Articles
Name | Author | |
---|---|---|
Case Study: Atlas Air – Paperless, that’s the plan | Andy Genao, Senior Manager, Maintenance Planning, and Michael Henry, Director Maintenance Planning, Atlas Air | View article |
Voice Technology Innovations in MRO | Scott Powell, Senior Manager, Product Marketing, Honeywell | View article |
The changing face of data | Sander de Bree, CEO, EXSYN | View article |
Information: how to get what you need | Bijoy Mechery, CEO, and Brent Heath, Senior Vice President, Seabury Solutions | View article |
Column: How I See IT – The Significance of Telepresence | Paul Saunders, Solution Manager, Flatirons Solutions | View article |
Case Study: Atlas Air – Paperless, that’s the plan
Author: Andy Genao, Senior Manager, Maintenance Planning, and Michael Henry, Director Maintenance Planning, Atlas Air
SubscribePaperless, that’s the plan
Andy Genao, Senior Manager, Maintenance Planning and Michael Henry, Director Maintenance Planning at Atlas Air share a case study in the evolution of paperless manuals and eSolutions
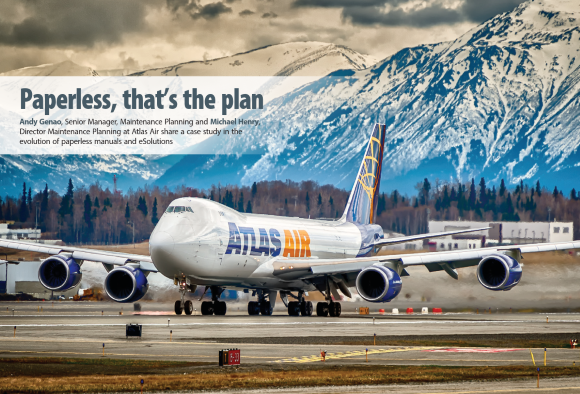
ATLAS AIR
Atlas Air has been in business since 1992, it has a fleet of 60 aircraft today with plans to grow that beyond 76 within the next couple of years. The fleet includes 41 B747s and 19 B767. The airline is also expanding its platforms with B737 and B777. The largest sector of the business is ACMI (Aircraft, Crew, Maintenance and Insurance) cargo where DHL is a major customer and partner; it also has a smaller involvement in passenger services including flying for the military and special charters. All of Atlas Air’s maintenance is outsourced to different MROs, there are inherited challenges in dealing with multiple suppliers around the world, hence the vision and goal of moving into a paperless environment in the near future.
WHY PAPERLESS?
These days, going paperless is prominent in many companies. Atlas Air decided on that direction based on the obvious management challenges of a paper workflow process… typically a document gets authored, reviewed, approved and eventually distributed. Going paperless allows that process to be streamlined, without the need to interact through paper. The interactions are instead vie more modern and sophisticated method; alerts, emails, and web portals. That, in turn, means that you can do your job from anywhere at any time – a great added benefit.
Going paperless boosts efficiency: there is a significant amount of resources and time dedicated to managing paper. Eliminating the time and effort expended in the filing and research alone will significantly improve efficiency. Data re-use is impossible and so is the integration with other systems. A paperless environment will enable users to leverage other systems and enhance their value. Like all airlines, Atlas Air uses various systems to manage its business processes: we believe that going paperless will enable us to realize the potential from those systems.
‘Going green’: this is today’s mantra. But going green is not just about saving the environment, it is also about saving the other ‘green’ stuff we call money. Many take for granted how much it costs to run a paper based process – paper, ink, toner, equipment maintenance – and how much could be saved if we were to reduce the amount of paper we print.
Increased Productivity: A paperless environment facilitates remote productivity, empowering and enabling field employees (MRO providers and field mechanics) to communicate with the company and its systems directly and remotely. With so many people working remotely these days, this capability is no longer a luxury; it’s a requirement.
