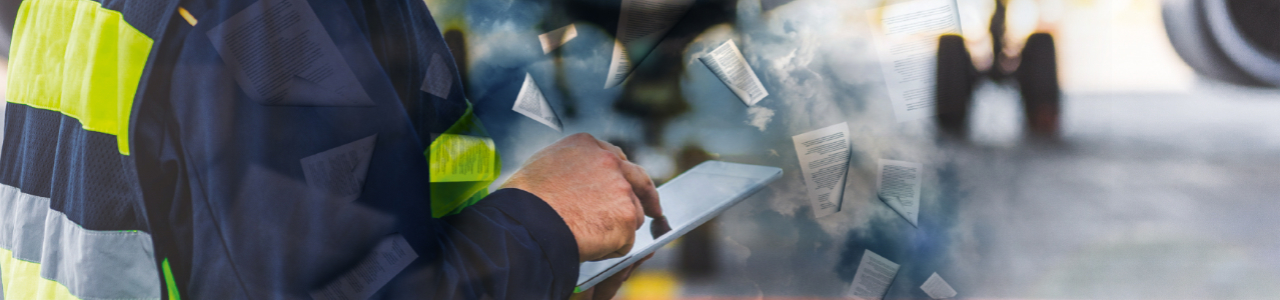
Solomon Airlines Deploy Maintenance Information System from Rusada®
Solomon Airlines Deploy Maintenance Information System from Rusada®
HONIARA, Solomon Islands, 31st October 2017. Rusada’s maintenance solution, Envision® has been deployed by Solomon Airlines as part of a technology refresh and consolidation project.
The airline, based in Honiara International Airport, is the national carrier for the Solomon Islands and operates a fleet of Twin Otters and a Dash 8 for its domestic operations and an A320 aircraft for international flights.
Before the technology project, Air Solomon’s maintenance information was managed using several separate legacy systems. The airline identified that consolidating many of these processes into a single system they would increase situational awareness and improve regulatory compliance monitoring.
Simon Obi, Solomon Airline’s CAMO Manager said: “As the Solomon Islands national carrier, it is critical that our airline maintains the highest standards of safety, maintenance and engineering. We recognised that as the demand on our fleet increases and the expectations of our regulators evolve, we would require a centralised maintenance information system to scale with these requirements.”
Rusada’s CEO Julian Stourton said: “Following a thorough technology evaluation, we were able to satisfy the team at Solomon Airlines that our Envision solution would meet their immediate and future requirements for an integrated maintenance information system”.
Julian continued: “Since signing the agreement in August, Solomon Airlines has been part of our Rusada ‘hyper-care’ program – an established project implementation methodology designed to facilitate a quick deployment – and is already live with the system”.
Solomon Airlines will continue to be supported by Rusada’s Australian based team who are responsible for the company’s customer base in the Asia-Pacific region.
Boeing Grows Leasing Software Presence with Everbright Financial Leasing
Boeing Grows Leasing Software Presence with Everbright Financial Leasing
AMSTERDAM, Oct. 30, 2017 – Boeing [NYSE: BA] subsidiary AerData is growing its leasing software presence in China under a new agreement with Everbright Financial Leasing Co., Ltd., headquartered in Beijing, that will consolidate data from multiple sources using a single Corporate Management System (CMS) platform. The platform will reduce risk for lessors by giving them full control and oversight of asset values, contract information and technical details.
“The AerData CMS application was a logical choice to support our rapidly expanding fleet,” said Wang Hua, head of Aviation, Everbright Financial Leasing. “CMS will be the foundation for all technical and financial processes used to manage aircraft leasing.”
CMS is an industry-leading program that supports aircraft leasing business processes and asset management including maintenance, upgrade and flight records for individual airplanes.
“Before CMS, lessors may have information on airplane assets in multiple systems,” said Matt Bull, AerData CEO. “CMS gives lessors a comprehensive view of their inventory. This helps lessors like Everbright Financial Leasing be more efficient as they expand their presence in the leasing industry.”
