Articles
Name | Author | |
---|---|---|
Case Study: Achieving Zero Inventory with Hyper-Connected and Automated Supply Chain at AMP Parts | David Rieth, Director Business Development, Airline MRO Parts (AMP) and Manoj Singh, Sr VP & Head of Aviation in Americas, Ramco Aviation | View article |
How I See IT: Digital threads and twins in MRO | Allan Bachan, VP, Managing Director, MRO Operations, ICF | View article |
Case Study: Virtual Reality Training at FL Techncs | Ramunas Paškevičius, Head of IT and Innovations, FL Technics | View article |
Solutions in Practice: Titan Airways uses CARDS Cloud Based Aircraft Transition Solution. | Dave Bunker, Engineering Director, Titan Airways | View article |
Case Study: 100% On Time Performance through Mobility and Paperless Solutions at JAL Engineering | Yuki Nakai, Director IT Planning, JAL Engineering | View article |
Case Study: Moving to a Cloud-based M&E System at Copa Airlines | Pablo Rousselin Avendaño, Senior Projects Manager, Copa Airlines | View article |
Case Study: 100% On Time Performance through Mobility and Paperless Solutions at JAL Engineering
Author: Yuki Nakai, Director IT Planning, JAL Engineering
Subscribe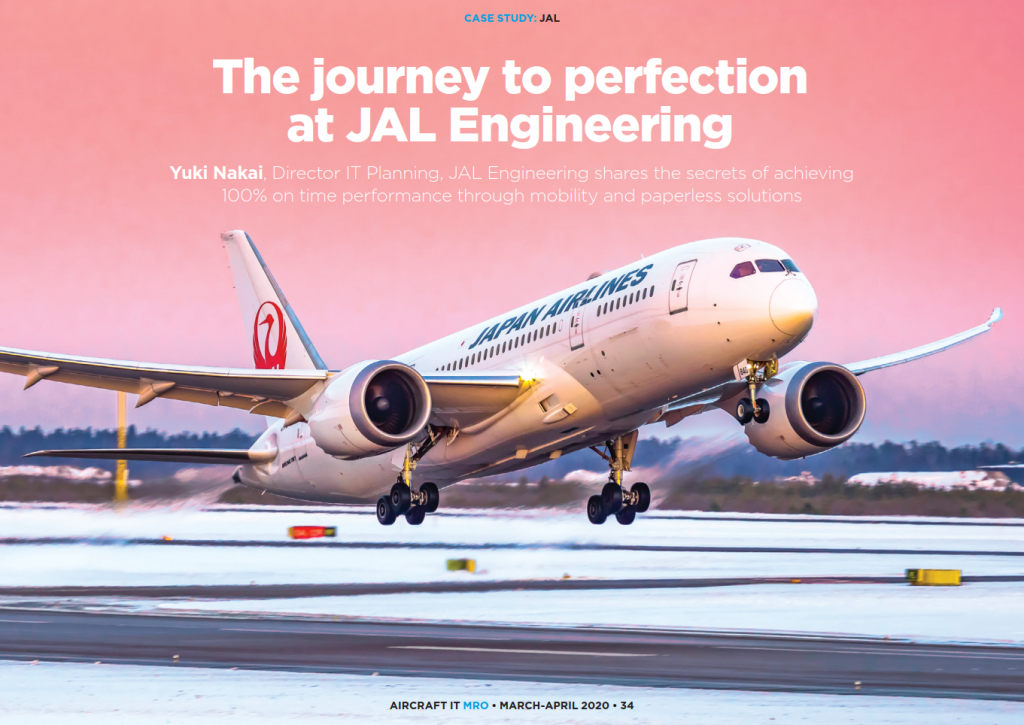
Yuki Nakai, Director IT Planning, JAL Engineering shares the secrets of achieving 100% on time performance through mobility and paperless solutions
This theme of this article will be to share with readers our experience at JAL Engineering of moving to a paperless and mobile M&E solution as the route to achieving a challenging efficiency objective. But first a few lines to tell you about JAL. Japan’s Flag Carrier flies more than 34 million domestic and more that 8.5 million international passengers between 56 Japanese and 350 global cities (figure 1).
