Articles
Name | Author | |
---|---|---|
The Power of Personalized & Targeted Distribution for WestJet Engineers | James Homeniuk, manager of Technical Standards and Audit Compliance with Lyndsay Steffler, Analyst, Technical Standards and Audit; both at WestJet | View article |
Improving the operational and financial performance of KAEMS MRO through digital transformation | Mr. Park Won, VP & Head of Operations at Korean Aircraft Engineering Maintenance Services (KAEMS) | View article |
Making the change to paperless at USA Jet | Pete Sasson, Project Manager, USA Jet / Active Aero | View article |
IATA Industry Restart Plan | Iryna Khomenko, Manager, Operational Efficiency, IATA TechOps | View article |
Managing digital assets with digital systems | Allan Bachan, VP, Managing Director, MRO Operations, ICF | View article |
IATA Industry Restart Plan
Author: Iryna Khomenko, Manager, Operational Efficiency, IATA TechOps
SubscribeIryna Khomenko, Manager, Operational Efficiency, IATA TechOps shares some ideas on maintaining parked aircraft and preparing them for a return to service.
Having endured many months of enforced inactivity or reduced activity, the aviation sector needs now to be looking to the future. So, in this article, I want to share with readers an industry restart plan that has been developed in IATA for the TechOps area.
ABOUT IATA
For readers who might not be familiar with what IATA does, I suggest that you go to YouTube and find the IATA TV page and the two-minute video that describes the IATA Mission, also describing how many airlines are members today and IATA’s motto, ‘To represent, to lead and serve the aviation industry’.
Governance Structure
With understanding of the governance structure (figure 1), it would be easier to understand the actions that IATA has undertaken to help the airline industry recover from the effects of the COVID pandemic.
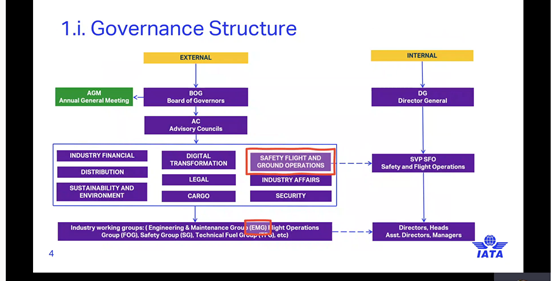
So, let’s start with a few words about the IATA Governance structure and where my colleagues and I sit within that structure. The structure on the slide is schematic; it is not an official org chart. As you’ll see, there are external and internal verticals on the schematic. That means that some industry related and some internal IATA actions and decisions are closely coordinated with the external groups, which consist mainly of airline representatives together with representatives from original equipment manufacturers (OEMs), some standard setting organizations, regulators and IATA’s strategic partners. Marked out in red is the Advisory Council that refers to my department and division and the Engineering and Maintenance Group (EMG) that is the holder of all documents and actions in the TechOps area.
CURRENT ECONOMIC SITUATION IN THE AIRLINE INDUSTRY
Before moving on to our activities within the TechOps and the aircraft maintenance area, I’d like to briefly discuss the overall economic situation of the industry. (figure 2.1).
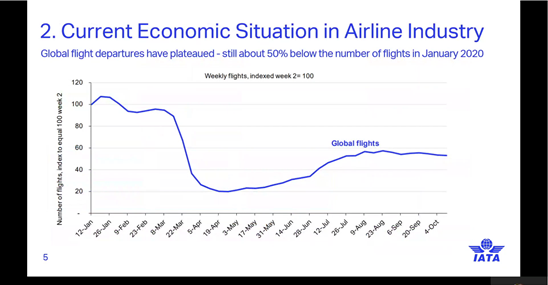
These figures are courtesy of IATA’s chief economist’s office showing the current situation. Figure 2, shows the total number of flights from the beginning of the year until the beginning of October and clearly shows the steep decline in activity related to the pandemic in the second half of March followed by a slow and difficult recovery through the summer which, as readers will know, has been mainly attributable to the pick-up in domestic markets. As domestic markets have become saturated but international markets have not yet opened there is a plateau in July-September and a slight decline in the line to October. We can also note that, historically, activity in winter is somewhat slower than in the summer period.
