Articles
Name | Author | |
---|---|---|
Case Study: Fuel Management at Ukraine International Airlines | Andriy Kostyuk, Technical Pilot E-190, Ukraine International Airlines | View article |
Aviation and the Environment | Guido Harling, CEO ETSverification GmbH | View article |
Norwegian EFB: to buy or build? | Klaus Olsen, EFB Administrator, Norwegian | View article |
Case Study: Fuel Management at Ukraine International Airlines
Author: Andriy Kostyuk, Technical Pilot E-190, Ukraine International Airlines
SubscribeYou can better manage what you know
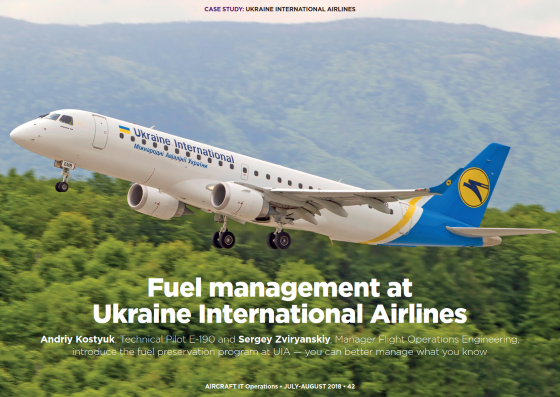
Ukraine International Airlines’ Andrei Kostyuk, Technical Pilot E-190 and Sergey Zviryanskiy, Manager Flight Operations Engineering, introduce the fuel preservation program at Ukraine International Airlines
As the aviation industry looks to the future, fuel efficiency and emission reduction play a dominant role in meeting the business challenges presented by global financial uncertainty. Ukraine International Airlines (UIA) has been flying for more than 25 years and, for the past ten of those years, has been applying and improving fuel saving procedures. The fleet includes Boeing types (737, 767 and 777) and Embraer 190; and, for the purposes of this article, we’ll focus on a fuel efficiency program as implemented with the Embraer fleet. But first, we’ll briefly look at those ten years of fuel saving initiatives.
HISTORY OF FUEL EFFICIENCY PROCESSES AT UIA
Our first step ten years ago was to analyze IATA manuals for some recommended good practices and to look at the manufacturers’ recommendations on the subject. We also looked at what other operators were doing for fuel management and, using the knowledge we had gained, created some fuel saving practices of our own. We supported it all with home-made programs to analyze the statistics from journey logs, tech logs, etc. The results that were generated might have been rough and uncertain ready but they were even those results were better than nothing and, in those early years, we learned a lot of useful lessons that have helped us leverage the best results from the fuel management solution we use now.
We learned that a successful Fuel Efficiency Program is only effective when all related staff (Maintenance, Flight Crews, Flight Operations Engineering, IT department and Management) work together and are fully aware that even small tasks and actions might have a significant impact on fuel savings. Indeed, fuel saving is the sum of small contributions that seem to be insignificant when considered in isolation, but are effective when integrated over the years.
Based on those first steps, we decided to implement fuel efficiency procedures in Operation Manuals OM-A and OM-B, as the main purpose is to modulate pilots behavior and manner of flight using fuel efficiency rules. At the same time, we also worked to optimize the OCC (Operations Control Center) and HUB center to choose alternative airports. We also created fuel efficiency operation manuals for each UIA fleet type at the time (B767; B737; E190), implemented fuel efficiency practices into SOP (Standard Operating Procedures) and started creating the fuel efficiency airport briefings.
Figure 1 illustrates some of the fuel efficiency practices that were reflected in the OM (Operating Manual) and SOPs (Standard Operating Procedures).
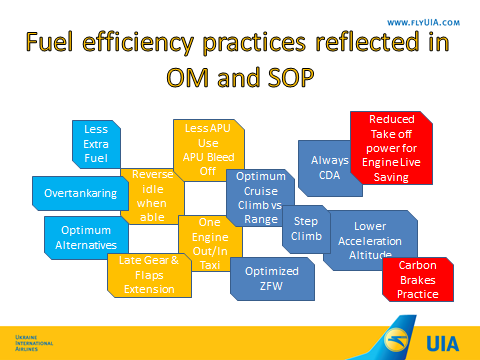
However, while we knew that we were saving fuel, we had little means to discover which of our new procedures was reaping the best returns or ways of testing new ideas to see what potential saving they might offer. In short, we knew savings had been made but didn’t know how much. Faced with the reality that we were unable to fully track, control and, therefore, manage the process of fuel efficiency, in 2014, we started to search for a fuel efficiency solution provider and, after a selection process based on the analysis of functional capabilities and their applicability in UIA, in 2015 a decision was made in favor of the Skybreathe system from OpenAirlines. Almost the first thing we did with the new system was used it to check our beliefs about the efficacy of our then current fuel efficiency programs (figure 2).
