flight schedule with the minimum delay and deviation. All of the above advantages reflect an optimized fleet utilization.
Contributor’s Details
Dr. Nima Safaei
Nima Safaei received a Ph.D. degree in system and industrial engineering from Iran University of Science and Technology. He held a postdoctoral position at the Center for Maintenance Optimization and Reliability Engineering (C-MORE), University of Toronto. Nima is currently with Department of Maintenance Support and Planning, Bombardier Aerospace as a Senior Specialist. He applies the advanced optimization methods to solve the challenging problems in aviation industry and airline operations.
Bombardier
As a manufacturer of planes and trains, Bombardier has an extensive and diverse portfolio of mobility solutions. Everywhere people travel by land and in the air, a Bombardier product is ready to transport them. From business jets and commercial aircraft to high speed trains and public transit that’s smarter than ever. But it’s not just products and services; the most important success factor is 74,000 employees focused on making mobility more efficient, sustainable and inviting than ever before.
Comments (0)
There are currently no comments about this article.
To post a comment, please login or subscribe.