Articles
Name | Author | |
---|---|---|
CASE STUDY: Streamlining maintenance planning at JetBlue | Erin Ritola, General Manager, Maintenance Planning, JetBlue | View article |
CASE STUDY: The transition to mobility | Stephane Menard, Chief technology Officer, M3 Solutions, Steve Bogie, Partner, AeroATeam and Frank Milillo, Partner AeroATeam | View article |
CASE STUDY: Virgin Atlantic uses an electronic record system for lease requirements and returns | Lee Butterfield, Head of Aircraft Programmes and Asset Management, Virgin Atlantic | View article |
CASE STUDY: Kalitta Air takes a big digital step | Luke Usher, QC Records Manager, Kalitta Air | View article |
CASE STUDY: Helvetic goes from a fully managed system to a SaaS solution | Christian Suhner, Chief Technology Officer, Helvetic | View article |
CASE STUDY: The transition to mobility
Author: Stephane Menard, Chief technology Officer, M3 Solutions, Steve Bogie, Partner, AeroATeam and Frank Milillo, Partner AeroATeam
SubscribeStephane Menard, Chief technology Officer, M3 Solutions, Steve Bogie, Partner, AeroATeam and Frank Milillo, Partner AeroATeam identify some considerations about mobility and how to manage mobile devices
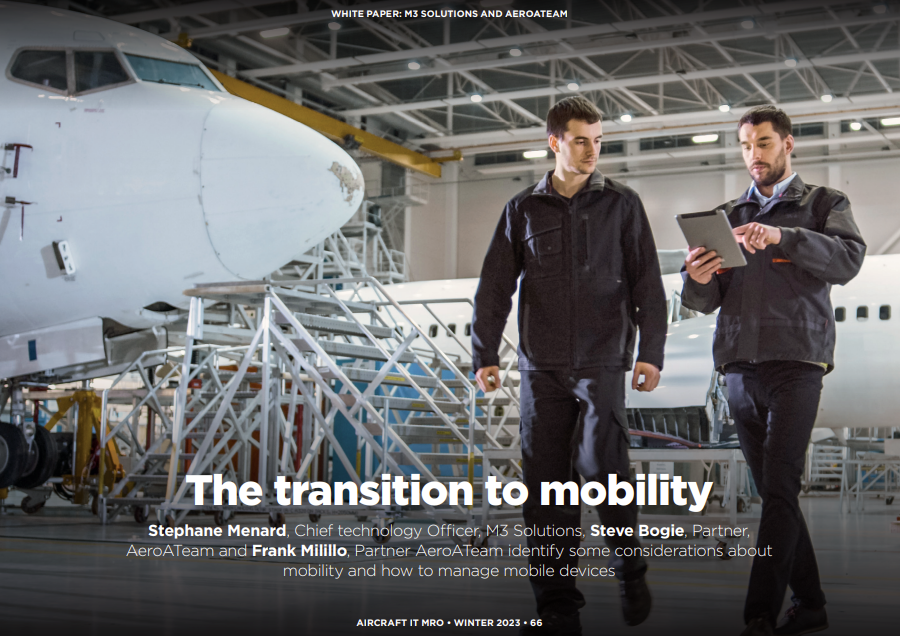
As the material for this article was gathered during a conversation, we have decided to retain the format of the conversation to show how the individual knowledge of each contributor has added depth of understanding to the conversation from three separate viewpoints. We’ll look to cover three main topics here:
- The challenges that stem from using a dedicated device model over a shared device model in MRO facilities when managing and synchronizing technical publications & maintenance manuals;
- Why a shared device model is crucial for keeping cost of ownership low, maintaining security and improving operational performance;
- How automating deployment of MRO mechanic content, application, and operating systems completely remote and unattended can eliminate bottlenecks and increase efficiency.
The focus of the article will be to compare two approaches to managing a fleet of portable devices used daily by mechanics in an MRO environment to perform their tasks.
Some airlines have opted to provide each mechanic with a device, the dedicated approach while others have opted for pooled devices shared across all mechanics, the shared approach. These two options each have their pros and cons, and that’s what we’ll cover here.
THE TRANSITION TO MOBILITY
Stephane Menard: Steve and Frank, what are your views on the transition to mobility across the industry as a whole? We have been discussing paperless operations for a while; and yet I’m always surprised to see that some line maintenance departments are still running on paper. What are your views on the state of this transition and its importance related to compliance, risk mitigation and operation efficiency?
