Articles
Name | Author | |
---|---|---|
HOW TECHNOLOGY WORKS: Taking a digital solution to MROs | Israel Revivo, CEO and President, IDMR Solutions Inc | View article |
WHAT IT CAN DO: The secret of a successful MRO IT System upgrade project | James Cornelius, President of ROTA Technology | View article |
CASE STUDY: Maintenance planning at FedEx Express: Today and the future | Roger L. Hutchinson II, Manager TechOps Strategic Mx. Planning, FedEx Express and Elliot Margul, CEO Aerostrat | View article |
CASE STUDY: Chrono Aviation and WAAS benefit with a modern IT solution | Dominic Cayouette, Project Manager, Chrono Aviation and Peter Mortimer, Executive VP Canada, Rusada | View article |
WHITE PAPER: Embracing digital transformation | Adnan Mansur, Head of Digital and Innovation Services, Asia Digital Engineering | View article |
CASE STUDY: Maintenance planning at FedEx Express: Today and the future
Author: Roger L. Hutchinson II, Manager TechOps Strategic Mx. Planning, FedEx Express and Elliot Margul, CEO Aerostrat
Subscribe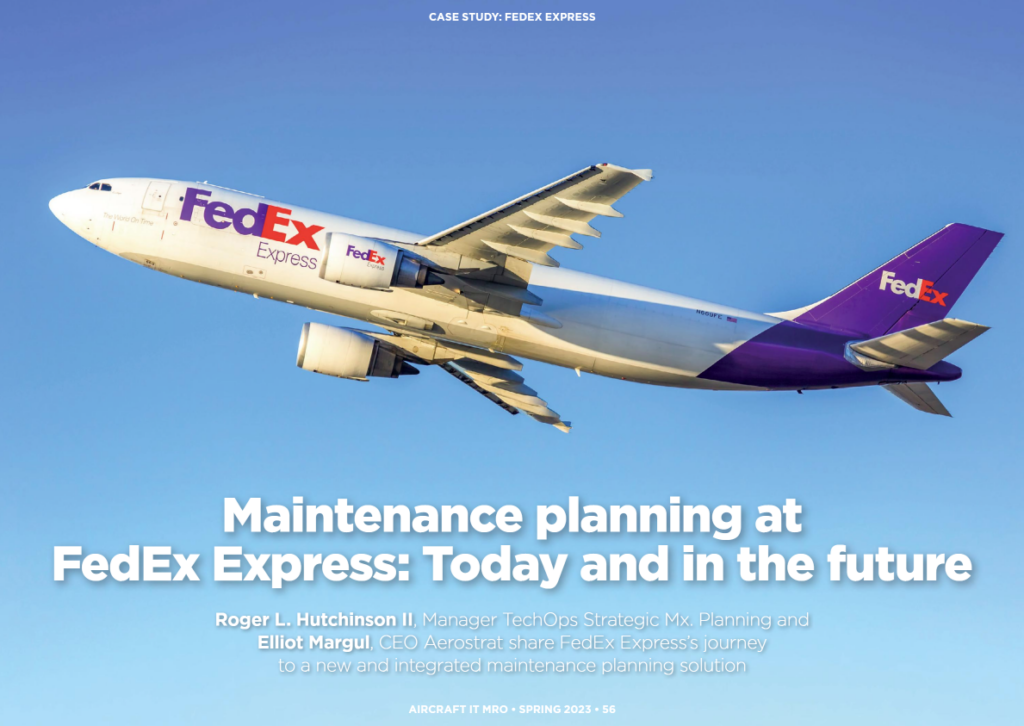
Roger L. Hutchinson II, Manager TechOps Strategic Mx. Planning and Elliot Margul, CEO Aerostrat share FedEx Express’s journey to a new and integrated maintenance planning solution
Like many airlines, six years ago, FedEx Express IT capability was based on old mainframe systems. However, with a large and growing modern fleet, the airline was looking for ways to streamline the maintenance processes, including maintenance planning. Roger had always been of the view that maintenance planning should not be difficult and that there should be ways to automate it as well as the software to make that happen. That said, FedEx Express had never previously had the systems or the sort of software solutions available today. This case study is about how FedEx Express started to change that and how it found the right partner with which to achieve the necessary modernization of maintenance planning as well as the integration of that modernized solution with the rest f the business.