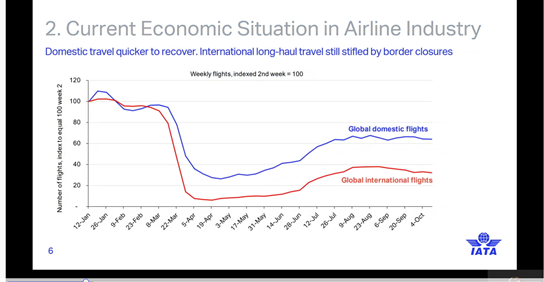
Figure 2.2 shows that at the time of writing, the international market still remained largely closed owing to quarantines and border closures, so the overall number of flights is significantly lower.
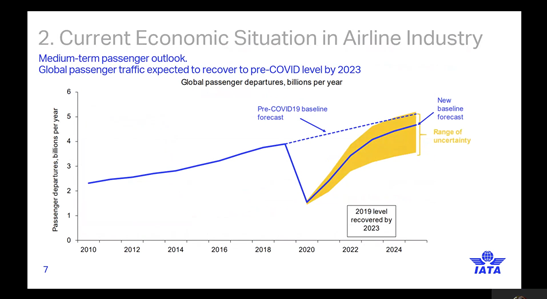
The graph of figure 2.3 represents the forecast trend of passenger traffic for the next three years. IATA’s economists believe that traffic will not recover to its pre-COVID baseline and trends until 2024 and even with that there is a wide range of uncertainty which will include factors like the progress of vaccines and vaccinations (there had been some positive news on this front at the time of writing), the existence of governmental restrictions and other factors.
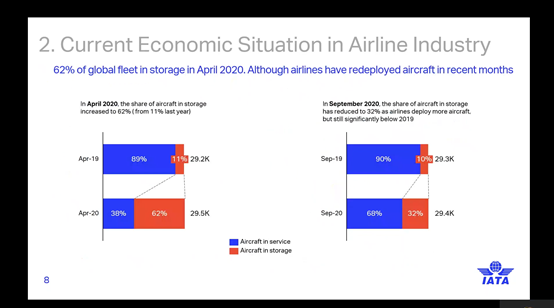
In figure 2.4, we have compared the number of parked aircraft at two points in a year, April 2019 vs April 2020, and September 2019 vs September 2020. This shows that the number of parked aircraft increased by April 2020 but that by September 2020 there was some improvement. However, we should also keep in mind that the number of active aircraft is never 100 percent, there is always a base line of approximately 10 percent of aircraft that are parked for various operational or maintenance/technical or business reasons, so we should discount the percentage of currently parked aircraft by the percentage of aircraft that would normally be parked anyway.
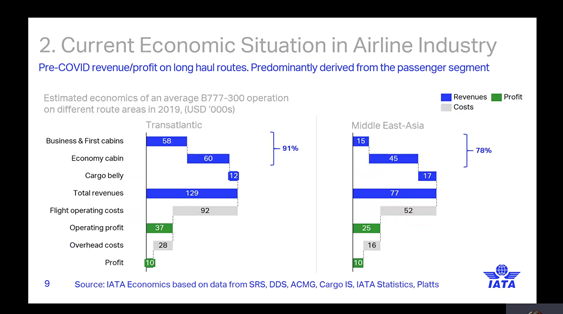
In figure 2.5, we can also see the approximate structure of revenue from a flight in pre-COVID times and that shows that passenger revenue equates to 90 percent for the Transatlantic region and nearly 80 percent in the Middle East/Asia region. It also shows the moderate profit levels generated in both regions, which is about 10 percent and it shows that cargo belly revenues contribute respectively 12 percent and 17 percent to the revenue.