More than 60 leasing companies worldwide use AerData systems to support their business.
UTC Aerospace Systems Celebrates Milestone Delivery of 100th Podded Propulsion System to Airbus in Mobile, Alabama
UTC Aerospace Systems Celebrates Milestone Delivery of 100th Podded Propulsion System to Airbus in Mobile, Alabama
CHARLOTTE, N.C., Oct. 26, 2017 /PRNewswire/ — One of the world’s largest aerospace systems providers, UTC Aerospace Systems, a unit of United Technologies Corp. (NYSE: UTX), today delivered its 100th podded propulsion system – a nacelle system integrated with an engine – to the Airbus final assembly line in Mobile, Alabama. UTC Aerospace Systems’ Aerostructures business provides the complete nacelle systems for the Airbus A320ceo (current engine option). Aerostructures’ Foley, Alabama, plant began podding propulsion system for the Airbus A320ceo as well as the Embraer KC-390 military transport in late 2015. The milestone nacelle was podded with a CFM56 engine for an AirbusA321 for Delta Air Lines.
“We’ve been delivering our high-value nacelle systems for the A320ceo since the mid-1980s. Being located near the Mobile final assembly line enables us to deliver quality nacelle systems to Airbus when they need them,” said Aerostructures President Marc Duvall. “We look forward to providing that same value and just-in-time deliveries from Foley for the A320neo propulsion systems in the future.”
Aerostructures was selected by Airbus in 2011 to provide the full nacelle systems for the Pratt & Whitney PW1100G-JM that will power the A320neo (new engine option) for the life of the program. Podding for those engines is currently taking place at other Aerostructures facilities collocated near Airbus final assembly lines in Toulouse, France, Hamburg, Germany and Tianjin, China. Globally, the Aerostructures business has invested more than $500 million to build or expand six company sites in support of the A320neo nacelle industrial ramp-up for the life of the airplane program. The company’s nacelles provide airlines and lessors a compelling value proposition through commonality and high in-service reliability. The innovative nacelle system for the A320neo is performing with 99.99% percent dispatch reliability.
Earlier this year, the Foley site inaugurated a new 80,000-square foot nacelle assembly and integration facility adjacent to its existing operations. The new building is used to assemble nacelles and do podding for propulsion systems going to the Airbus final assembly line in Mobile. The Foley plant was recognized as one of six Best Plants in North America by IndustryWeek in early 2017, and at the 2017 Paris Air Show, the Aerostructures business received the Airbus Supplier Support Rating for exceptional aftermarket support of airplanes.
Lufthansa Systems develops seamlessly integrated generation of flight planning and navigation solutions
Lufthansa Systems develops seamlessly integrated generation of flight planning and navigation solutions
Further convergence of successful Lido product lines from airline IT specialist
Raunheim, October 26, 2017 – Lufthansa Systems today announced that it is developing a new generation of flight planning and navigation solutions following the slogan #takeoffwithlido. The proven Lido/Flight 4D (flight planning), Lido/Navigation (navigation solutions) and Lido/Performance (flight performance calculation) product lines will become even more integrated, providing airlines a seamless digital process across all flight operations – from flight planning to an aircraft’s parking position at its destination. Lufthansa Systems emphasizes its role as a market player that is independent from aircraft manufacturers, which enables it to offer a standardized solution for all of an airline’s different aircraft types.
“Digitalization is affecting the entire aviation industry. We see this in the flight planning and navigation process in particular. Everything is becoming increasingly dynamic and data-driven. Paper maps are being replaced by state-of-the-art apps. New technologies such as in-flight connectivity offer the opportunity to display tactical real-time data such as weather, airspace and traffic information. This is precisely where our integrated Lido solutions come in,” explained Dr. Bernd Jurisch, who took over as Head of the Lido product lines at Lufthansa Systems in October.