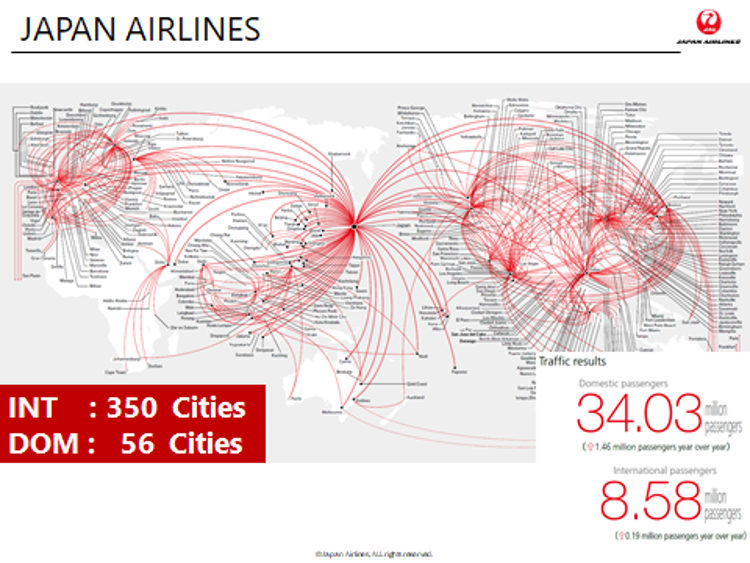
Figure 1
The fleet (figure 2) reflects the varied scope of JAL’s operations with large aircraft, Boeing 777, and medium size aircraft, Boeing 767 and 787 types as well as Boeing 737s and regional jets.
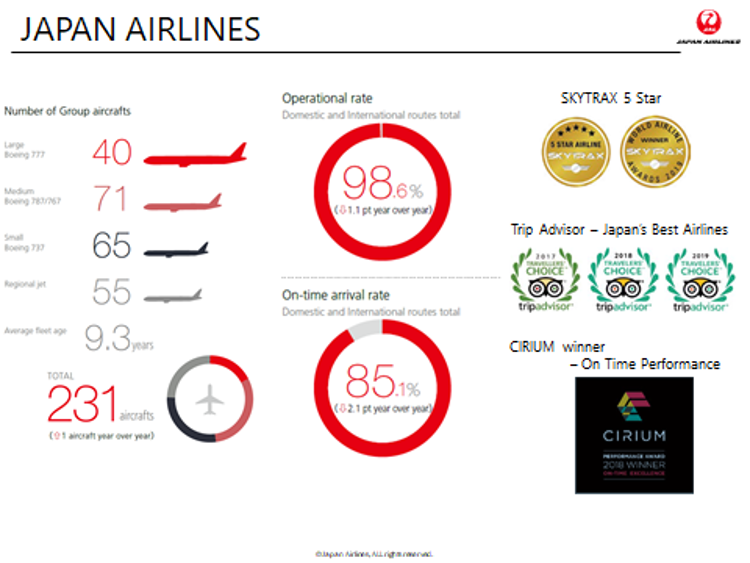
Figure 2
At the time of writing, JAL was also introducing the Airbus A350 XWB to the fleet. JAL Engineering looks after those aircraft in the JAL fleet and its subsidiaries’ fleets.
OUR ULTIMATE GOAL – 0-0-100
In the Japanese domestic market, what matters most to users is efficiency, so we are very proud that JAL achieves 98.6 percent operational rate for flights in the combined domestic and international markets as well as 85.1 percent on-time arrival rates, i.e. with zero minutes of delay. The reason that I mention this in because JAL’s domestic market competition is not other airlines but, especially in the domestic market, it is the Shinkansen train, sometimes known as the Bullet train, because their average delay time is just 24 seconds. JAL’s aircraft have to compete with those trains. We are proud of our 5 Star status with SKYTRAX and to have been voted Trip Advisor Travelers’ Choice as Japan’s Best Airline in three years, including 2018 and 2019 as well as Cirium’s On-Time Performance Award in 2018. But readers will know the complexity of modern aircraft making it really tough to achieve those kinds of performance rates (zero to 24 seconds delay) that the train manages, and we have to contend with weather and high traffic levels around the main airports at peak times.
All the above is the reason we have decided to concentrate on our ultimate goal of Zero–Zero–100 percent and the challenge that it generates. The key words in JAL are Zero–Zero–Hyaku (Hyaku means one hundred in Japanese) (figure 3). Let me explain.
