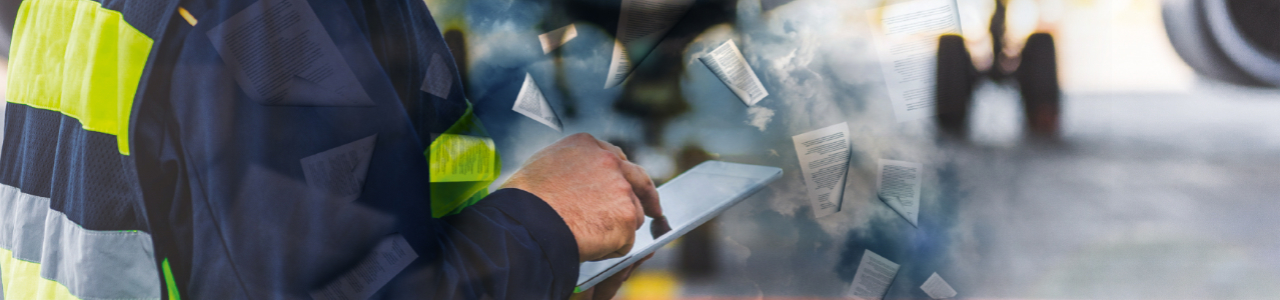
Alkym project complete at Air Seychelles: delivered with extras
Today Volartec announce yet another successful implementation project of Alkym Management and Control System for Aircraft Maintenance. Air Seychelles are the latest customer to have been delivered a successful project within the time frame that many say is impossible. In just five weeks the onsite implementation team have completed configuration, data transfer, training and on-site support to ensure Air Seychelles is getting a return on their investment in the quickest time possible.
On top of the normal project deliverables many opportunities surface during these types of projects where the Volartec expert teams can assist the customer in optimising their current maintenance programs. Dealing with similar airlines from all over the world on a consistent basis has allowed our project teams build upon their own existing knowledge from within the aviation sector. This knowledge transfer comes as standard with our flexible approach to ensure we maximise the customer experience.
On this occasion Robert Chong-Seng, Head of Technical Support at Air Seychelles pointed to “the professional approach in the planning, implementation and management of the project.” And how the team “displayed so much enthusiasm, passion and focus all the while enjoying what they were doing. In particular we appreciated how they assisted us in using the scope of the project to ensure we were getting maximum value from our current maintenance program and practices. This was beyond the normal expectation but our team wanted to work closely with Volartec to ensure all the skill sets from both sides complemented each other.”
Upon the completion of this phase of the project John Barry, VP Business Development with Volartec stated that “We see this as a step in building a long term relationship with the customer. Our dedicated team will continue to support Air Seychelles even after they leave. In the early stages of the customer support the people that visited the customer take core responsibility to ensure smooth transition to our world class support service. This personal touch gives the customer extra confidence in the change process.“
About air seychelles
In operation since 1978, Air Seychelles has evolved from a purely domestic operation into a professional and highly respected National Carrier. With its HQ at the International Airport on the island of Mahe they have a current fleet of 9 aircraft. The domestic fleet consists of 3 Twin Otter and 1 Shorts 360 whilst the international fleet has 5 Boeing 767 aircraft. Next year will see the arrival of two new Boeing 787 Dreamliner’s.
About Volartec
Volartec is one of the fastest growing IT companies in the aviation industry. Specialized in the development and implementation of world class software systems, Volartec provides the most profitable products and services of the market.
With more than 10 years of experience in the aviation industry and constituted by a highly qualified IT and aviation experts team, Volartec assures a successful combination of professionalism and experience.
