Articles
Name | Author | |
---|---|---|
Wearable M&E Devices – The new era of hands free computing | Suresh Subramanian, Principal Consultant-Aviation, Ramco | View article |
Column: How I See IT – 2015: The year we (finally) go mobile | Paul Saunders, Solution Manager, Flatirons Solutions | View article |
Ask an Expert | Michael Wm. Denis, President, Aviation Wikinomics, Inc. | View article |
Flexible MRO IT Systems for CAMO | Mark Rogers, Commercial Manager, McLarens Aviation | View article |
Case Study: American Airlines: Mobility for Mechanics | Blair Gregg, Managing Director of Technical Strategy For Maintenance & Engineering, American Airlines | View article |
TAP M&E RFID Case Study: Achieving visibility and traceability | Fernando F. Matos, Head of Information Technologies, and Carlos Quinta, Head of RFID Competence Center, MEGASIS TAP IT | View article |
The top five key Civil Aviation MRO trends to watch out for in 2015 | Espen Olsen, European Director for Aerospace & Defence, IFS | View article |
TAP M&E RFID Case Study: Achieving visibility and traceability
Author: Fernando F. Matos, Head of Information Technologies, and Carlos Quinta, Head of RFID Competence Center, MEGASIS TAP IT
SubscribeRFID technology offers what an MRO needs but first it needs to be successfully introduced say Fernando F. Matos, Head of Information Technologies and Carlos Quinta Head of RFID Competence Center at MEGASIS TAP IT owned department
%20image%205~%20RFID%20in%20use_sm.jpg)
Although TAP is a state owned company, it is financially self-sufficient and generates its own revenue which means that there is an onus on the airline to be efficient. It was bearing this in mind that we started to look at how we could apply RFID solutions. The first prompt in this direction was when, in 2007, we had an engineering customer who wanted to ensure that we kept their tools separate from TAP M&E’s tools; and so we started to look at the possibilities of RFID which was then beginning to appear in industrial applications. The problem was that we had no real knowledge about the technology and had some difficulty in specifying the problem that we wanted to address; plus TAP M&E didn’t have a team who could be assigned for that kind of work.
That said, we did know what problems can occur in an engineering workshop… parts get mislaid, leading to disruption of work because you don’t know in which workstation the part is being held; that, in turn, detracts from safety, quality and efficiency which are all very important matters for an MRO; especially safety. We thought that RFID could be the answer to all of these challenges because RFID is about visibility, physical visibility, tough visibility.
In November 2007, AIRBUS was looking for a partner to develop an RFID project and we took that opportunity, by creating a team with them, AIRBUS, MEGASIS (the TAP-owned IT unit) and TAP M&E.
FIRST PROJECT AND LESSONS LEARNED
This project, MEERA (Mobile Enabled Engine Repair Application) took around three years to go live: from negotiating the partnership, business case and proof of concept, to implementation. Mistakes were made.
The first mistake resulted from a very good business case validated by an excellent proof of concept which showed a hugely valuable return on investment. However, whenever you do a proof of concept, do it by replicating exactly the normal operation, be it in human, material or other terms.
We were separated from the real production and, when we asked them, mechanics suggested that everything was always put away in its right place with proper labels so that, when we tried to scan it, everything would be OK. However, when we went into production, we discovered that, in reality, a lot of labels were not written.
Notwithstanding that, by 2012 we were the first MRO to have a fully integrated and operational application of RFID to aircraft engine components (see Aircraft IT volume 1 issue 5 ‘Spring 2012’) and we were able to draw some conclusions from the experience. It had taken a large investment of around €750,000 and we had expected to see a return on investment (ROI) of four times that outlay in one year: that, as it turned out, was very, very optimistic. With a new technology such as RFID, there is a slow learning curve. You have to tell mechanics that even when they think that they know where spares and components are, they still have to take the reader with them. Otherwise, they’ll keep looking for the parts where they used to be and, sometimes, they won’t find them there. Our optimism had been misplaced.
Similarly with the hardware, the first scanners we had envisaged at proof of concept stage assumed that everything would be stacked neatly on the shelves whereas, in reality, the mechanics put parts onto the rack in a way that meant that labels were at all sorts of angles. As a result, we had to buy circular polarization RFID readers that could cope with this reality and we had to adapt the system accordingly, which meant even more cost. So the lesson is, build a portfolio of hardware and test it intensively. And then there was the old chestnut of change management. This is a new tool and a new technology but people need to understand that it can’t solve all of their problems. It will make some processes more efficient but we need to identify which ones.
