Articles
Name | Author | |
---|---|---|
Case Study: American Airlines addresses repetitive faults with data | Karl Ries, Senior Manager Tech Support Desk Maintenance Ops Control, American Airlines | View article |
Industry Standards: an ATA perspective | Ken Jones, Director Electronic Data Standards, ATA e-Business Program | View article |
Case Study: Alaska Airlines takes control of inventory | Jim Parish, General Manager Material Stores and Distribution, Alaska Airlines | View article |
Case Study: American Airlines addresses repetitive faults with data
Author: Karl Ries, Senior Manager Tech Support Desk Maintenance Ops Control, American Airlines
SubscribeAmerican Airlines addresses repetitive faults with data
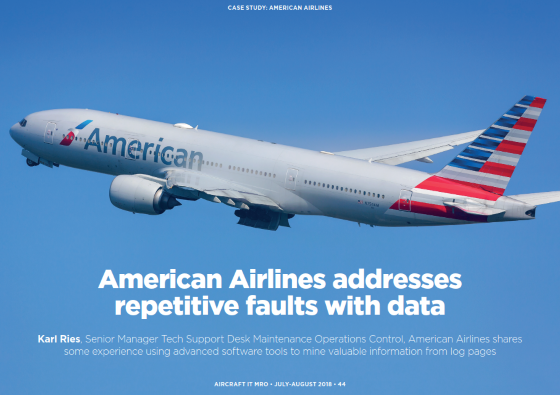
Karl Ries, Senior Manager Tech Support Desk Maintenance Operations Control, American Airlines shares some experience using advanced software tools to mine valuable information from log pages
Before launching into the meat of this case study, it will probably be useful to set the scene with some information about American Airlines, where it has come from and where it stands today.
AMERICAN AIRLINES
The History
The business has been flying for 92 years from starting with Charles Lindbergh who, in April 1926, flew the first American Airlines flight – carrying U.S. Mail from St. Louis, Missouri, to Chicago, Illinois. After eight years flyinf mail routes, the airline began to form into what it is today. American’s founder C.R. Smith worked with Donald Douglas to create the DC-3; a plane that changed the entire airline industry, switching revenue sources from mail to passengers.
Today
Currently, American Airlines serves over 350 destinations in 50 countries on five continents and has a main fleet of more than 900 aircraft comprised of nine different aircraft types. There is a wide body fleet of Boeing 777-200 and -300, Boeing 787-8 and -9, the proven Boeing 767 and the Airbus A330-200 and -300. The narrow body fleet includes Boeing 757, Airbus A320 family (A319, 320 and 321) with nearly 400 aircraft, the proven Boeing 737 and 737 MAX also nearly 400 aircraft, the Embraer E190 and MD80.
So the business has to manage lots of different fleets generating lots of data, especially when it comes to pilot and maintenance reports.
CHALLENGES FACING MAINTENANCE OPERATIONS CONTROL
Integrated Operations Center
Dallas Fort Worth is where American Airlines’ Integrated Operations Center (IOC) is located. At 149,000 sq ft (13,840 sq m) over two floors.
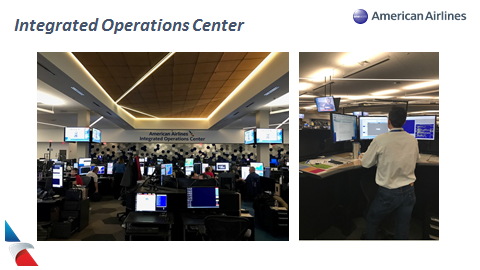
Figure 1
In figure 1, the picture on the left shows the Bridge Center where management is located to help and support the operation. On the right is one of the maintenance control positions – team members get ergonomic desks and can choose to stand or sit to use their three display screens. Although with ChronicX there is no need for multiple screens, the people in the IOC have lots going on, it’s not just maintenance control here, there’s also Ops, Operations Planning, dispatchers, Weight & Balance… a lot of different work groups make up the IOC and its 1,600 or so people.
