Articles
Name | Author | |
---|---|---|
Aircraft M&E / MRO Software Survey 2015 | John Hancock, Editor, Aircraft IT | View article |
Column: How I see IT – Wearables 2.0: leveraging your body parts for MRO, including your feet? | Paul Saunders, Solution Manager, Flatirons Solutions | View article |
Seize the digital future for Aviation MRO business | Jacob Baiju, Practice Head, MRO IT Services, Hexaware Technologies | View article |
Big data in aircraft maintenance | Sander de Bree, Managing Director, ExSyn Aviation Solutions | View article |
MRO Technology Innovations | Ravinder Pal Singh, Global Chief Information and Technology Officer, Air Works India | View article |
Seize the digital future for Aviation MRO business
Author: Jacob Baiju, Practice Head, MRO IT Services, Hexaware Technologies
SubscribeStandfirst Jacob Baiju, Practice Head, MRO IT Services at Hexaware Technologies looks to the future by understanding the past and considering the technology we’ll have to use
The future is ours to make
“The best way to predict your future is to create it”. Abraham Lincoln said it first; countless others have said it since and it remains true. But part of that creation process relies on understanding what forces have driven us to where we are today and what patterns can be discerned in the past that might help us in understanding what future we should prepare for. So, before looking to the future, it might be useful to look back a decade or so, to the technology we were using around 2004 to 2006. We will probably have been looking at a green screen as part of our legacy M&E system. Some would have graduated to Windows or to a web platform but most IT users in aircraft MRO will still have been communicating with their system through a green screen. And, nearby, there will probably have been a technical records room with stacks of paper files. What wasn’t around then was any sort of Smart phone such as an iPhone or any tablet such as an iPad because neither device existed. There were tablets of a sort from Palm but they were not very popular.
If in 2004 to 2006 we had been having a discussion about ‘what will be the future for MRO IT in ten years from now – 2015?’ could anybody have predicted pilots using iPads as electronic flight bags (EFBs) or have expected that the technical records room would disappear, with every record being digitized and indexed for easy access? Who would have thought that MRO technicians would be able to look up manuals in an electronic and easily searched form from a small hand-held device? If anybody had advanced predictions like that, we wouldn’t have believed them because we could not have imagined that we would progress so far in such a short time; but we did.
On that basis, there is no reason to believe that progress and change between now and 2020 will be any different… we could be working in a completely different technology landscape from where we are today. The question is; are we prepared as an industry, as product builders, as partners, as OEMs (original equipment manufacturers) to move towards that goal of a further improved technology environment by 2020? Are we ready to create our future?
IT enablers for MRO and airline maintenance
These are all key thoughts but I really don’t want, in this article, to predict what our IT world will look like in the future. However, I would like to share some experiences that we believe will shape that future and determine our journey to it. And, while I might not wish to predict exactly what MRO IT will look like in 2020, we already know that we will have to manage a transformation of our systems; to build an intelligence layer over those systems as well as leveraging mobility, cloud and other cutting edge technologies. But even we accept all of that, are we prepared, are we willing to do what it will take and are we already taking the initiatives that will be needed to get from where we are today to whatever future is in store for us?
I recently met with a senior maintenance director in a large airline. Although a professional with a great deal of experience in maintenance and engineering, when it comes to technology, he remains to be convinced about the value of tablets or smartphones; in short he is comfortable with the old school technology with which he is familiar. Yet when we discussed initiatives that he has underway, one was to roll-out an iPad application for his line maintenance technicians. That surprised me because I hadn’t thought he would be interested in these new technologies. So I asked why he had undertaken this initiative and he explained that he could clearly see the productivity gains that would accrue to his team from the new technology; he might be ‘old school’ but he understands the importance of technology to enhance the processes for which he and his team are responsible.
MRO IT in the future
So, what is the IT future for MRO? If you were to be asked what would be your wishes for 2020, the answers should not be any different than if you were asked what you want today. Whether in the past, today or in in the future, you would want to run an efficient, safe operation and to achieve that profitably. The difference will be between how you achieve it today and how you will achieve it in 2020 in a different competitive landscape with new technologies available, new generation systems with the latest technologies of the day and much more information from which to create decision making analytics. There will be a much more integrated supply chain than even today and the workforce will be fully technology enabled. But we still need to think how we will get to that future reality.
