Articles
Name | Author | |
---|---|---|
Future-proofing the Supply Chain | Saravanan Rajarajan S, Associate Director – Aviation Practice, Ramco Systems | View article |
new way of looking at and managing pre-maintenance data Part 1 | Steve Sayers, Director of Technical Publications, FLYdocs | View article |
Paper to Data – Data to Dollars Part 1 | Rob Saunders, Managing Director, Air2MRO | View article |
Case Study: Counting beans and tightening bolts | Kevin Chi-Ming Chen, Senior Vice President, Evergreen Aviation Technologies Corporation (EGAT) | View article |
Case Study: Fleet Technical Management and CAMO | Darmilo Sosa, CEO, Wingbox Aviation | View article |
Future-proofing the Supply Chain
Author: Saravanan Rajarajan S, Associate Director – Aviation Practice, Ramco Systems
SubscribeFuture-proofing the Supply Chain
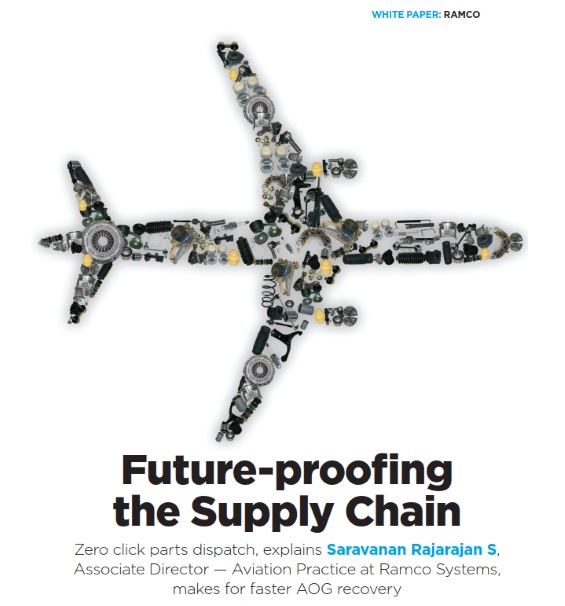
Zero click parts dispatch, explains Saravanan Rajarajan S, Associate Director – Aviation Practice at Ramco Systems, makes for faster AOG recovery
AOG (Aircraft on Ground) events are straight forward; one cannot plan for them but they happen due to technical faults or non-availability of material. However, proactively planning the possible response to these situations can help save valuable time. An AOG can potentially trigger cascading events such as sourcing, matching parts demand, logistics, payments and even reverse logistics of a unserviceable parts. But one thing is true for all of those events; time is of the essence across critical phases of accessing the supply chain.
THE CHALLENGES AND COMPLEXITIES IN AOG RECOVERY
The AOG desk races against time to get the right part to the aircraft on time but the part search process is challenging due to two key factors: the part’s applicability to the grounded aircraft and sourcing the part in a complex SCM (Supply Chain Management) context involving the OEM, distributors, the market place, and shipping carriers.
Figure 1 illustrates a case where the AOG desk, in order to meet their technical requirements, need to visit multiple OEMs, distributors and market place systems to check the availability of stock. Many of the transactions are email or phone based. Furthermore, AOG desks spend considerable amounts of time with the MCC (Maintenance Control Center) or Maintenance crew to re-confirm alternate parts, Mod Deviations, etc., if the requested Part# is not available. Even a slight error in the entire process may lead to delayed recovery or even with the wrong part fitted to an aircraft.
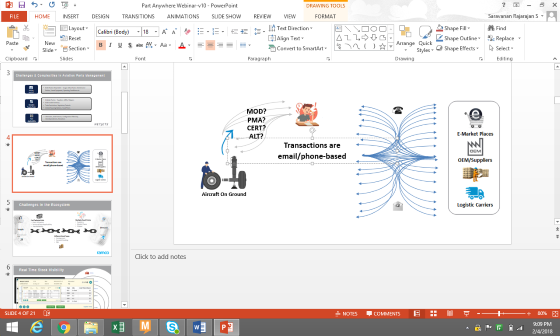
Figure 1 – Recovery through Manual Process
Part applicability: even though it looks trivial, thousands of dollars have been lost just because the wrong part ended up in a grounded Aircraft’s location. When a demand is placed for Part#, it implies that all the other requirements, as listed in figure 2, should be met while sourcing. These additional factors, adding up to the part, increase the interactions to check and confirm internally before the order is placed. This contributes significantly to the lead time and is also prone to errors.
