Articles
Name | Author | |
---|---|---|
CASE STUDY: Sky Airline finds more efficient way to plan flights and save fuel costs | Yonathan Perelmuter, Chief Technical Pilot, Sky Airline | View article |
CASE STUDY: Jekta gets the latest in digital documentation | George Alafinov, CEO and co-Founder of Jekta and Marc Rauch, co-Founder and CBO of Yonder | View article |
CASE STUDY: The Blueprint of a Digital Fueling Process | Christian Mietz, Emissions Monitoring & Fuel-IT at Deutsche Lufthansa AG and Claudio Corfú, First Officer Boeing 777 with SWISS International Airlines | View article |
CASE STUDY: Introducing and integrating a new performance solution at Air Nostrum | Juan Diaz, Head of Flight Support, Air Nostrum | View article |
CASE STUDY: Real-time flight path optimization at Volaris | Luis Fernandez San Miguel, Fuel Efficiency Manager, Volaris and David Rytter, CEO, AVTECH | View article |
CASE STUDY: Viva Aerobus gets to grips with digitally powered fuel efficiency | Nancy Madrigal, Head of Fuel Conservation – VIVA AEROBUS | View article |
WHITE PAPER: One communications platform for all purposes | Trent McCabe – Sales Manager and SME, Smart4Aviation | View article |
CASE STUDY: The Blueprint of a Digital Fueling Process
Author: Christian Mietz, Emissions Monitoring & Fuel-IT at Deutsche Lufthansa AG and Claudio Corfú, First Officer Boeing 777 with SWISS International Airlines
Subscribe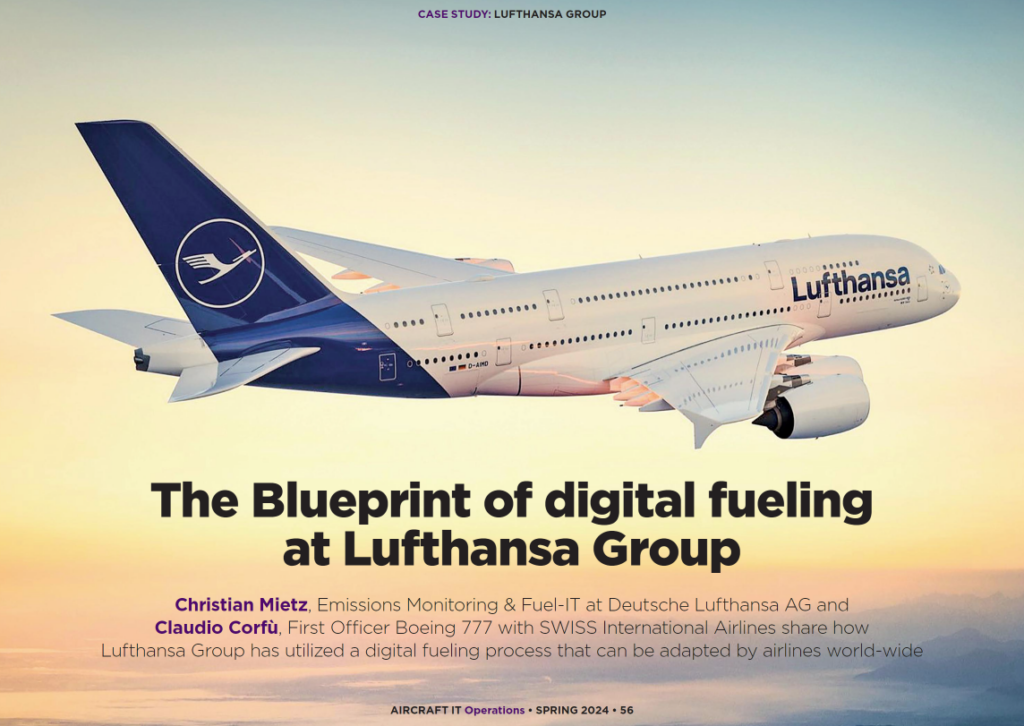
Christian Mietz, Emissions Monitoring & Fuel-IT at Deutsche Lufthansa AG and Claudio Corfú, First Officer Boeing 777 with SWISS International Airlines share how Lufthansa Group has utilized a digital fueling process that can be adapted by airlines world-wide
This case study explores the digital fueling process implemented and executed by the Lufthansa Group and its affiliate airlines. Guided by a centralized fuel management department, the program incorporates essential operations such as fuel purchasing, hedging, emissions monitoring, and reporting. It also oversees IT solutions that facilitate daily operations. The study aims to shed light on the obstacles encountered in establishing a digital fueling process that has led to more efficient and faster turnaround times, enhancing the operational performance of the Lufthansa Group’s airlines. Emphasis will be placed on the solution’s network architecture, feedback from our pilots, and the latest efforts to future-proof the digital fueling process.
