Articles
Name | Author | |
---|---|---|
The Power of Personalized & Targeted Distribution for WestJet Engineers | James Homeniuk, manager of Technical Standards and Audit Compliance with Lyndsay Steffler, Analyst, Technical Standards and Audit; both at WestJet | View article |
Improving the operational and financial performance of KAEMS MRO through digital transformation | Mr. Park Won, VP & Head of Operations at Korean Aircraft Engineering Maintenance Services (KAEMS) | View article |
Making the change to paperless at USA Jet | Pete Sasson, Project Manager, USA Jet / Active Aero | View article |
IATA Industry Restart Plan | Iryna Khomenko, Manager, Operational Efficiency, IATA TechOps | View article |
Managing digital assets with digital systems | Allan Bachan, VP, Managing Director, MRO Operations, ICF | View article |
Making the change to paperless at USA Jet
Author: Pete Sasson, Project Manager, USA Jet / Active Aero
SubscribePete Sasson, Project Manager, USA Jet / Active Aero shares the challenges and advantages of implementing e-Signatures.
In this article I want to cover some facets that arose with the issue of implementing e-Signatures at USA Jet Airlines. These range from the challenges we faced to the current status of the project, future plans resulting from the project and some notes about implementation projects that will, hopefully, help readers contemplating a similar program of change.
A brief introduction to me: my background was in the United States Marine Corps before starting as a mechanic and moving on to become Director of Quality in a regional airline. From that I moved into IT which, in turn, led to me undertaking AMOS implementations including, quite recently at the time of writing, an implementation at USA Jet to move to e-Signatures and near-full paperless operations.
THE CHALLENGES
USA Jet was largely still using a paper-based system when I first became involved but was already a year into an AMOS implementation; however, things were not going as fast as they might have wished. One challenge they faced was that a lot of paperwork was being sent to and from their stations but it was often getting lost, either mechanics not taking it off the aircraft or it may not have even made it onto the aircraft in the first place. The result of that was that maintenance jobs were being held up, they weren’t even managing to get sign-offs due on time; there was a lot of need to re-create paperwork or contact mechanics. There were often delays between the sign-off and the system update because people had to read the material, and then others were reviewing the paperwork: it ultimately led to lost time and productivity due to having to fix those paperwork issues.
Change management was also a significant challenge because there were many departmental silos owing to the absence of clear or defined processes. It wasn’t clear who was supposed to do what, and that created infighting between departments and within departments. Alongside that, there was a lot of user resistance to change. Some of that could be attributed to more established staff being familiar and comfortable with the way things had always been done but that was, to an extent, offset by a cohort of younger staff who were open to new ideas. However, there were very few staff in between those two groups.
Operationally, there was not good fleet visibility as to where the aircraft were in their maintenance schedule and data management was virtually non-existent plus the inventory included a lot of inaccuracies because the paper system just could not manage it well.
CURRENT STATUS
AMOS Version 12 was launched at USA Jet on May 28 2019 And, on the next day, May 29, the airline was granted the OpSpec A025 from the FAA which allowed electronic signatures in the digital records keeping. That granting was based on demos given to the FAA on AMOS with all the business processes that had been developed beforehand. So, we’re currently utilizing the AMOS e-Signature functionality which gave us the opportunity to establish a hybrid system because, at that point, we weren’t ready technically to go fully paperless, so all the sign-offs are completed within AMOS and then it goes through a records review, and once that’s finished the final document is printed out and maintained in a file system. The expectation is that USA Jet will go paperless in due course. Nowadays, inventory issues are a lot less than before with not many issues being experienced now and, for those that are, they are of less severity. So that is now maintained without the need for a paper-based system. And data issues have virtually disappeared.
HOW DID WE GET THERE?
One thing that worked for us at USA Jet was that we created a separate AMOS Manual, allowing us to revise the AMOS manual without having to revise the GMM (General Maintenance Manual) which gave us a separate place to list all of the business processes and systems. We also formed a dedicated AMOS team with sole responsibility for the quality of the AMOS implementation. Prior to that we had been trying to put the burden of responsibility on the departments and the department heads to produce the work that was required but that just wasn’t working for an organization of that size. We focused on the core processes: sometimes the project team had been getting into the weeds with trying to implement more than they could handle so the decision was taken to focus on just the core processes that were needed for the implementation. We broke out the things that were wanted later into phase two and phase three of the project.
