Articles
Name | Author | |
---|---|---|
WHITE PAPER: Current Trends in the Predictive Maintenance Aftermarket | Dr Ip-Shing Fan, Senior Lecturer in Enterprise Systems at Cranfield University and John Maggiore, senior aerospace leader and consultant and Senior Advisor to the Integrated Vehicle Health Management (IVHM) Centre at Cranfield University | View article |
CASE STUDY: Making a good digital start at Heston Airlines | Edgaras Knyzas, Head of CAMO, Heston Airlines | View article |
CASE STUDY: Production planning and control at China Airlines | Wei-Fong Wang (Matt), Senior Engineer, Maintenance Division, China Airlines | View article |
CASE STUDY: An RFID cabin monitoring tool at AirAsia Thailand | Banyat Hansakul, Group Head of Engineering, AirAsia and Nazrulazli Najmudin, Senior manager, Product and Technology, Asia Digital Engineering (ADE) | View article |
CASE STUDY: Making a good digital start at Heston Airlines
Author: Edgaras Knyzas, Head of CAMO, Heston Airlines
SubscribeEdgaras Knyzas, Head of CAMO, Heston Airlines shares the start-up airlines experience of working with OASES right from the outset
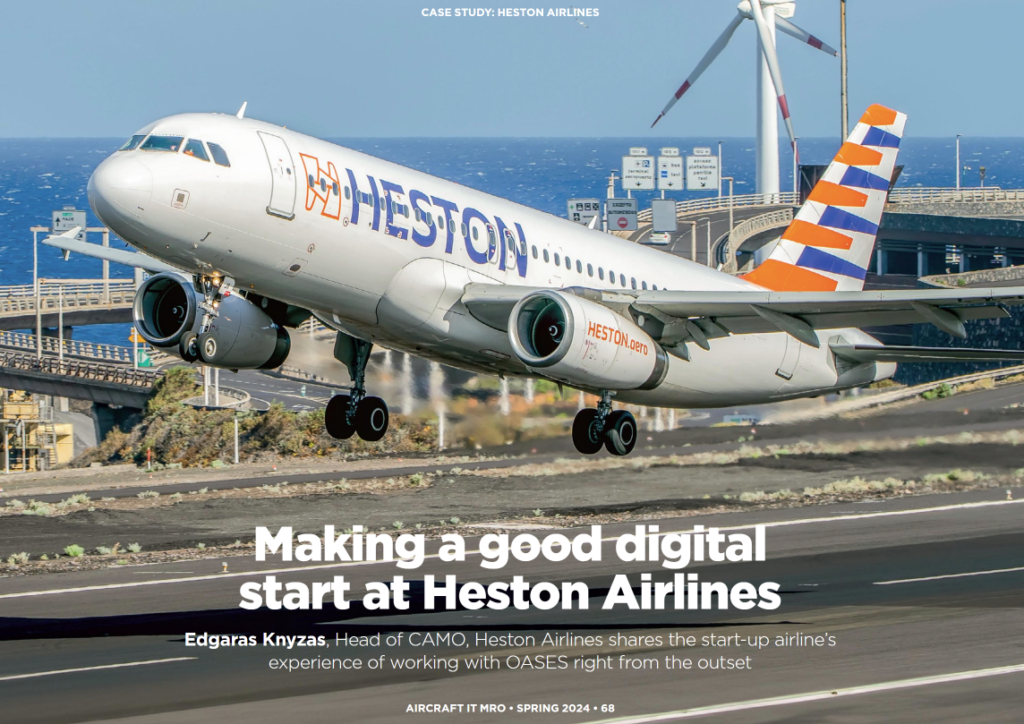
One of the purposes of a case study is for readers to learn how any new solution might work in their airline, their working environment. To do that, it’s first necessary to learn about the airline that is the subject of the case study. So, we’ll start with some information about Heston Airlines.
HESTON AIRLINES
Based in Vilnius, Lithuania, Heston Airlines was set-up in 2021 during the pandemic and the main reason for starting the airline was that there were a lot of aircraft available in the market at good prices at that time. The founders used that situation to their benefit to make a fast start with a new airline which currently operates 15 aircraft of which 12 are from the Airbus A320/321 family while a further three are the larger Airbus A330s. We operate ACMI and Charter with world-wide operations. In the northern winter season, we fly to destinations such as Nigeria, Uzbekistan and Dominican Republic: during summer operations our services are focused more on Europe where we fly from Norway, Finland and Germany on behalf of operators such as SmartWings and Condor.
