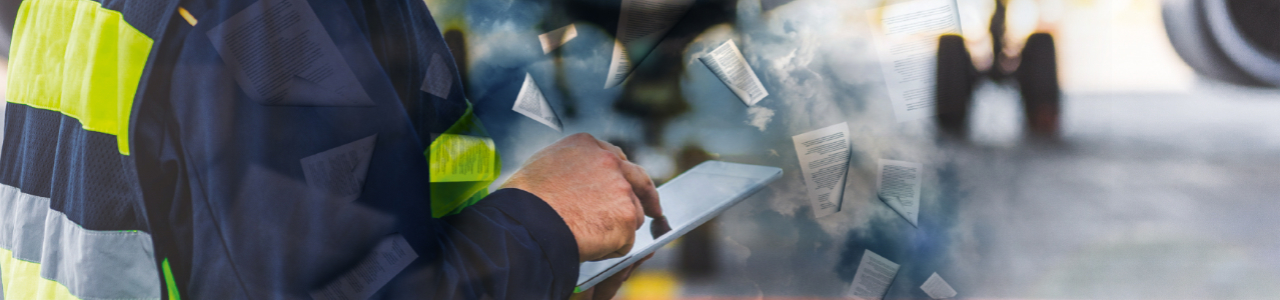
Air France Industries KLM Engineering and Maintenance Sign Enterprise Agreement That Expands Enigma Software
Air France Industries KLM Engineering and Maintenance Sign Enterprise Agreement That Expands Enigma Software
System Will Help Maximize Safety, Reliability and Uptime
BURLINGTON, Mass.—February 28, 2011—Enigma Inc., the leading software company for improving equipment service and parts processes, today announced that Air France Industries KLM Engineering and Maintenance (AFI KLM E&M) is upgrading and expanding their Enigma implementation to the Enigma 3C® InService MRO solution to improve maintenance in its aircraft maintenance, engine services and components shop divisions.
Since their merger in May 2004, Air France and KLM Royal Dutch Airlines have become the largest European airline group. Both airlines run their own operations from their respective hubs, Paris-Charles de Gaulle and Amsterdam-Schiphol. Air France and KLM carry more than 71 million passengers per year. They have a combined fleet of over 600 aircraft enabling them to fly 2,500 daily flights to 236 destinations worldwide.
The corporate-wide license agreement allows Air France and KLM Royal Dutch Airlines to use Enigma’s InService MRO and Revision Manager solutions to support publishing and management of all technical content. Over the past seven years, AFI KLM E&M implemented a highly customized solution based on the Enigma 3C Platform that delivered aircraft maintenance data to all of its overhaul and line-maintenance mechanics. AFI KLM E&M had also implemented Enigma’s InService Revision Manager to help compare and reconcile documentation changes from Boeing and Airbus, with changes made by AFI KLM E&M, which ensured fast, accurate maintenance and support. As a result, AFIKLM E&M documented a 10% reduction in aircraft maintenance IT costs with Enigma 3C, and the company expects Enigma InService MRO and Revision Manager to provide additional savings. As a long-term customer, AFI KLM E&M recognized the advantages of moving to the commercial off-the-shelf solution (COTS), Enigma InService MRO. Now, AFI KLM E&M will reap the benefits of simplified IT configuration and integration capabilities, and a streamlined workflow and user interface.
Enigma InService MRO provides a production environment that supports S1000D and ATA iSpec 2000/2200/2300 (and earlier) specifications as well as PDF, including effectivity filtering, for aircraft, engine and component manuals. It automates the creation and distribution of a product encyclopedia that simplifies the maintenance and support of complex equipment, as well as the deployment of illustrated parts catalogs that can be integrated with existing back office systems, such as ERP and maintenance planning, inventory and logistics, and scheduling systems. For AFI KLM E&M engineers, planners and technicians, the Enigma solutions will be the single source for all information related to airframe and engine maintenance, including OEM maintenance manuals and parts catalogs, maintenance supplements, service bulletins and schematics.
“We are committed to optimizing safety, reliability and uptime for our fleet, and for the past seven years Enigma technology has been a key component of our maintenance and engineering operations,” said Peter de Swert, Executive Vice President, KLM Engineering & Maintenance. “By significantly accelerating the implementation of tens of thousands of maintenance updates and revisions, Enigma’s InService MRO will provide another competitive advantage for our aircraft, components and engine services operations,” he added.