We also made sure to involve all the departments to increase communication, and we started holding workshops and sessions, where everybody came together, to break down some of those silos and get everyone working as a team. Another significant component was that everyone was held accountable: if someone was assigned work and they were responsible for completing it then they were held accountable for doing that… everything was done collectively. Furthermore, each change was documented along with the results emanating from that change. Often with these projects in AMOS, there is a large volume of changes in settings and things that can be done: it’s very important that these changes are documented in as much detail as possible and that the results are regularly reviewed to ensure that there are not more issues being generated by the change.
FUTURE PLANS
AMOS was upgraded to the latest release on March 23 2020: now we’re planning a mobile device solution for inventory management using mobile devices that will aid in the barcode scanning of the bins and the material products in the store which will reduce the amount of time when people have to go to a computer workstation to use a keyboard and mouse to check inventory in and out. A further plan is to have full digital record keeping in less than two years and the implementation of AMOS Mobile in the same period. Looking further out, we’re considering an electronic TechLog, having identified that would be beneficial, and then another thing is we’re looking at our Heavy Maintenance Vendors and starting a conversation with them about establishing AMOS Data Exchange instead of exchanging heavy files of papers – usually done by email with PDFs that then get printed out. Finally, we’re considering Customer Reliability Reporting using the AMOS Report Designer software.
HOW AMOS WORKS FOR USA JET
In figure 1 we have what we in USA Jet have called our Paperless Pie.
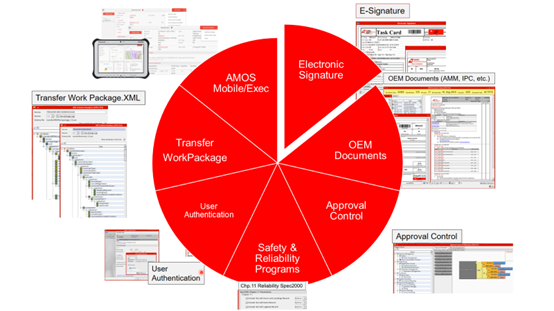
This paperless pie encompassed all the areas that we had to bring together, with e-Signature being one of them, to ensure that there was a paperless solution.
There were also some regulatory considerations that we had to look at (figure 2).
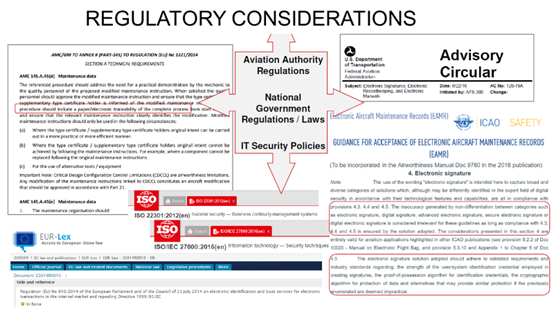
The figure shows regulatory issues such as the Advisory Circular that covers electronic signature. There are some ISO references that also talk about security of data.
For readers who are interested in the technical side, there is some information in figure 3.
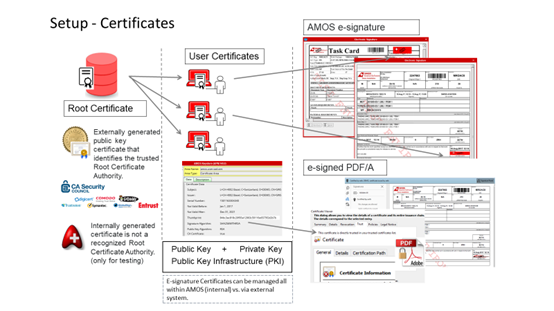
It uses a Root Certificate with a public key and a private key set-up to ensure security.
Customizations that worked for USA Jet
What really helped us getting our Ops tech and in getting the approval was that AMOS allows users, in the Wizards that they use, to customize the fields that will trigger the e-Signature set-up (figure 4) …
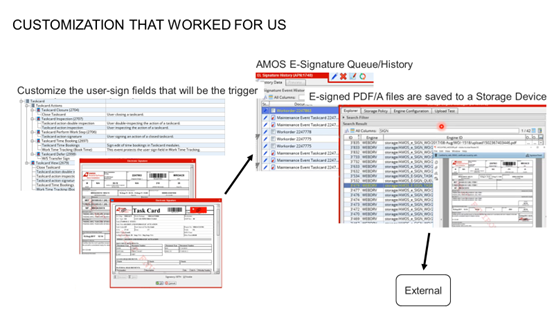
… and will prompt users to start entering their information to e-sign whatever task they’re doing. The figure includes some paperless aircraft operations information from IATA (figure 5.1).
