Articles
Name | Author | |
---|---|---|
CASE STUDY: Sky Airline finds more efficient way to plan flights and save fuel costs | Yonathan Perelmuter, Chief Technical Pilot, Sky Airline | View article |
CASE STUDY: Jekta gets the latest in digital documentation | George Alafinov, CEO and co-Founder of Jekta and Marc Rauch, co-Founder and CBO of Yonder | View article |
CASE STUDY: The Blueprint of a Digital Fueling Process | Christian Mietz, Emissions Monitoring & Fuel-IT at Deutsche Lufthansa AG and Claudio Corfú, First Officer Boeing 777 with SWISS International Airlines | View article |
CASE STUDY: Introducing and integrating a new performance solution at Air Nostrum | Juan Diaz, Head of Flight Support, Air Nostrum | View article |
CASE STUDY: Real-time flight path optimization at Volaris | Luis Fernandez San Miguel, Fuel Efficiency Manager, Volaris and David Rytter, CEO, AVTECH | View article |
CASE STUDY: Viva Aerobus gets to grips with digitally powered fuel efficiency | Nancy Madrigal, Head of Fuel Conservation – VIVA AEROBUS | View article |
WHITE PAPER: One communications platform for all purposes | Trent McCabe – Sales Manager and SME, Smart4Aviation | View article |
CASE STUDY: Sky Airline finds more efficient way to plan flights and save fuel costs
Author: Yonathan Perelmuter, Chief Technical Pilot, Sky Airline
Subscribe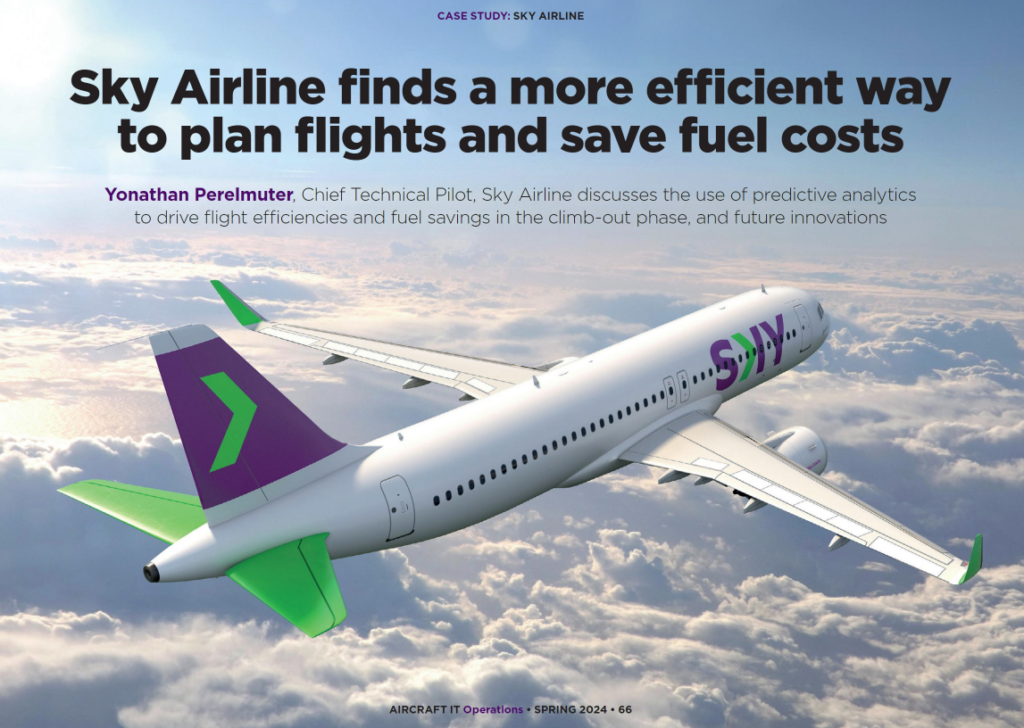
Yonathan Perelmuter, Chief Technical Pilot, Sky Airline discusses the use of predictive analytics to drive flight efficiencies and fuel savings in the climb-out phase, and future innovations
SKY AIRLINE
Sky Airline is a low-cost carrier based in Chile and Peru.