INTRODUCTION
The now well-established digital fueling process at Lufthansa Group began modestly, initially implemented at our hubs in Germany where flight volume was high and relationships with into-plane companies and fuel suppliers were strong. However, quite quickly we asked ourselves how we could scale this process to more airports and other group airlines.
Before delving into the specifics of this expansion, we will introduce you to the Lufthansa Group and discuss the necessity for digitalized processes, as well as the initial IT system landscape that needed to be managed.
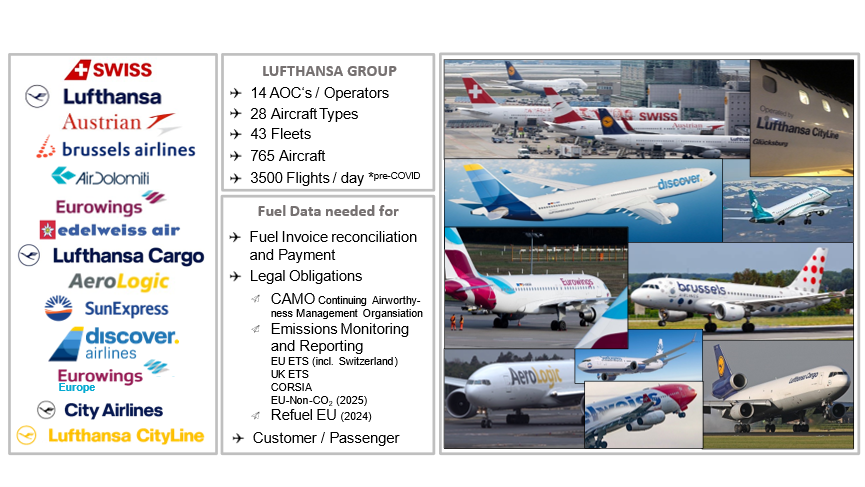
The Lufthansa Group operates under 14 AOCs managing 28 aircraft types across 43 fleets with nearly 800 aircraft. Pre-COVID, these aircraft were responsible for 3,500 flights a day, each requiring fueling. To optimize these operations and maintain stability, a highly digitalized process is essential.
However, the significance of fueling extends beyond operational concerns to the back office. Daily fuel data is critical for invoice reconciliation and automated payments to manage the sheer volume of flights. Moreover, digitalization is mandated by legal requirements, not only for CAMO purposes but also for the latest in environmental (emissions) monitoring. At the time of writing, four different emissions monitoring systems are applicable in Europe – EU ETS, UK ETS, Swiss ETS, and the global CORSIA system, with EU-non-CO2 monitoring and the forthcoming Refuel EU initiative focused on emissions and consumption monitoring. Additionally, there is a growing demand from customers for carbon footprint tracking to compensate for their flights. This multitude of reasons underscores why we collect comprehensive data.
LH GROUP SYSTEM LANDSCAPE
With many different airlines under the wing of Lufthansa Group it is common to encounter a variety of dispatch and air-ground-communication systems in use.