For more information please visit www.volartec.aero or contact info@volartec.aero
JorAMCo Enables Business Process Optimization with Mxi Technologies’ Maintenix Software
JorAMCo Enables Business Process Optimization with Mxi Technologies’ Maintenix Software
Software upgrade a catalyst for business-driven organizational transformation
News at a Glance
- JorAMCo live with upgrade to Maintenx software
- Maintenix enables business-driven organizational transformation
- Software seen as key enabler in optimizing business processes and operational efficiencies
Ottawa, Canada (August 23, 2011) – Mxi® Technologies, the leader in aviation maintenance management software, announced today that JorAMCo, Jordan’s leading Maintenance, Repair and Overhaul (MRO) provider, has gone live with an upgrade to the Maintenix® software. Building off of JorAMCo’s vision for organizational optimization, this recent go-live further supports the company’s goals for maintenance and engineering excellence.
JorAMCo’s Project TOGA successfully went live with the industry-leading Maintenix software on May 12th, 2011. The enterprise-wide implementation was put into operation via a wholesale approach with all software modules going live simultaneously. Project TOGA was run jointly with operational experts at JorAMCo, trainers, data migration specialists, and leadership of the project team.
JorAMCo’s Maintenix upgrade includes the foundational establishment of a comprehensive software footprint in support of their business operations and process reengineering. In addition to the extensive use of maintenance planning and business analytic tools to facilitate reduced turnaround times, the recent upgrade offered enhancements to MRO invoicing, third-party maintenance and the further integration of materials, planning, purchasing, and execution.
“At the outset of this project we established an ambitious vision in reference to our goals for business process reengineering and optimization,” says Simon Tate, Chief Executive Officer, JorAMCo. “To that end, Mxi and the Maintenix software have been key enablers in facilitating the achievement of our project objectives and our mission for being a world-class MRO provider with a penchant for using market-leading technologies in support of our customers’ success.”
“This go-live firmly establishes JorAMCo as a regional and industry innovator in the field of MRO,” says Dave Seibel, Chairman and CEO, Mxi Technologies. “Throughout the project we have been impressed with their dedication to current and future success and we are pleased to have Mxi’s Maintenix software serve at the core of this considerable transformation.”
About JorAMCo
JorAMCo started operations as Royal Jordanian’s Maintenance and Engineering Department in 1963. Following the government’s decision in October 2000 to privatize and restructure the airline, JorAMCo was officially launched as an independent MRO service provider, offering then a range of airframe maintenance services to Airbus, Boeing and Lockheed aircraft fleets.
Since then, JorAMCo started an aggressive growth and expansion plan to strengthen its customer base and customer support capability, JorAMCo completed a hangar space expansion which brought the total available hangar space to 30,000 square meters, engaged the services of additional technical staff and certified technicians, increased the range of backshops capacities by setting up partnerships with OEMs and manufacturers, and launched a modern academy to ensure a steady supply and enrollment of fresh and qualified technicians and engineers of the right caliber.
JorAMCo is certified by the Jordanian Civil Aviation Regulatory Commission “JCARC” and by a number of regional and international Aviation Authorities including US FAA and European EASA – Part 145.
About Mxi Technologies
With solutions designed specifically for aviation maintenance, Mxi Technologies provides integrated and intelligent software, support, and services to commercial airlines, MROs, OEM aftermarket service providers, and defense operators. Mxi Technologies’ Maintenix® software uses a modern architecture and provides advanced capabilities such as a role-based Web browser interface, long range and automated line planning, automated workflow, electronic signatures, support for portable wireless devices, and a comprehensive range of integration APIs. Mxi Technologies’ customers range from emerging, small to midsized organizations to the largest global enterprises.
CONTACT:
Jennifer Smart
Marketing Communications Manager
Mxi Technologies
T 613-747-4698 x 7438
M 613-697-0347
jennifer.smart@mxi.com
www.mxi.com
United Airlines Launches Paperless Flight Deck With iPad
FIRST NETWORK CARRIER TO INTRODUCE PAPERLESS AERONAUTICAL NAVIGATION CHARTS; MOVE ENHANCES EFFICIENCY, SAVES FUEL, IMPROVES SAFETY
CHICAGO, Aug. 23, 2011 — United Continental Holdings, Inc. (NYSE: UAL) today announced that it is converting to paperless flight decks and deploying 11,000 iPads to all United and Continental pilots. The electronic flight bags (EFB) replace paper flight manuals, and as a first for major network carriers, provide pilots with paperless aeronautical navigational charts through an iPad app. Distribution of iPads began earlier this month, and all pilots will have them by year end.