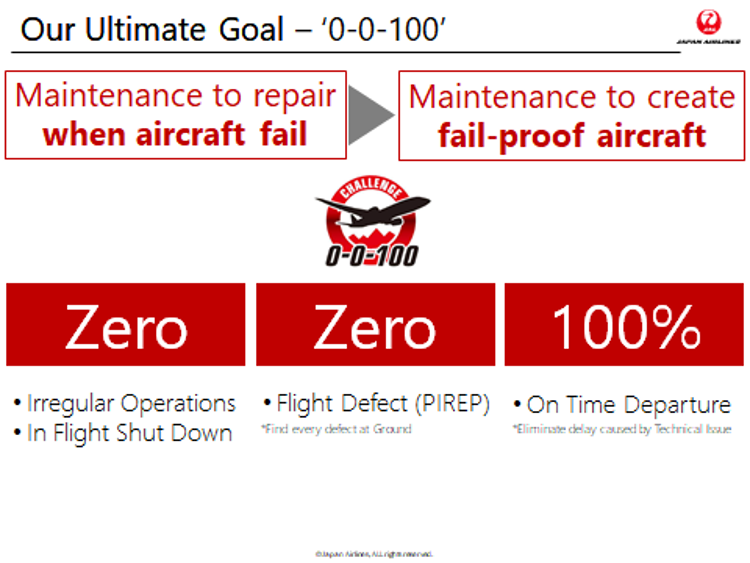
Figure 3
In the past, maintenance was focused on undertaking repairs when the aircraft failed. We have had to change that to maintenance focusing on creating fail-proof aircraft. For that to happen, we have to find any defects while the aircraft is on the ground and before it can fail; that is our ultimate target, to which end we have created a logo. The first ‘Zero’ means zero irregular operations or in-flight shut downs; the next ‘Zero’ means zero flight defects such as might appear in the pilot report (PIREP) – while there will always be defects, we aim to find every defect while the aircraft is on the ground, before take-off. The One Hundred (Hyaku) is for 100 percent on-time departures – of course, there can be other reasons for delays outside of JAL’s control but we aim to eliminate delays caused by technical issues within our control.
JAL’s management Board established this goal and my first thought, on hearing it, was that it’s a crazy idea. Zero irregular operations, zero in-flight defects, 100 percent on time departures seemed impossible. However, once that target of Zero-Zero-100/Hyaku had been set, the workforce really concentrated on how we might achieve it. It’s sometimes difficult to get JAL’s four thousand engineers to all face in one direction but this very strong objective to achieve Zero-Zero-100 was a clear goal on which the whole engineering team was able to focus.
One solution was digitalization. It is easy to improve aircraft quality and one way to do that is to replace the fleet with new generation aircraft. Ten years ago, Japan Airlines fleet mainstays were the Boeing 747 and the 737 classic plus we had DC10, and defects often manifested themselves during flights, causing on-ground delays. Today, the fleet includes the Boeing 787 and the Airbus A350 which are very stable; so that, renewing the fleet with new generation aircraft has been one part of our solution (figure 4).
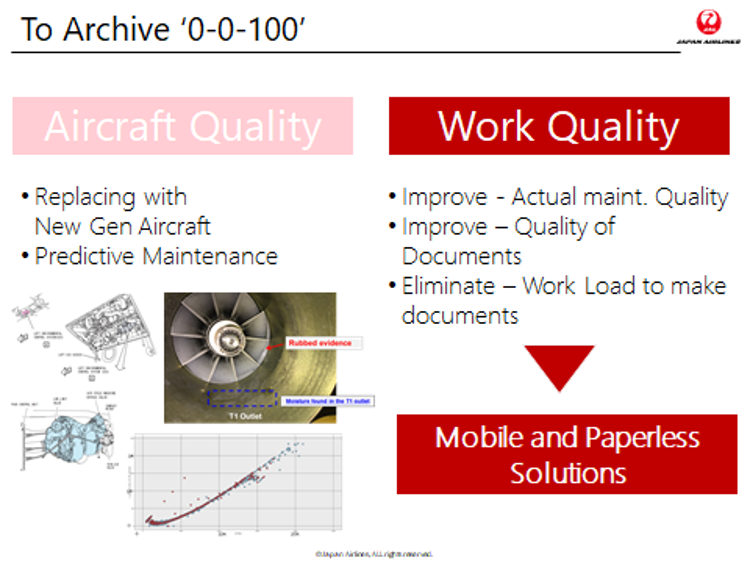
Figure 4
Another part of the solution has been that JAL is now undertaking predictive maintenance such as with the 787 Air Cycle Machine where we’re using sensor data with algorithms to find defects before they happen. That works well and we had, at the time of writing, 40 or 50 types of predictive algorithms. That means that there is now a high probability that we’ll identify potential trouble before an actual failure occurs. However, to improve identification of potential problems is one thing; to improve our work quality is more difficult. The challenge was: how to improve the quality of work, mechanics and maintenance, plus improve the quality of the recording documents and eliminate the workload to create those documents? The reason why it is important to eliminate the workload in document creation is that it is not a core function for the engineers. Engineers have to maintain and repair the aircraft, and improve the quality of the aircraft but document creation does not creating value in terms of the engineer’s job. As much as possible, we wanted to make time for the engineer to appraise the aircraft and make the analysis such as predictive maintenance or to better understand the details about that aircraft’s condition. So mobile and paperless solutions were, we believed, the best route to achieve the Zero-Zero-100.