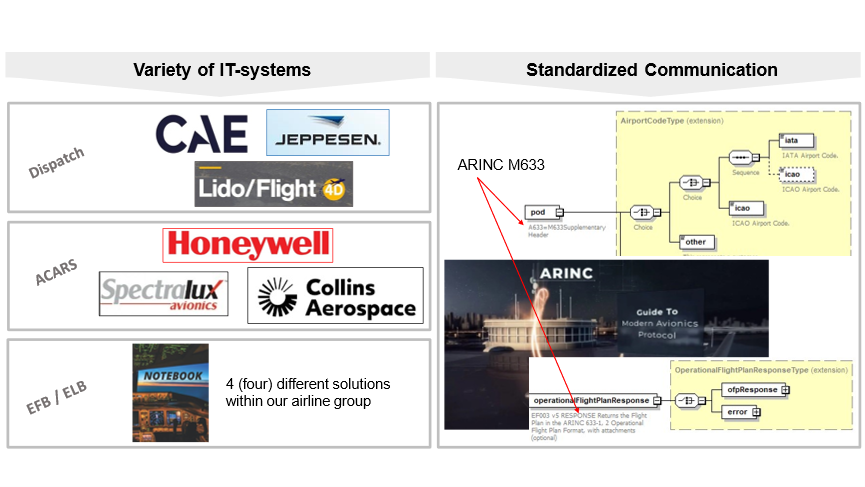
Systems like CAE, Jeppesen, and Lido/Flight are all capable of interfacing with our internal eFueling service. This compatibility extends to ACARS; we can transmit ACARS messages to eFueling through the various available systems and receive them likewise. The same holds for EFB and ELB: within the Group, we utilize four different solutions, either iOS or Windows Surface-based, all of which are compatible with the eFueling solution.
Over time, the IT landscape has become increasingly diverse. To ensure standardized communication with these varied IT systems, we have adopted the ARINC M633 standards. This standard is supported by all the solutions we use, facilitating seamless connections to back-office processes and ensuring smooth operations.
That covers the air-to-ground communication. But what about the ground-to-ground communication, that communicates the relevant fueling information to the refueling companies? For that we rely on a the AIDX data standard of IATA.
IATA – CONTRIBUTIONS AND LIMITS
For ground-to-ground communication with the refueling companies, there isn’t a standard like ARINCs M633 in place. This necessitated our search for the next best option, which we found in the IATA AIDX (Aviation Information Data Exchange) data schema. AIDX is an XML messaging standard designed for the exchange of flight data among airlines, airports, and any third parties involved in operational data consumption. The broad adoption of the AIDX industry standard has delivered significant benefits, including enhanced data quality and accuracy, increased standardization, and expedited system integration for airlines and their operational partners.
While IATA’s contribution through AIDX has been instrumental in establishing a standardized digital fueling process, it’s important to note that IATA’s role primarily involves advocating for airlines and setting global standards for safety, security, and operational efficiency. However, IATA does not provide IT solutions for establishing standardized connections between airlines and into-plane service providers. Therefore, finding or developing such IT solutions falls to the open market or must be addressed directly by the airlines themselves.
WHY USE A DATA HUB
The pivotal question that arises now is, who provides this IT solution that connects the airlines with the into-plane agent side? If each airline were to develop a separate interface for every airport or refueling company, a sprawling network of non-standardized communication interfaces would result. Considering the multiple refueling companies at many airports, the complexity and number of these interfaces could double or triple. The sheer effort required to establish and maintain such a vast array of interfaces would be impossible for any single airline to undertake alone.
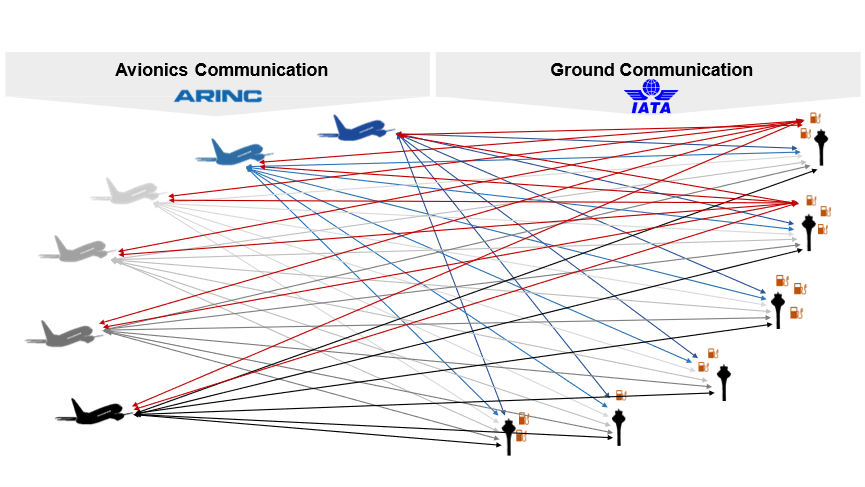
What’s needed is a centralized entity that standardizes and manages communication between both sides. Imagine a data hub, similar to the platforms we use daily for emails or services like Uber, which enables communication with everyone through a standardized protocol.