“The paperless flight deck represents the next generation of flying,” said Captain Fred Abbott, United’s senior vice president of flight operations. “The introduction of iPads ensures our pilots have essential and real-time information at their fingertips at all times throughout the flight.”
Navigational Charting App Breaks New Ground
The iPads are loaded with Jeppesen Mobile FliteDeck, the industry’s premier app featuring interactive, data-driven enroute navigation information and worldwide geo-referenced terminal charts. The enhanced full-color, high-quality information display ensures the right information is displayed at the right time.
“We are proud to partner with United Airlines on a project of this magnitude with Jeppesen Mobile FliteDeck,” said Mark Van Tine, president and CEO of Jeppesen. “Jeppesen and United share a long and storied history that includes development of numerous innovations for the aviation industry. We look forward to continuing this partnership in integrating our digital mobile solutions that increase efficiency, reduce costs and optimize operations.”
Saving 16 Million Sheets of Paper and 326,000 Gallons of Jet Fuel a Year
Each iPad, which weighs less than 1.5 pounds, will replace approximately 38 pounds of paper operating manuals, navigation charts, reference handbooks, flight checklists, logbooks and weather information in a pilot’s flight bag. A conventional flight bag full of paper materials contains an average of 12,000 sheets of paper per pilot. The green benefits of moving to EFBs are two-fold—it significantly reduces paper use and printing, and, in turn, reduces fuel consumption. The airline projects EFBs will save nearly 16 million sheets of paper a year which is equivalent to more than 1,900 trees not cut down. Saving 326,000 gallons of jet fuel a year reduces greenhouse gas emissions by 3,208 metric tons.
iPad Improves Efficiency and Safety
With iPad, pilots are able to quickly and efficiently access reference material without having to thumb through thousands of sheets of paper and reduce clutter on the flight deck. United and Continental pilots’ work will be streamlined as they can immediately download updates on iPad to their electronic flight materials, rather than waiting for paper updates to be printed and distributed. In addition, by eliminating bulky flight bags loaded with paper, pilots will have less to lift and carry through airports and onboard the aircraft, reducing the risk of injury while on duty.
High-resolution images of United pilots using the iPad in the flight deck are available for download at UnitedContinentalHoldings.com > Media Center > Media Downloads.
About United Continental Holdings, Inc.
United Continental Holdings, Inc. (NYSE: UAL) is the holding company for both United Airlines and Continental Airlines. Together with United Express, Continental Express and Continental Connection, these airlines operate an average of 5,765 flights a day to 377 airports on six continents from their hubs in Chicago, Cleveland, Denver, Guam, Houston, Los Angeles, New York/Newark Liberty, San Francisco, Tokyo and Washington, D.C. United and Continental are members of Star Alliance, which offers more than 21,200 daily flights to 1,185 airports in 185 countries. United and Continental’s more than 80,000 employees reside in every U.S. state and in many countries around the world. For more information about United Continental Holdings, Inc., go to UnitedContinentalHoldings.com. For more information about the airlines, see united.com and continental.com or follow on Twitter and Facebook.
AeroMechanical Services Signs AFIRS 220 Contract with Middle Eastern Airline
Calgary, Alberta – August 17, 2011 — AeroMechanical Services Ltd. (TSX-V: AMA) (the “Company” or “AMA”) has signed a contract with a Middle Eastern Boeing 737 operator for the Automated Flight Information Reporting System (“AFIRSTM“) 220.
The contract requires AMA to install the AFIRS 220 on two Boeing 737-300 aircraft serving the Middle East and North Africa. This airline’s original interest in AFIRS was for satellite voice and flight following features only. Upon learning of the other AFIRS 220 capabilities, the airline will also utilize the engine trending, airframe and engine exceedances, and Out, Off, On and In times (“OOOIs”).