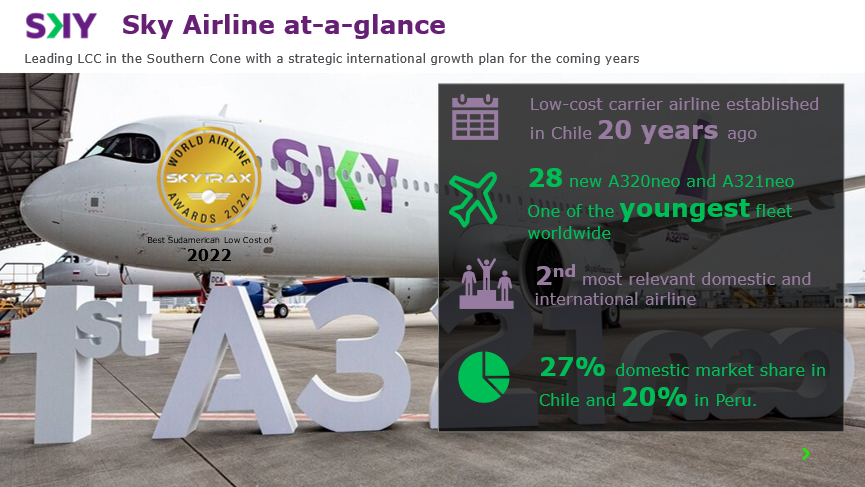
We have been operating for twenty years, now with a fleet of Airbus A320neo and A321neo aircraft. It’s one of the youngest fleets in the world and one of the only fleets that are all neo generation aircraft. Sky Airline is ranked as the second domestic and international airline in Chile with 27 percent of the Chile domestic market as well as 20 percent of the domestic market in Peru. Today, Sky Airline operates in Chile and Peru flying to most of South America as well as to Miami, Cancún and Punta Cana, with further destinations planned for the future.
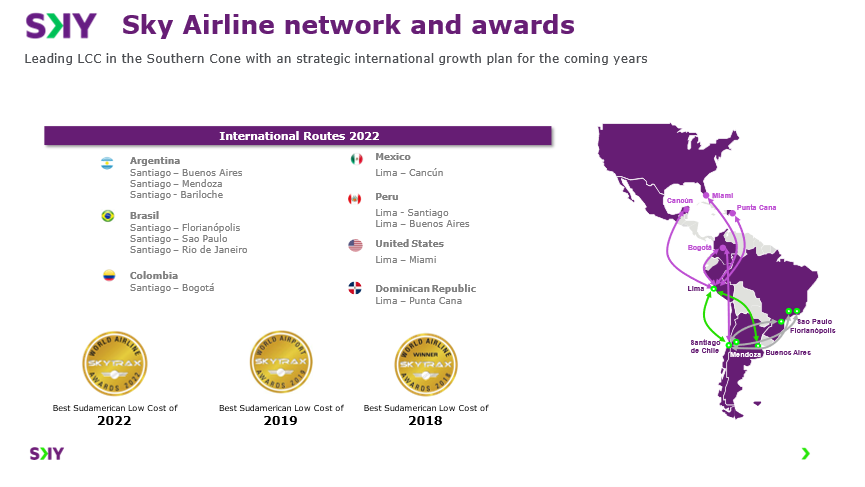
EXPERIENCE WITH SITA OPTIFLIGHT®
Sky Airline has been using OptiClimb® from SITA since the very beginning as launch customer for the Airbus fleet operating both ceo and neo generations. The solution generates a dedicated prediction and speed recommendation for the climb-out phase and our experience with it has been very positive. Using powerful data to optimize the climb-out phase, Sky Airline has achieved massive savings with minimal effort from flight crews.