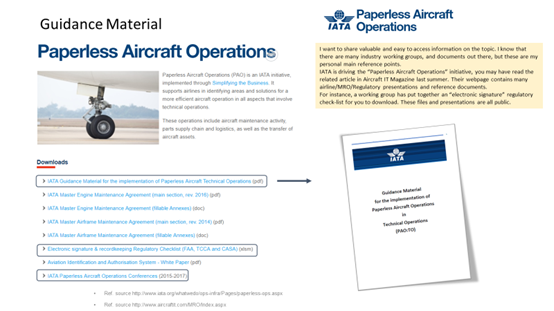
There is a lot of information out there but IATA seems to have made the most advances in this field: they have a lot of guidance material including one looking at paperless; so, they’re well worth checking for those readers who are embarking on this paperless course. There is a ‘Guidance Material for the implementation of Paperless Aircraft Technical Operations’ maintained by IATA and other guidance (figs 5.2 to 5.5).
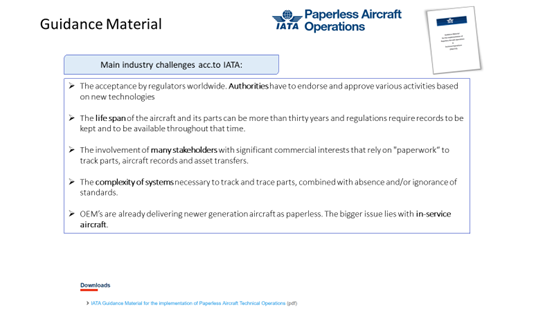
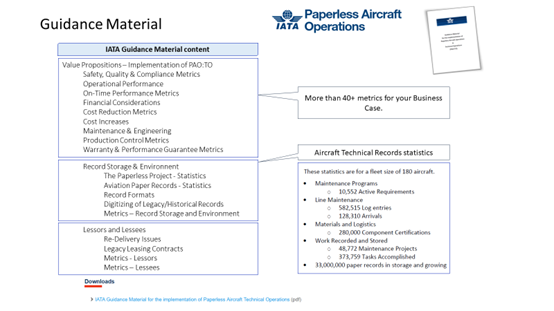
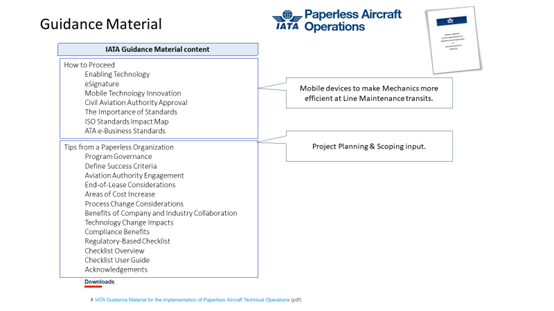
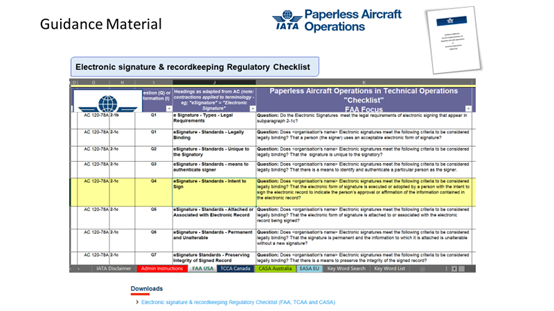
IMPLEMENTATION STEPS
We used a combination of on-site support and virtual classroom training (figure 6) to accomplish this implementation.