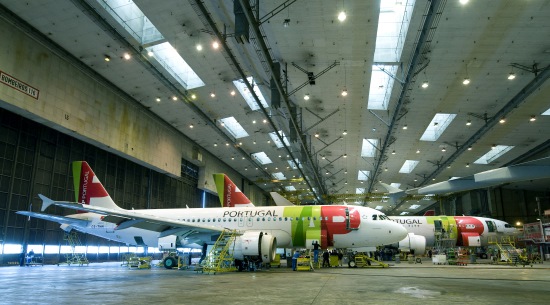
So, out of all this, we had to define an RFID strategy that was aligned to our business processes, architecture and integration. It’s not a separate tool or technology; but, rather like mobility today, it has to be a part of the overall MRO maintenance information system. This is really important. For our strategy, we decided that, after we had incorporated engine parts into the new system, we would next go to tools and GSEs (ground support equipment). Then, because, from 2017, we will be taking delivery of a new fleet of A350 aircraft with RFID incorporated in more than 400 parts including life vests and seats, we will have to align this within our strategy and what we have already defined. Beyond that we’ll go to chemical products to check their shelf life. Then we’ll go on to integrating RFID with our mobility program in line maintenance.
We learned a lot of lessons from this first project and we know that we made a lot of mistakes but, as Jazz trumpeter Miles Davis said, “When you hit a wrong note, it’s the next note that makes it good or bad.” As with Jazz, we were able to use our wrong notes to create a great overall outcome.
NEXT STEPS AND A STRATEGY FOR THE FUTURE
Now, having looked at the technology applied to an engine repair shop, we want to consider RFID technology combined with bar code technology and how both technologies can deliver visibility and traceability for tools, and ground support equipment (GSE). Putting this in the context of TAP M&E; as an MRO we have a lot of tools more than half of which are specific aircraft maintenance tools, the rest being generic tools and calibrated tools. There are also numerous GSEs. Our current system, which has been running over the past six years, is an offline system running within a PDA covering four tool stores run by seven store managers. Every tool has a barcode either on the tool or in its drawer.
GSEs are not controlled and are available for whoever needs them to complete a job. They take the GSE, do the job and should then return the GSE to its previous location but, in most cases, that doesn’t happen, so significant time is spent searching misplaced GSEs.
For instance, at our Lisbon base tools and GSEs are constantly moving between the three hangars and parking zones, a lot of movements; so we need to get better visibility of these tools and GSEs. Because we have an offline system which relies on people manually uploading updates, we have visibility problems. An example would be where a tool is checked out for a specific aircraft, and for a specific mechanic, checked back in to the store and in the meanwhile checked out again for a different aircraft and mechanic. If the tool store manager hasn’t yet uploaded the information to the back end system or if it’s only uploaded every hour or even at the end of every shift, until that upload happens, there will be no reliable information regarding the availability of that tool and all the movements that have been done.
AN APPROPRIATE SOLUTION FOR GSEs
GSEs are used on a self-service basis and we need to get visibility for the most critical ones, the most needed and most expensive; plus the ones that we have in small quantities. Again, we have visibility issues and tracking issues because we need to know where equipment is all the time which we cannot manage with any current system. And, as readers will know, the audit department can make life very difficult if we’re not able to address those issues, especially with tools. So those are currently our main pain points as far as keeping track of tools and GSEs are concerned.
Notwithstanding those pain points and requirements, when we did our cost benefit analysis we realized that it would be difficult to make a strong business case from a purely financial point of view; so we needed to take a different approach. The approach we settled on was to focus on quality, safety – FOD (foreign object damage) risk mitigation – and image – when a customer wants to have a check carried out in your facilities, he will want to know what tools are being used in an aircraft and, if you can’t answer, you might lose the customer. Citing those three drivers, we managed to get approval for our solution.
In the end we decided to use RFID for our GSEs but not for tools. RFID is a robust technology which means that we can leave GSEs out in the parking zones for prolonged periods and still be able to read the RFID tag. Providing the process is executed the way it is supposed to be, RFID will deliver real-time visibility and traceability: and will enable us to perform a fast inventory and search which is not so easy to manage with barcodes. That’s why we decided to use this technology to achieve visibility and traceability of GSEs. In future, every time somebody wants to move a GSE between two locations, he will be able to use the RFID technology to record that movement in the system, which is not what we do today. And, using RFID tags with the GSEs and at the locations, whenever a GSE gets sent to a location, we’ll know where it is.
