Articles
Name | Author | |
---|---|---|
Columbia Helicopters Case Study: Paperless end-to-end aircraft maintenance | Israel Revivo, President & CEO, IDMR Solutions, and Paul Myrand, Project Manager, Columbia Helicopters | View article |
Meeting the new MRO order: Mobile MRO as part of the ERP | Espen Olsen, European Director Aerospace & Defense, IFS | View article |
CMS and MRO Systems Integration – Part 2 | Thanos Kaponeridis, CEO & President, AeroSoft Systems Inc. | View article |
Case Study: Safer, Faster, Better: China Airlines M&E IT upgrade case study | Houng Wang, Vice President, Engineering Division, China Airlines | View article |
Column: Autonomics and the Network of Everything (NoE) | Michael Wm. Denis, VP Customer Engagement, Flatirons Solutions | View article |
Columbia Helicopters Case Study: Paperless end-to-end aircraft maintenance
Author: Israel Revivo, President & CEO, IDMR Solutions, and Paul Myrand, Project Manager, Columbia Helicopters
SubscribePaperless end-to-end aircraft maintenance
Columbia Helicopters have implemented a totally paperless MRO/M&E process from maintenance management and scheduling to task cards and e-signatures
We’ll go through the lifecycle of the Task Cards from creating, to approving, to integration and finally to work execution with e-signatures, non-routines and routers. Also, we’ll look briefly at how the systems can work on conventional computers or on mobile devices. But first, it will be useful to explain a little bit about the three businesses involved.
IDMR Solutions
IDMR Solutions has been developing and implementing aviation software for the aviation industry since 1998, primarily dealing with M&E documents and Corporate Manuals. Task cards, being their first module, gives them over 15 years of experience and proven solutions in this arena. The document management system, InForm, was written from the ground up with the idea that users could author and maintain virtually any document in the system using a template based solution.
Templates are created in the system allowing users to write directly onto the electronic documents which resemble their paper origins. All necessary tools, such as; revision control, check in/out, workflows and much more are built into the platform and can be accessed via an easy-to-use interface. The web and mobile portal allows users with mobile devices to complete approvals and view documents along with manuals from the palm of their hands. InForm integrates with many M&E systems to create a single point of entry, avoiding the need for duel entries in multiple systems. As soon as an entry is made and approved, it automatically flows into the M&E system.
Columbia Helicopters
Columbia Helicopters, Inc. (CHI) was founded in 1957 and since then has become the world’s largest heavy lift operator and only commercial operator of both the Columbia 234 Chinook and Columbia 107-II. The business currently operates six Columbia Model 234 Chinooks and 14 Columbia Model 107-II helicopters. CHI holds the Type Certificates and Production Certificates for both the 107 and 234 type aircraft. This has created documentation challenges with the ERP (Enterprise Resource Planning) system, which is not usually manufacturer-based, but is a MRO-based system. In 2012 CHI achieved AS9100/9110C Certification and also has DoD (Department of Defense) Air Carrier Certification.
The firm operates worldwide in sectors such as petroleum exploration support, firefighting, construction, forestry and is a Part 91 and 135 operator. Operations areas have included Australia, New Zealand, Saudi Arabia, Sudan, Chile, Ecuador and Malaysia, as well as, currently, Papua New Guinea, Afghanistan, Peru, Canada, Alaska and the continental U.S. Where CHI has gone mainly paperless is in Technical Services, with a hangar and eight repair shops to support the CHI fleet and various external customers for overhaul and repair services. Customers include the U.S. Army (Special Forces and flight training divisions) and National Guard, various foreign militaries (including Australian Defense Forces) and commercial operators.
The Engine Shop can repair and/or overhaul AL-5512, T55-712 and T55-714 engines and accessories. There is also a complete overhaul shop that can deal with the CT58 and T-58 engines and accessories, and it can undertake repairs of components. Other engine services include full engine test cell capability, extensive fuel control and fuel accessory overhaul and repair capability, and dynamic balance operations.
CHI’s Structures Shop can undertake major and minor repairs, major and minor modifications with the use of fixtures, and repairs and fabrication of components using E-glass, Kevlar and carbon graphite materials.
With all this, it was a priority to standardize on the various forms that the company used, so moving to one standard with IDMR and task cards was a big challenge. Once that was done, CHI was able to admit the e-signature. The only printed document that accompanies a job today is the tally sheet. Everything else is uploaded into the Ramco Shop Work Order (SWO) packet and is accessible through the FTP site.
Ramco Systems
With over 60 customers across 24 countries Ramco serves three segments… airlines, helicopter operators and MROs. Columbia is an example that covers multiple sectors: it has a manufacturing certificate; is an operator and undertakes MRO services. Columbia has been a Ramco customer since 1997 and upgraded to Ramco’s Series 5 in 2013.