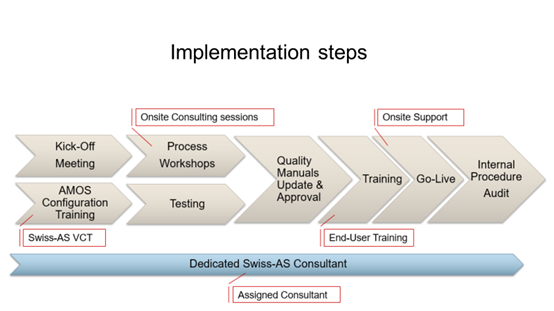
We also used a dedicated Swiss-AS consultant for the duration of the implementation.
SOME USEFUL TAKE-OUTS
As a result of our experience, we’ve come away with a few useful tips for implementation (figure 7).
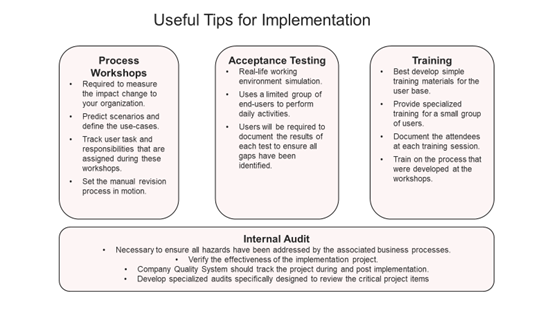
Process Workshops are needed to measure the impact of change on your organization, and that is where you’re going to identify all the gaps during the implementation. You’ll also do well to predict the scenarios and define the use-cases for it as well as track the user tasks and the responsibilities that are assigned during these workshops – remember we mentioned above that we held people accountable for the tasks they had taken on.
Finally, you’ll need to set the manual revision process in motion. For Acceptance testing, it’s really important that users document what they are testing and the results of those tests so that the quality team can review them. During training it’s best to keep the training materials simple and focus on the core processes. And, again for accountability, it’s a good idea to document all attendees who are training at the training sessions in order to keep everyone honest.
One very important piece would be the Internal Audit which is necessary to ensure that all the hazards have been addressed by the associated business processes. That will verify the effectiveness of the project. It’s a good idea for the quality team to develop specialized audits for this project so that they can close any gaps with the principal regulator, in this case, the FAA.
Contributor’s Details
Pete Sasson
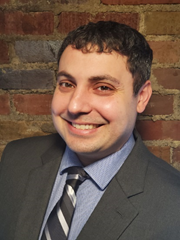
Pete Sasson is the founder of AirMost, LLC, a professional services company dedicated to helping clients optimize their business systems, while increasing efficiency and decreasing risk, by the implementation and management of Information Technology Systems. He has extensive experience in both military and commercial maintenance organizations where he’s focused on process vulnerabilities and risk management. Pete has dedicated his professional life to solving unsolvable problems, by taking a measured approach to ensure the right solution is applied the first time.
USA Jet
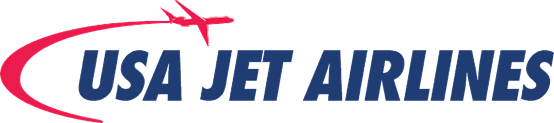
Since the 1980s, USA Jet been helping businesses fly mission-critical freight across North America. USA Jet is an FAA certified airline, has received the Platinum rating by ARGUS International for eight straight years and is proud to operate more than 36 percent of the available heavy-lift cargo aircraft in the industry. USA Jet Operates a fleet of B-727, MD-83, DC9-15, DC9-30 and Dassault DA-20 aircraft under a 121 Supplemental Air Carrier Certificate providing on-demand cargo charter service throughout North America, the Caribbean, Central and South America.
Swiss Aviation Software
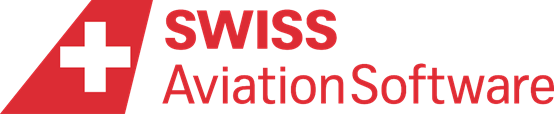
Swiss AviationSoftware’s AMOS is a comprehensive, fully-integrated software package that successfully manages the maintenance, engineering and logistics requirements of modern airlines and MRO providers. Tightly linked to an airline business, Swiss AviationSoftware is able to capture MRO trends at an early stage. With over 30 years of IT experience, Swiss AviationSoftware offers a functionally unsurpassed and technologically state-of-the-art maintenance system, used by over 190 customers worldwide, making AMOS one of the industry-leading MRO software solutions.
Comments (0)
There are currently no comments about this article.
To post a comment, please login or subscribe.