Steve Bogie: As we exit the pandemic, we’re seeing greater focus on cost and operations efficiency from most carriers. What this means is a heightened awareness of the ability for, in this case, mechanics and those supporting aircraft operations and MRO operations, to be completely dedicated to their job. As a result of that, airlines and MROs are looking to technology in an effort to drive efficiency.
Digital and mobility are critical components in achieving maximum hard time for mechanic, EMEs and support functions on the aircraft. This is a new and evolving trend which has been in existence for a while but with a heightened and growing awareness in recent years.
Frank Milillo: From the end user perspective, in the heavy maintenance environment, we’re always focusing on increasing optimization; creating an environment where the technician can do everything s/he needs to every day or shift while staying on or near the aircraft and with access to technical publications. This is something that we have been striving for over the years and, in the base maintenance environment, mobile devices offer a great opportunity to move forward.
From the maintenance perspective having the publications and the reference documentation with the correct revision status all the time is key; we don’t have to worry about whether the rev status is up-to-date or whether or not mechanics are working with documentation that is at rev status. A big thing in a base maintenance environment or a heavy maintenance environment is uncontrolled documentation; so, all too often, we get non-compliance findings because there are outdated, non-compliant references that might be on a tool box or on a stand or on the aircraft. Mobile and paperless documentation eliminates that risk.
SM: I assume it is a complex transition, moving to paperless. I was surprised to see many corporations are still paper based. From a technology perspective, what does it entail to make this transition?
SB: Moving to paperless cannot just happen at the flip of a switch; it involves a lot of coordination, good system partners, good system integration and good training of on the new processes as well as designing sound, straightforward processes and procedures that meet the obligations to the regulator. First and foremost is the repository where these documents would sit. You need to build the foundation, transition the business to digital documents and, once that’s sound, get sign off from the regulator before transitioning over, and then quickly generate mobility.
From a true IT technical perspective, there are some mature systems out there. You want to integrate those systems tightly with your active director or whichever authentication program you’re on to make sure that the right people have access to the right systems at the right time. But once you’ve made the transition to digital and mobile, there’s a speed and efficiency benefit. Rather than taking days weeks and months to do revisions and distribute the paper (print it and pull it in and out of manuals); in a digital format, that can be done in hours. Considering the savings in printing costs and shipping costs, paper (especially for a very large airline) and the environmental impact of all that, there are lots of benefits to moving in this direction but, as was said earlier, it’s not just the flip of a switch. Any transition to paperless and mobile should be well thought out, well planned and I would encourage anybody looking to do it to closely involve the whole business, front-line workers as well as the regulator.
SM: If I understand you correctly, you feel that there’s no technology hurdle at this point. Technology is there but it’s more a question of implementation which was probably not true ten years ago.
SB: Fair assessment and I’d definitely say that this is not a technology problem. This is about people and change, change management, a questioning process; it’s not a technology challenge.
TWO APPROACHES TO MOBILE DEVICE MANAGEMENT
SM: Right, let’s go to the heart of this article: What is the best model for your organization; a shared device approach or a dedicated one? All airlines will have to go through the process of evaluating which way to go which will not be an easy process but will be worth the effort.
The kind of question you will have to ask yourself is, for example, do you want the mechanics to be responsible for the device and/or content related tasks such as updating OS, updating the apps and making sure that the technical publications are synched properly. At the beginning, it might seem manageable but over time the number of apps will grow and then data for these apps will get more complex and larger. This is important, especially if you want locally hosted content which is important to ensure that data is always available for your mechanic, even if the Wi-Fi or cellular connection is weak in some areas or not available at all.
I’ll elaborate on this some more. Almost all the apps that deal with content have online capabilities; so, the data is always available as long as a network is but having locally hosted content enables mechanics to always have access to the data to do their job. So, it provides for a more robust and high availability solution while increasing the efficiency of the workforce. This is not to be minimized as over the last ten years, this model of having data on the devices in addition to online access has proven to be more efficient: a better approach and definitely more reliable.
That’s one question. Another one would be, how do we deal with spares? Spares will be needed because equipment will fail, a device will be lost or won’t be updated properly or a mechanic will find, in the morning, that the device is not charged enough to last the day. Should all this be the mechanic’s responsibility?