FEDEX EXPRESS MAINTENANCE PLANNING GOALS
Let’s start with why FedEx Express needed a new software solution. Throughout its history, FedEx had implemented data systems both purchased from other carriers and developed in-house and was looking for a better way to do things such as having the ability to track defined tasks and to add their own data into a system. This was reflected in two sets of planning goals with the overall objective to modernize and streamline the business but which also identified several individual goals within those overall objectives. First, to modernize:
- Improve speed of planning;
- Amount of detail;
- Better collaboration across planning and department;
- Provide a modern UI for legacy systems;
- Provide a platform to enable planners to make strategic planning decisions rather than ‘plan what’s next’.
The second set of objectives could be summarized as ‘streamline the business’ expressed as… streamline the planning process from plan to induction; hasten the process of understanding changes and variables via scenarios; automate as much as possible and ensure the team focuses on value-added tasks.
THE SOLUTION SELECTED AND IMPLEMENTED BY FEDEX EXPRESS
Aerostrat started six and a half years ago and was exhibiting for the first time at MRO Americas with what might best be described as a shell of a product compared with today. Notwithstanding that, two people from FedEx went to the booth and started a long conversation that turned into a longer and ongoing project which is the subject of this case study. Following that first meeting, Aerostrat and FedEx Express worked on the airline’s needs and pushed the software product in ways that had not been anticipated by its creators when they first built it, stretching the team and the product with different levels of innovation. Because of that, Aerostrat and FedEx Express commenced a multi-year project which. Rather than just focusing the Aerostrat product on creating a modern maintenance planning solution for FedEx Express, it was instead used as interface for multiple legacy systems as well as, in the long run, being able to drive a large range of business simulation software.
The Aerostrat product, Aerros, is a heavy maintenance planning solution creating a platform for users to add whatever tasks they want to track, all the necessary fleet data to a high level of detail. For either or both aircraft and aircraft models, users can create a utilization model that is static or set for an absolute date range. That information, with tasks can be used to actually forecast every time that each requirement will have to be met, right up to end-of-life for each aircraft.
The solution then takes the constraints that are required to complete heavy maintenance with a range not limited to maintenance allocations or track allocations. Additionally, the system understands the compatibilities between tracks and requirements, and requirements and requirements. The solution also monitors and optimizes the yield goals for every single task: what is the minimum and maximum yield that’s allowed for each task and what is the target yield for each task. Furthermore, Aerros takes in capacity information down to the shift on a specific day and what is the amount of labor required to get the maintenance visit accomplished.
The system incorporates all these various data inputs and uses an auto scheduling tool to create an optimized plan that spans multiple years: almost all of Aerostrat’s customers maintain a five-year schedule with that information. The solution also offers users the ability to quickly edit the information, push the data out to stakeholders, edit any variable down to a day or a shift, re-flow the schedule and understand the implications of that change. From there, Aerros gives users the tools to analyze those outcomes so that they can understand what that variable will do if it did change or create a new maintenance plan as a result of that change.
Why Aerostrat was chosen
Early on, when FedEx Express and Aerostrat first started to meet, one of the things that attracted the airline to the software business was that, speaking with Aerostrat, it seemed that their goals lined up with those of FedEx Express. Also, being a small business at the time, they were very customer focused (figure 1).
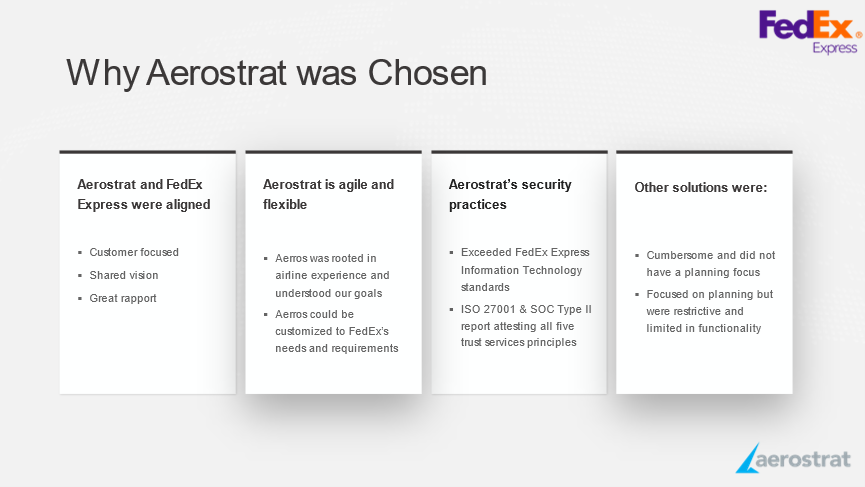
Figure 1
The conversations about maintenance planning and scheduling, allocation management and the future state of what planning would look like, revealed an instant connection between the two businesses with a lot of commonalities in thought. While the lengthy contracting process was underway, the joke was that FedEx serves 230 markets around the world, almost 90% of the GDP companies of the world, and can be just as big and bureaucratic as the anyone, including when it comes to getting a new software solution approved. But, during that process, the parties were able to work together over several meetings, some very in-depth discussions, testing the software with a lot of questions back and forth. It gave Aerostrat a great chance to understand what FedEx Express was doing and it gave the airline a great chance to learn about better ways of doing things.