Fortunately, the market provides a solution to this gap. The product, known as aFuel, developed by Information Design One, addresses all the major challenges previously highlighted. With a single airline-facing interface, aFuel enables standardized communication with multiple into-plane agents worldwide.
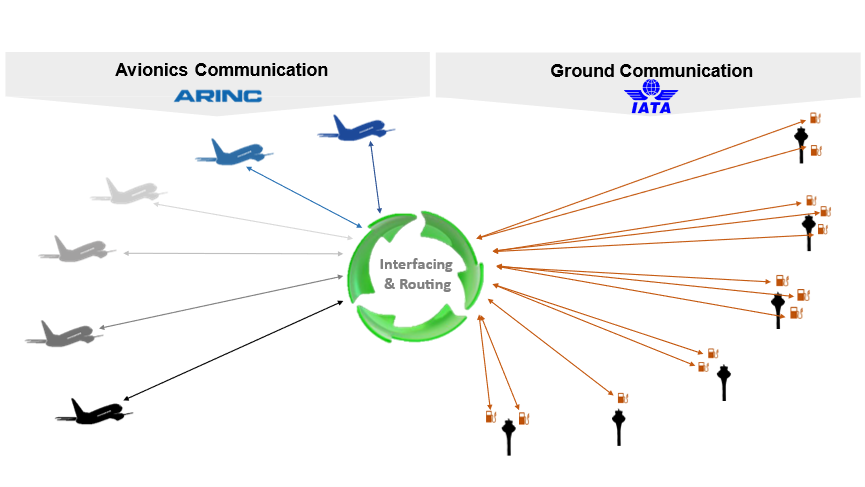
Although some internal integrations and data streamlining are necessary within an airline, the external communication is fully managed by aFuel. Airline-related systems requiring integration include Weight & Balance, ACARS, and the pilot’s EFB/ELB, among others. Additionally, downstream integrations to solutions like AVIATAR or to fuel management, emission monitoring, and data warehousing systems are feasible to enhance back-office and other operational processes.
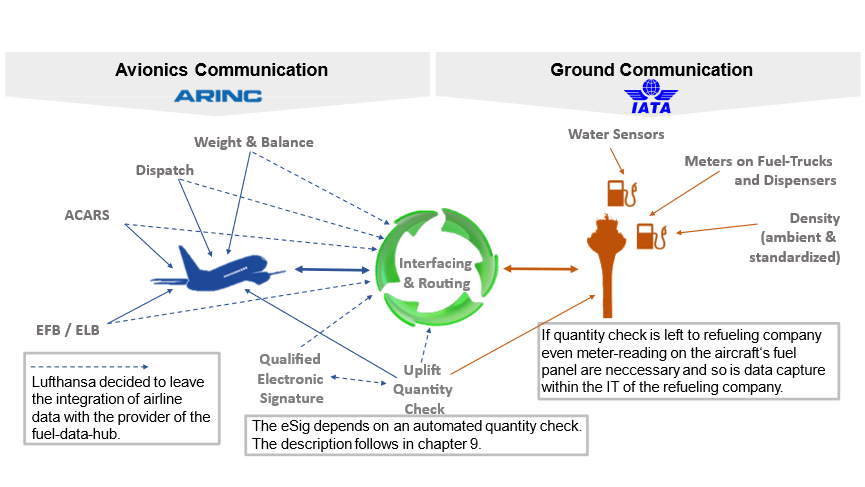
On the side of into-plane-agents, integrations are needed, which are usually done by the provider of the into-plane-dispatch-system in use. The central dispatch system integrates installations in fuel-trucks and, if in use, mobile devices, i.e. quantity meters, density meters, and more to provide the necessary information for each refueling operation.
For Lufthansa, opting to outsource the internal (airline-related) integration work to our trusted partner, Information Design One, was a strategic choice. Their extensive experience in airline data integration has allowed us to continuously improve our internal systems to adapt to changing internal and external regulations.
LUFTHANSA GROUP – AFUEL PROCESS FLOW
Now, let’s have a look at how the digital fueling process works during daily operations.