Let’s look at the shared device model. In that case, the IT and the logistic team will manage the devices. The logistic team will manage the hardware as well as device check-in, check-out, tracking the devices, tracking the user, and managing repairs and spares. This could become a cumbersome task as the fleet of devices grows. At the beginning, with a few hundred, that might be fine but when it gets to thousands it will get more complicated. On the IT side, they’ll be managing the content of the devices with all that that entails. In the end, it will be time consuming and costly but at least, in that case, the appropriate staff will be doing what they’re good at.
That said, what are the opinions of our two experts? Frank from an Operations perspective and then Steve from an engineering standpoint?
FM: I’m on the side of shared devices. Technicians are technicians, they want to fix airplanes; they don’t want to have to maintain a computer or a device or a tablet. We have a hard enough time getting a technician to enter data into the enterprise system that they’re currently using so that has to be made as easy as possible. Placing that burden of updates and the control of the device onto a purpose-built solution and platform strikes me as beneficial. At the end of the day, the technician returns the unit to its proper place and goes off until the next day. S/he doesn’t have to worry about accountability for it. Also, I think that having the shared responsibility of maintaining the device, maintains the integrity of the unit itself.
SB: With most of these decisions, each carrier will have different priorities and approaches. There are pros and cons for each model but putting the onus on people to keep the devices updated has risks. In an environment where compliance is so important and with a shortage of skilled technician resources available to undertake the work, mobile devices become mission critical when paper has been removed because there is no fallback other than additional devices. If they don’t get updated, they become vulnerable to, say, some ransomware getting on them if somebody is using the device at home for non-work activities. Also, if the technician forgets to plug the device in to charge and the battery goes dead halfway through their shift, that will cause disruptions to the organization with the aircraft service delayed and it not being returned to the line on time.
There’s certainly some risk associated with the dedicated device but there are also a couple of pros. Personalization can sometimes be an employee benefit letting them gain ‘ownership’ of the device. Plus, there is the potential for off-site training. There are some upsides to a dedicated device and, at Air Canada, we considered both options very closely before, in the end, opting for the managed device model which very quickly proved to be the right decision. We were very comfortable that the devices were tracked, they were always up-to-date, they were always charged and, if there was some sort of an issue with either the charging and/or the content updating or technical issues, we knew about it right away and could dispatch an IT technician to deal with the issue rather than worry about a non-trained individual trying to troubleshoot it out on the frontline. We very quickly came to the conclusion that the benefits of the shared model far outweighed any downsides and was our preferred solution for Air Canada.
SM: It looks as if we’re all in agreement that each team member in an organization should focus on what they’re skilled for: mechanics stay at the airplane, logistics manage the device and the IT team deals with device content or anything related to IT around the device. Of course, it’s easy to say and we realize that it could be complex to implement in any tool cribs and that is exactly why the M3 platform was developed, the system essentially automates the processes that the logistic and IT teams will need to do in a shared device environment. In fact, the concept was developed with Air Canada in 2015 (Aircraft IT MRO Issue 54: Winter 2022 ‘Managing and synchronizing devices of all types at Air Canada’) where M3 was first approached and the idea was exactly that: a shared approach is a better approach for them but we needed to eliminate the heavy lifting of the content management and also asset tracking and maintenance. That’s how M3 Platform came about.
THE M3 PLATFORM
Now, I’d like to tell you something about the M3 Platform; what it is, how it works and what it does for a fleet of devices.
The solution can be defined by two main components: the Kiosk hardware and the content management software. The kiosk itself controls access to the devices via a card reader, a badging system, which could be an RFID, an NFC or other type of reader. Importantly, when the device is in the kiosk, it is physically locked so that the technician will need their badge to check it out. In the kiosk, the device charges and will communicate with our back-end software which enables the content management. Generally, the solution supports tablets and laptops both of which are deployed with some customers, including Air Canada, and the operating systems supported can be Windows, iOS and Android plus it’s fully scalable, so can go from an installation with only a few dozen devices to some with thousands of devices. Most of the time, the kiosk is in a self-serve environment; so, check-in and check-out is done by the mechanics, eliminating the logistic part of it. When a mechanic needs a device, they go to the kiosk, get a device and go to work. If it gets broken or runs out of battery, s/he comes back to the kiosk and takes a new one. The logistics are taken care of by the kiosk.