Towards a paperless environment
Among a number of industry trends, the growing movement towards a ‘paperless office’ is the most prominent; although, much as we might wish for it, we don’t see an airline fully paperless in the near future. That said ‘InForm’ succeeds in providing a unique technology which allows both e-sign and paper at any given time.
The Columbia Helicopters project
Looking at Columbia Helicopters, while this implementation covered paperless component shops, it still provides paper for other hangar activities because CHI still wanted ‘dirty fingerprints’ on some documents. Together with the CHI team we are working towards having their hangers paperless as well with Task Cards, Engineering Tasks, Non Routines, Routers etc. all flowing through the shop floors through screens not paper. In addition to being paperless, operators want to ensure that cards are standardized – with multiple shops and departments there are often multiple pieces of paper with different styles but calling the same type of work.
One of the first challenges at CHI was to work with their team to devise a standard task card; it sounds easy but after a drill down analysis into their shops we quickly learned how the same field can mean different things to different departments. The final solution was to have headers that are dynamic i.e. Airframe Tasks record different information from Component Tasks while the rest of the Task Card (such as the work instructions, reference information, material pages, images etc.), all remain the same. After about a month we had creted a standard template where everything would look the same, regardless of which writer or department is authoring it. A standard template also makes it easier for whoever is performing the work, not to have to fumble through different styles of the same document. The new task card had to comply with regulatory mandates, company requirements and look like a paper document ready for dirty finger prints. E-signature needed to be secure and follow the FAA’s guidelines. We also needed to ensure that the system had the capability of increasing security, scale and integration as required.
CHI’s requirement was for a single solution to store documents – task cards, EOs (engineering orders), non-routines and reports – in a single environment. This is because mechanics won’t want to go through several applications in order to get to their work, even if they’re all electronic and on the computer. In order to create a solution for this, everything in the project has been made available through IDMR’s web portal. Another requirement was for a seamless interface with CHI’s Ramco M&E system. The interface, as you will see below, needed to be more than a one way pass of spreadsheets for upload/import. The systems needed to actively communicate and synchronize. There is no dual entry, master tables are maintained in one location, and lookups and combo boxes are all synchronized in real time.
Distribution, viewing, and sharing of documents is controlled because not everybody should have access to all documents. The distribution is built into the dynamic workflow of the system and controlled releases and versions of the documents and manuals. Additionally, there are also alerts and notifications; when documents are routed, there’s no need to walk it over for a signature, an email alert is sent and approval can be completed over the web on a computer or mobile device. As soon as the task card is submitted a dynamic workflow tool routes it to the next person or group on the chain. Business rules are built into the template as well. For instance, if a non-routine goes over a cost or man-hour threshold, it can get routed for additional approvals. Workflows are also routed to external sources, for example, with a major repair that has to be routed to the FAA, InForm will send a notification to the FAA and provide them a controlled portal to log-in to, where they can then see and approve documents awaiting their approval.
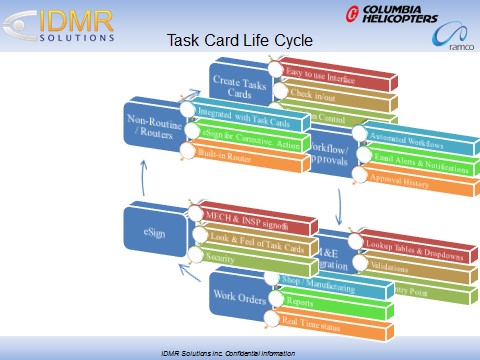
Creation
The first thing is to create a task card for which, in the case of CHI, users entered the information manually. When digital data is available like SGML/XML the system can import that data and reconcile revisions as they arise, allowing the customer to fully re-author the card after the import as well as open mech/insp blocks.
Creating Non-Routine
Creating Task Card
Electronic Sign-Off
Check-in/check-out
While a task card is created or modified, there is an automated check-in/check-out process so that, when one person is editing, a lock is placed on the task card and nobody else can edit it at the same time. When that user closes the document, the system automatically checks it back in, and unlocks it.
Revision Control
All documents have strict revision control; a task card is initiated in a draft status and remains there until all the required signatures are collected. When a user revises an approved card the system automatically creates a copy of the card and places that copy in the draft status. On the approval of the revised card the last revision drops into a ‘history’ bucket and is accessible for lookups and reporting. The entire process is controlled by the system. Approved and History cards are stored an archived. All iterations of a card are stored and easily obtainable.
A familiar appearance
For clarity and continuity of understanding by users, the electronic documents looks like the paper version. Our goal was to take the old paper document and add features such dropdown, popup windows, that are all linked to the M&E system. So while the appearance is of a simple document, there is a lot going on behind each field. Following the iSpec, the task cards instructions drill down to give ‘task’ ,’topic’, ‘sub-task’ and so on; all of that information is captured correctly and signoffs are assigned.