THE CASE FOR IMPLEMENTING OASES
As a start-up airline, Heston had no legacy of processes with pain points to address and when I started with the airline, OASES was already in place. However, my understanding from colleagues with previous experience in other airlines was that they used to manage aircraft maintenance using in-house, small software solutions or even, if the fleet was not too large, would track the aircraft on Excel spreadsheets. The pain was lack of automation or any automatic notifications of due dates. It was hard to generate a work order but, frankly, all of these issues are addressed in OASES because the solution makes it much easier to manage a bigger fleet with more complex aircraft. It’s theoretically still possible to manage a small fleet with few aircraft on Excel spreadsheets but that approach is highly susceptible to human factor errors which is why we need tools that allow the automating of processes and that will eliminate the errors that could be caused with human interventions.
At the start, the company management forecast a rapid growth for the airline with the consequent large amounts of incoming data that would need to be handled. There was no question about the need for a system which could automate the handling of that amount of data. A few of the main solution vendors were evaluated and the short list came down to OASES and one other. In the end, OASES was more approachable with the pricing plus the quality of the services was very good as was the accompanying IT support from the OSAES team. As a result, Heston Airlines launched with OASES already in place because the founders were familiar with the system and already considered it to be a balanced solution for a start-up airline. With a cost range that fitted the budget and the quality of provided services being equivalent to the cost, we also found it to be a cost-effective solution.
THE IMPLEMENTATION
Although it was a straightforward process, it took some time to implement the new solution. It needed a lot of training and support for our people to get their hands-on experience of OASES, to get a feeling for the solution. As with any solution, we found it was important to bring people up to the specialist level needed to get the best from the solution and to ensure that they acquired the specific knowledge about the software. That meant that there was a need to deliver proper training to use the system and that took some time; then to import the first aircraft into OASES was a challenge and for people to start to use the system, to know how to do it. That said, after the first few aircraft had been imported to the system, the rest of the fleet was quite straightforward because the personnel already knew how to do it.
Heston Airlines was developing its various processes around the system at the same time that the implementation was underway. OASES, as a system addresses a lot of the topics in aircraft and airline management starting from planning, continuing with repetitive defect investigations then AD (Airworthiness Directive) assessments with dent & buckle, charts management, Service Bulletin assessments and all of that sort of important information.
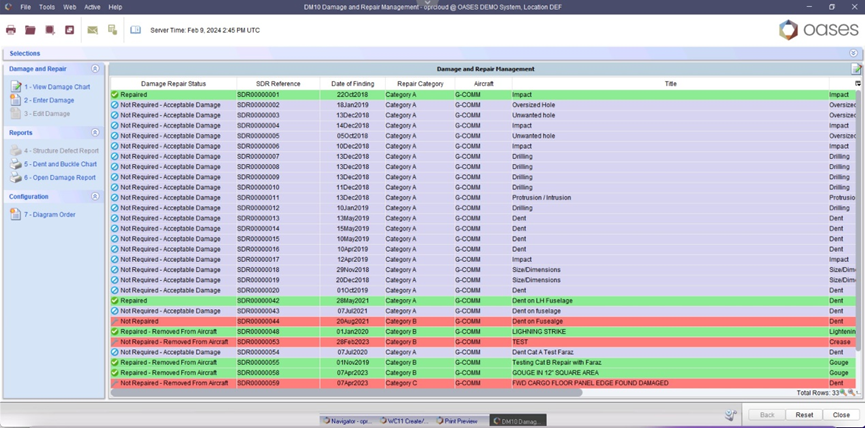
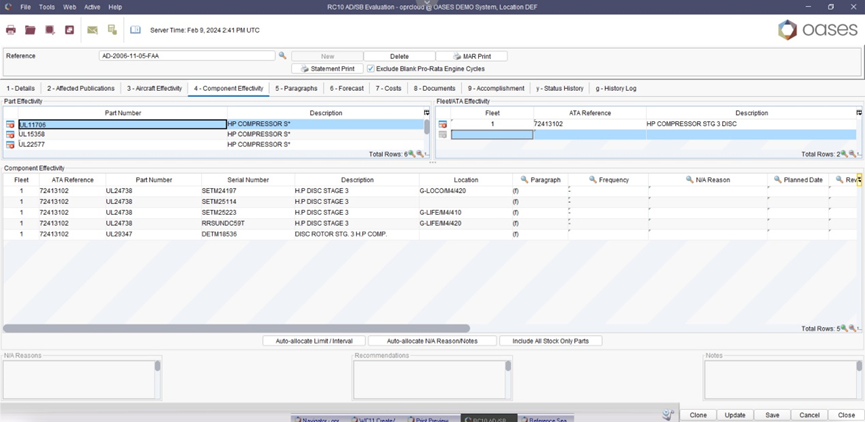
In general, OASES creates a tool that delivers everything the business needs to manage the continuing airworthiness of the aircraft. If you build your processes around the system, you don’t need to invent new ways to manage airworthiness because there is already the tool with OASES to do everything that is required by the regulations. OASES offers a structure that is useful when starting an airline.