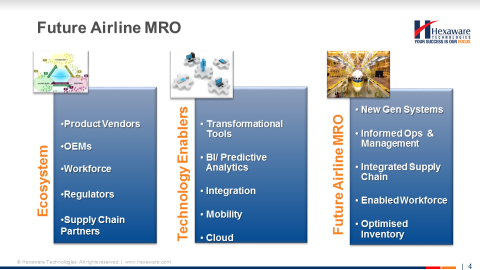
• Product vendors who provide the platforms;
• OEMs on whose aircraft we work;
• Our own workforce, which is subject to constant change;
• Regulators who specify the framework within which must operate; and
• Our supply chain partners.
We have to include all of these actors in our future vision through various business tools, BI (business intelligence), through integration and the latest technologies such as mobility and cloud. To make this a little clearer, I have created a road map for how we can get from where we are today to where we want to be in the future.
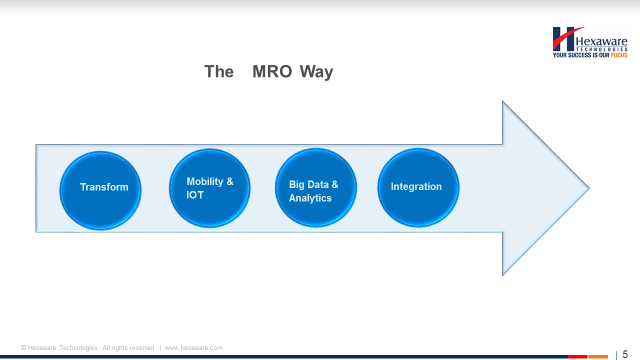
Once a system is in place, it will be possible to build analytics on top of the new system. It will also be possible to enable the workforce using mobility. And last, but not least, to integrate with as many customers, suppliers and OEMs as possible, for a smooth information flow as the basis for a very efficient operation.
Transformation and migration
At a recent conference I met a friend and colleague who I have met at many such events where he has been looking for ideas to help in selecting a new system to replace his old legacy application. On this occasion, he explained that he had finally settled on a new system; he’d achieved buy-in from all the stakeholders, had got the budget approved and was going to sign the contract for the new system. I asked whether he’d planned for his data migration, integration and testing: the answer was ‘no’ because he didn’t expect those processes to be that complex. I felt obliged to explain what lay ahead in this project – that it is not complex but is extremely complex – and that how one determines the plan to manage these steps will determine what value can be derived from the new system. In extremis, it could even be career defining inasmuch as you could lose your job if you don’t think about this.
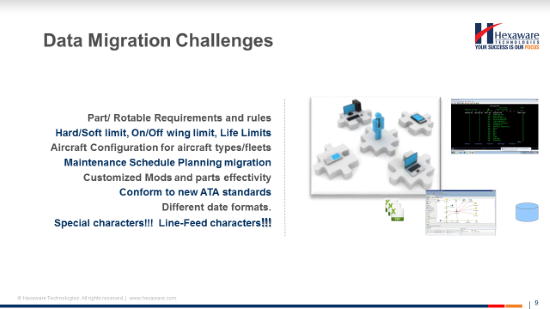
Popular legacy applications were developed years (decades) ago so that many of those who supported the applications, understood the data structure and knew how to extract from it, are no longer in the business. There are also a lot of custom and home grown applications still in use to deal with limitations in legacy applications or with changes that have happened in the industry. And there is a lot of non-system data that the new system will require but that is currently on paper, in PDFs or other off-system applications. A due diligence exercise will usually reveal more data to be migrated than that in the legacy system alone.
Vendors might well have the functionality and the process but the user has to provide the right clean data… as the popular IT adage puts it: ‘Garbage In, Garbage Out’. No matter how many millions of dollars a new system has cost, if the data going in is garbage, there will be no return on that investment: the new system will look good but will probably function worse than the old system. There must be a plan to address data migration challenges. In this, one important challenge is the ‘extraction’ of data from legacy systems and other sources (see above) which requires a range of talents to convert them to a standard format from which they can be transferred.