AUTOMATION ADDS REAL VALUE
Now that is for the hardware, essentially and, as you can see, this really automates the logistic component.
On the software side, the main function of the solution is to automate content deployment of any kind; it could be an app update, it could be an OS update, it could be technical publication deployment or any other content that requires to be side-loaded to a specific application. By integrating with each app, which we do all the time, the process becomes totally seamless and really zero touch. The IT team is not involved at all when it comes to content management. M3 has a team which is dedicated to that, to automation, and they are constantly integrating apps from different vendors in order to satisfy that goal of seamless and zero touch operation. Additionally, the solution can wipe the device clean after each usage which most of our customers use so that there’s no login information or browsing information. If need be, information can be uploaded before performing a wipe if, say, there there’s some data that needs to be synched for the next user and you don’t want to lose that dataset
For simple tasks related to device management, M3 has integrated with Best of Breed MDM. For iOS and MacOS we use Jamf, for Android we use Knox and for windows we use Microsoft Tools. The goal was always to make the shared device model the approach of choice and through automation, we believe that it removes all the pain points in an implementation. It means being able to logistically and from an IT perspective, have teams in place where you need them across the organization to deliver these tasks.
For those who haven’t used the M3 Platform, this may sound theoretical; so we’ll ask Steve to discuss his hands-on experience with the solution when it was deployed at Air Canada, starting in 2015. Since then, the environment has grown from one to a dozen or so apps and a great deal more of data but when you implement automation, you’re making yourself future proof.
GOING MOBILE AT AIR CANADA
SB: At Air Canada, we did not start by saying we’re going to use M3. Early in the process, we identified the objective of how to keep the mechanic planeside, working on the airplane. The idea was, give the individual a mobile device with all of the digital content that they need to keep them planeside, whether that’s aircraft manuals, IPCs, a view of the inventory stock, scheduled time for the aircraft and even links to fleet specialists and other tools that we had provided. That was our view and that was our goal. We started with one app, a ‘walk before you run’ approach where we wanted to start slow but scale it fairly quickly thereafter. At first, we were using dedicated devices but soon realized that it was very difficult to manage with some of the challenges we covered earlier in the article when devices hadn’t been updated, hadn’t been synched, hadn’t been charged and so on. We looked around for different solutions and ended up selecting M3 which Air Canada continues to use today.
This wasn’t without its challenges and, as we scaled, a lot of the infrastructure that we had in our hangar facilities, which was was dated at best, had to be upgraded to accommodate the large volumes of data that we were synching back and forth to our M&E system, to our content management system, to things like Boeing Toolbox. At that time, Air Canada was flying Airbus, Embraer, Boeing and Bombardier airplanes so we had to address every OEM. We wanted a single device because we didn’t want to get into different devices for different OEMs, plus it was necessary to scale and build a lot of infrastructure with processes and controls to ensure that the right people had it. Also, the devices were synchronized to Air Canada’s authentication systems and the corporate cyber security plan was built out to ensure that our devices were secure. All the devices were registered centrally with Air Canada’s IT support organization and asset management organization; it was really just an extension of what Air Canada did. There was a little more work when we did it but that paid dividends in the long run and it saved us from creating dual and parallel systems and processes. Today, Air Canada has complete automation of its device management.
FM: Perhaps I can add in a couple of things that we haven’t touched on yet. When we talk about heavy maintenance environments and MROs, we should always focus on safety, quality, schedule and cost and there is a safety element in this shared device system. When you have a system such as M3 is offering, there is the consideration of space which, in many hangars, is at a premium; there is also the consideration of productive labor and unproductive labor. There are many organizations with a separate room in which they keep all of their tablets, laptops, printers and other hardware but that room might be at the opposite end of the hangar from where the technician is working and, of course, that is unproductive labor when that technician is travelling across the hangar, going to the room and doing what needs to be done – printing up the reference document and then going back to the airplane – which is, again, unproductive labor. The more area and space that’s freed up in the hangar environment, the more organized we can be which, in turn, will lead to increased safety and lower levels of risk.