THE SMART PROJECT – A FIVE YEAR JOURNEY
In figure 5, you will see the SMART Project, the name for JAL’s mobile and paperless solution which started in 2016-2017 with Phase 1.
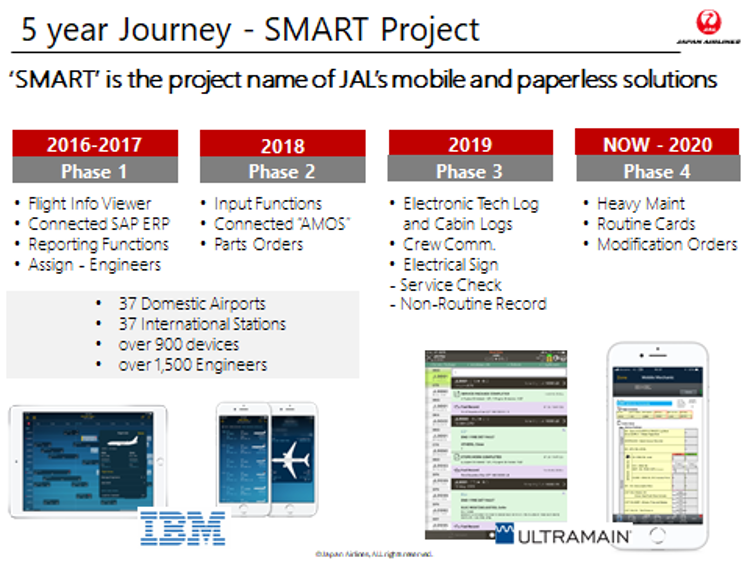
Figure 5
Phase 1 included the Flight Information Viewer and the connected SAP ERP plus reporting functions were implemented as well as the assigned engineer function. JAL worked with IBM (bottom left on figure) in creating the necessary Apps for the engineering manager to assign the aircraft (Assign Tech) while on the right is the Inspect and Turn, an iPhone Application to let each engineer know on which aircraft he has to work and which jobs are still remaining for the day plus details about the defect or the fuel or the departure time all in the one App. That was all created in 2016-2017 and implemented in April 2017 starting at Tokyo Narita Airport and the following week to Tokyo Haneda Airport. After another week, the system was rolled out to 37 domestic airports in one process before, one month later, expanding it to 37 international stations. At the time of writing, there were over 900 devices using the App and more than 1,500 engineers using the solution. The App doesn’t require too much training: not only is the IBM App good but it was also created with input from our engineers who are not IT specialists but understand repairing aircraft, know what information is required on the App. They co-operated with IBM and our internal system integrators, JAL Infotech Technology, as well as IT specialists, who supported the creation of the Apps. Every kind of information that the maintenance engineers require is on those Apps making it easy to understand.
In 2018, Phase 2, saw us getting involved with input functions to SAP ERP and getting the project connected with the AMOS system for smaller aircraft in the fleet plus the parts order function was also implemented. 2019 saw a giant leap with Phase 3 in which we collaborated with Ultramain Systems to implement Electronic Tech Logs and Cabin Logs as well as the Crew Communication System – one button for the cockpit crew to use. If they need the assistance of a mechanic, they just push that one button and the iPhone Facetime Application enables easy communication with the engineer. This phase also included the implementation of Electronic signatures for the Service Check and for Non-Routine Records.
Now, in 2020, Phase 4 will see the solution expanded to the heavy Maintenance Check, the Routine Cards and the Modification Orders as well as the other aspects of maintenance. The SMART Project is a five year journey; it isn’t easy going to a paperless and mobile solution but year by year people are learning how digitalization works, how we can go paperless, how to achieve Zero-Zero-100 with digital weapons.
Scope of Phase 3
As we’ve just completed it, I want to share with readers some more details about Phase 3. The paper items on the left of figure 6 are familiar for all airlines. In JAL now, the Tech Log form and the Cabin Log form will be using Ultramain’s ELB system and iPad Applications to be used by flight crews, cabin crews and maintenance crews.