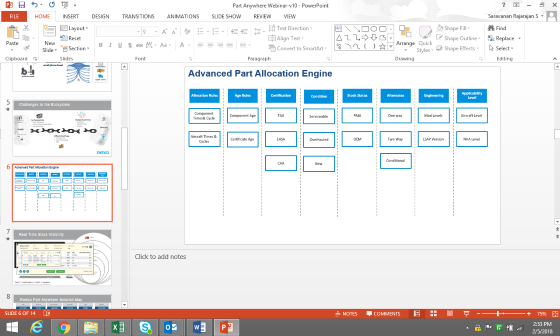
Figure 2- Part Applicability Requirements
Complex supply chain: sourcing parts during an AOG is a very complex and time consuming process since it involves multiple parties like the OEM, distributor, market place vendors across the value chain. Supervisors at the AOG desks typically scour for parts using multiple portals to find the availability especially with the OEM and distributors. With part applicability requirements it also means that the search has to be very detailed and comprehensive, since it’s not just about availability. Sometimes it may necessitate calling up the supplier or OEM to verify the technical requirements like certifications and other paper work.
CONNECTED SUPPLY CHAIN ECO SYSTEM FOR FASTER AOG RECOVERY
The latest B2B connectors and state-of-the-art API (Application Programming Interface) based architecture helps in these independent systems, wherein the interrelated systems within and across the organizations can be integrated and the relevant information can be processed and shared in real time, making it a truly connected Ecosystem. This will ensure that the right parts reach the right location at the right time
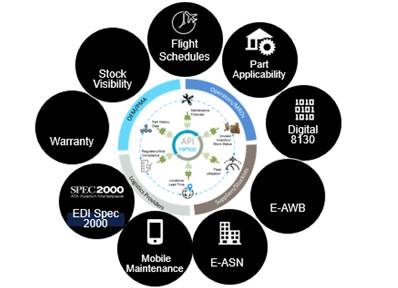
Figure 3 – Connected Eco System for AOG recovery
BENEFITS OF CONNECTED ECO SYSTEM
Automated allocation processing
When the stock is available to meet the AOG demand, picking up the right serial number will reduce the time for part movement with conventional strategies like FIFO, LIFO and Remaining Life. The M&E system should be configurable to automate picking the right serial# in compliance with part applicability requirements.
Auto suggest internal sourcing options
An M&E system is expected to provide the real-time demand processing capabilities from demand placement till POD (proof of delivery) acceptance of the part, which can be done by enabling technologies like mobility and Chat Bots. This significantly reduces the error in relaying the message through voice or through other paper based processes. An intelligent M&E system is expected to provide the possible sourcing options like swapping from any other grounded aircraft or aircraft currently under base maintenance, and the possibility of expediting the inspection and certification if the Item is WIP (work in process) at the receiving bay or shop. This sourcing option should consider the multiple part applicability requirements driven by the aircraft, customer contacts and regulatory requirements.
Real time stock availability
One of the significant added values of this connected eco system is getting real-time stock visibility from the all the entities like the OEM, the distributor and the market place. The AOG desk can process the part number and send the demand data with applicability requirements to multiple suppliers in the eco system. Through API calls, the availability positions of the stock at given locations and meeting the applicability requirements are received on a real time basis at the AOG desk for processing. Furthermore, the AOG desk may decide to process an RFQ (request for quote) or PO (purchase order) based on the circumstances and, on processing, the transactions are processed through SPEC 2000 EDI Channels.
Zero Touch Ordering
The entire ordering process can be automated through a connected eco system , wherein, once a demand has been placed for the part, an auto search can be executed and the availability positions from the various suppliers are received through API calls. The right part is identified by filtering out with applicability requirements. Applying the rule configurator, the right supplier is identified and the order is auto approved and processed through EDI channels.