Even at this stage, there will be a number of checks to be applied as the data is transferred. In a nutshell, if we look at a high level, we can see the different stages of data migration…
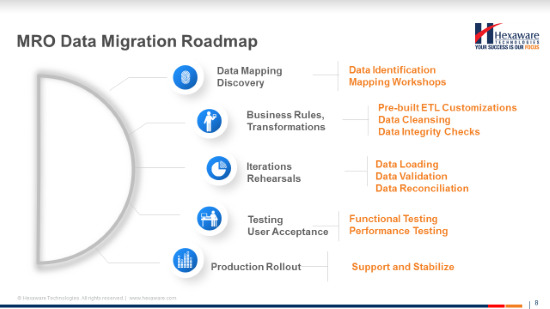
Case Study
To illustrate what is possible, we have recently completed a migration from two existing MRO systems (one for maintenance engineering and one for materials management) into AMOS for a large EMEA airline, Part 145 certified, with a fleet of more than 150 aircraft and with ten years of historical data to transfer. The plan was for an 18 month migration and that was achieved despite encountering many data quality issues and data was in multiple formats. We were also able to ensure that the data integration and quality in the target application were good enough to leverage all the functionalities of the new system, and ensure a return on investment.
Data warehouse and analytics
Now, having migrated to a new system, what additional value can be realized for MRO? One key subject area of interest is in analytics. There is no doubt that it will shape the future of our business. Some product vendors and OEMs are developing a raft of operational analytics around the data generated by aircraft which will prove very useful for the industry especially in securing a safe future. But we still need to have an enterprise-wide consolidation of pure data to support analytics throughout the business to generate a competitive advantage.
One airline with which I have worked has recently undertaken an initiative to optimize inventory with the objective of reducing that inventory by $100million. This is a common objective but how can it be achieved? It is first important to understand the data around the inventory – what are fast moving and slow moving items; what are critical items; how is supplier performance around these items? Again, there are challenges, especially the integration of data from different systems, and also opportunities that can be derived from the analytics platform when it’s applied as part of a proactive maintenance program.
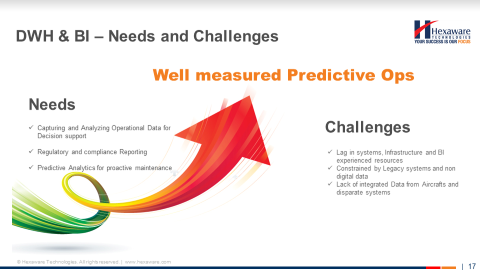
Predictive maintenance
What all of the above is leading to is ‘what can we do with all of this data?’ For MRO, one important application is predictive maintenance, something of which any head of maintenance and engineering today will be dreaming.
Preventive maintenance has been with us for a long time but still we cannot predict failures as much as we would wish. Predictive maintenance will be a boon for the industry, supporting safer and more efficient flights, and is definitely part of that future landscape referred to in the early part of this article. Also, predictive maintenance need not be restricted to operations: predictive analytics can be applicable in a range of areas such as inventory, labour skills or planning. Airlines and MROs will need to build a platform to support predictive maintenance over and above whatever the vendors and OEMs can offer: the question is ‘how?’
E-enablement: mobility and integration
Once a proper platform has been established with proper analytics – the data warehouse has been built – what is the next step? How can all the actors around the business be enabled. New technologies offer many opportunities to enable those actors quickly and easily; those new technologies fall into the phenomenon SMAC (social mobility and cloud); delivering flexibility and integration, and data capture capabilities. But, no matter how good they might be, how can these platforms be leveraged to deliver all of the benefits that we want?
Mobility and cloud: emerging trends
The future
This is the future for which we must all prepare and which we must create and there are initiatives in the industry to drive towards that future. But, come what may, that future of MRO IT is in our own hands.
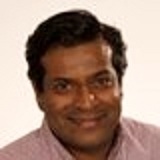
Jacob Baiju, Practice Head MRO IT Services, Hexaware Technologies
Jacob Baiju has over 15 years’ experience in IT consulting with the travel and transportation industry. In his many years with the industry he has worked in various roles including consultancy, program management and practice development. He now leads the MRO practice for Hexaware globally with a focus on providing innovative solution frameworks for the MRO Industry in key areas for their business transformation needs.
Hexaware
Hexaware’s MRO IT service is part of a Global Travel and Transportation practice with over 1200 consultants working with leading travel and transportation customers. Catering to three out of the world’s Top 10 airlines, Hexaware is one of the fastest growing IT services organizations. The MRO practice leverages its experience to create tools and services which help customers efficiently migrate to newer M&E Systems, implementing industry specific Data Warehouses and Analytics as well as Independent Application Testing Suites.
Comments (0)
There are currently no comments about this article.
To post a comment, please login or subscribe.