“The Enigma InService MRO suite is designed to help companies like AFI KLM E&M keep their capital equipment running at peak efficiency. These unique solutions enable maintenance and engineering organizations to identify the correct parts and relevant service information, which is critical to maximize productivity and compliance,” said Jonathan Yaron, CEO of Enigma. “We are pleased that one of the world’s largest airlines is expanding their relationship with Enigma and is further investing in software solutions that help them service aircraft, engines and components more accurately and efficiently.”
About AFI KLM E&M
Air France Industries and KLM Engineering & Maintenance, which joined forces following the Air France KLM merger, are world-leading multi-product MRO (Maintenance, Repair, Overhaul) providers with a joint workforce of over 14,000, offering comprehensive technical support for airlines, ranging from engineering and line maintenance to engine overhaul, as well as the management, repair and supply of aircraft components, structured around a powerful logistics network. Since the 2004 merger the group has set up a Joint Sales Organization. Development and Strategy, Sales and Marketing, Corporate Communications and Legal Affairs have been merged for enhanced efficiency through the quest for synergies. The joint organization has simplified customer relations and delivered greater transparency. Together they support more than 1,230 aircraft operated by 150 major international airlines. For more information visit www.afiklmem.com
AMOS chosen by three airlines of the BMI Group
ANOTHER AMOS CUSTOMER FROM THE LUFTHANSA GROUP
Swiss AviationSoftware (Swiss-AS) and the bmi group have recently signed an agreement for the implementation of AMOS at British Midland International, bmi regional and bmibaby. Swiss-AS will provide the entire range of its maintenance management solution from Material Management to Engineering and Production.
“The decision to implement AMOS into the entire bmi group furthermore strengthens our footprint in the UK. We take pride in this high-profile deal and are happy to welcome another member of the Lufthansa Group into the AMOS customer circle,” states Ronald Schaeuffele, CEO of Swiss AviationSoftware.
COST-CUTTING POTENTIAL DUE TO FULLY INTEGRATED SOFTWARE
After a classic selection process in spring 2010 and a site visit to an existing AMOS reference customer, AMOS was shortlisted by bmi. Later, bmi and Swiss-AS arranged several web demonstrations dedicated to specific topics of interest. This approach turned out to be ideal, since different user groups were given the chance to address their needs and requirements to Swiss-AS and to familiarise themselves with AMOS, prior to the final decision being made by bmi. Swiss-AS and bmi are confident that the high user acceptance will positively contribute to the project’s success.
The AMOS Go-Live is planned to take place after 12-14 months of project work containing key and end user training, workshops, data transfer support, technical/consultant onsite support regarding Go-Live etc. A key challenge will be the modelling and streamlining of business processes within all three airlines.
By replacing the current non-integrated and fragmented IT landscape in the maintenance division, the UK based bmi group will substantially benefit from AMOS’ full integration and its very advanced interfacing capabilities. This will result in bmi having access to relevant information at the click of a mouse and will provide a significant reduction ofoperating costs. The implementation of AMOS will also improve the aircraft availability and optimise the allocation of bmi’s capacities and resources.
Enigma announce the release of InService MRO 5.0
InService MRO v5.0
“InService MRO is the only service and parts solution in the market that is designed for integration with other critical business systems, to guarantee that maintenance operations are fast, accurate and profitable.” Jonathan Yaron, CEO Enigma
Enigma InService MRO v5.0 is the best-in-class solution for the maintenance, repair and overhaul of capital equipment such as aircraft, locomotives and other complex assets. This out-of-the box publishing and delivery solution improves the management and distribution of service and parts information throughout maintenance and engineering organizations—from planning, scheduling and procurement to line, heavy and shop maintenance.
InService MRO helps to dramatically reduce equipment downtime, optimize inventory, simplify logistics and ensure regulatory compliance. Optional modules for job card generation and revision management are available to simplify the management and rollout of service and parts updates and revisions, and to generate complete and accurate job /task cards. The solution is modular and configurable allowing your maintenance environment to move from a paper or a legacy environment directly to the web in record time.
InService MRO enables maintenance organizations to:
- Manage ongoing content publishing and updating cycles and distribute approved content to multiple channels and devices
- Manage various content types (manuals, catalogs, best practices, etc.) from multiple sources (OEM, field engineers, suppliers, etc.) across different business processes (maintenance, procurement, planning, etc.)