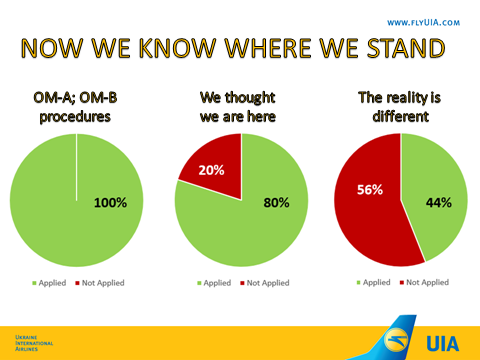
Taking all of the procedures we had introduced, we knew that 100% of them had been added into the Operating Manuals OM-A and OM-B and we thought that about 80% of the time they were being followed by our pilots. The first proper analysis carried out using SkyBreathe revealed a quite different picture; that the fuel efficiency procedures were only being applied about 44% of the time. We also learned for the first time what proportion of any savings we were making could be attributed to different initiatives (figure 3).
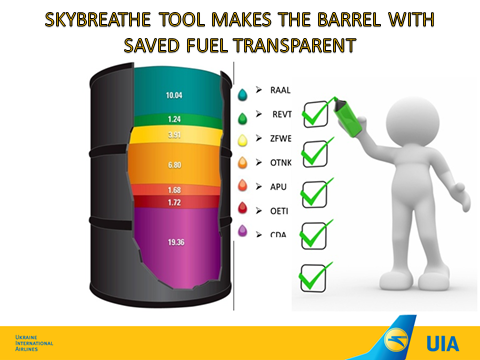
FUEL EFFICIENCY PROCESSES AT UIA TODAY
Today, many departments are involved in fuel efficiency using SkyBreathe to improve theair quality as part of their roles in the fuel efficiency programmprogram e system in Ukraine International. The airline is now able to work with Air Traffic Service providers, especially the terminal area design team and especially regarding UIA’s base airport. So, first of all, we’ll start from the ??????? Uksatse in Kiev with whom we are working to renegotiate the standard arrival procedure based on real flight statistics over a long period. The target is to reduce this procedure by 21 nautical miles.
A FUEL EFFICIENCY FLIGHT
But the best way to illustrate UIA’s fuel efficiency is to talk about one fleet and we’re going to use the example of Ukraine International Airlines’ small fleet of Embraer 190 aircraft through explaining a fuel efficiency demo flight.
Briefing
Every flight starts with a briefing, the most important part of fuel efficiency because it concerns how much fuel the pilot decides to carry. With the help of the Fuel CoachSkyBreathe’s MyFuelCoach™ EFB application who which is consulted by every EFB pilot the captain can analyze all the information he needs for a decision; so this application can help to understand how much fuel should be taken for the flight. It is not quite the correct decision to simply take more fuel. Usually, an increase of 50 NM on the distance will increase trip fuel used by 10kg, and the usual extra fuel taken by Embraer pilots is 22kg but360 kg , if it’s not taken correctly, we lose 22kg . increases trip fuel by 22kg per flight.
One usual practice is to compare GPU (Ground Power Unit) with APU (Auxiliary Power Unit). So, we created an airport briefing in which we considered the cost of using a GPU within handling packages; how long can a GPU be used for free time and what would be the extra charges beyond that free time. So the pilot/captain knows definitely where and how long he can use APU GPU and when to start using GPUAPU. In some places GPU is not available and so APU has to be run. But even running the APU, it is possible to save fuel, especially during the summer when the outside air temperature (OAT) is warmer.
Ukraine International has created fuel efficiency manuals for each type of aircraft in the fleet and figure 4 is an extract from the Embraer 190 Fuel efficiency manual.
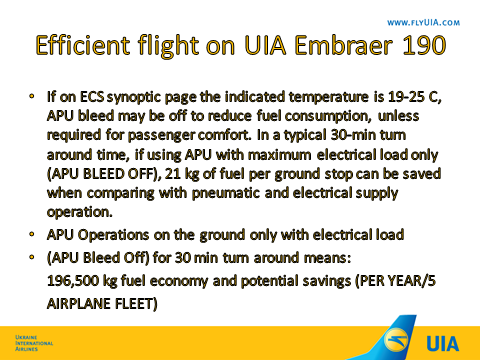
As soon as the temperature is between 19-250C, the cabin passenger compartment is comfortable and so the pilot is recommended to switch off the APU bleed; a very simple action but it was calculated, using the SkyBreathe system, that for a fleet of five aircraft just during warm days in the summer, this will deliver a saving of 196,500kg of fuel in the year.