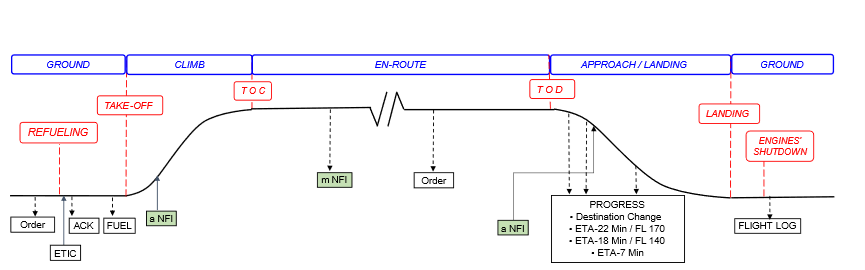
To start the process, the fuel truck driver needs to know how much fuel a flight requires. This information is transmitted electronically from the pilot, either through the ACARS module on board the aircraft, the EFB/ELB, or another mobile solution during the briefing. For wet-lease partners, we utilize a mobile solution provided by Information Design One, equipping our partners with the necessary application on short notice when full ACARS integration isn’t feasible.
There are multiple methods to send a fuel order, but all aim to directly send it to the into-plane agent’s dispatch office and subsequently to the truck driver who serves the particular flight. Once the order is received, the truck proceeds to the aircraft. Upon arrival and connection of the fuel hose, the actual fueling begins, which, despite being the least remarkable part of the process, is of course crucial. Throughout the approach and the fueling, various milestones are communicated by the truck, keeping both the pilot and the back office informed about the progress.
After fueling is completed, the truck driver issues an electronic fuel slip, which is sent via the aFuel interface to the aircraft’s ACARS module. This eliminates the need for a paper printout that the driver must hand to the pilot or handling agent. On the Lufthansa side, this is the sole part of the process fully reliant on ACARS, as only the aircraft can automatically confirm the fuel receipt instantly. This real-time confirmation includes an internal quantity check, comparing the ordered fuel quantity with the actual uplift. If the quantities are within defined thresholds, an automated acknowledgment is generated. Should there be a discrepancy, the into-plane agent is notified to print the ticket and contact the pilot directly. For airlines with different ACARS configurations or without ACARS, aFuel offers an alternative to perform a quantity check as part of its data processing.
Once the aircraft sends the acknowledgment to the refueler, the data is stored on the MCDU (Multifunction Control Display Unit) or printed directly via the ACARS printer. With the acknowledgment received, the refueling company considers the process complete. However, for internal purposes, Lufthansa requires confirmation from the pilots regarding the fuel quantity on board prior to refueling, the uplifted quantity, its density, and the fuel supplier. This information is sent in a separate message by the pilot, essential for emissions and ETS monitoring and reporting, as well as the payment process. Following this, the aircraft departs for its destination.
NO-FUEL-REQUIRED PRE-ADVICE
Having a direct communication channel with the into-plane agents even during flight allows for a more flexible handling of tankering flights, enabling the Lufthansa Group to save costs by eliminating fees for canceled fuel truck dispatches from the into-plane agents.
There are various ways to manage the so-called no-fuel indicator. Once the aircraft takes off, we can assess the onboard fuel quantity to determine whether it is sufficient for the current flight only or also for the subsequent flight. If the onboard fuel is deemed adequate for both flights, we send a No-Fuel Indicator (NFI) message to the cockpit and to the refueling company at the destination airport, cancelling the refueling service for that particular flight. This proactive cancellation translates into significant cost savings, as into-plane companies typically charge airlines for unnecessary fuel truck dispatches.
While some airlines within the Lufthansa Group rely on an automated No-Fuel Indicator, others assign the responsibility of manually initiating such a message to the pilots. In addition to the No-Fuel Indicator, we have also implemented a feature that allows sending the block fuel order for the next flight during the current flight, further stabilizing the turnaround process.
To enhance the accuracy of the automated NFI, we also utilize progress reports, a standard feature of ACARS systems. These reports keep track of fuel onboard quantities during the flight. As the aircraft approaches its destination, we use these quantities, along with the estimated time of arrival and dedicated statistics, to predict the remaining fuel consumption until on-block. If the approach is delayed, the no-fuel indicator is recalculated to verify if the onboard fuel will still be sufficient for the subsequent journey. If it is found insufficient, the NFI is overridden, and an automated message is sent to the into-plane agent to re-order a fuel truck, typically around twenty minutes before touchdown.
The statistics used for this calculation are based on a rolling average, considering fuel onboard quantities from flights over the past three months, with a greater emphasis on the most recent four weeks. This methodology gives the No-Fuel Indicator a reliability rate of ninety-seven percent, which is exceptionally high for an automated process.