Compared to other areas of the world, where Sky Airline operates, we serve airports at high altitudes, some with extreme heat and extreme humidity, some hidden between mountains. The scenario is changeable and dynamic; there are no two flights that are exactly the same. Because of that, any solution that we use also needs to be dynamic, tailored to every tail, that we operate as well as every route and every flight. Using SITA OptiFlight®, and with it being a simple-to-use solution, generated very positive feedback from pilots and today we have a steady application rate of over 85 percent rising in some months to 91-92 percent. This is very good, having the pilots believing in the value of the solution. To see how this has been achieved, we need to know how the solution has worked.
HOW OPTIFLIGHT® WORKS
When an airline works with OptiFlight®, the solution starts by building a tailored model for each tail in the airline.
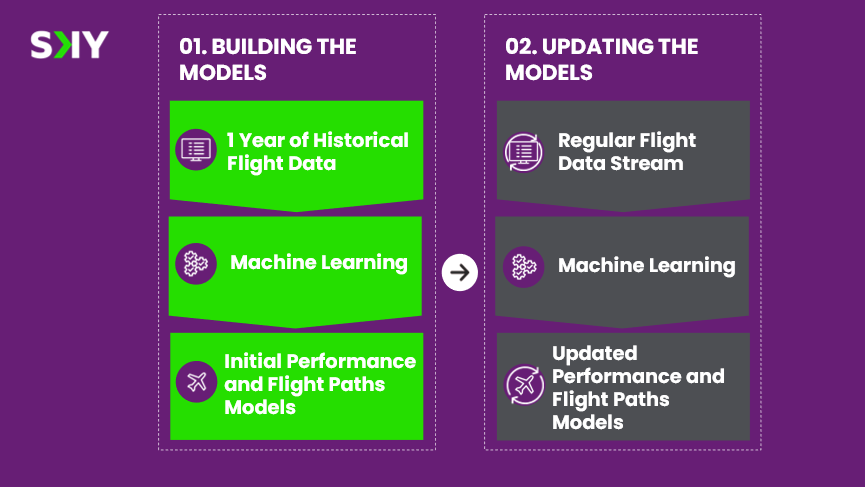
Using historical DAR (Digital ACMS Recorder) data, the software creates Machine Learning (ML) models tailored for each route and each airplane. But there is more.
Some readers might be familiar with off-the-shelf solutions where you contract the service and do the onboarding, they deliver the solution to you and that’s all; after that, you’re on your own. But, with SITA OptiFlight®, the models are regularly updated; things change depending on a number of factors like the season or the degradation of the airplane; we know that airplanes do change over time so the model needs to be adjusted over time. Also, after Covid, the way we operate, the load factor, the flights, they all changed. I can’t say that the way we looked at OptiFlight® in 2018, when we started with 13 older and different aircraft, is the same way that we look at it today. To make that clearer, let’s look at how it works.
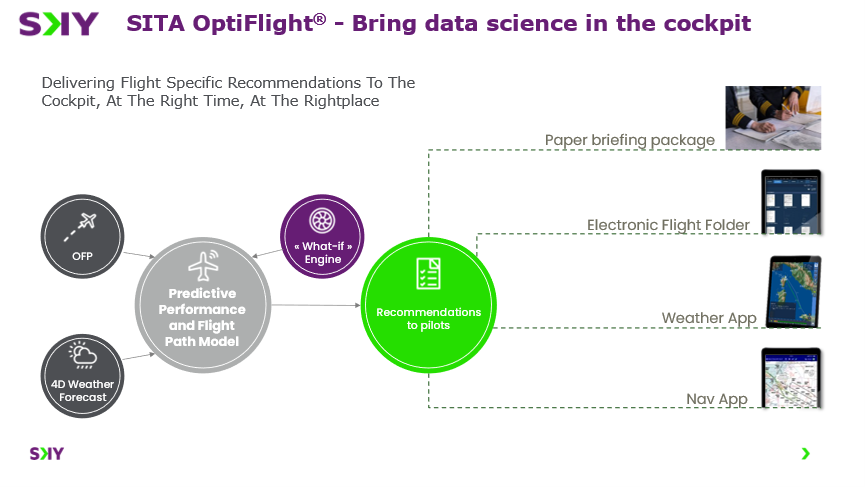
The model takes into account a lot of sources with the most important source being the OFP (Operational Flight Plan) because we need to take into account the weight of the airplane, the airplane itself and the cost factor, then assigning it to the actual model and, obviously, we need to take into account weather; the solution has a dedicated 4-dimensional weather model which is updated and refreshed, and is more up-to-date than the one used in the flight planning solution. With all that done, the solution starts running thousands of ‘what if’ scenarios looking for the best outcome for the flight in question. Once that has been generated, it takes about three to five minutes from starting the flight plan, it is sent out in various ways.