Fuel management during taxi
An efficient taxi uses one engine only but it might not be that simple. UIA has kept a record of risk assessment for one engine taxi out. With the Embraer, it is necessary to increase power of the one engine at the start of the taxi, when taxiing uphill, on rough surfaces or on a curved taxi route. There is also more work for the flight deck during one-engine taxiing plus it’s necessary to take account of head down procedures and airport taxi hot spots.
Fuel management at take-off
After taxi, at take-off or rather preparing for take-off, there is an immediate decision to make. Maximum take-off power saves fuel while reduced take-off power saves engines. UIA has calculated that it is better to save engines and so the usual take-off mode is with reduced power. The way it works is that, considering fuel economic aspects, reduced take-off will burn slightly more fuel once less thrust is used. It means that lower rates of climb are provided until reaching the second segment so more time is spent at higher fuel flows. Another consideration at take-off is flaps selection. For the time being, UIA Embraer pilots use Flaps 1 for take-off whenever possible. But, during the initial training, pilots used to take-off with Flaps 2 and it took nearly six months to change pilots’ minds that it is better and safe to fly with Flaps 1. Now, almost everyone takes-off uses Flaps 1, saving 10kg to 20kg or more of fuel on each take-off, depending on field length, temperature and elevation.
Fuel management in flight
Our first consideration is the reduced acceleration altitude. For the Embraer 190, the reduced acceleration altitude is 400ft. when Noise Abatement Department procedure (NADP) are not required. Based on a calculation using SkyBreathe, UIA set all reduced acceleration altitudes from 1000ft. to 400ft. which small change alone saved between 10kg to 13kg per flight.
Some results
In figure 5 you’ll see some of the results for the UIA Embraer fleet from using less Flaps in take-off in the past year.
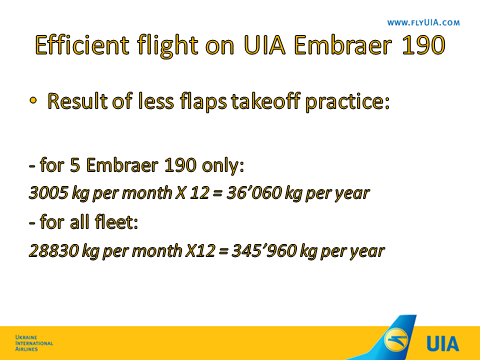
Just from the five Embraer 190s there was a fuel saving of 3,005kg per month which totaled up to 36,060kg per year. Looking at the results for the whole fleet, UIA reckons a monthly saving of 28,800kg of fuel which amounts to 345,960kg of fuel in a year simply from using less flaps at take-off.
The climb
Looking at short to medium range flights, the next stage of the flight, the climb phase can represent 20% to 40% of the trip time with fuel flow at 40% greater than in cruise. When we considered this and calculated the profits from the climb schedule, we reviewed the fuel from the take-off to the top of the descent. There is an option available; whether to use Climb 1 or Climb 2 is an operator’s decision whether to save on engine wear or to save fuel. For instance, with UIA’s Embraer 190s, using Climb 1 delivered fuel saving of between 0.5% and 1.5% (depending on total route distance) but, using more power reduces the engine time-on-wing by 5%. So, after some discussions with General Electric, the engine maker, UIA took the decision to use Climb 2, moving to the lowest safe power setting as soon as practicable.
In another case, UIA is looking to implement Continuous Climb Operation (CCO) next year. From all of this, UIA has developed a climb schedule (figure 6) that recommends specific climb parameters for varying distances of flight.
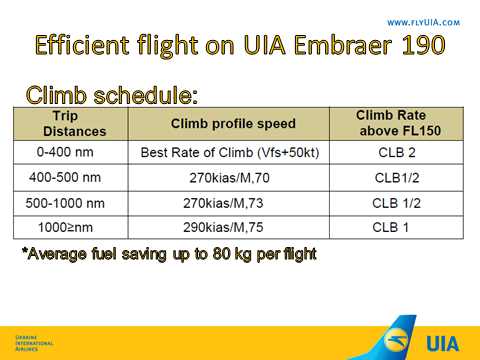
Most importantly, we calculated that using this schedule could save up to 80kg of fuel per flight from take-off until top of descent.