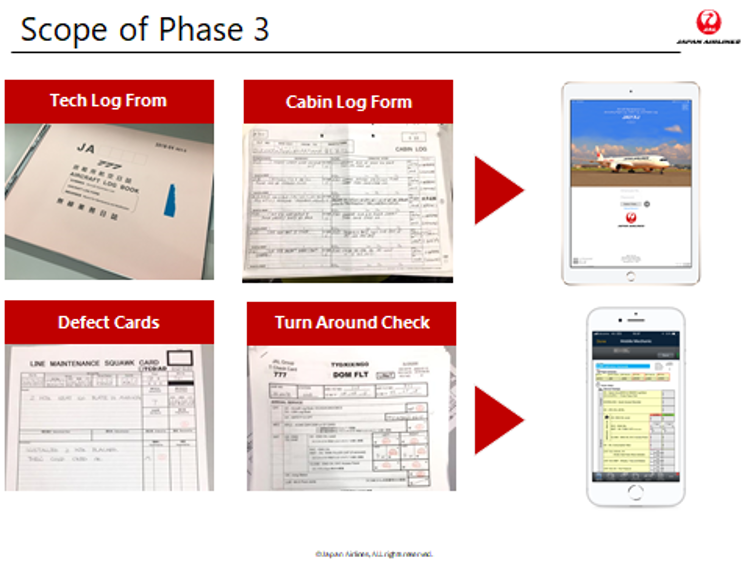
Figure 6
There are also records such as defect cards and turn around checks for which we use a mobile App and the Mobile Mechanic from the Ultramain system which JAL has introduced and merged with the existing IBM system.
FROM A PAPER-BASED TO A PAPERLESS SOLUTION
The traditional paper-based workflow was as in figure 7.
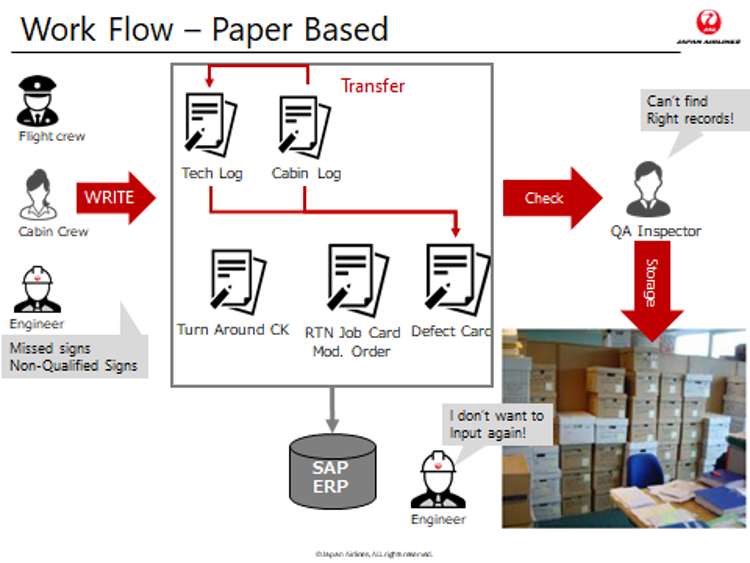
Figure 7
Flight crew and cabin crew were writing entries into the Tech Log and Cabin Log. Engineers were writing up the turnaround checks, routine job cards, modification orders and defect cards. So many people were involved and, in some cases they missed signing or, with so many different qualifications in the group, sometimes a signature would not be qualified because the wrong person had signed for a particular job or aircraft type. Sometimes there were cases where material that should have gone into the cabin log went to the tech log or the tech log and cabin log information was wrongly transferred to the defect cards… Finally, engineers had to input to the SAP ERP the same data in order to send it back to the office. People did not want to have to keep putting the same information into different parts of the system. That was a pain point in the past. Also, those documents after checking by the QA (Quality Assurance) Inspectors had to be stored in huge numbers of boxes (bottom right of figure). So, if it was necessary to find something, that entailed searching in the boxes, but sometimes we missed the records or could not find what we wanted and that was a problem.
The paperless solution, at the time of writing, looks like the plan in figure 8.

Figure 8
Of course, flight crews and cabin crews, and engineers are still in the system and the two iPads on the aircraft are being used for inputs by cockpit crew and cabin crew for their respective eLogs. The devices can also back each other up so that, if for some reason, the cockpit eLog device fails it is possible to use the cabin log device to accept inputs from the cockpit. The devices are connected peer-to-peer with Bluetooth so can be easily adapted even when Wi-Fi is not available on the flight. After landing a 4G LTE connection connects the devices to the ground server in a simultaneous real-time connection with the SAP ERP. Also, the data is transferred to the V9 server of the Ultramain system for transfer to the eRecord which is used for turnaround check cards. So, if the engineers find some defects while the aircraft is on the ground, those will be inputted to the eRecord system on an iPhone and is automatically transferred to the SAP ERP to complete. At the time of writing, in 2019, the Job cards and Modification cards were still on paper but the will be paperless in 2020. So, for the moment we remained on the routine job cards which were scanned into GE’s Airvault system to be finally archived. A QA Inspector also checked the quality of the record. But in the paperless system, it can be on the screen and can be easily found with just one click which will dramatically change the process of finding records should they be needed.