Holding those numbers in mind as we look at figure 2.6 to see the current situation post-COVID…
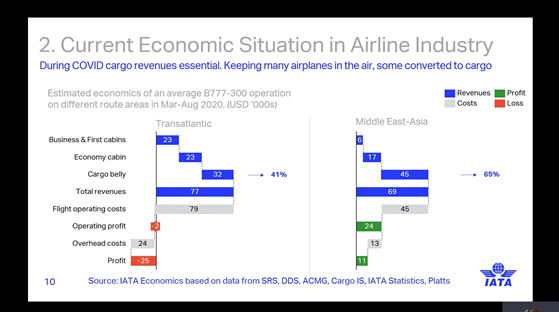
… right away, it can be seen that cargo belly revenues have increased to respectively 32 percent (Transatlantic) and 45 percent (Middle East/Asia) in the structure of flight revenue. Also, it can be seen that the total loss on a flight in the Transatlantic region averages to -25 percent while in the Middle East/Asia region flights are still profitable mostly due to that increased cargo belly revenue. Also, in the Asian region, domestic markets are almost restored to pre-pandemic levels which also improves the situation and generates 11 percent profit on the average flight.
IATA AT THE FOREFRONT OF ADVOCACY FOR A SAFE RESTART
Now, let’s take a look at the measures and activities that IATA has undertaken and supported since the beginning of the pandemic. IATA has been staunchly advocating for the safe restart of the industry and for relief measures to support the industry during the crisis. In support of this, IATA has been working with our member airlines, ICAO, with WHO, and with the many stakeholder organizations to, raise awareness of the difficulties that operators are facing today, and to support operators in accessing the necessary help and support (figure 3).
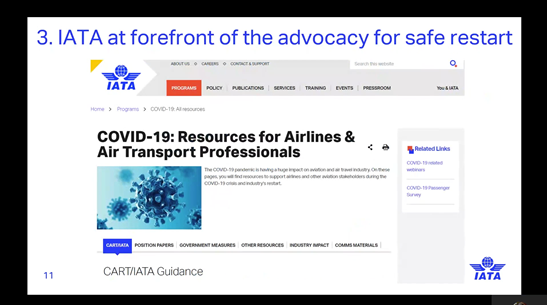
At the bottom of the figure, you can see a number of tabs. First, the CART/IATA Guidance shows the activity that has been carried out jointly with ICAO which came forward with the Council Aviation Recovery Taskforce (CART). IATA has been a regular participant in CART meetings, working with our member airlines to share industry expertise and know-how. Our website contains a lot of information to support our members and other stakeholders during this crisis and help prepare for the restart.
INDUSTRY RESTART PLAN
At the beginning of the pandemic, many of our activities were placed on hold, and the Board of Governors established new emergency priorities. These new emergency priorities became the basis for creation of the Industry Restart Plan.
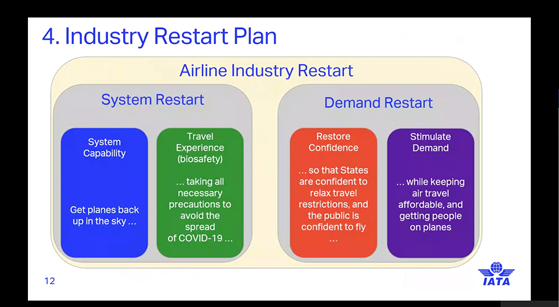
As readers will see in figure 4, the Industry Restart Plan comprises four parts over two areas: each part will be dedicated to a specific airline industry area; the technical operations are situated in the System Capability section. There are also activities underway on Stimulating Demand, working with passengers and working with bio-safety in Travel Experience and working to Restore Confidence, convincing states that there is a safe and efficient way of travelling without completely closing borders.
System capability
In the Restart Plan, let’s drill down in detail to System Capability in the System Restart bucket (figure 5).