As a start-up airline, there were lessons to be learned and OASES was a valuable tool to use in that. For example, for reliability monitoring of the aircraft, there are some very good tools in OASES, reliability reports that can be exported from OASES as well as a repetitive defect tracking module.

LESSONS LEARNED
Having these tools has identified for us things that we need to do. Another thing is that, when we started, OASES was provided through a sub-contractor and we later transferred to the OASES contract being directly between Commsoft and Heston Airlines. The issue here was that we needed to transfer all of the data for Heston’s aircraft that had been in the sub-contractor’s system, into the system at Heston Airlines. The lesson from that is that, if you’re starting a new airline, have a contract directly with the software provider from the outset because sooner or later, as the airline grows, that contract will be required and there is an issue when transferring data when the new system might be involved that is a little different from the sub-contractor’s system, different language and differences when controlling the data. In short, the process of taking the data from the old system through the sub-contractor and importing it into Heston Airlines’ OASES was not straightforward or easy to do and it took a few months for the project to take the data and transfer it. It also took a few tries before everything was running smoothly. The lesson was that it’s best to start with a direct contract between the airline and the software vendor. If sub-contractor services are needed the access can be granted to the sub-contractor to use the airline’s OASES software.
CHALLENGES, OBSTACLES, TIMELINE AND APPROVALS
The main challenge was to train personnel, particularly as we were building the team, adding new people who were fresh to OASES, they needed time to properly grasp what is OASES. In some cases, there was additional training needed to help people get a good understanding of the solution. The main thing is to spend some extra resources on preparing the team and preparing new employees for using the system. At the beginning, there were only a few people involved in Heston, so it took three or four months from the first contact with OASES until the induction of the first aircraft.
There was no specific need to get approval from regulators for OASES but, of course, the national authority had to approve the whole organization with its processes. So, our Continuing Airworthiness Management Organization (CAMO) was approved by the Lithuanian National Aviation Authority and the processes that work with OASES were also approved together with that.
WORKING WITH THE COMMSOFT TEAM
There were some ups and downs if ever we weren’t completely happy with something, the OASES team took note of that and addressed it. Overall, we are very pleased with the communication. They have a very good and supportive team who are very professional and there is a system for addressing the inevitable bugs and issues that arise from time to time, and that works really well. If we have any kind of an issue, we can get a solution quickly, response time is really good.
FUTURE PLANS
Now that the system is up and running, our people find OASES to be overall very good. There are some questions around the formats of Airworthiness Directive reports and Service Bulletin reports which formats are specific to OASES and which can make it hard to filter exported data. Also, some modules can only be used by one person at a time. For example, for planning, if one employee is using the module for a specific aircraft, another employee cannot enter the same aircraft with that module. It creates a problem with future scalability when the fleet has expanded with a lot more aircraft and there will be a need for several people to work in parallel using the same module.
That said, Heston has fleet expansion plans in the near future to double the fleet in two to three years and we see the OASES solution as a good fit for that. What we are also planning to do is to use the API (Application Programming Interface) services provided by the tool to link the OASES software with our other flight schedule management tools which will allow us to automate part of the data input from those systems directly into OASES and reduce the manpower needed to manage all of the records.
OVERVIEW OF OASES
OASES is designed to enhance the efficiency of aircraft maintenance and fleet management processes. Tailored to meet the intricate demands of the aviation industry, OASES stands out for its ability to streamline airworthiness compliance and maintenance planning processes, making it an indispensable asset for airlines, maintenance providers, and aviation leasing companies seeking operational excellence and regulatory compliance.
Production
The production module provides real-time visibility of task status and automatically generates reports on KPIs, such as budget vs actual labour expended, defects raised, and materials issued or returned. You can plan resources, from hangar level down to individual tasks. All work cards may be bar-coded, which makes it easy to capture work in progress data. As the employee number, materials used and start and finish times are recorded, it enables fast and efficient analysis of the task’s progress.
Line Maintenance Control
The Line Maintenance module enables you to integrate data from many sources (such as electronic tech logs) to improve short-term maintenance planning, and ensure defects are rectified.
It integrates planning and material control functions to intelligently and automatically reserve stock or send a picking notification to stores. You can see all short-term scheduled activities, component removals and defect rectifications – forecast on a single screen, and automatically create and send LMC worksheets to the relevant workstation. You can also view defect history to identify problems faster.