In figure 9 is a photo from the first day of the new system on 10th August 2019.
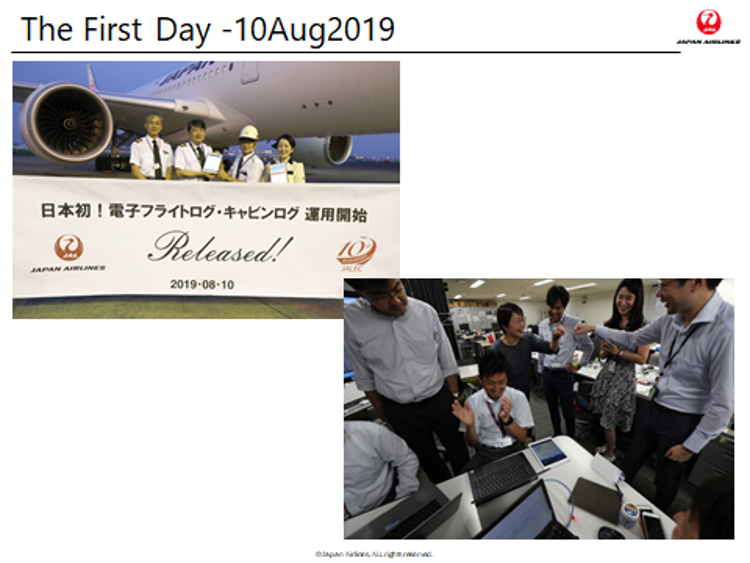
Figure 9
The writing is in Japanese but it says, ‘This is a first in Japan’ when the cockpit eLog and the cabin eLog started operation. In figure 10, we show the first record from the A350 aircraft created on the new eLog and being confirmed in JAL’s Operations office.
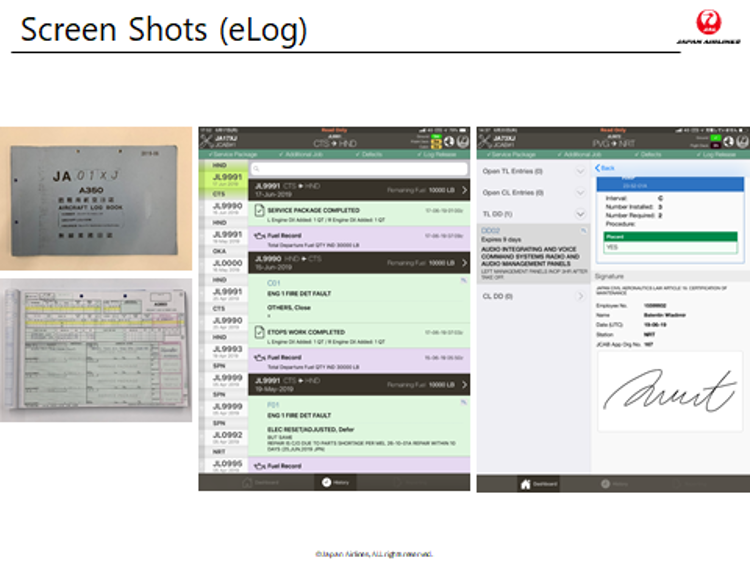
Figure 10
This is a photo of the A350 TechLog which was originally paper with a screenshot of the paperless version. There are three colors: black for Journey Logs; green for correction of technical records; and pink for fuel records. It’s now easy to find the aircraft history and what has happened with that aircraft while on the ground.
There is also a more detailed record for malfunctions that have occurred on the aircraft and a signature space. It is not a mandatory requirement from the regulator to have an electronic signature on these records but we decided to add this function for handwriting on the records because, in the past, on the paper logs, we signed our names to release the aircraft. Changing to the electronic system, engineers wanted to keep the signature so that they would have the confidence to release the aircraft. That they wanted to retain that aspect of the legacy culture was interesting.