The mutual exchange of data is a key benefit to using Lido products for flight planning and navigation. This is because Lido provides the same information to everyone involved in flight operations – both in the air and on the ground – in situations such as an approach with poor visibility, for example. The information seen by pilots on their Lido/Navigation maps is based on the same data as the information available to the flight planner. This means the pilot and flight planner can coordinate the minimal decision height more safely and efficiently when choosing an alternate airport and make well-founded decisions in critical situations – such as whether a landing should be aborted or not.
The shared database is also used when acute meteorological phenomena demand a change to the planned route. New information can also be conveyed to pilots immediately during a flight. All of this not only saves time, it also improves safety.
During normal flight operations, too, the solutions work together seamlessly. Dispatchers can use Lido/Flight 4D to calculate the best route for a specific flight based on all flight-related data. Pilots can access this briefing information online. Thanks to the seamless integration of the products, Chart Notices to Airmen (NOTAMs) can also be added to the flight plans of Lido/Flight 4D. At the same time, information from the ATS flight plan can be uploaded and displayed in the mobile map solution that the pilots use for navigation. This covers departure, destination and alternate airports, takeoff and landing procedures, and waypoints along the route.
Lufthansa Systems additionally offers solutions for calculating and monitoring flight performance. These help airlines keep track of the continually changing obstacle situation at airports so they can adapt their departure procedures accordingly and optimize their fuel consumption for flight planning. The Lido product suite thus offers the perfect portfolio for an airline’s entire flight operations.
Overview of the Lido product suite:
Lido/Flight 4D
- Lido/Flight 4D – Flight planning solution
Lido/Performance
- Lido/AirportObstacleData – Airport-specific obstacle database with departure procedures
- Lido/TakeOff & Lido/Landing – Calculation of optimal flight performance for takeoff and landing
- Lido/APM – Service for comparing target/actual performance data (aircraft performance monitoring)
Lido/Navigation
- Lido/FMS – Navigation data for flight management systems
- Lido/SkyData – ARINC 424 data
- Lido/SurfaceData – Full-coverage obstacle database
- Lido/RouteManual – Paper-based navigation maps
- Lido/eRouteManual – Windows-based app for navigation maps
- Lido/mPilot – iOS-based app for navigation maps
- Lido/AMM – Airport Moving Map
- Lido/AMDB – Geo-referenced database for airports
The “Take-off with Lido” video describes the phases of flight operations that can be controlled smartly and efficiently using Lido products. https://youtu.be/RLFvM3iJsuQ
Caption (Copyright: Lufthansa Systems): The Lido product suite from Lufthansa Systems offers the perfect solution for every phase of flight operations – from gate to gate.
More information on the Lido product suite can be found online at https://www.lhsystems.com/solutions/flight-navigation-solutions
Rusada’s ENVISION™ nGen Technology to Manage Blue Islands Maintenance Information System
Rusada’s ENVISION™ nGen Technology to Manage Blue Islands Maintenance Information System
GUERNSEY, CHANNEL ISLANDS, 25th October 2017. Blue Islands has selected Rusada’s Envision nGen technology to manage the maintenance and engineering requirements of its fleet of ATR 42 & 72 aircraft.
Blue Islands is a privately-owned Channel Islands based regional airline, which became a Flybe franchise partner in 2016, operating flights in Flybe branded aircraft between the Channel Islands and the UK.
Envision nGen will be used by Blue Islands to manage Continuing Airworthiness requirements as well as supporting their regulatory reporting obligations.
Ronald Janssen, Blue Islands Chief Technical Officer said “We were very impressed with the Envision nGen system and we expect that our investment will provide both an optimized framework for managing our CAMO obligations as well as a clear route to additional cost savings and business efficiencies in managing our manpower and materials.
Rusada’s CEO Julian Stourton said: “In developing Envision nGen, we set out to engineer it in such a way that it would eliminate data blindness, where users are bombarded with information that they don’t need to do anything with. Our dashboards ensure that only actionable information is being surfaced to the user while all the routine tasks and reports are working away in the background.”