Challenges faced at American Airlines
Although we faced a number of specific challenges, they could all be grouped under the broad heading of Repetitive Discrepancy Control; looking at pilot and maintenance reports and being able to identify repetitive issues that needed to be addressed. From the merger of US Airways and American Airlines, we inherited two legacy based systems for identifying repetitive issues. This gave rise to a number of challenges. First was simply managing two systems and processes, a big issue to start with; also we lacked a single platform from which to be able to do everything – monitoring, reporting, etc. – which drove a lot of ad hoc and interim solutions which is not what we really wanted: we wanted a final solution to be able to better perform all of our tasks every day. We also had difficulty with the analysis and validation of corrective actions so, once again, we found ourselves using numerous applications to try and obtain data for reviews – get to one answer or one source of information. Having different sources could prolong the work and didn’t always deliver the clearest answer.
Ultimately, we found that the legacy tools prolonged the workload, just to identify items, without even generating follow-up actions or the research required to address those items. They also provided potential for missed alerts and inaccurate results and prevented an efficient process for management and oversight, i.e. it was difficult and labor intensive to get reports telling us what was the main issue of the day.
Figure 2 shows an example of one of the legacy tools.
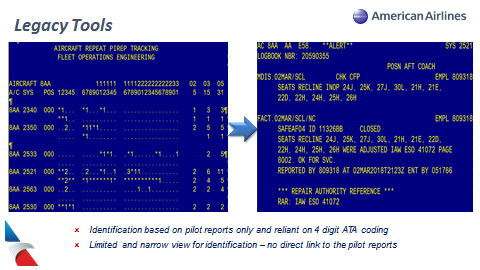
Figure 2
On the left is just one screenshot relating to one particular aircraft showing all the ATAs that are being triggered or had a write-up against them in a 31 day period. All the punched numbers are actual dates. The figures on the right of that screen were the triggers. But, even with that information, there was no direct link and users had to go to another partition and start looking at each individual write-up. This was all the maintenance controllers had to work with and so it is easy to see where things could get missed as they had to work between different screens. Also, because there was no continuity between reports of issues, it was easy to miss a repetitive issue on any one item. Identification base was based on PIREP (Pilot Report) reports, not picking up on maintenance reports. That was another place where a data set was completely missing and was heavily reliant on 4 digit ATA coding which, if it was off by just one digit, meant we were not capturing the potential for a repetitive defect. There were limited views to try to identify issues and there was no direct link to the pilot reports.
PARTNERSHIP WITH CASEBANK AND USING THE CHRONICX TOOL
Bearing all of the above in mind, we determined to search for a solution starting with talking with others in the industry and to our One World partners to find how they managed repetitive defects, how they managed data mining from the pilot reports and maintenance reports? One of the One World partners told us how they were using a new product called ChronicX®, sent us a demo and suggested that it might also interest American Airlines. From that demo, we could see that there were a lot of things that could interest us so we reached out to Steve Lightstone at CaseBank Technologies to arrange a demo which decided us to set up a trial and see whether this could be a solution for the new, merged and combined American Airlines’ Tech Ops and, of course, a fleet size of near 1,000 aircraft.
A trial period
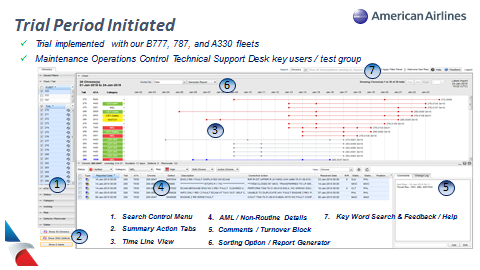
Figure 3
It was decided to conduct the trial on American Airlines’ wide body fleets; the Boeing 777s and 787s, and the Airbus A330s. The idea was to get a good population and the trial period focused on the maintenance control technicians working at the Tech Support Desk because the primary objective was to identify repetitive issues. The screenshot in figure 3 shows the main screen of ChronicX® with each numbered area showing the key elements that make it up. So, is the Search Menu Bar or Control Menu where users can select fleets, specific aircraft, date ranges… it’s very customizable to how the users want to work; it will meet their workflow needs, does not impose any workflow or preconceived notion on how users should manage their data. Looking into further detail, there are Summary Action Tabs that will tell the user how many issues are identified as repetitive, or the user can look at all the write-ups. There’s a Time Line View that shows a quick identifier of where a repetitive issue began, if it’s still occurring or when it ended and it generates a quick visual identification if the users wants to dig further; so, once again, speeding up those kinds of efficiencies to improve the identification process.