Another function in the eLog is the ground Dashboard through which office workers can also see the aircraft status (figure 11)…
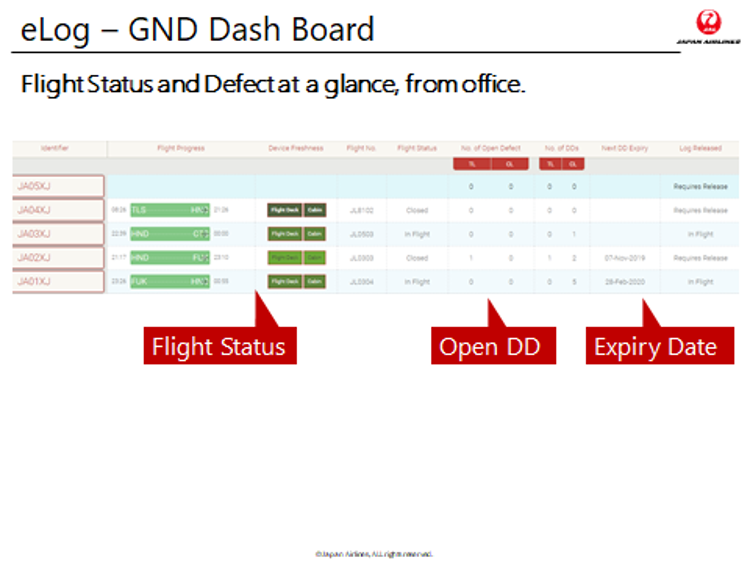
Figure 11
… flight status (which aircraft is going to which location), how many open defects are live for that aircraft and what is the expiry date of those defects; with all of that information available at a glance. In the past, we had to communicate with phones or by emails or fax to know what kind of defects were live for each aircraft and the target date by which they should be fixed. Now we can see the one table to know what aircraft has defects that are more important to have the resources assigned to them. These are interesting things. Cabin crew can report just either before arrival or just after landing so that we can prepare the resources to deal with any problem or defect that needs to be dealt with.
Figure 12 has some screenshots for eRecords.
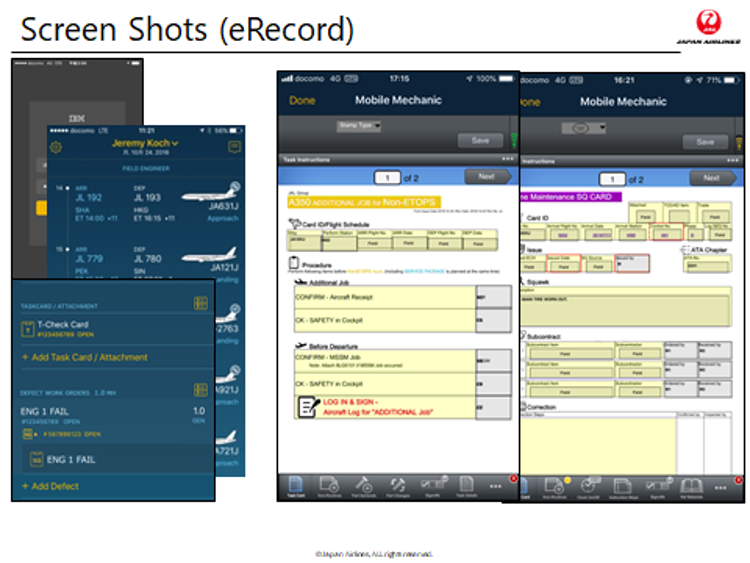
Figure 12
This is an IBM App, on the left, from which we can know what defects are on which aircraft and the task cards for the turnaround check. On the right are the cards for the defect records using the same design as the paper system so as not to confuse people between the digital and paper versions because some aircraft are still flying with paper. Common designs and input methods are being carried in to digitalization.
WORKING WITH THE REGULATOR
The final part of this article deals with working with the local regulator (figure 13) which, in Japan, is the JCAB (Japan Civil Aviation Bureau).