“The AFIRS 220 is a valuable solution for many airlines,” said Bill Tempany, Chairman and CEO of AMA. “The AFIRS 220 provides functions that offer a return on investment, operational improvement and increased safety for operators around the world. We see this product providing strong value to our customers for many years to come.”
AMA will be providing equipment and services over a five year contract. Installations are scheduled to begin before the end of the third quarter. If AMA completes installation on all contracted aircraft and provides recurring service for the full term of the agreement, gross revenue to AMA will be approximately US$182,000, excluding optional services. AMA holds all the necessary certifications to provide services to this customer.
This disclosure as it relates to this agreement is subject to the following disclaimer:
When a contract is initially signed, the intended number of aircraft, pricing and potential installation schedules is agreed to by the parties. The actual installation schedules as well as the number and types of aircraft are often revised throughout the term of the agreement as the airline realigns its fleet of aircraft with its business requirements. Delays in installations can and do occur which can affect the total value of the contracts such that the revenues noted above may not be fully achieved. Fulfilment of the contract terms may also be affected if there are any changes to government statutes, regulations or rules of the applicable governing bodies. The contract terms and values disclosed herein are based on the original information available to AMA upon execution of the contract and are subject to change. For the actual revenue earned, please see AMA’s financial statements including its revenue recognition policy disclosed within the notes to the Audited Annual Financial Statements.
About AeroMechanical Services
AeroMechanical Services Ltd., under the brand name FLYHTTM, provides proprietary technological products and services designed to reduce costs and improve efficiencies in the airline industry. The Company has patented and commercialized three products and associated services currently marketed to airlines, manufacturers and maintenance organizations around the world. Its premier technology, AFIRS™ UpTime™, allows airlines to monitor and manage aircraft operations anywhere, anytime, in real-time. If an aircraft encounters an emergency, AMA’s triggered data streaming mode, FLYHTStream™, automatically streams vital data, normally secured in the black box, to designated sites on the ground in real-time. The company has been publicly traded on the TSX Venture Exchange since 2003 under the trading symbol AMA.
AFIRS, UpTime, FLYHT, FLYHTStream and aeroQ are trademarks of AeroMechanical Services Ltd.
Contact Information
AeroMechanical Services Ltd.
Thomas R. French, CGA
VP Finance and CFO
403-291-7427
tfrench@flyht.com
Barnes Communications Inc.
Colin Languedoc
Senior Consultant
416-367-5000 ext. 225
clanguedoc@barnesir.com
Join us on social media!
www.facebook.com/flyht
www.twitter.com/flyhtcorp
www.slideshare.net/flyhtcorp
www.youtube.com/flyhtcorp
AeroMechanical Services Installs Second Operations Centre in Nigeria
Calgary, Alberta – August 15, 2011 – AeroMechanical Services Limited (TSX.V: AMA) (the “Company” or “AMA”) has received payment for the establishment of a second Operations Centre (“OC”) at a new state-owned and operated airport in Nigeria.
The airport will use the OC for real-time weather information and forecasting. Operators at the facility will be able to observe up-to-date weather within Nigeria and configure their displays to identify different weather layers. The system will aid aircraft flying into and out of the airport and will provide weather information to assist air traffic control on the safety of flying conditions.
This is the second OC of its type AMA has set up in Nigeria. The first such facility, in Lagos, was commissioned in the spring of 2011, as announced on April 7, 2011. Nigeria is continually working to improve its aviation industry, and OCs provide vital information on operating conditions and the location of aircraft in flight.
“AMA is proud to be a contributor to the modernization of the facilities in Nigeria and is committed to the long term strategy of providing OCs as critical pieces in aviation safety in Western Africa,” said Bill Tempany, Chief Executive Officer.
AMA’s responsibilities include the layout and design of the operations room, and provision of the equipment, installation, software, and training for OC staff to use the system. The Company received US$400,000 as payment for the facility.