Also, when mechanics use desk top PCs, sometimes they might forget to sign out and them still being signed in is another compliance aspect that we haven’t touched on yet. With a shared device, that unit is with that person and is under the control of that person the whole time. And, of course, with everything in the room at the end of the hangar, there is the cost associated with computers, monitors and devices, the seating and the real estate for all of those things in the hangar environment. That cost is virtually eliminated with a system such as the M3 solution.
SB: All that is so true including for people involved in Line Maintenance where the desktop computer might be a long way from the gate where the mechanic has to work on the aircraft.
SM: Let’s close by thanking Steve and Frank for contributing to the article. We hope that, our explanations of the move from paper to digital with the adoption of mobile devices and how to manage them will have demystified the process and that readers who have been considering such changes will be encouraged to set out on their own project.
Contributor’s Details
Stephane Menard
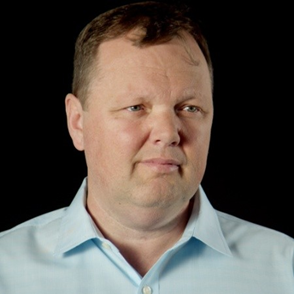
After three years as Senior Product Manager at Nortel Networks, Stephane was appointed Chief technology Officer (CTO) at Simpler Network in March 1999. In 2010, he took on the role of CEO at M3 Solutions Technologies and then, in 2019, became Chief Technology Officer. Stephane has particular skills in the areas of embedded systems and embedded software.
Steve Bogie
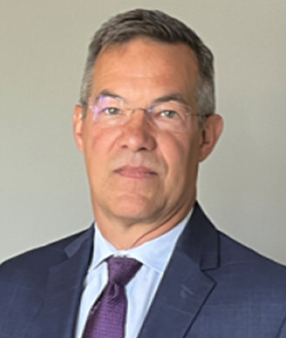
Steve has over 30 years of experience in commercial aviation mainly in the Air Canada, Jazz family. Starting his career in Airport Operations, Steve then moved to Systems Operations Control and then into the technology side of the business until 2020 when he became a partner in the AeroATeam with a continuing focus on technology in the aviation space and helping commercial airlines to move forward.
Frank Milillo
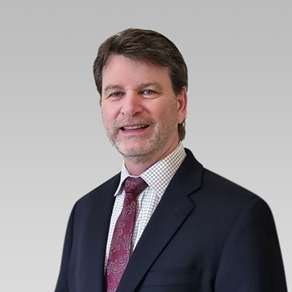
Over 30 years in the airline industry, Frank’s career started in the United States Air Force before working in the original Pan Am, American West Airlines, US Airways and American Airlines. At both US Airways and American Airlines, Frank had responsibility for Base Maintenance at a senior level as well as for quality control.
AeroATeam

The AeroATeam includes industry experienced colleagues delivering complete MRO technical services, operations & technology support; offering incredible people combined with advanced technology licensing, hosting, and custom application development. AeroATeam capability offering combines five critical elements of success: Software Licensing Options; IT Technology Hosting and Integration; Implementation and Management; Maintenance, Engineering, and IT Tech Services; Airline and MRO Technical Operations Business Support.
M3 Solutions Technologies
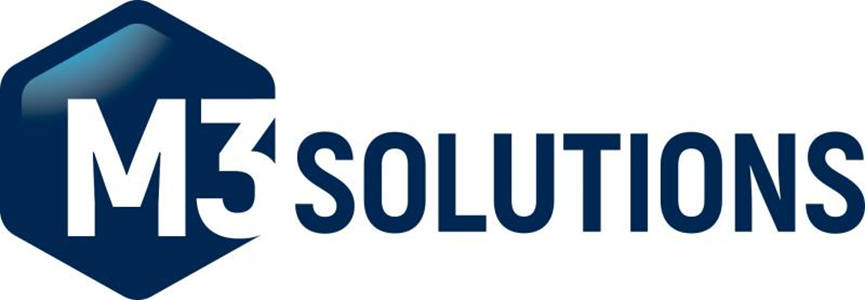
M3 Solutions is the company behind the M3 Platform, a comprehensive hardware and software solution for portable device and content management. M3 solutions has sales facilities to service customers worldwide. The solution allows administrators to control the managing, distributing, charging, and monitoring of an organization’s portable device inventory with easy remote and unattended content distribution including OS, App & Content deployments, across all devices in the network, anywhere, within minutes.
Comments (0)
There are currently no comments about this article.
To post a comment, please login or subscribe.