Less often discussed but very important is disaster recovery. A warehouse of stored paper is vulnerable to natural disasters (fire, floods) and all sorts of risks, whereas cloud solutions already offer off-site back-up systems and archiving solutions. Companies in this sector all have established and offer protocols for backing up and dealing with disaster risks. Why not take advantage of those capabilities?
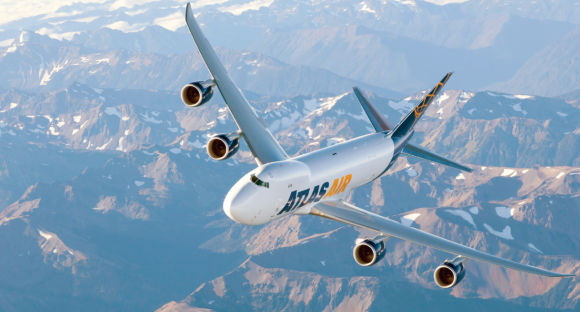
THE CASE STUDY
Process evolution
Looking at the process evolution at Atlas Air, figure 1 shows a timeline from 1999 with some highlights of what has been accomplished over that time.
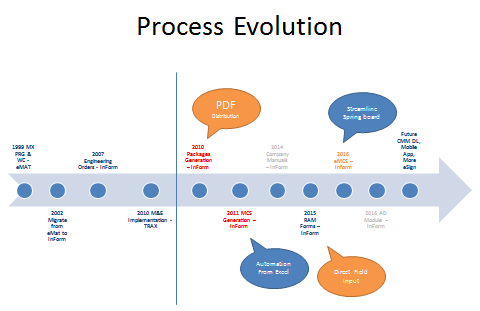
Figure 1
In 1999, we were still printing, using and processing paper from various sources within Atlas and from MRO providers. Our current M&E system is Trax, our document management solution is IDMR.. We’ve integrated those systems to create maintenance Work Orders and the supporting documents. Along the way, with the creation of digital versions of AMMs (aircraft maintenance manuals) and IPCs (illustrated parts catalogs) the ease of distribution and consumption gained traction in the industry, it was truly a revolutionary step; one that sparked how the industry now produces, distributes, and consumes technical documents.
Next, we saw the first paperless solution – PDF. While it is a limited solution, it did render some key benefits at the time, benefits of which we took and still take full advantage. The creation of PDF files allowed us to postpone and transfer the printing process to our MRO partners. It significantly cut down on our printing and shipping costs. At the end of the day, even PDFs resulted in paper, as the returned product from the MRO was and still is paper.
In 2011 when we undertook a conversion to Trax and the integration with IDMR we looked at the gaps between what we had in our M&E system and the documents we wanted to get out to maintenance. That’s where our MCS (maintenance control sheet) comes into play. The MCS (sometimes known as an accountability sheet or a tally sheet) is to control, measure, and audit the accomplishment of a work package’s task cards. At Atlas Air and, I’m sure, in other airlines, it’s a live document with revision controls to keep track of and account for changes. For us, on a C check there might be ten to 45 changes within the life of that service, with revisions driven by changes to multiple routine documents (EOs, TCs), non-routine findings, along with changes to the check work scope. From a paper standpoint, that creates an issue because physical signatures are recorded on an ever-changing MCS document. Revisions to the MCS force us to reprint the MCS and re-capture those signatures. The creation of the MCS was a manual process until 2011 when, via the integration between Trax and IDMR, we automated this process. Not having to manually create the MCS has eliminated the inherent errors of data transposing and cut our resource effort by as much as 48 man hours per C and D check work orders. That was a huge step for us. Now the planner can concentrate on value added tasks as opposed to spending time copying and pasting.