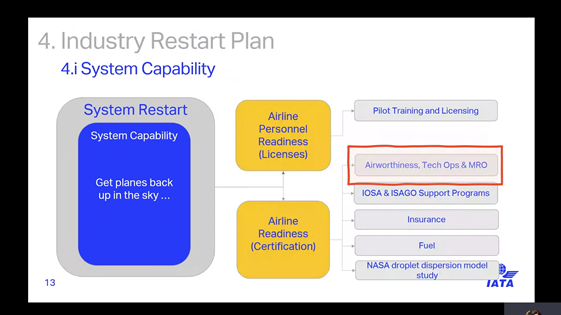
The System Capability bucket includes a few areas supporting return to service, particularly, we look into ‘Airline Personnel Readiness’ with all the issues related to the renewal and extension of the licenses needed for the personnel, facilitating the necessary training in the circumstances of the borders closure. We also are looking into airline readiness, including getting all necessary certification and beyond to have aircraft ready to fly. As you’ll see on the right side of the slide ‘Airworthiness and Tech Ops, and MRO’, is the part of Airline Readiness.
I’d like to say a couple of words about airline personnel, specifically technical personnel and aircraft maintenance personnel who would be in the ‘Airline Personnel Readiness (Licenses) rectangle. At IATA, we have looked into the issues with licenses with regard to aircraft maintenance personnel: these covered a few issues including whether there are any difficulties with obtaining the licenses, renewing the licenses, or whether there are any shortages of personnel to do the work during the pandemic. Also, we have investigated whether there are any problems with the access of personnel to the remote locations where the aircraft are parked. After some exchanges with the operators and some surveys, we have realized that, in fact, the industry is coping quite well and no specific measures are needed at this moment on the global scale to help with the licenses renewals. For that reason, the work in that area has focused mainly on pilot training and licensing.
System capability – TechOps issues
So, then, if we look to Airline Readiness Certification and specifically in the area of Airworthiness and TechOps (figure 6) we observe a few issues in that area.
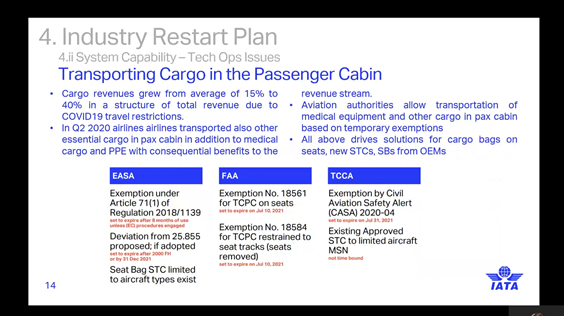
I’d like to start with the question or topic that naturally flows out of the earlier figures 2.5 and 2.6, about changes in the revenue structure of a flight where we saw that revenues from cargo have significantly increased. In addition to the belly cargo profits, airlines have also realized that the passenger cabin can be and should be utilized for transportation of personal protective equipment (PPE) that was essential in the early days of the pandemic and also to generate some revenues to support the airline while passenger traffic is low.
This is how the issue of transportation of cargo in the passenger cabin came up. Readers will be aware that aviation authorities permit the transportation of medical equipment in the passenger cabin but that permission is based on exemptions given by the various authorities. In figure 6, you’ll see some of the references for these exemptions. However, the exemptions are soon due to expire which would not solve the problem for airlines utilizing the passenger cabin to generate much needed cargo revenue. As a result, IATA sought to identify some not especially new but not widely used solutions. These included cargo bags on passenger seats, also some new STCs (Supplemental Type Certificates) were developed plus the OEMs have developed some SBs (Service Bulletins) to serve this end.
The other issue that has become apparent and very important for the continuation of operations is the bio-safety of personnel on board, including crew, maintenance personnel and the disinfecting of surfaces and equipment on board.