Workflows
Having created a task card, the next step is to make sure that it goes through a dynamic and automated workflow. The workflow email notifications include a pdf copy of the card and reports like the BOM (Bill of Material) and scheduling, giving the approver all the information they need to quickly e-sign and move on to the next step. Each task card/document also stores a history of all approvals (and any rejections, with reasons) applied to it. A rejection will notify the creator and remove all previous approvals. All of this is available on conventional computers and on mobile devices.
M&E Integration with Single entry and submission
Once the task card is created and has been through its approval process, the next step is to send it over to the M&E system. This is because, as we’ve already covered, users want a single point of entry. Each M&E Provider has their required fields for a valid task card. IDMR built their screens to include Ramco’s required fields directly into the task card. Now all the Task Card’s information is available in Ramco without any user interaction.
Both systems are constantly updated in both IDMR and Ramco. Ramco and IDMR developed exchange tables that communicate on every transaction. Any changes made on the M&E master tables flow into document management systems and information is available in real time. This, again, saves users from having to move in and out of systems or wait until the next synchronized update, which could be 24 hours away. To make the integration work properly we developed exchange tables which communicate bi-laterally and allow data flow between both IDMR and Ramco.
Work Orders
When creating a work order (from, say, the Ramco Planning Screen) users simply hit the ‘print’ button to automatically send that order to the exchange tables for InForm to pick up and process. An email is sent to the planner letting him know when the Work Package is ready for print and/or electronic signature. Once the work order has been created, it also provides reports for all materials, components, consumables and tools etc. that are required for the work.
Electronic signatures
After a work order has been created, it needs to be signed off, which means electronic signatures. The mechanic and inspector click on icons placed in the MECH/INSP blocks which look like the paper version, that familiarity supports confidence, along with this idea we made the e-signature looks like a ‘dirty fingerprint’ version – again, familiarity. Also, in addition to stamping the e-signature, IDMR included the mechanic or inspector ID directly on the stamp so that, for future reference, it’s possible to see who signed off that task whether it is printed or viewed on the screen. InForm records and validates a security key, date, time, location and skill to complete the transaction. InForm also allows mechanics to record parameters in the electronic document so that everything about the task is kept within the InForm system and can be data mined at any time. If an inspector rejects a mechanics work, a reason is recorded and the mechanic’s signature icon is available for re-signing.
Non-routines and routers
While performing the work order, non-routines and routers are created. A simple click of the mouse and all the work order and originating task information flows into a new non-routine as the mechanic is typing up their findings. In order to ensure a complete paperless workflow, the Non-Routine gets electronically signed just like the task cards.
Non-routines are created and tracked back to the originating task card and work order. The non -routine also allows CHI to route steps to other shops each with multiple corrective actions and electronic signatures. When the non- routine is completed, InForm sends and updates right back to Ramco and attaches it to the work orders.
Real-time reporting enables the managers to see the process at will. The level of detail is available by drilling down into a task card pending signoff. Reports also display all of the parameter recordings for each task and provide validations if data is out of range.
Summary
The whole implementation took approximately one and half years for the IDMR in including the Ramco interface. The finished system capabilities can be summarized…
- Virtually any documents can be stored.
- There is E-Storage, E-Sign and E-Route of task cards and documents.
- The templating of forms with business rules have resulted in and 80% reduction in data entry mistakes and 100% document consistency.
- Reporting results in actual cost savings for material allocation, man hour forecasting and non-routine hours.
- Revision control.
- A seamlessly integrated document management system.
Contributors’ details:
Paul Myrand: Project Manager, Hydraulic Shop Manager, Columbia Helicopters Inc.
Paul Myrand has over 30 years of Aviation experience. The past two years Paul has been one of the key members of the integration and implementation team in the ERP and M&E project at Columbia Helicopters.
A US Navy vet, his career and love for aviation began in the Navy. After his service he earned both a degree in Aviation Maintenance Technology and, an A&P license. In 1987, Paul joined Columbia Helicopters, Inc. and has been the Hydraulic Shop Manager for the last 10 years.
Columbia Helicopters Inc. (CHI) is the largest privately owned heavy lift helicopter company in the world.
Israel Revivo: President & CEO, IDMR Solutions
Israel Revivo graduated from Embry Riddle Aeronautical University in 1996 and immediately began working with major airlines such as Air France, KLM and JetBlue. His first aviation position was at TowerAir where he used his skills to streamline IT applications and replace manual intensive functions with new technologies. These processes quickly resulted in several millions of dollars in savings. Mr Revivo quickly climbed the corporate ladder and in less than two years was promoted to a director’s position reporting directly to the CEO. He understood that other airlines and MROs could benefit from the same type of analysis and controls and started consulting on projects for American Express, Atlas Air and other manufacturing companies.
Comments (0)
There are currently no comments about this article.
To post a comment, please login or subscribe.