About AeroMechanical Services
AeroMechanical Services Ltd., under the brand name FLYHTTM, provides proprietary technological products and services designed to reduce costs and improve efficiencies in the airline industry. The Company has patented and commercialized three products and associated services currently marketed to airlines, manufacturers and maintenance organizations around the world. Its premier technology, AFIRS™ UpTime™, allows airlines to monitor and manage aircraft operations anywhere, anytime, in real-time. If an aircraft encounters an emergency, AMA’s triggered data streaming mode, FLYHTStream™, automatically streams vital data, normally secured in the black box, to designated sites on the ground in real-time. The company has been publicly traded on the TSX Venture Exchange since 2003 under the trading symbol AMA.
AFIRS, UpTime, FLYHT, FLYHTStream and aeroQ are trademarks of AeroMechanical Services Ltd.
Contact Information
AeroMechanical Services Ltd.
Thomas R. French, CGA
VP Finance and CFO
403-291-7427
tfrench@flyht.com
Barnes Communications Inc.
Colin Languedoc
Senior Consultant
416-367-5000 ext. 225
clanguedoc@barnesir.com
Join us on social media!
www.facebook.com/flyht
www.twitter.com/flyhtcorp
www.slideshare.net/flyhtcorp
www.youtube.com/flyhtcorp
BAE Systems Selects Mxi Technologies to Enhance After-Market Service Capabilities
BAE Systems Selects Mxi Technologies to Enhance After-Market Service Capabilities
Maintenix software chosen as key enabling technology for BAE Systems’ fully-integrated maintenance management solution
News at a Glance
- BAE Systems selects Maintenix as integrated maintenance solution for after-market programs
- First phase offers maintenance management support for MOD fleet
- Project will extend to multiple customer fleets
Ottawa, Canada (August 11, 2011) – Mxi® Technologies, the leader in aviation maintenance management software, announced today that BAE Systems has selected the Maintenix® software as the core enabling technology for their after-market support programs.
The first phase of the project, currently in implementation, serves as a platform for the induction of military aircraft operated by the United Kingdom’s Ministry of Defence (MOD). Following successful completion of this stage, a comprehensive Maintenix footprint will be rolled-out in support of BAE Systems’ portfolio of defense after-market services for military aviation assets. The full project will culminate in a fully-integrated maintenance management environment standardized for end-to-end asset lifecycle management across multiple customer fleets.
“Following a rigorous evaluation process, it quickly emerged that Mxi Technologies was the right partner — and Maintenix the right software — to enable BAE Systems’ organizational goals for our current and future sustainment programs,” says Martin Blaze, Maintenance and Support Director for BAE Systems military air sector. “Throughout the vendor assessment, Mxi continually impressed us with their industry knowledge and their ability to demonstrate proven value within key areas of our business.”
“We are pleased to announce BAE Systems as part of Mxi’s growing defense customer community,” says Dave Seibel, Chairman and CEO, Mxi Technologies. “Our positive, ongoing engagement with the organization speaks to the value of our partnership and the opportunity for future growth, both within the scope of the current project and beyond.”
About BAE Systems
BAE Systems is a global defence and security company with approximately 100,000 employees worldwide. The Company delivers a full range of products and services for air, land and naval forces, as well as advanced electronics, security, information technology solutions and support services.
About Mxi Technologies
With solutions designed specifically for aviation maintenance, Mxi Technologies provides integrated and intelligent software, support, and services to commercial airlines, MROs, OEM aftermarket service providers, and defense operators. Mxi Technologies’ Maintenix® software uses a modern architecture and provides advanced capabilities such as a role-based Web browser interface, long range and automated line planning, automated workflow, electronic signatures, support for portable wireless devices, and a comprehensive range of integration APIs. Our customers range from emerging, small to midsized organizations to the largest global enterprises.
CONTACT:
Jennifer Smart
Marketing Communications Manager
Mxi Technologies
T 613-747-4698 x 7438
M 613-697-0347
jennifer.smart@mxi.com
www.mxi.com