It generates a PDF file that is either physically handed to the pilot or integrated to the EFF (Electronic Flight Folder) solution. It can work with SITA’s eWAS application as well as in the chart application. At Sky Airline, we have chosen to deliver the recommendation to the EFF and I will explain below how that works. But, before that, why are we doing this?
WHY SKY AIRLINE IS USING OPTIFLIGHT®
First, looking at the climb phase, at Sky Airline, we find that the climb phase a great opportunity for saving as it is a phase that consumes a significant amount of fuel during a very short period of time and the legacy cost-index model can today be tweaked and optimized using machine learning.
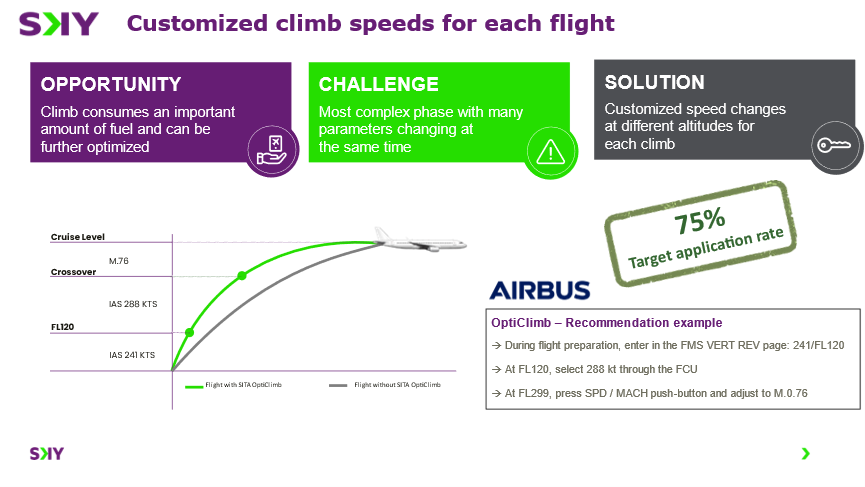
There are challenges here because that phase of flight is very dynamic with changes in temperature, in wind, in weight, various changes while the aircraft climbs as opposed to the cruise phase where conditions and the state of the aircraft are more stable with the main variable being changes in the wind. How that is targeted is with a customized climb profile dedicated for that specific flight, in that specific aircraft at a specific weight according to the flight.
The climb is divided into three phases. In the graph in figure 5, the green line depicts the OptiClimb® versus the ECON plan in gray. We can see that it is slightly curved in the early phases of the climb and then, after the first phase, which is slightly slower and slightly higher than the standard 250 flight level 100, we start a gradual acceleration through the cross-over altitude which gives the same trajectory until reaching cruising altitude. In most cases, we reach the cruising altitude slightly earlier than in an ECON climb which means that we transition to cruise parameters much faster.
INTEGRATING OPTIFLIGHT® INTO THE AIRLINE’S ECOSYSTEM
As a pilot myself, I know that pilots want something that is easy to use. They don’t want to have to use another application and they don’t want to have to call someone to request the numbers or have to look for and fetch information from different places: they want it to be seamless. To make that work, we integrate SITA OptiFlight® into Sky Airline’s ecosystem.