Cruise speed management
Looking at LRC (Long Range Cruise) UIA decided to manage for an optimum flight level using the FMS (Fuel Management System) option based on actual ambient conditions encountered. Using the system, it was made clear that the pilot setting the exact correct speed was a contributor to fuel consumption inasmuch as even if he set the speed just Mach 0.01 faster than planned, that would burn an additional 14kg of fuel per flight. Going to step climb, as reflected in the OFP (Operational Flight Plan), when the optimum flight level is not selected by flying, say, 2000ft below the optimum altitude, can increase the average fuel used by 37kg per flight.
Descent
UIA now calculates the most applicable method of descent taking into account the aircraft weight, the wind and other factors and uses continuous descent approach (CDA). Also, to minimize fuel consumption, idle thrust is recommended during descent because descent methods that require thrust application will increase fuel burn. Using the SkyBreathe solution, UIA has generated a number of clear results.
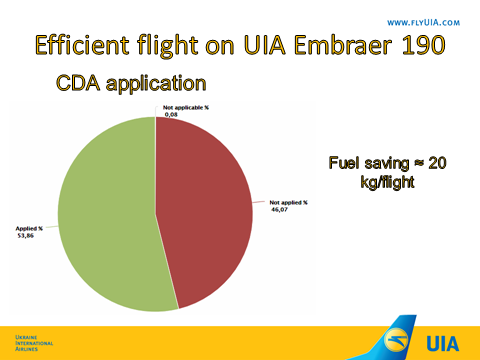
In figure 7 the red area is where fuel saving steps were not applied in CDA and the green area identifies where fuel saving steps were applied. In this element alone, the average saving managed on the Embraer fleet during continuous descent approaches is 20kg per flight.
Less flaps approach
Some pilots prefer to land with full flaps so we asked them why that was. Their response was they were simply more comfortable to land with full flaps. The airline suggested that, if the runway is not restricted, if there no requirement to make a full performance flaps landing, the pilots could try landing with flaps 5. They did so and we now know that using flaps 5 instead of flaps full saves per approach 10kg.
Landing gear and flaps extensions
An extract from the fuel efficiency manual says ‘you should keep a clean configuration for as long as possible’; if flaps are extended and the gear is lowered too early, fuel consumption will increase by 150%. UIA wants its pilots to be aware of that.
The approach
Looking at the approach, and assuming good weather, pilots are encouraged to make a visual approach. UIA has analyzed 7,000 approaches and they are typically IMC (Instrument Meteorological Conditions) approaches with an average fuel consumption of 150kg. However, when the pilots are cleared for a visual approach under Visual Meteorological Conditions (VMC), there is a fuel saving with an average fuel consumption of 122kg; a saving of 28kg for a visual approach. Across the whole group of 7,000 approaches analyzed, UIA was able to save 10,100kg using this method.
Reverse thrust
As the aircraft touches down, the captain has to decide whether or not to use reverse thrust. Of course, if the runway is limited, they’ll have to use it but if there is enough runway and it isn’t necessary to use full reverse thrust then UIA prefers pilots to use idle reverse thrust.

Figure 8 shows three possibilities. The gray sector, 14% of landings, is where idle reverse thrust would not be applicable such as in poor weather conditions (rain) or if the runway is contaminated or not long enough. But it also shows in the red sector that in 17% of landings, pilots did not use the idle reverse thrust method where it could have been applicable. Most pilots (69%), though, did apply the method as a result of which, the average fuel saving is 10.2kg.
Taxiing in
To save fuel, one engine taxiing in is recommended and that, we now know, saves an average of 11kg per flight. Figure 9 shows comparisons to illustrate the effect of using the MyFuelCoach™ EFB application.
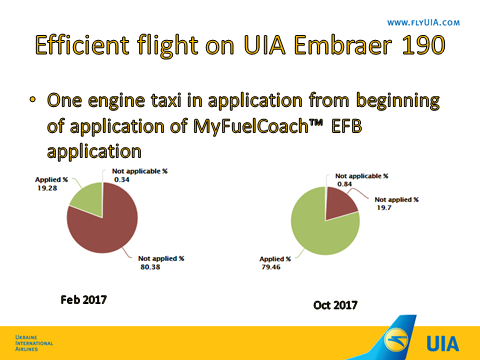
Before we were using MyFuelCoach, as can be seen, in February 2017, less than 20% of UIA pilots were using one engine taxi in whereas, using the application, by October 2017, that had risen to nearly 80%. Using the app, a pilot can analyze his own performance and this example shows the achievement that UIA’s pilots have achieved for the airline.