The aircraft arrives and the flight is finished as soon as the aircraft is on-block, and the engines are shut-off. At this point, we again require information about the remaining fuel quantity for back-office purposes. In an ideal case the shutdown quantity for flight A will be equal to the remaining quantity before refueling of flight B. As the aircraft is the only source of information for the onboard quantities, we collect that twice.
EXPERIENCE OF THE COCKPIT CREWS
Turning our attention to the cockpit crews’ perspective, we draw insights from Claudio Corfu, First Officer on a Boeing 777 at SWISS. His experiences highlight the tangible benefits of the digital fueling process.
A decade ago, Claudio was tasked by his superior with a seemingly straightforward task: Find a way to cut our into-plane agent fees for flights to Nice. Zurich to Nice is a short flight, favored by pilots for its approaches. However, the variability in approach times, ranging from five to twenty minutes, significantly impacts fuel consumption. Given the typical flight duration of fifty minutes, pilots must decide post-landing whether the remaining fuel is sufficient for the return journey or if refueling is necessary. Conventionally, this decision was communicated to the fuel truck driver with a simple thumbs up or down, with a thumbs down resulting in an unnecessary and costly dispatch charged by the into-plane service provider. At Nice, such unnecessary dispatches could cost between 30 to 50 euros each, cumulating up to around 50,000 euros annually for SWISS.
To address this issue, a solution was devised that could be utilized at any phase of the flight – in-flight, before landing, or post-landing – and had to be straightforward to operate, considering the pilots’ workload during these times.
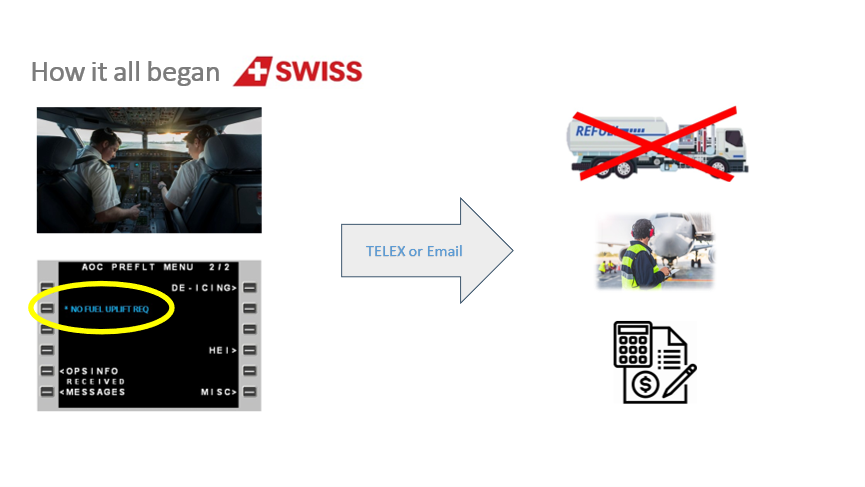
The introduction of a button that triggered a message indicating no fuel truck is required for the flight proved to be an effective solution, humorously dubbed the ‘50,000 Euro button.’ This innovative approach paved the way for updating our ACARS system. The core idea behind the update was to enable the sending of a no-fuel message not just to the flight planning and Weight & Balance system but also to the handling agent, although direct communication with the fuel truck was not yet possible.
Nevertheless, we were happy with the system but to fully understand the benefit of the system, we’ll take you a little bit deeper into how the fueling process practically works.
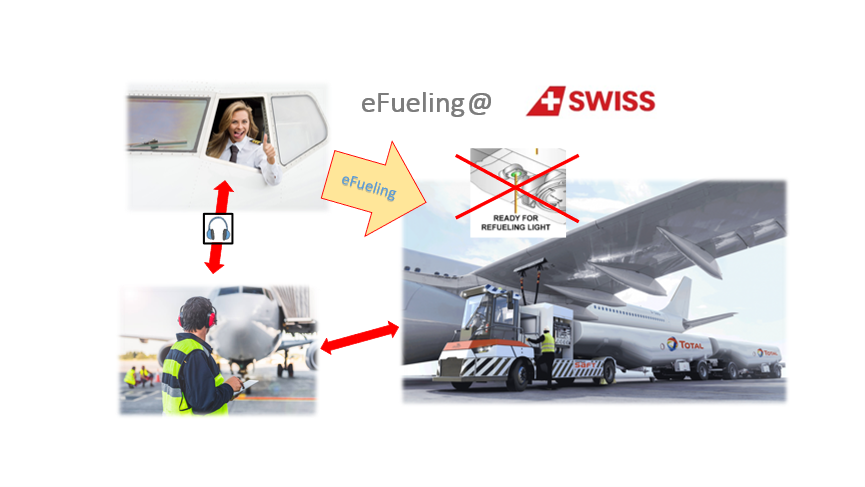
The fuel truck driver arrives at the aircraft, connects the refueling hose and uses the panel on the aircraft’s underside to enter the fuel figures. But how does the truck driver know those figures? Either the pilot opens the windscreen and communicates with the truck driver, or the handling agent does that.