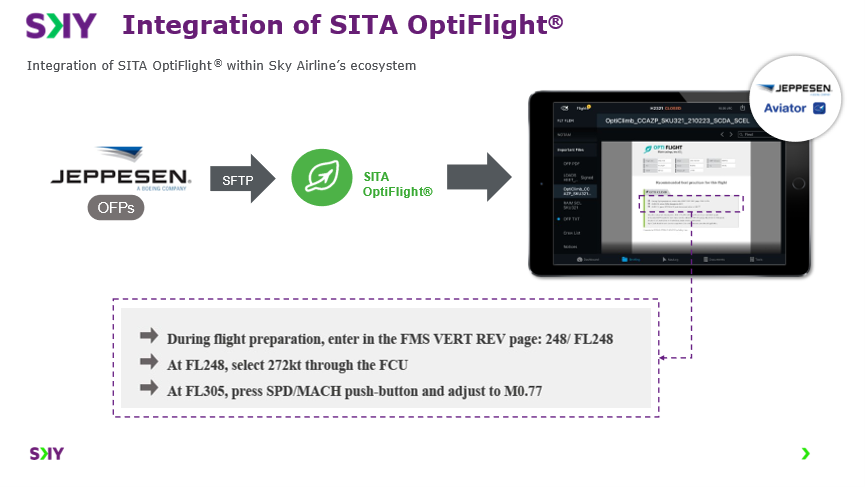
We use Jeppesen’s flight planning solution which pushes to an SFTP (Secured File Transfer Protocol) endpoint, the OFP, which is then processed and, three to five minutes after that, it is sent back automatically to be integrated with Jeppesen’s Aviator from where the pilot receives it in the EFF as just an additional file with the climb speed. And what the pilot has to do is modify the speed limitation, the vertical revision, for the first phase So, in this case, for example, it’s 248 knots at flight level 248 for a high-altitude airport (Cusco). As pilots will know, we start with a steady climb and then transition to the acceleration phase. So, how does the pilot remember when he needs to change to the next speed? Because it is the same thing as flying in regular ECON conditions; you feel that the aircraft starts accelerating and we go to phase 2. From phase 2 we go through the cross-over altitude and it’s the same again. At the end of the day, it’s a small change in the operation but the outcome, the ROI (Return on Investment) is really high.
DEMONSTRATING AND MEASURING SAVINGS
To identify savings, we compare OptiFlight® flight data with ECON flight data. We received the first neo aircraft in 2018 so have already built up more than five years of knowledge with a lot of flights that are ECON flights and a lot of flights that are OptiFlights®. So, we have established a baseline to do the natural comparison between OptiFlights® and ECON flights as long as they have the same:
- Take-Off Weight (TOW) within less than 2000kg;
- Top Of Climb (TOC);
- Departure airport;
- Tail Number;
- Temperature (Delta ISA) within less than 5 degrees;
- Initial speed at 3000 ft AGL within less than 10 kt;
- Final speed when both aircraft are stabilized in cruise;
- Wind (using air distance to cancel the wind difference);
- Fuel Factor (by checking Fuel Flow vs Altitude);
- Climb mode (by checking N1 vs Altitude).
The most important factors are the weight, the Top of Climb, the SID (Standard Instrument Departure), the airport, the tail, plus the temperature is very important. That gives us the baseline to compare the speed and altitude, the fuel factor and the fuel flow consumption for that particular flight and the climb mode.
We use two tools to make the comparison. First, a very comfortable and reliable source that we have to do the comparison is the tool that SITA provides for that purpose).