Rusada’s ENVISION™ nGen Technology to Manage Blue Islands Maintenance Information System
Rusada’s ENVISION™ nGen Technology to Manage Blue Islands Maintenance Information System
GUERNSEY, CHANNEL ISLANDS, 25th October 2017. Blue Islands has selected Rusada’s Envision nGen technology to manage the maintenance and engineering requirements of its fleet of ATR 42 & 72 aircraft.
Blue Islands is a privately-owned Channel Islands based regional airline, which became a Flybe franchise partner in 2016, operating flights in Flybe branded aircraft between the Channel Islands and the UK.
Envision nGen will be used by Blue Islands to manage Continuing Airworthiness requirements as well as supporting their regulatory reporting obligations.
Ronald Janssen, Blue Islands Chief Technical Officer said “We were very impressed with the Envision nGen system and we expect that our investment will provide both an optimized framework for managing our CAMO obligations as well as a clear route to additional cost savings and business efficiencies in managing our manpower and materials.
Rusada’s CEO Julian Stourton said: “In developing Envision nGen, we set out to engineer it in such a way that it would eliminate data blindness, where users are bombarded with information that they don’t need to do anything with. Our dashboards ensure that only actionable information is being surfaced to the user while all the routine tasks and reports are working away in the background.”
Rusada’s ENVISION™ nGen Technology to Manage Blue Islands Maintenance Information System
Rusada’s ENVISION™ nGen Technology to Manage Blue Islands Maintenance Information System
GUERNSEY, CHANNEL ISLANDS, 25th October 2017. Blue Islands has selected Rusada’s Envision nGen technology to manage the maintenance and engineering requirements of its fleet of ATR 42 & 72 aircraft.
Blue Islands is a privately-owned Channel Islands based regional airline, which became a Flybe franchise partner in 2016, operating flights in Flybe branded aircraft between the Channel Islands and the UK.
Envision nGen will be used by Blue Islands to manage Continuing Airworthiness requirements as well as supporting their regulatory reporting obligations.
Ronald Janssen, Blue Islands Chief Technical Officer said “We were very impressed with the Envision nGen system and we expect that our investment will provide both an optimized framework for managing our CAMO obligations as well as a clear route to additional cost savings and business efficiencies in managing our manpower and materials.
Rusada’s CEO Julian Stourton said: “In developing Envision nGen, we set out to engineer it in such a way that it would eliminate data blindness, where users are bombarded with information that they don’t need to do anything with. Our dashboards ensure that only actionable information is being surfaced to the user while all the routine tasks and reports are working away in the background.”
skybook takes off with flydubai
skybook takes off with flydubai
flydubai, the Dubai-based airline, has chosen skybook to provide a new digital flight briefing solution that utilises the flagship software product from Bytron Aviation Systems.
Now live across flydubai’s flight operations, skybook is handling approximately 250 sectors per day, providing the operations teams with the latest tools to dispatch flights as well as providing pilots with flight briefing information digitally.
Modular and scalable by design, skybook is a flexible modern flight dispatch, crew briefing and journey logging solution that can be tailored to meet the exacting needs of any operator, across any sector, regardless of fleet, size or budget.
Implementing skybook will enhance existing flight operations processes helping drive efficiencies, save time and ultimatly reduce operating costs across every sector being flown.
Bytron Aviation Systems Managing Director Shane Spencer said: “flydubai is one of the UAE’s national carriers with an extensive network and I am proud to be able to say that they have chosen skybook as their premier solution for flight dispatch and digital crew briefing.”
“We carried out an intensive trial and evaluation period together, testing each and every aspect of skybook’s functionality, reliability and overall performance.”