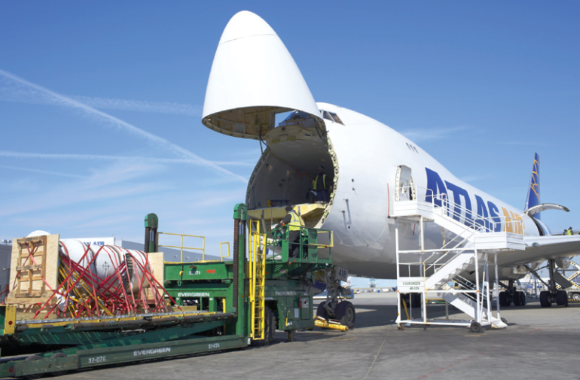
Last year, Engineering at Atlas Air rolled out their eRAM (Electronic Repair and Maintenance) form. We have an engineering process in which the MROs provide feedback to Atlas about what they have repaired, including all findings, pictures, etc. That used to be a PDF/paper process managed via emails. Now it’s all captured and delivered through a web portal where the MROs go directly into our system, fill-out the eRAM and push a button. That data goes back to engineering who are triggered to process their reviews, give their approval and issue paperwork. When engineering decided to do that, other departments were encouraged to deploy similar solutions, which led to the eMCS (Electronic Maintenance Control Sheet), the phase that will act as a springboard to the next generation of e-solutions at Atlas Air.
Figure 1 shows just a simple timeline of how the process has evolved at Atlas Air including plans for the future. In 2016 the development and deployment of the eMCS will get rid of all the intricacies and difficulties that are associated with managing an ever-changing revision controlled document that needs to be returned to planning in a timely manner. Also in 2016, Atlas Air plans to apply the same techniques to ADs (Airworthiness Directives) tracking and AD reporting. The same advantages will be deployed to the CMMs (Component Maintenance Manual) via a Data Library module, mobile applications and more eSign solutions.
Challenges
Among the challenges that we faced in this transition process was synchronization, internally within Tech Ops and externally between providers. In this, it made sense for Maintenance Planning to take the initiative. Maintenance Planning is the bridge between Tech Ops and the MROs. This allows for internal feedback to improve engineering processes and for a push to MROs on new solutions.
There are competing priorities and projects being worked on by different departments. In the past six years Atlas Air has implemented four additional maintenance programs along with the addition of over 20 aircraft to the fleet. That has bogged down engineering as they try to make improvements while expanding and changing the maintenance programs and related task cards.
We also recognize that MROs don’t only deal with Atlas Air; they have other customers with similar needs and priorities as well as their own procedures to contend with; so an MRO might not be immediately ready to implement the new Atlas Air processes, which means they have to be synchronized in at an appropriate time.
Then there’s adaptability or change management – how people accept and adapt to changes. Although it will be different for each individual, department and organizations; it’s always a challenge. The new process has to be explained and resources helped along so that it can be adapted and used. Which leads us to process recovery, making initial changes is not always the final solution. There are feedback channels that have to be established that will enhance and push tweaks to the process. All this takes time and resources which, in itself, is a challenge.
Outlook
With so many issues to contend with as we’ve progressed from paper to Excel, to PDF, we are now ready and willing to get eSign: putting it all together, going full circle, creating a self-sustainable process (see figure 2).
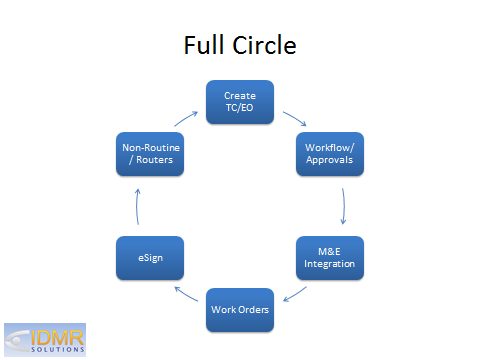
Figure 2
The eMCS (see above) now produced electronically through the integration of our two systems is still a paper-based document. Our solution is to take it a step further, to generate the MCS electronically and have it signed-off electronically: enhancing all the features, security and delivery options obtain by going fully digital. That will resolve a number of the issues we have today with paper; no longer having to worry about issuing a revision at the last minute and in doing so starting a paper re-print circus. Now that it’s an electronic document it can be changed in whatever way necessary while maintaining signature history and completion status.
In the past the industry has regarded eSign as a pipe dream and yet nowadays, the big topic in the industry is ‘going paperless’, it’s now attainable. So, what is eSign going to do for us?