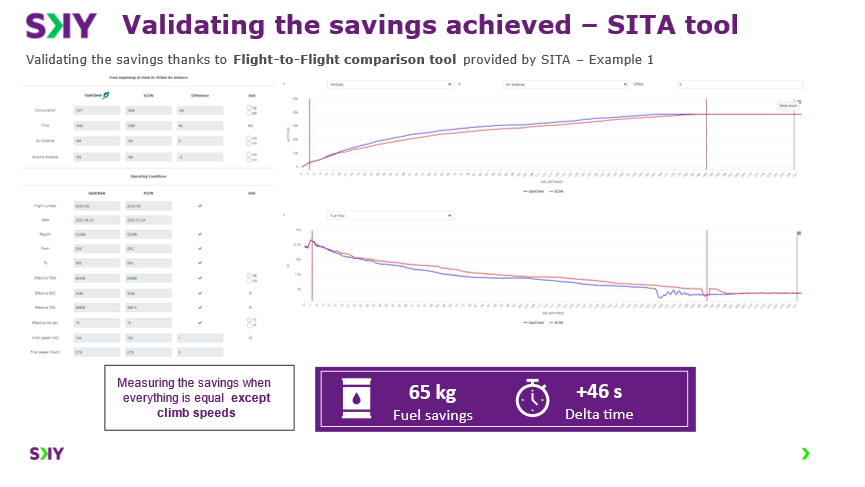
As you can see, there are two flights with which we can see the parameters and we can see a graph that depicts the actual climb. Let’s look at the bottom graph which is more interesting because the blue line represents fuel flow on an OptiClimb® while the red line represents an ECON climb and we can see that, throughout the entire climb, fuel flow was lower with the OptiFlight®. This is nice but, it is calculated by the tool supplied by the vendor. So how can we create a vendor neutral check? At Sky Airline we have our own data analytics solution, Skywise from Airbus; so, we made the same comparison using Skywise, which allows us to leverage sensor data.
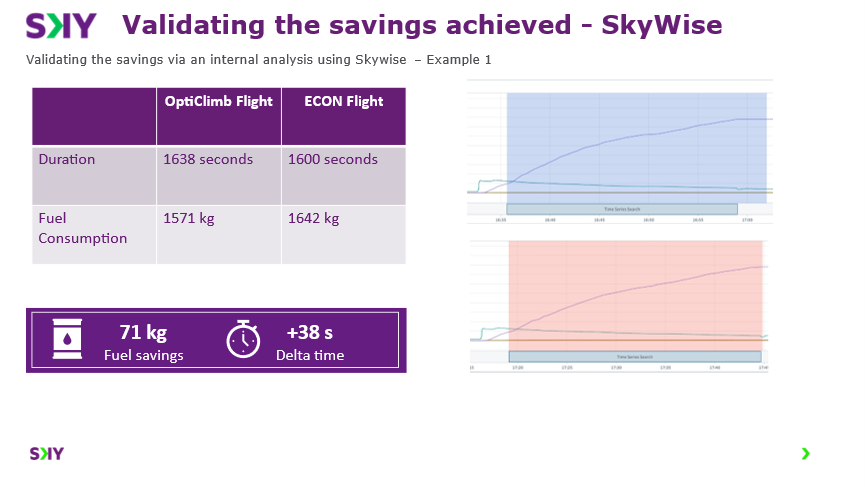
We ran the exact same comparison and reached very similar numbers with the small differences resulting from recording aircraft health complications or from the way the box records. But, overall, the two tools showed very similar savings which, for the climb in the figure were around 65 kg of fuel saved and about 46 seconds more, using the SITA tool and, using Skywise, it was 71 kg and 38 seconds. While it is very granular and manual for us to do the actual comparison, we do, from time to time, audit and validate that the savings recorded, which we receive every month, are in line with the savings that we think we have achieved.