Another way in which fuel can be saved during taxi is with late APU start up. The common procedure here is land, flaps up, taxi start, APU. What we have done at UIA is implement a practice of taxi, lights off then start the APU which will be running by the time the main engine is switched off. This practice was about to be implemented at the time of writing and was expected to save up to 8kg of fuel per flight.
AFTER THE FLIGHT
As part of the debriefing, UIA generates an ‘ideal’ potential saving for a flight (figure 10)…
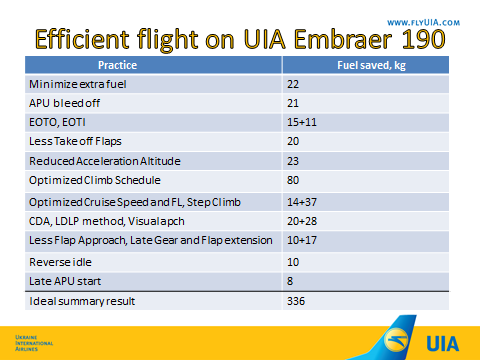
… that shows what fuel saving could have been achieved if all best practices were used; in this case, 336kg of fuel. Of course, this ‘ideal’ flight will never happen but these numbers highlight what could be achieved to maximize fuel efficiency.
If pilots follow best practice, they have the chance to be listed in theanonymous list of the airline’s Embraer squad s top 10 pilots for fuel saving achievement (figure 11).
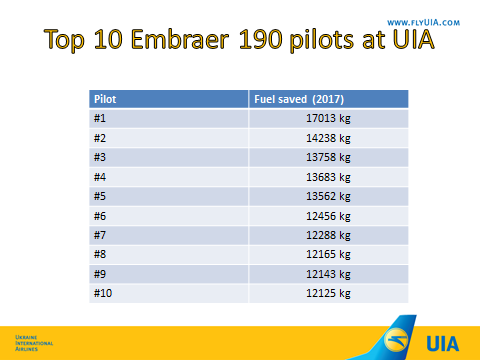
And, if you add it up, just those ten pilots saved nearly 132,000kg during 2017 simply by applying the new fuel saving practices when applicable to do so.
STAGES OF IMPLEMENTATION
UIA implemented its fuel efficiency initiative in stages (figure12).
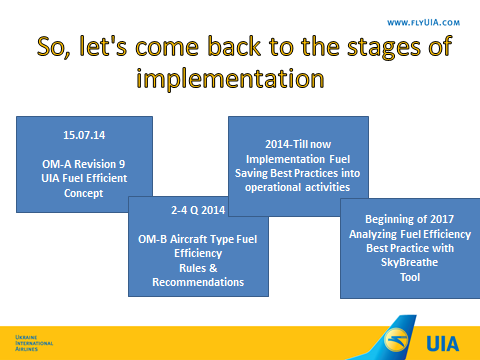
In 2014, the airline made revision 9 with Operation Manual A (OM-A) when the UIA Fuel Efficiency concept was designed. The next step was to design the fuel efficiency manual for each type of aircraft in the fleet, taking account of the characteristics of each type in Operations Manual B (OM-B). With that all in place, the airline began to implement fuel saving best practices into operational activities, increasing the number of new practices from time to time in the SOP (Standard Operating Procedures) and the aircraft fuel saving procedures. By 2017, we were using the SkyBreathe tool which means that we can now see how much has been saved.
Contributor’s Details
Andriy Kostyuk
Andriy has been in aviation since 1986 and, in 2002, retired from the Ukraine Air Force as a Major. From 2002 to 2008 he flew for the Antonov Design Bureau and from 2008 to 2012 flew for DniproAvia Airlines. In 2013 he joined Ukraine International Airline where he has been Involved in the e-Enablement Program, EFB Program, Fuel Efficiency and Preventive Maintenance Program. Andriy is a Captain, Technical Pilot on the Embraer E190 fleet.
Sergey Zviryanskiy
From 2004 to 2005, Sergey was Flight Manager in the cargo airline Applex LLC and from 2005 to 2006 Sales Regional Manager JSC ‘Monomakh’. From 2006 to 2007 he was Operations Manager at British Gulf International Airlines then joining Ukraine International Airlines as Fleet Assignment Officer. In 2011, he was appointed Operations Engineer of UIAS and, in 2012, Head of Navigation Department. From 2015 to the present, Sergey has been Manager Flight Operations Engineering and Fuel Efficiency – EFB Administrator.
Comments (0)
There are currently no comments about this article.
To post a comment, please login or subscribe.