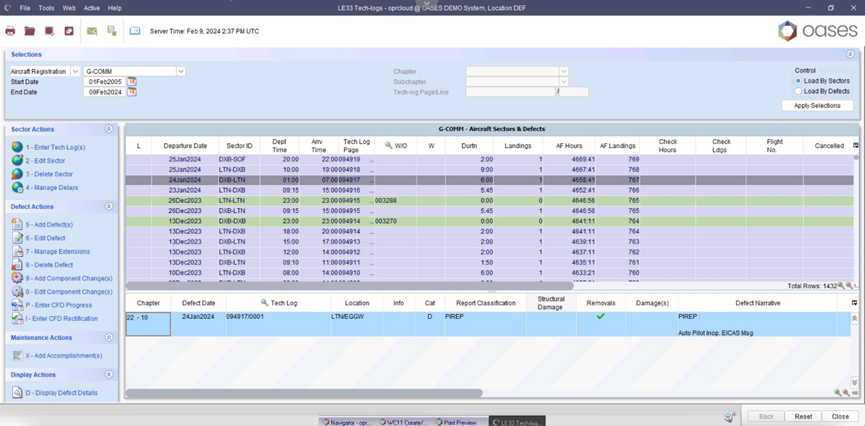
Material Management
The Material Management module helps you improve the cost-effectiveness of your stock control and ensure availability when required; no waiting for parts to arrive, no delayed schedules, no loss of income (figure A).
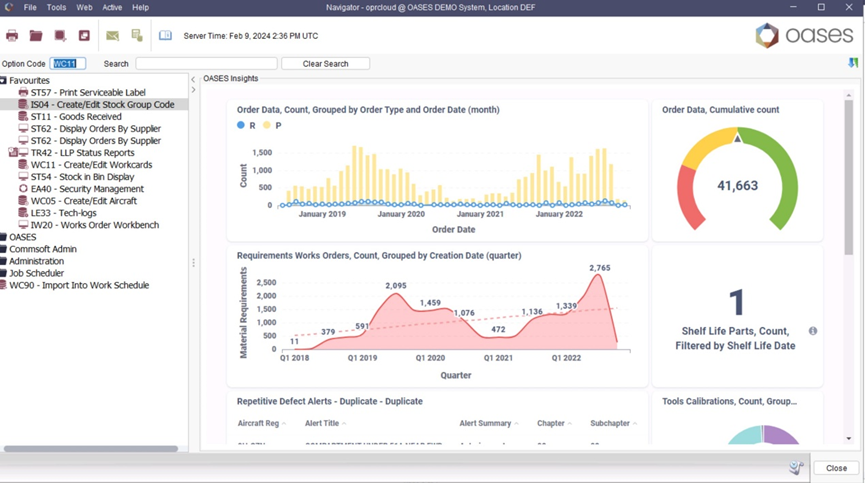
You can even check stock and issue parts on the move with the OASES mobile app. Automatically log parts in and out, use RFID for tool control, create requests for quotes, send orders and pass through to accounts for payment.
Commercial Management
For deep coordination, analysis, and reporting across all financial aspects of the business, check out the Commercial Management module. You can accurately track and invoice labour and materials for third party work, simplify processes and analyse financials in real-time to make operational changes as needed. Commercial Management is also used for the admin processes around invoicing, cross-charging, forecasting, and reporting.
Heston primarily uses the Continuing Airworthiness and Planning modules.
Continuing Airworthiness:
The Continuing Airworthiness module is used to ensure aircraft are maintained in a condition for safe operation. This module facilitates comprehensive oversight of maintenance records, airworthiness directives, and service bulletins, ensuring that all maintenance activities are performed in accordance with strict regulatory standards. It automates the tracking and management of critical airworthiness data, significantly reducing the risk of non-compliance and enhancing the safety and reliability of the fleet.
Planning:
The Planning module of OASES helps optimise the efficiency of maintenance schedules. It enables planners to forecast maintenance requirements, schedule maintenance events, and allocate resources effectively, ensuring minimal downtime and maximising aircraft utilisation.
Release 11:
With the latest addition to the OASES software, Release 11, powerful new functionality is added, including a completely redesigned Maintenance Control module, a new user interface, streamlined API capabilities and the new business intelligence tool, OASES Insights.
In summary, OASES stands out in the aviation maintenance software market for its depth of functionality, flexibility, and user-friendly design. By offering a comprehensive suite of tools that cover the breadth of maintenance operations, OASES empowers aviation professionals to enhance operational efficiency, ensure compliance, and ultimately, maintain the highest levels of safety and reliability in their fleets.
Comments (0)
There are currently no comments about this article.
To post a comment, please login or subscribe.