- Control all system and user processes, content flow, access rights and personalization
- Find relevant service information through serial number, configuration and fault-code filtering
- Maintain an accurate parts list for each asset
- Deliver service and parts information offline or online
- Integrate easily with IT and ERP systems
Manage both structured content (SGML, XML) and unstructured content (PDF, images, binary); any schema or DTD, including S1000D, ATA2200/2300 and a variety of military specs.
Volartec’s Alkym MRO system enters Ukraine with a bang: Two airlines go live at once
Volartec are delighted to announce the dual successful implementations with their new customers in Ukraine.
In September and October last year Volartec reached agreement with two Ukrainian based Airlines as the vendor of choice for maintenance management software. Firstly Bukovyna Airlines and then UM Airlines selected Alkym to enable their organisations optimise their productivity.
The implementation projects were run in tandem in order to meet the client requirements to be live in 2010. Both were successfully concluded in 5 weeks ending at the beginning of December.
John Barry, VP Business Development with Volartec commented “The unique challenge of running simultaneous projects with GO LIVE planned for the same day gave us another opportunity to prove our strong project management skillset. We are delighted to say we exceeded the customer expectations in both projects having time to bring added value improvements to their set up”
Alkym® represents a complete solution to all requirements related to aircraft maintenance. Alkym® was chosen on this occasion for the ability to provide this full suite with the entire functionality required, at the most competitive price on the market.
Vadim Levtushenko, Head of Purchasing Department with UM Airlines was impressed with the project team on site stating “We were promised an awful lot in the sales process to be delivered in what we considered a short timescale. The team that arrived to assist us with the implementation were extremely professional and delivered on all aspects that had been promised. In fact we felt they exceeded our expectations. We now have Alkym in a live environment managing our fleet.”
His comments were echoed by Alexander Manko, Head of Engineering Support Department for Bukovyna Airlines who was “pleased to be able to see a return on their investment so quickly. We had no idea that such an undertaking could be delivered so professionally in the short time frame. The disruption to our operation was always one of the reasons we did not commit previously. In this case we had no major disruption.”
navAero Secures EFB Contract with TUIfly Nordic
SUNDSVALL, SWEDEN February 22, 2011 — navAero announced today the contract signing with TUIfly Nordic for the deployment of the tBag™22 Electronic Flight Bag system on the airline’s B737-800 and B767-300 fleets.
The contracted navAero EFB architecture includes cross-connected dual tBagC22 EFB systems with the newly commercialized tPad™000 display. The systems will also include the navAero-designed, UMTS/HSDPA/3G cellular communications modem module to enable on-ground data transfer.
TUIfly Nordic plans to equip the EFBs with the Lufthansa Lido/eRouteManual software suite and the TUI Group Aircraft Performance Software. TUIfly Nordic will also integrate their operational document browser software on the EFB. This is part of a proprietary solution for the Windows PC, Mac OSX and iPhone/iPad platforms used by flight crews to have offline access and stay up to date with company manuals, briefs and operational notices. The TUIfly EFB program will be launched with the navAero systems being first deployed in one B737 and one B767 aircraft.
“After a thorough evaluation, we have concluded that no competing EFB Class 2 system matches the performance, connectivity and affordability provided by navAero.” stated Johan Gauermann, Director, Flight Operations, TUIfly Nordic. “While there are many EFB vendors in the market, navAero’s EFB solution offers the best cost/performance rate. We are pleased be in the technology forefront, here in Europe, to soon be able to deploy Class 2 EFBs into revenue operations.”
navAero spokesperson, Knut Aabo, VP Sales & Marketing, states “The addition of TUIfly Nordic to the navAero customer roster is a major accomplishment for our company. We are proud to have been selected to fulfill this airline’s need for robust yet affordable Class 2 EFB technology. Not only does this TUIfly Nordic represent our 10th European airline customer, but it also gives navAero the opportunity to show our technology to the rest of the TUI Airline Management organization and demonstrate the true beneficial savings that can be realized through the deployment of dedicated Class 2 EFB systems.”