There are other specifics but, looking at the new screen compared with what was available before, figure 2, this represents a major improvement; we called it one-stop-shopping, one area, one platform to be able to identify, manage and validate the corrective actions for repeat issues.
Search Controls
To look at some specifics regarding the Search Controls…
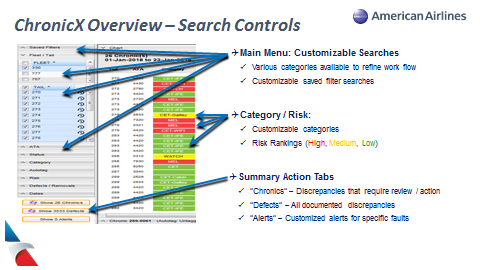
Figure 4
… as can be seen on the left of figure 4, this example is based on the A330 fleet with all the A330s selected but the system is customizable with various categories available to refine the users workflow. Similarly, Categories and Risks are customizable and, if the user wants to use Risk Rankings for an SMS (Safety Management System) type of philosophy, the system provides the capability to mark something High, Medium or Low and it can be seen that a couple of MEL (Minimum Equipment List) referrals had been identified as High Risk items. Also, there’s one marked CET, an abbreviation in American Airlines for Cabin Experience Team whose focus is on passenger experience related items – interiors, IV Wi-Fi – and the item in question was because the Wi-Fi was wholly inoperative. Then, looking again at the Summary Action Tabs, it can be seen that the system has identified 26 chronics that need to be reviewed for action. The option is also available to look at all the Log Book or Maintenance Reports items. This screen shows zero Alerts, that’s the customizable email alerts, an option where the user can set-up an alert based not on a repeat but on just one specific write-up or a key word that the user is looking for; the system will send an email ahead of time to ask whether the user wants to address that issue.
The recurring word or theme that can be seen is ‘customizable’ and, once again, what the administrator writes within ChronicX allows users to go into the categories and use their own terminology and needs at their airline. It isn’t necessary to get back to CaseBank every time a user needs to change things. It’s all very customizable by users.
Time Line
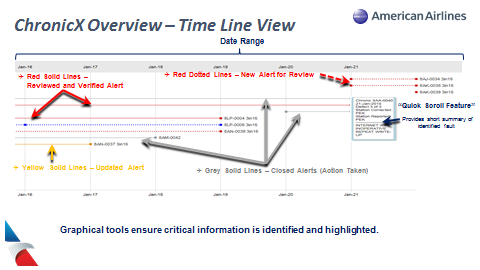
Figure 5
Figure 5 shows a time line view, with the colors of American Airlines’ choice, as is the date range. In this one, the red dotted lines indicate new alerts for review and each square identifies a write-up which offers the team a quick identifier that they need to take a look, access those alerts, get all the log page data or the maintenance reports to figure out if there’s an issue there that needs to be addressed.
The solid red lines indicate that the issue has already been looked at and verified and, most likely, it’s been decided to build a follow-up item, be that within the Maintenance Operations Control or the engineering groups on an action plan to address that repetitive issue. A feature that I also like is; let’s say there was a write-up today that was thought to be a proper corrective action but where the issue repeated shortly after the action, that will come back flagged as a yellow alert or an updated alert that’s identifying to the user that’s an additional item where they need to go back and take a further look because it has not been fixed.
The gray lines are closed alerts, items reviewed and where actions have been taken that the user believed fixed the issue. So, looking at this example, say there was an aircraft with a pressurization problem; the first time it was actioned it was dealt with by a reset, the second time by replacing the cabin pressure controller, then, on the third time, the outflow valve was replaced and, having decided that was a good fix, the issue can be closed. But if it were the case that the outflow valve did not fix the discrepancy, it would come back the next day, as a yellow alert, if it was reported again and the users would take a look at it to decide what action to take next but all the information is there, it isn’t necessary to dig or hunt for it.
The Quick Scroll feature is one that Maintenance Control in American Airlines has identified as one they like. Without having to click to look at all the details, they can easily scroll to see a quick and short summary of identified faults, what they relate to, the station at which they were reported and a brief description of the discrepancy.