These requirements have also been driven by the authorities (EASA, FAA, etc.) with an increase in the amount and complexity of those requirement, and OEMs, of course, were at the forefront of development and approval of the disinfecting methods employed. Some of the available options for disinfecting before the current situation, include chemical disinfectants, electrostatic sprayers, use of HEPA (High Efficiency Particulate Air) filtering into the cabin airflow systems (which is the case for almost all aircraft today), UV (Ultra-Violet) technology and antimicrobial coatings.
But, of course, some other solutions have also been considered and could be further developed such as thermal disinfection, ionization or a UV capability that can be built into aircraft.
With these requirements, the OEMs have intensified their efforts on this subject and have focused their communication with operators through topic dedicated AOTs (All Operator Telexes) and MOMs (Multi Operators Messages) plus raising the awareness of operators about new methods of disinfection and their approvals.
We also know that, with extended aircraft parking, maintenance programs have also been significantly shifted or changed. So, at the beginning of the pandemic, we knew that close to 70 percent of aircraft were parked. We also know that the OEMs have started to develop new programs as against the usual programs that already exist in the AMMs (Aircraft Maintenance Manuals) due to the uncertainty that the pandemic has brought about plus due to the uncertainty as to when and how the aircraft will next be needed for operations (figure 7).
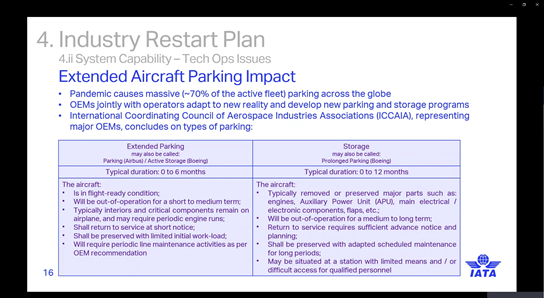
There has been a lot of work in the ICCAIA (International Coordinating Council of Aerospace Industries Associations), of which IATA is a part, and, as a result, definitions of extended parking and storage have been developed. IATA was, at the time of writing, conducting a data collection project on parked and stored aircraft: the definitions in figure 7 are given in the data collection and are taken as a base in that data collection.
So, how, exactly, has extended parking impacted on operations. As we’ve already considered, normal aircraft maintenance was replaced by the preservation procedures taken from the OEMs – Chapter 10 of (aircraft type) Aircraft Maintenance Manual – plus, of course, there are a set of new recommendations that have been developed by the OEMs. These new parking and storage programs have the objective to preserve the airworthiness of an aircraft while keeping it ready for operation at any given time. Then, of course, OEMs and operators work together to look into existing maintenance programs to reduce the maintenance burden of MPD (Maintenance Planning Document) and OMP (Operator Maintenance Program) tasks – on a parked aircraft and revise calendar or time-based maintenance tasks. The aim is to see if some can simply be postponed, or another term that has been familiar in various groups is so-called ‘clock stoppage’. In fact, the OEMs have been able to revise maintenance programs and to push many tasks intervals from, say, seven to 14 days, 30 to 90 days or 90 to 180 days.
One good example of this work is that Airbus’s requirement to perform a non-revenue flight after 90 days of parking has been moved to 180 days and, for some types (still to be confirmed at the time of writing) to as much as 360 days, 12 months of parking. All OEMs are undertaking similar exercises and these sorts of measures alone have saved millions of dollars for the industry. We have also seen, from some surveys conducted by IATA, that operators are striving to keep their fleets operational and not rushing to preserve their aircraft in prolonged storage. That would require many laborious tasks such as removing the carpets, the Oxygen bottles, batteries and other components plus moving the aircraft to a remote location from which it can often be difficult to retrieve it. So, contrary to the fact that almost 70 percent of the global fleet was parked at the beginning of the pandemic, the operators have remained conservative and did not want to send those aircraft into storage.
In figure 8, I’ve set out some basic information about the impact of extended aircraft parking and some mitigation actions to address those impacts. I’m sure that engineers reading this could add a few more but the table includes some issues that have manifested themselves during the pandemic.