“This was an excellent opportunity to not only prove our worth but to also learn from flydubai’s experience and to further develop skybook based on their operational requirements. This partnership has realised major benefits for ourselves as well as for all of our current and future clients.“
“skybook is now handling the dispatch and briefing process for every flydubai flight, automatically generating the information required to produce up to 250 sector briefings per day, all meeting the exacting requirements needed for flydubai’s pilots, helping to save time, improve efficiency and consistency and to benefit operating costs in the future,” added Spencer.
Commenting on the project, Captain Christopher Grazel, Senior Vice President, Network Control Centre at flydubai, said, “We chose skybook as a digital briefing solution not only due to the capabilities of the system, but as a result of the willingness of Bytron to continue to develop the product in line with industry best practice. The highly configurable solution provides a useful tool for our pilots, as well as for our Flight Operations and Network Control teams. We look forward to working with skybook on further developments going forward.“
To find out more about skybook and how we can help to modernise your flight dispatch, crew briefing and journey logging processes visit https://www.bytron.aero/aviation-systems
To arrange your skybook introduction, simply contact us at info@bytron.aero and we’ll do the rest.
We’re taking skybook on tour
If you are planning on visiting the 11th Annual Flight Operations Conference at Heathrow on the 28th and 29th November, we’ll be there with skybook. Why not book your demo now as we have slots available over both days and would love to meet you. Contact us at info@bytron.aero and we’ll get you booked in.
About Bytron
Bytron is a UK based company specialising in aviation data systems, delivering weather, operational data and totally integrated 24/7 flight data management solutions for airlines, airports and air traffic control. With over 30 years of experience supplying aviation systems to Air Traffic Control and Airline customers, we are experts at getting the right data, to the right place, at the right time.
The BYTRON team is second to none within the industry, comprising software developers, software testers, business and aviation specialists. The company’s design philosophy is, and has always been, to provide highly flexible, technically innovative, and compliant user oriented solutions. We believe in being adaptable; reacting quickly to customer requests, enhancing our products to improve the service and help our users.
About flydubai
Dubai-based flydubai strives to remove barriers to travel and enhance connectivity between different cultures across its ever-expanding network. Since launching its operations in 2009, flydubai has:
Created a network of more than 95 destinations in 44 countries.
Opened up 67 new routes that did not previously have direct air links to Dubai or were not served by a UAE national carrier from Dubai.
Operates a single fleet type of 58 Next-Generation Boeing 737-800 aircraft and will take delivery of more than 100 aircraft by the end of 2023.
In addition, flydubai’s agility and flexibility as a young airline has enhanced Dubai’s economic development, in line with the Government of Dubai’s vision, by creating trade and tourism flows in previously underserved markets.
For the latest flydubai news, please visit our newsroom.
UTC Aerospace Systems Honored by Aviation Week for Groundbreaking Work in Aviation Safety
UTC Aerospace Systems Honored by Aviation Week for Groundbreaking Work in Aviation Safety
- Company recognized for scientific research and development of advanced icing wind tunnel; development and qualification of industry’s first airspeed sensors capable of operating in severe icing conditions; and production ramp to provide retrofit probe solution
CHARLOTTE, N.C., Oct. 24, 2017 /PRNewswire/ — At Aviation Week Network’s 16th Annual Program Excellence Awards banquet last night, a team from UTC Aerospace Systems’ Sensors & Integrated Systems business was honored for the company’s groundbreaking achievements in improving aviation safety in severe icing conditions. The team won in the Supplier Research and Development/System Design and Development category. UTC Aerospace Systems is a unit of United Technologies Corp. (NYSE: UTX).
The adverse effects of high altitude icing on aircraft propulsion and air data sensors have been a growing concern of the aerospace industry and airworthiness authorities. The combination of modern aircraft reliance on air data sensing systems for primary flight controls and increased air traffic in inter-tropical regions has increased exposure to high altitude icing conditions. These conditions can affect multiple or all pitot probes installed on an aircraft and can lead to unreliable airspeed measurements. As a result, actions were taken across the industry to improve safety, including new regulations embodied in Federal Aviation Regulation (FAR) Part 33, Appendix D, “Mixed Phase and Ice Crystal Icing Envelope.”