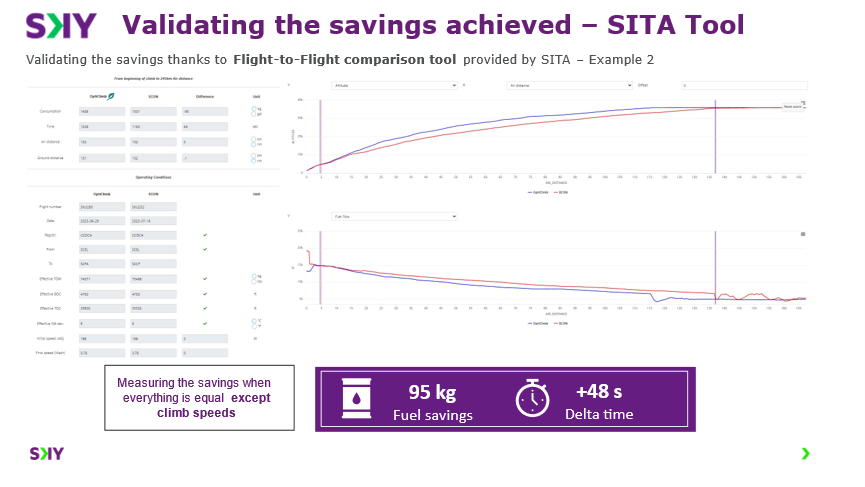
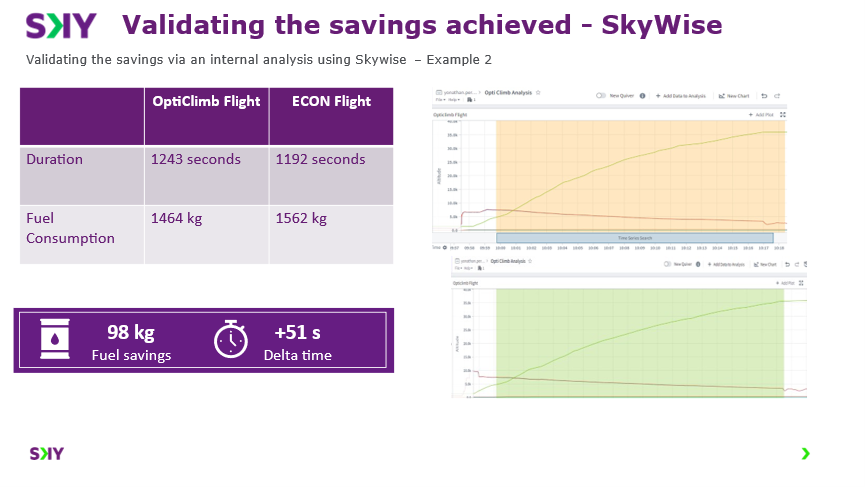
There are differences in savings and differences in when we can apply the initiative or not but overall, we can see that the data is steady and that it actually works.
Of course, while we have all of these solutions, in flying we encounter a lot of things such as ATC restrictions, noise abatement procedures, weather… there are a lot of moving parts. The way that we measure OptiClimb® is with regard to applying the entire initiative throughout the entire climb-out phase; a lot of our pilots say that, if they were requested to maintain a specific speed for a certain amount of time, after that, should they go back to OptiClimb® or from then on just follow ECON. So, we ran an analysis on that which resulted in us providing guidance that it depended on what was the phase of flight, for how long they had to deviate from the current OptiClimb® profile. For a small deviation, it’s still more efficient to go back to the OptiClimb® model rather than reverting to ECON as opposed to when the pilot knows that it’s going to be a steady deviation, in which case just deviate. The same thing happens when there is a big difference between the fuel weight in the OFP and the uploaded fuel weight, then use ECON; if there is turbulence then we adjust the speed accordingly. Given all that, Sky Airline wouldn’t suggest that pilots do anything that goes against safety: it is very important to work with the pilots because if they are not on-side with any innovation like OptiClimb®, they won’t do it.
Moving to our overall numbers, Sky Airline had 30 aircraft at the time of writing with more on order.