The rule configurator can be combination of key following key parameters with ranking to assist the auto picking of the supplier.
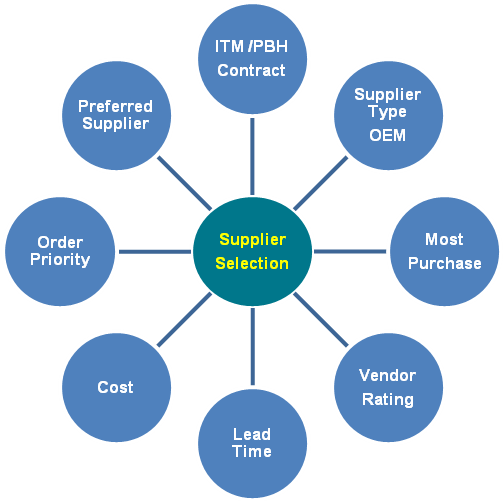
Figure 4 – Auto Supplier selection Factors
Predictive Dispatch
A connected eco system can enable organizations to set up the dispatch in anticipation of the confirmed part requirement. Artificial intelligence and Big Data technologies play vital role in this enablement.
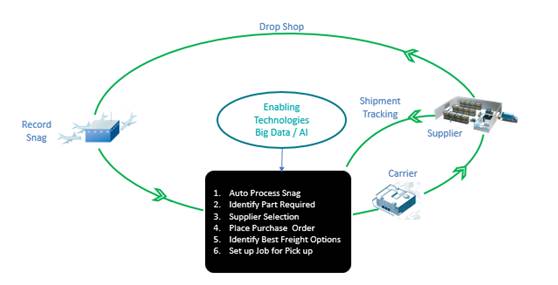
Figure 5 – Predictive Dispatch
With Next-Gen technology enablers like Big Data processing and Artificial Intelligence (AI), the efficiencies of the connected eco system can be enhanced further by predicting the parts demand and initiating the movement once a snag is recorded.
When the snag is reported by the mechanic, using Big Data and AI, the required part number can be ascertained with a high degree of accuracy. Once this is identified, the ordering process is automatically initiated. In addition, as the origin and destination is known, the data can be fed to multiple shipper or freight tracking systems and the best (lowest time with high delivery probability in consideration of HAZMAT / oversize factors) shipper is identified and job can be initiated for the shipper to pick the part from the supplier.
Real time information is shared across the various parties through E-ASN (e-Advanced Shipping Notice) and AWB (Air Waybill) tracking from Pick up till POD. Any deviations or delay in the processes can be altered for possible manual intervention.
While relationships between the AOG desk and supplier still matter, the most effective AOG desks leverage technology to provide them with assisted decision making capability to reduce the lead time needed for AOG recovery. In the future, MRO systems are expected to be able to take decisions on behalf of the AOG desk supervisors and that will only get better with machine learning to optimize performance. The need to supplement the decision assist capabilities in AOG recovery has never been more critical.
Contributor’s Details
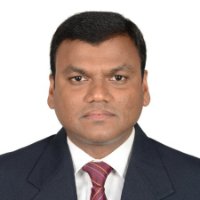
Saravanan Rajarajan S is an astute professional with over 15 years’ experience in the aviation domain. He heads the Center of Excellence for Ramco’s Aviation Practice and is a subject matter expert on the aviation supply chain, with diverse experience in implementing Ramco Aviation’s M&E MRO solution in more than 40 organizations. He has explored synergies with technologies like Mobility, Big data and BOTs to foster the aviation MRO Industry. He possesses a strong educational background with Degrees and Certifications in Mechanical Engineering (B.Tech), Business Administration (M.B.A), and also holds the APICS – CPIM Certification.
Ramco
Designed to be accessible on cloud and mobile, Ramco Aviation Software continues to add technological innovations with ‘Anywhere Apps’, redefining the power of Mobility, to significantly reduce transaction time both during AOG conditions and critical aircraft turnarounds. The software helps aviation companies ensure zero tolerance to error, with higher safety standards.
Comments (0)
There are currently no comments about this article.
To post a comment, please login or subscribe.