These graphical tools ensure that users have critical information that is readily available and quickly identified to let users decide how they want to manage it or address it.
Details
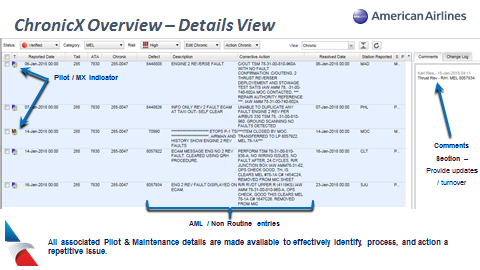
Figure 6
The Details View shown (figure 6) shows where there was a repetitive issue with a thrust reverser on an A330 and some of the write-ups can be seen with pilot and maintenance reports in the AML (American Maintenance Log) with the non-routine items generated by Maintenance and with all the detail there (including dates and times) using crew and maintenance reports to tell the story of what is going wrong with this aircraft. It also gives updates with regards to the Comments section that allows anyone to make a comment on what it is and how it will be dealt with. So, instead of this repeat constantly recurring, within the time frame it was possible to capture it, keep it contained and take corrective action.
Text Analytics
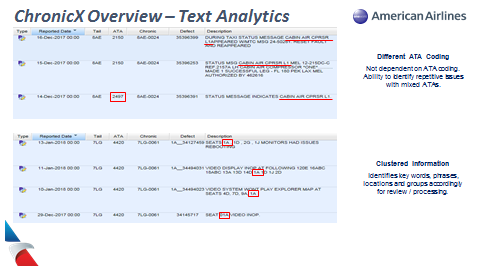
Figure 7
The top line illustrates where the power of text analytics and CaseBank’s algorithms really can support the operation. In the illustrated example (figure 7), on a 787, for three days in a row it had a cabin air compressor L1 decision fault. It can be seen that two of the ATAs were properly coded at 2150 but one was coded at 2497. With the legacy tools, that would never have been noticed and the first write-up on December 14th would have been missed. But the ChronicX system is not dependent on ATA coding; it can identify repetitive issues with mixed ATAs; it really focuses on and does a great job with analytics.
Looking at the bottom example, there are some interior write-ups that deal with IFE (In-Flight Entertainment) and there is a cluster of seats written up for each one. With the clustered information, ChronicX is able to pick out or, at least identify for the user to make the decision or settle on the solution they wish to take with regards to, is there an issue? As can be seen with the bottom example, it picked up on seat 1A which was being reported constantly during that time frame; so that flagged for a Cabin Experience Team to take a look at and generate follow up for seat 1A for the IFE related issues, giving the seat a health check so that passengers using that seat get a better experience when flying on American Airlines. The clustered information is narrowed down to that level of detail which really helps find those hidden chronics.
Reporting
Reporting is a very nice feature with two options of a chronics summary and then there is ChronicX which provides all the detail: but ultimately, it’s an ability to generate reports based on user input and it can identify a certain fleet, a certain aircraft, a certain aircraft with certain sets of ATAs… it doesn’t matter, the choice is up to the system user as to what data they want to be displayed but there’s a standardized format for them to do those reports. And if the users want to put it into an Excel format, leave things out or add things in, that option is available. On the figure is an example where there was an interior write up on a 787 for a C2A / seat 2A being inoperative. The good thing about this is that the report is standardized, so everyone will get used to looking at the same report in the same format, as opposed to the ‘ad hoc’ reporting that had gone on before, so everyone knows what to expect. There’s a quick summary at the top of the report telling users that, in this case, in the past 10 days there were three write ups, who they were allocated to (in this case, again, the Cabin Experience Team). The report doesn’t just dump data into a spreadsheet,, it also offers a pre-defined header that can be presented to various different workgroups in the organization, be that engineering or senior management for something on which they need a quick answer.
All Defects
Going back, the solution that we were looking for in American Airlines’ Maintenance Operations Control was a quicker, more efficient and more accurate way to identify repetitive issues. Figure 8 shows the All Defects View.