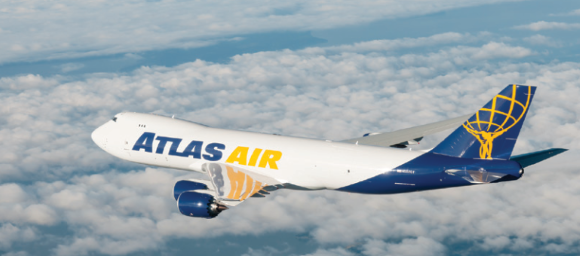
It’s going to open the door to an array of opportunities, real time task card data capturing being among the top benefits. Task specific parameter capturing will provide the airline with tons of useful data on which to evaluate and make decisions. Airlines will have the data to make the operation safer and more efficient. We can analyze the process and the individuals implementing it; expand on the strengths and shore up the weaknesses. It’s possible to identify trends and implement fixes. All of this can be managed through dashboards which we use today for documentation, manuals, etc.… once the data is available, there’s no limit as to what it can be used for.
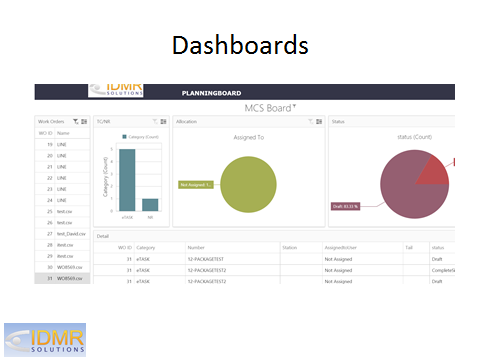
LESSONS LEARNED AND RECOMMENDATIONS
These changes have to be a reform not a revolt. The business culture has to change as part of going paperless, but not in a revolutionary forced way; rather, leadership has to listen to what employees and partners are saying and make the change as a reform driven from the top. There has to be a long term vision, one that can be shared by directors and managers both internally and with business partners.
A sensible approach makes for more sustainable progress: nothing happens overnight and pushing changes of this magnitude onto people doesn’t work. It has to be incremental, using small steps to ensure continual progress expansion and improvement.
Finally, partnerships are important; they are the relationships that work best whether with vendors, suppliers or employees; working together.
Contributor’s Details
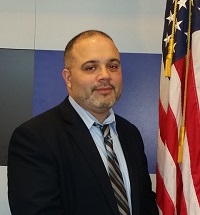
Andy Genao has spent 17 years in the aviation industry, primarily in Technical Operations. Andy started his aviation career in 1999 with Atlas Air, in 2003, he joined jetBlue where he held various positions. In 2007 Andy joined an M&E System provider (RAMCO), in 2010, he returned to Atlas and has concentrated on aircraft acquisitions and system phase-ins, maintenance planning, Engineering and continual process improvement projects.
Michael Henry has spent the last 19 years in the aviation industry, primarily in Technical Operations and is the Director of Maintenance Planning at Atlas Air. He started his aviation career in 1997 with KIWI International as a Technical Librarian and then moved on to planning. In 1999 he joined Atlas Air as a maintenance planner. Since then he has held positions as a maintenance planning manager and Director since March 2009.
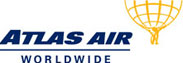
Atlas Air Worldwide Holdings is a global airfreight business which started in 1992 and has experience serving the airline and freight industries, commercial and military customers. The carrier deploys a largely wide-body fleet of 58 aircraft, B747 and B767 variants, and boasts the world’s largest fleet of modern Boeing 747 all-cargo aircraft.
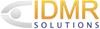
IDMR is a global provider of Technical Documentation Management Solutions for Fleet operators, MRO providers and OEM organizations. IDMR’s Solutions have proven success in increasing operational performance and decreasing operational cost while insuring airworthiness, safety and regulatory compliance at multiple airlines. The vendor offers a range of Maintenance and Planning, Records, Flight Ops, and Ground Ops products and can develop customized applications if required.
Comments (0)
There are currently no comments about this article.
To post a comment, please login or subscribe.