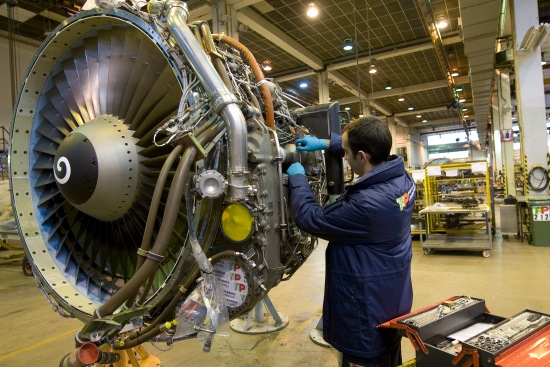
AN APPROPRIATE SOLUTION FOR TOOLS
On the other side of the coin, readers might ask why we won’t immediately be using the same technology for tools. It’s a case of ‘horses for courses’. First of all, our tools are all already barcoded, which is the easiest thing to do. And second, it will be quite a challenge, given that we have around 20,000 tools, to decide how many RFID tag types (form factors) will be needed to cater for the hundreds of different sizes and shapes that we have. Also, on what tools do we decide to put an RFID tag: calibrated tools; generic tools? What would be the rational? It wouldn’t also be possible to tag a lot of small tools as well. It’s quite a challenge. And, as we’ve already seen, one of the benefits of RFID technology is that it allows users make a fast inventory and to search for a specific asset, which we don’t do on a regular basis, as well as search at tool store level because it’s a controlled environment where barcode technology works well – it’s reliable and trustworthy. For these reasons, for the time being we will continue to work with the way it is today… using barcodes for tools.
In the near future, as an enabler for continuous improvement processes at aircraft production level , we plan to bring some specific tools close to the aircraft – calibrated tools and specific aircraft maintenance tools; those tools that we know we’ll always need for an ‘A’ check. When that happens, it will make sense to use RFID technology because we’ll probably need to create an inventory and we may need to search for tools. But, at present, tools are managed in a controlled environment within the tool stores and, just for checking-in and checking-out tools, we don’t need RFID technology.
One thing of which we’ve had to take account is that in order to get real-time visibility with RFID technology you need a wireless infrastructure – you can’t use an offline solution such as the one that we have today. So we are going to use a wireless infrastructure and a mobile solution to record the movements of GSEs and tools. As part of the overall system architecture We are going to use a back office solution as well with the information recorded in the PDA so that management has immediate visibility of all tools and GSEs. In summary, we will use a combination of bar code technology for tools and passive RFID technology for GSEs, plus the new mobile and wireless architecture to solve our current problems about visibility and traceability of tools.
%20image%201~%20Login%20MTMS%20Backoffice_SM.jpg)
%20image%202~%20MTMS%20Events%20Backoffice_sm.jpg)
%20image%203~%20MTMS%20Tools%20Backoffice_sm.jpg)
The system is going to be called ‘mobile tooling management system’ (MTMS) and will bring TAP MRO’s tool management and GSE management systems right up to date using the latest but also the most appropriate technology for each job.
For a selection of
MTMS screens click here.
AUTHORS
Fernando Matos is a telecommunications and electronic engineering graduate of Lisbon Technical University and joined TAP Maintenance & Engineering in 1980. In 1991 he was Project Manager for TAP M&E Information Strategy Plan and from 1994 co-ordinated development of TAP’s in-house integrated IT platform, COSMOS. He became head of TAP M&E IT in 2005 and has for three years also been in charge of IT at TAP Maintenance & Engineering, Brazil.
Carlos Quinta joined Megasis, a subsidiary of TAP Portugal group providing IT services, in 1991. He is currently the Head of RFID Competence Center. With almost 15 years of experience as an MRO Senior Project Manager and having worked closely with Airbus since 2009 with RFID technology, he is currently responsible for all RFID solutions running within TAP M&E as well as any business process initiative where this technology might prove to be an enabler to accomplish M&E business needs.
TAP Portugal is Portugal’s leading airline and a member of Star Alliance. The airline was voted ‘World’s Leading Airline to Africa’ (2011 and 2012), ‘World’s Leading Airline to South America’ (2009, 2010, 2011 and 2012) and ‘Best European Airline’ (2011). Last year, TAP flew 10.7 million passengers to 198 destinations with a fleet, at the time of writing, numbering 77 aircraft, including six introduced during 2014.
Comments (0)
There are currently no comments about this article.
To post a comment, please login or subscribe.