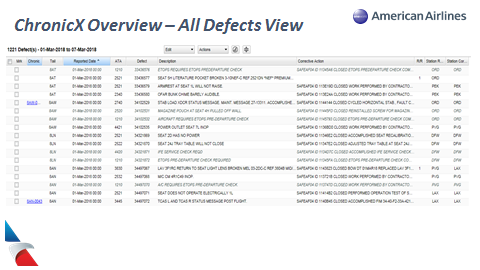
Figure 8
Defects, as defined by CaseBank, includes all write-ups; maintenance write-ups, pilot write-ups and, as you’ll see from the table, in some cases, some of the italicized entries, are items that would not normally be categorized in a repetitive research review such as maintenance check sign-offs or installed gear pins, things of that nature. But, if the user wants to look at all the write-ups, they can. At American Airlines, as we were doing the trial and sharing it with other departments like Engineering and the Quality QATS (Quality Assurance & Testing) teams, we found the flow and the speed of the data was quite impressive for them but, additionally, (see figure 9) so was the key word search.
Key Word Search
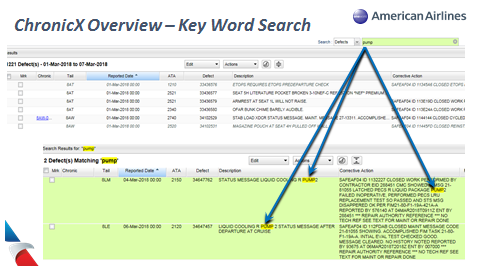
Figure 9
In the figure there’s an example with the 787. At the top the user can type in any key word or phrase, in this case the word ‘pump’, and, as soon as the user hits ‘enter’ the system does all the data mining and finds all the places where a pump is part of the issue. This saves the time spent doing data mining, so it’s been helping the Maintenance Controllers as well as Engineering, Quality control, Reliability by speeding their efficiencies and workflow, cutting down on data mining and getting them to where they need to go and getting them the answer right away where they can efficiently and quickly summarize any analysis that they’re trying to accomplish or answer they’re looking for.
Customized Alerting
This was mentioned earlier in the article and it’s about the email alerting. To give an idea of what we were experiencing at American Airlines, on our wide body aircraft, we were getting issues with cabin odor and specifically around the lavatory areas. There were numerous write-ups where there were sporadic reports of a lavatory leaking and we found out that the carpet in that area was getting soiled which was the driver for the cabin odor. So we were getting a lot of repetitive issues driven by just carpets. The custom alerting allows users to set up key words and hunt down what they’re looking for. There are some good examples in the figure on how the key word searches were set up by using ‘odor’, ‘stink’, ‘smell’ with goal of, instead of it becoming a repetitive issue, we could get it the first time. So, as soon as we started seeing these sporadic write-ups where the lavatory was leaking or the carpet was soiled, we were able to generate actions to attack the problem and get the carpets replaced. So, once again, this custom alerting is not based on ATA coding but allows users to define their own terminology or slang or words, and it’s not dependent on any specific timeframe, it can be set up with one write-up the first time it happens and the email alert is received so that the user can react accordingly, At American Airlines, we’re moving this towards other things like engine oil leaks and the like to attack those items the first time they’re reported instead of having those ‘no fault found’ findings that we know are going to come back.
TRIAL RESULTS
What we found as a result of the trial was accuracy, with more repetitive issues being revealed; efficiency, with decreased time in identifying those repetitive issues; and knowledge, finding we have a powerful analytical tool with the key word search that could be used in other areas of Tech Ops. We found awareness with the new capability to have email alert notifications for specific events and then inform with those customized reports which have assisted in the reviews that I have to accomplish, audits that, say, regulatory teams want to conduct but also correspondence where users can share with other workgroups, be that line maintenance, engineering or anybody involved with trying to address that repetitive issue.
Contributor’s Details
Karl Ries
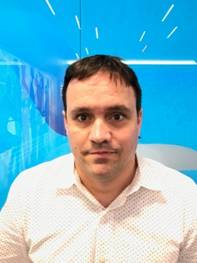
American Airlines

CaseBank Technologies
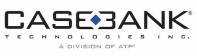
Comments (0)
There are currently no comments about this article.
To post a comment, please login or subscribe.