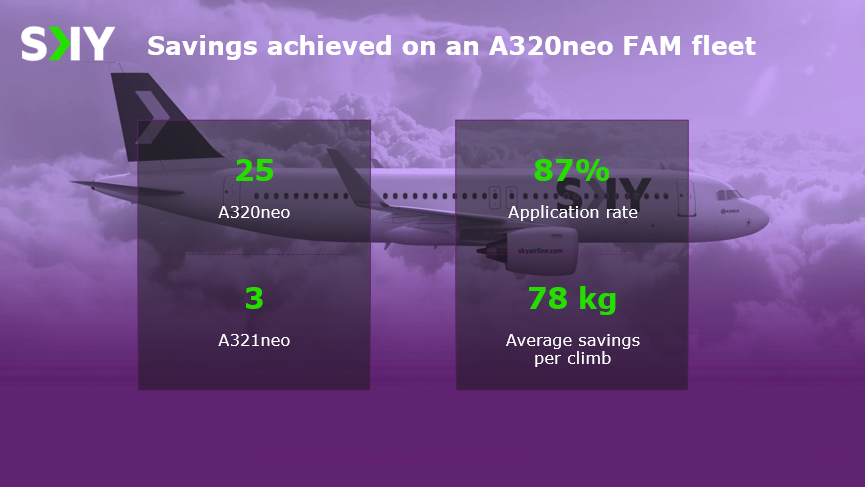
The average application rate for OptiFlight® is 87 percent over both AOCs. There are seasonal variations but we monitor those and work with the pilots because we know that if we don’t find ways to motivate them, any new solution will not work: I make no apology for emphasising this because pilot cooperation is what will make an implementation like OptiFlight® work. Here’s how we did it at Sky Airline.
Training and motivation
We started by running technical webinars; the SITA team worked with us to create a webinar which we ran together. SITA explained, to the pilots, the technical side of OptiFlight® because pilots are technically minded and like to understand the technology because that is is how they can believe in the solution; if pilots don’t believe in the solution, they won’t use it. Then we held interactive briefing sessions with the pilots. A lot of pilots told us that they’d done the climb as prescribed and that, according to their own calculations, they did not think it was a good idea so we had to demonstrate why they were wrong. We did that by looking at the tool and analysing together the particular flight that the pilot had cited. Then, we encouraged pilot feedback which is very important because that enabled us to work with OptiFlight® to tweak the model. With this, pilots feel that they actually know that what they are seeing matched with what they have seen in the aircraft. There are times when the pilots are right and it is then that we go back to OptiFlight® to work with them on improving the model.
We also do live demonstrations at pilot meetings and include an item on efficiency; it’s all part of our recurrent training program. So, when pilots start using OptiClimb® on their first day on the line, as well as their training, we have a briefing package which includes an OptiFlight® that was used when we created that flight plan and the pilots follow it. Pilots start using OptiFlight® from their first day in the company, so it’s just like any other initiative.
FUTURE INNOVATION
Throughout this article, we have referred to climb, time and again but there are, of course, more things that we can optimize and the next thing for Sky Airline to optimize is cruise.
Sky Airline started with OptiFlight® when it was an independent company but nowadays, we leverage the fact that the business is now owned by SITA, leveraging the SITA communication and ACARS communication to support a better cruise solution. We are now working on an integration with OptiLevel which leverages the cruise speed and the cruise altitude. It is similar to other solutions on the market but we know that there is opportunity, we know that there is room for optimization, we already have the models so it is something that we will be able to develop and achieve together. We know that today the FMS (Flight Management System) has certain limitations and, at the end of the day, the A320 is a relatively old aircraft type so, with all of the machine learning and artificial intelligence technologies that are available today, we know that we can leverage a little bit more than the FMS.
What do we need to think about when we’re thinking about this solution? One of the things that we, at Sky Airline, believe are key is the fact that we use tail-specific performance models plus, in cruise, the most important external factor is wind, and the change in wind and weather. It has to be a simple solution; there cannot be any human interaction involved because then it’s additional work for the dispatcher and for the pilot. As with the climb, we generate recommendations which can be transmitted through ACARS to connected airplanes but we always have the OFB and the FMS speeds to revert to. Also, if the pilot thinks that recommendation for that particular flight is wrong, they can always revert to ECON or to FMS. This integrates with various solutions, including with our previous and with our current EFF vendor. For me, every month I have to go to our management and show them that it actually works. The reporting suite is really good and the reports that are provided with the KPIs are really useful.
This has been the experience of Sky Airline with OptiFlight® and I hope it will help others considering a similar development in their planning and fuel management program.
Comments (0)
There are currently no comments about this article.
To post a comment, please login or subscribe.