The third possibility was specific to the Airbus A320 which has refuel preselect panel to preselect the fueling figures electronically directly out of the cockpit. This system also provided the capability to override and halt fueling directly from the cockpit, a critical feature in situations where fueling with passengers onboard is restricted.
This process worked very well for many years. It was simply a pragmatic approach. However, in November 2017, we were approached by Lufthansa and Information Design One and decided to adapt the aFuel process. This marked a significant leap forward, eliminating the need for verbal communication of fuel figures and introducing digital delivery of fuel slips to the cockpit. These advancements have streamlined the turnaround process, saving valuable time and resources.
The adoption of aFuel has also led to significant cost savings. For instance, it eliminated the need to purchase expensive refuel preselect panel for the new Airbus A320neo fleet, saving approximately €30,000 per aircraft. Moreover, the system facilitates pre-fueling operations, which are particularly beneficial for long-haul flights, and has dramatically reduced instances of over-fueling, even when aircraft changes occur, disrupting the planned fueling process.
BENEFITS FOR THE INTO-PLANE AGENTS
A comparative analysis between traditional and digital fueling processes, as facilitated by aFuel, was conducted by a major refueling company at a German airport. This study compared the same flight on two different days to assess the impact of digitalization on the fueling timeline (figure 9).
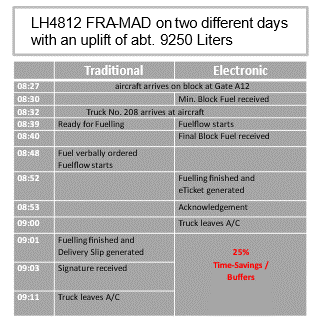
The findings revealed that the digital process is approximately ten minutes faster than its traditional counterpart. This timesaving, when applied across all refueling operations, accumulates to significant efficiencies at any airport, regardless of size.
The acceleration of the fueling process allowed this specific refueling company to optimize its fleet management, resulting in a reduction of two vehicles from their operations. Such downsizing translates into lower staffing requirements, decreased maintenance costs, and reduced fuel consumption for the trucks themselves. Consequently, airlines benefit from reduced operational costs. Furthermore, the digital process enables the refueling company to smooth out operational peaks during busy hours, thanks to the ability to pre-fuel and receive preliminary fueling information, which aids in better planning of shifts and truck utilization.
LATEST DEVELOPMENTS
In collaboration with Information Design, we are continually working to enhance aFuel and tailor it to meet both internal and external requirements. As mentioned earlier, one of the recent advancements we’ve focused on is the integration of qualified electronic signatures. Based on EU legislation, this type of electronic signature must be accepted by any organization within the EU, serving as the legally binding equivalent to a handwritten signature on paper. This development opens up new possibilities for us to extend the application of aFuel, particularly in Southern Europe.
From a practical standpoint, using a qualified electronic signature in conjunction with aFuel is straightforward. It requires a digital certificate, typically issued by a trust center or a governmental body of an EU member state. This certificate is then securely stored in an external Hardware Security Module (HSM) for enhanced security. aFuel accesses this certificate to sign the fuel slip on the airline’s behalf with a qualified electronic signature. Thus, transitioning from a traditional to a qualified electronic signature is seamless with aFuel, facilitating a digital process that aligns with local and EU-wide customs regulations.
To further improve the process on the airline side, we have integrated the eSignature process with the previously mentioned automated quantity check. This check compares the expected uplift quantity according to the difference of fuel-order minus the shutdown-quantity of the previous flight with the actual uplift quantity on the fuel slip. If the difference falls within predetermined limits, which vary depending on the aircraft and order size, aFuel automatically acknowledges and electronically signs the fuel slip. If the discrepancy exceeds these limits, the into-plane agent is alerted, necessitating a printed fuel slip to be manually signed by the pilot.