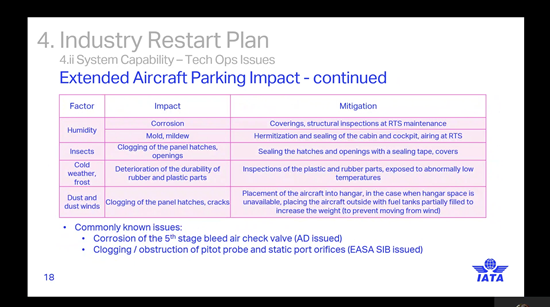
Corrosion is an issue, especially for operators who are based in warm humid environments plus, as winter comes on, in a wider range of places. There have also been issues with pitot probes and static port orifices where the tubes have become clogged with insects and debris and will then need a thorough clean before the aircraft is returned to service.
IATA Guidance Material
So, to summarize, I’d like to draw your attention to the many documents put forward in the TechOps area to help airlines in coping with this current situation and specifically for major documents that are publicly available on the website. These documents cover a range of topics.
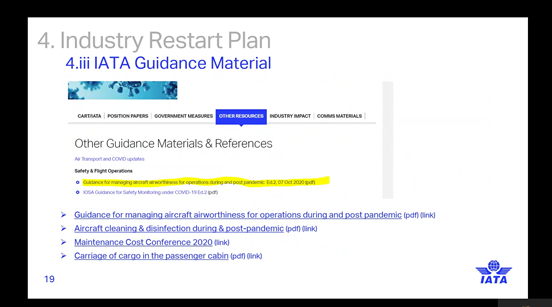
There is ‘Guidance for managing aircraft airworthiness for operations during and post pandemic.’ ‘Aircraft cleaning and disinfection during and post pandemic.’ which has been drafted in collaboration with OEMs and operators and covers procedures and new methods. Also, IATA has given a series of virtual webinars during the pandemic, including ‘Maintenance Cost Conference 2020’. There is also guidance on the increasing topical subject of ‘Carriage of cargo in the passenger cabin’ as mentioned earlier in the article.
I hope this has both reassured and informed readers about the specific issues that the COVID pandemic has brought to the airline business. Also, some of the initiatives in which IATA is engaged to ensure that airlines know what to do when the time comes to bring all of those parked aircraft back into full revenue generating service.
Contributor’s Details
Iryna Khomenko
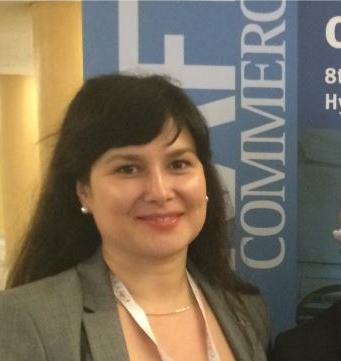
Iryna Khomenko is a Manager of Operational Efficiency in IATA with 14 years’ experience in Aircraft Operations including, for the last six years, being responsible for development and progress for several projects within the Digital Aircraft Operations Initiative. Before joining IATA Iryna worked at Aerosvit Airlines in Ukraine for 6 years, having started her career in Ukrainian – Mediterranean Airlines after she had obtained her master’s degree in Management and Economics.
The International Air Transport Association – IATA
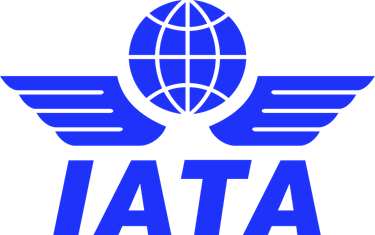
The International Air Transport Association (IATA) is the trade association for the world’s airlines, representing some 290 airlines or 82% of total air traffic. IATA supports many areas of aviation activity and helps to formulate industry policy on critical aviation issues. Over more than 70 years, IATA has developed global commercial standards upon which the air transport industry is built. The aim is to assist airlines by simplifying processes and increasing passenger convenience while reducing costs and improving efficiency.
Comments (0)
There are currently no comments about this article.
To post a comment, please login or subscribe.