UTC Aerospace Systems responded by addressing both short- and long-term industry needs. A lean production system was developed utilizing the United Technologies ACE (Achieving Competive Excellence) operating system to streamline the production of a pitot probe that had increased robustness to Appendix D conditions. This allowed operators to retrofit their aircraft with the improved probes more quickly than would otherwise have been possible.
At the same time, UTC Aerospace Systems launched a 5-year effort to develop a new facility capable of creating and testing extreme icing conditions, and a new generation of air data sensors capable of operating in the expanded certification envelope. In 2015, the company completed construction of its advanced icing wind tunnel and soon after successfully qualified the industry’s first air data sensor, a pitot probe, to the full Appendix D envelope.
“From a technical perspective, creating an environment in which to study, design and test air data sensors in new and extreme icing conditions represented a significant undertaking,” said Mauro Atalla, vice president of engineering and technology for Sensors & Integrated Systems. “Our advanced icing wind tunnel is generally recognized in the aerospace industry as the most capable air data icing tunnel when considering its unique combination of airspeed, altitude, temperature and ability to deliver coverage of Appendix D conditions.”
The Aviation Week Program Excellence Award the company received for its work was given in recognition of both the performance and execution of this complex project and its parallel development efforts. This parallel development allowed for faster project execution and ensured that each aspect of the project met its objectives. UTC Aerospace Systems is continuing to use the results from the project to develop Appendix D-capable versions of more air data probe models.
“At UTC Aerospace Systems, we’re committed to leading the aerospace industry in solving its most pressing challenges through operational excellence and development of new technology, and that is exactly what our team did here,” said Sensors & Integrated Systems President Justin Keppy. “We’re honored to receive this prestigious award from Aviation Week, which is a testament to the hard work, dedication and ingenuity of our team.”
The Aviation Week Program Excellence Awards honor global aerospace and defense programs and projects, their leaders and their teams for going beyond meeting requirements to exemplify the best in value creation, leadership, adapting to complexity and executing with excellence. Developed in 2004, the awards were created in response to repeated concerns about the complexity and difficulty associated with managing and leading the aerospace and defense programs that are the foundation of the industry. During the evaluation process, more than 300 program management representatives from across industry and government score each application, resulting in the widespread sharing of innovative practices and processes.
Ernest Airlines takes off with AMOS
Ernest Airlines takes off with AMOS
At a glance
– Ernest Airlines goes for open-source database PostgreSQL
– Swiss-AS offers AOS and hosting services
– Quick start and lean implementation
Start-up relies on proven AMOS software system
Swiss-AS is pleased to announce that AMOS has been selected by the Italian start-up airline Ernest Airlines. The low-cost carrier is in the fortunate position that some staff members are already familiar with AMOS – a good basis for the envisaged swift implementation and quick project start. Ernest Airlines relies on a Swiss-AS “care-free package”, a combination of the proven AMOS Operation Services (= AOS, covering the application and database administration) and hosting.
“It is a pleasure for us to accompany Ernest Airlines right from the beginning of this adventure to establish a new airline and to support its growth in future,” states Ronald Schaeuffele, CEO of Swiss-AS.
Despite the fact that national flag carriers and some of the biggest MRO providers worldwide have recently chosen AMOS, Swiss-AS is keen to emphasise that AMOS is also designed to fully meet the requirements of small organisations. To accommodate the needs of start-ups and smaller airlines on tight budgets, Swiss-AS also supports AMOS implementations on the open-source database PostgreSQL.
“AMOS is the reliable system we were looking for the ERNEST CAMO and Swiss-AS has been able to provide a solution suitable for a start-up looking at fleet expansion,” states Carlo Besenzoni, Continuing Airworthiness Director at Ernest Airlines.