About navAero
navAero is the industry leader in developing and commercializing cost effective electronic flight bag products for the airline industry. navAero AB is headquartered in Sundsvall, Sweden. Sales, marketing, certification and technical support for the Western Hemisphere is based in Miami, Florida, USA. navAero encourages operators to contact us for complete information about available and pending certifications for our EFB technologies. For further information, visit the navAero website at www.navaero.com or e-mail us at info@navaero.com.
About TUIfly Nordic
TUIfly Nordic is the largest charter company in Sweden, with over one million holiday travelers annually. The airline is part of TUI Nordic Group, which consists of the Leisure Travel and its sister company Star Tour of Denmark and Norway, Finnmatkat in Finland, TEMA and Nazar. Fritidsresor group is part of the world’s largest travel group, TUI Travel Plc.
TUI Travel Plc serves 30 million customers annually, by 48 000 employees, offering flights from 20 countries globally, from Thailand in the East to the West Indies in the West.
For further info about the airline, the TUIfly Nordic website at: www.tuiflynordic.se and for information on the TUI Travel Plc, visit: www.tuitravelplc.com
navAero Ab
Forradsgatan
4 856 33 Sundsvall
Sweden
www.navAero.com
Tel +46.60.66.4100
Int +1.305.358.0065
Fax+1.305.358.0073
Contact:
Knut Aabo
navAero, Ab
+46.76.768.4610
Knut.Aabo@navaero.com
Condor Lands with navAero For Class 2 Electronic Flight Bag
SUNDSVALL, SWEDEN, February 18, 2011 — Condor Flugdienst, headquarted in Kelsterbach, Germany, announced today the selection of navAero to supply the t_Bag™C22 Electronic Flight Bag system for the airline’s fleet of Boeing 757-300 and B767-300ER aircrafts.
After a successful implementation fleet test in one of the airline’s B757 during fourth quarter 2010, the navAero EFB performance exceed the expectations of Condor’s management team as to the system’s reliability and functionality. Condor will begin fleet installations for their B757 and B767 aircrafts beginning in March, 2011.
The navAero Class 2 EFB flight deck hardware chosen by Condor will include the t_Pad 1500 10.4” display. The navAero EFB CPU will configured with the navAero-designed UMTS/HSDPA/3G cellular communications module which enables on-ground data transfer. Condor will deploy their own application suite with a wireless data manager. The airline will also be using the EFB platform for viewing document as well as displaying aeronautical charts as provided by the LIDO eROUTE MANAGER charting application
“Condor is committed to being at the forefront of using technology to improve the safety and efficiency of our operations.” stated Mr. Gunnar Schmidt, Post Holder Flight Operations, Condor. “Our three-month in-use trial evaluation of the navAero EFB system clearly showed us that theirs is the right technology solution for our airline. We were able to remove the 50kg Navkit, which allowed us to realize increased fuel savings all of which helped us toward meeting our corporate goal of reducing our carbon footprint. All in all, the navAero solution demonstrated its ability to meet all our financial and technological requirements that will give us the means by which we can deploy the right blend of applications we need to meet our business goals.”
navAero spokesperson, Simone Giordano, VP Customer Operations, stated “We welcomed Condor’s challenge for an in-flight, real-world evaluation of our EFB technology. The navAero legacy with B757 and B767 operators deployed with our EFB system showed Condor the true reliability and versatility of our highly affordable technology offering. We are extremely excited in welcoming Condor into our growing family of forwarding-thinking airlines who have not only embraced Class 2 technology but have clearly seen the navAero difference as to what a purposefully-built Class 2 system can provide.
About navAero
navAero is the industry leader in developing and commercializing cost effective electronic flight bag products for the airline industry. navAero AB is headquartered in Sundsvall, Sweden. Sales, marketing, certification and technical support for the Western Hemisphere is based in Miami, Florida, USA. navAero encourages operators to contact us for complete information about our EFB technology and the available STCs for our solutions. For further information, visit the navAero website at www.navaero.com or e-mail us at info@navaero.com.
About Condor
The German airline, Condor Flugdienst GmbH, was established in 1956 and continues as one of the leading carriers to over 90 destinations worldwide. Condor’s fleet of 34 Aircraft includes Airbus 320, Boeing 757-300 and Boeing 767-300. Parent company of Condor is the Thomas Cook Group Plc. For more information, visit www.condor.com.
Contact:
Simone Giordano
navAero, Ab
+46 60 66 41 00
simone.giordano@navaero.com