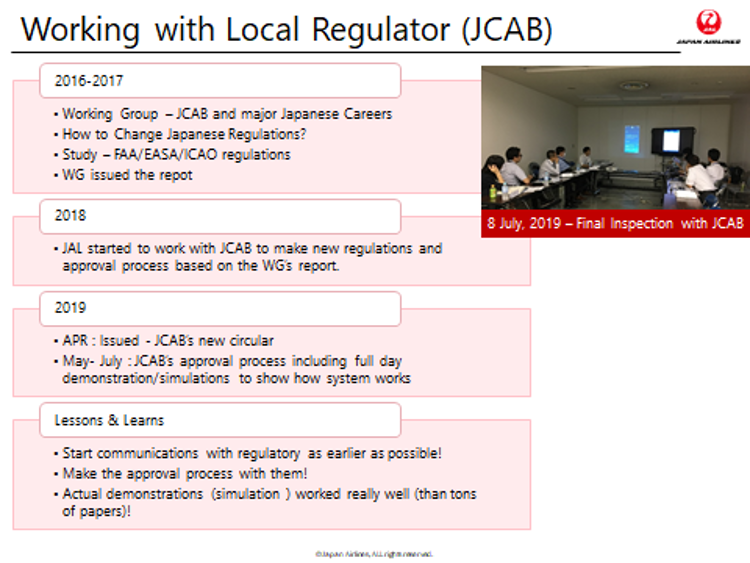
Figure 13
Starting from 2016-17, a working group was established with JCAB and the major Japanese carriers to consider how to change Japanese regulations. At that time, we didn’t have regulations of the sort that FAA, EASA, ICAO had to cover the latest technology developments so we wanted to create our own regulations but started with the FAA/EASA/ICAO regulations from which the working group issued a report. Then, in 2018, JAL started to work with JCAB to make new regulations and approval process based on the WG’s report. The most important things to show were the devices and the actual design of the system – seeing is believing. At first the group from JCAB didn’t understand these developments, what is digitalization, what is the goal in digitalization but once they knew about that (‘this is the application’, ‘this is the concept of the software’) they could easily understand and we could negotiate the approval process.
In April 2019, JCAB issued a new local circular to cover the use of digital applications for data records then, in May to July of that year, rolled out its approval process which includes a full day demonstration/simulations to show how system works (JAL’s final approval day is in the photograph at top right of the figure). We had to show how engineers behave with digital records using a parallel run of an actual aircraft operation with a 45 minutes turnaround plus what involvement there would be from the cockpit crew and cabin crew as well as the maintenance crew; showing how they do the jobs with paper and then using the new records system.
Lessons learned
The first lesson was to start communications with the regulator as early as possible; that is the most important thing, to establish an approval process to work with them. Also, actual demonstrations and a simulations work better than tons of papers. Of course, there is a place for explanatory papers but demonstration is most powerful.
CONCLUSION
Our target was not in and of itself to go paperless but to achieve that Zero-Zero-Hyaku (0-0-100) goal as our ultimate target Paperless was the means to achieve our objective, not the end in itself. Working with the regulator, from the beginning we realized that seeing is believing plus, although the cockpit crew and engineering do different things, with good communication they can easily understand each other and work together. Digital transformation makes people happy; our engineers are happy to use the devices and the solutions. A paperless solution works best if the engineers are involved with creating the Applications because, having been involved in the transformation, they will then easily accept the new system.
Contributor’s Details
Yuki Nakai
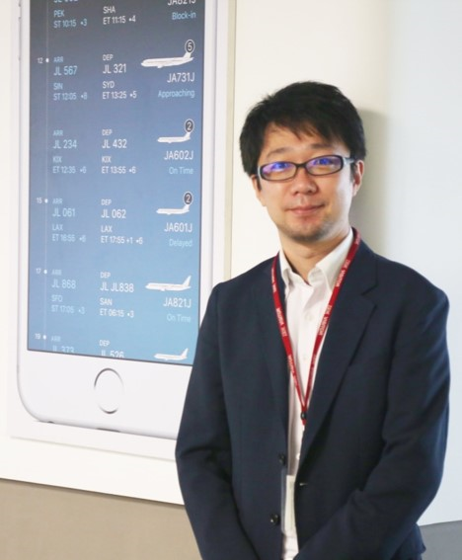
Yuki joined JAL in 2002 as an Aircraft Engineer then, in 2007-2008 joined the migration team implementing JAL’s 1st ERP system. In 2008 he was appointed Project Manager – Aircraft Cabin Interior and, in 2013, Director – Fleet Transaction /Procurement. Since 2017 Yuki has been Senior Director – IT Planning, leading 30 staff to achieve 24/7 Operations of the M&E System and digital transformation of aircraft maintenance including predictive maintenance and AI.
JAL Engineering
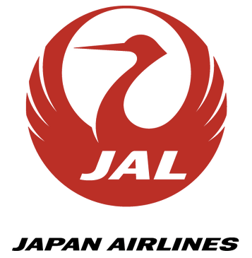
JAL Engineering is the wholly owned Maintenance and Engineering Division of Japan Airlines (JAL), managing 100% of JAL aircraft and providing MRO services to more than 50 global operators.
Ultramain

Ultramain Systems delivers simple mobile paperless electronic logbook ELB software along with a comprehensive suite of MRO / M&E software. A proven aviation software provider, Ultramain has aircraft M&E / MRO customers running paperless, end-to-end solutions, from the cockpit to the ground, with solutions covering the aircraft logbook, line and base maintenance operations, and MRO operations.
Comments (0)
There are currently no comments about this article.
To post a comment, please login or subscribe.