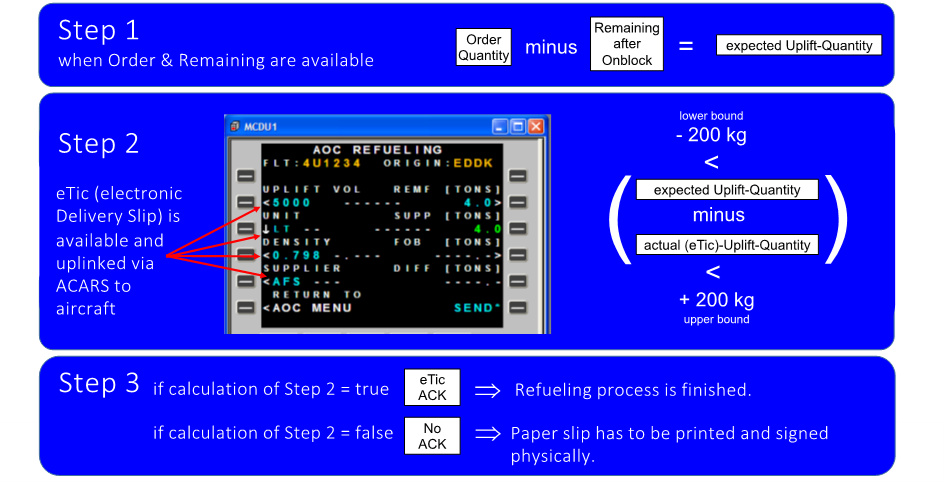
This enhancement not only streamlines the acknowledgment process but also combines the time-saving benefits of automated quantity checks with the legal assurance provided by the digital signatures, in accordance with EU legislation.
STATE OF THE AFUEL NETWORK
To conclude this case study, let’s examine the current reach of the aFuel network. As of now, aFuel is operational at 61 airports across 24 countries worldwide, with a particular focus on Europe. The extensive integration of various into-plane dispatch solutions with aFuel significantly expands the potential number of airports that can benefit from this digital fueling process.
The fact that aFuel is an open solution available to all airlines underscores the Lufthansa Group’s pioneering role in digital fuel management. Finnair and Cathay Pacific have already joined the network, sharing our commitment to broadening the aFuel network’s global footprint. As airlines, we possess the collective leverage to encourage more into-plane agents to adopt this digital process and connect to the aFuel network on a global scale. Therefore, we, as the Lufthansa Group, urge airlines worldwide to collaborate with us in making the digital fueling process powered by aFuel a global standard. We hope this case study on the digital fueling process utilized by the Lufthansa Group has provided valuable insights into the potential benefits for your airline.
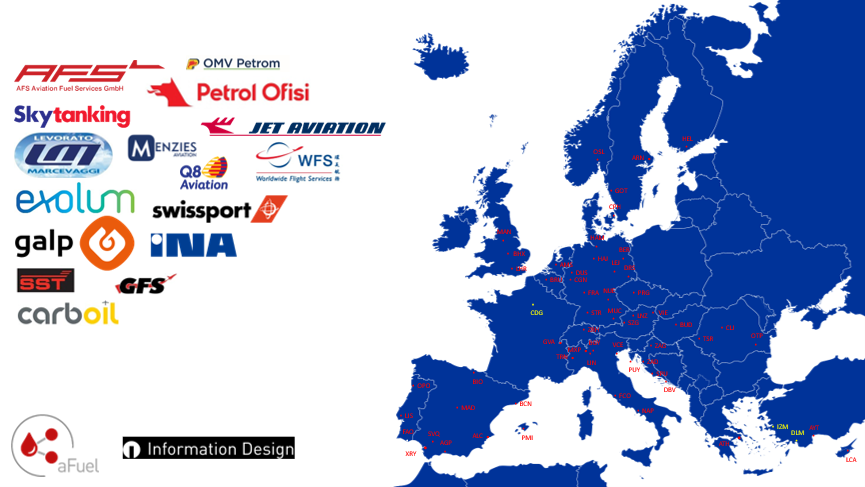
Comments (0)
There are currently no comments about this article.
To post a comment, please login or subscribe.