Also, FedEx Express found Aerostrat very responsive and adaptable looking at the legacy systems that the airline had and, to some extent, still has. At FedEx Express, Air Operations was the first division to completely migrate away from the green screen main frame systems to internally cloud based systems and the team at Aerostrat were a big part of that. Also, from a security standpoint, Aerostrat has met and exceeded all of the FedEx Information Security requirements, in fact feedback from FedEx’s information security people was that, for an at the time small company, it was surprising how well Aerostrat could handle security matters.
FedEx Express had been looking around the market already, looked at other products but when they met the team at Aerostrat, it seemed to be a better fit with the ability to take on some challenging tasks and FedEx was a significant challenge.
IMPLEMENTING THE NEW SOLUTION
FedEx Express is currently going through four processes (figure 2) in which they’re currently at the enabling output and decision-making stage between ‘Streamlining data flows’ and ‘Enabling Output and decision making’.
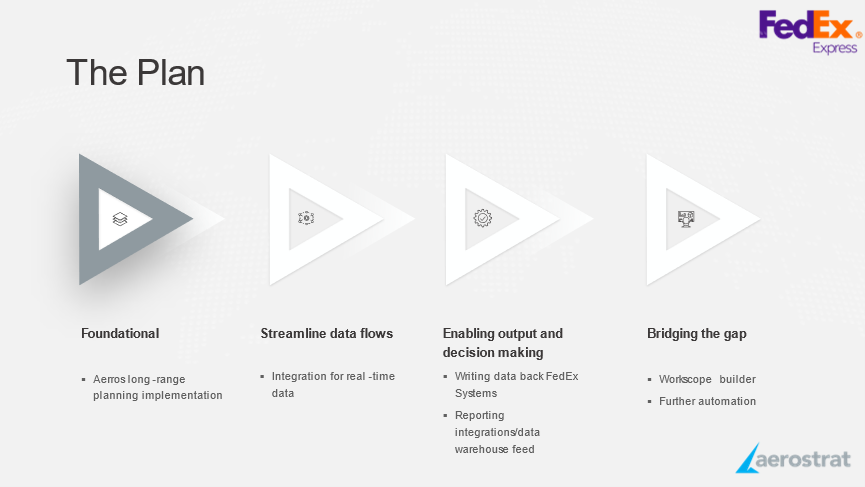
Figure 2
Stage 1
The first stage was ‘Foundational’ (figure 3), bringing the software into FedEx Express, getting it white listed and getting all the communications going.
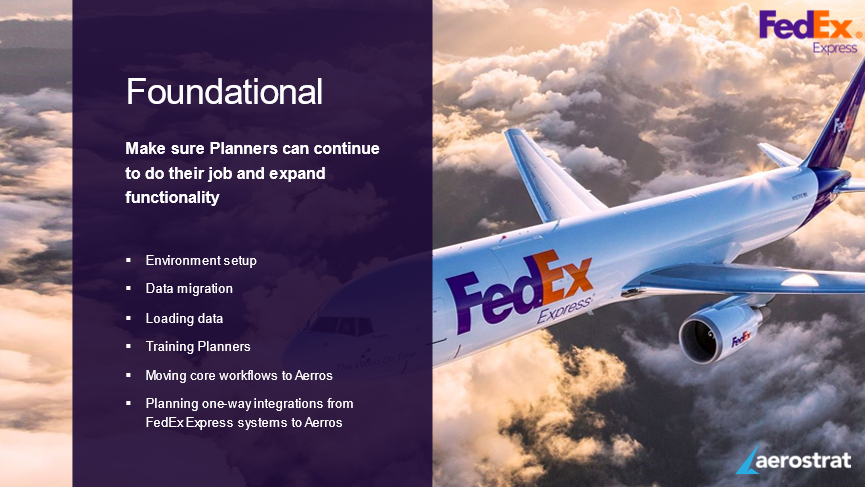
Figure 3
‘Streamlining data flows’ referred to legacy systems: Aerros was turned on at an early stage and some legacy software was turned off. Everybody involved was told about the new software and the go-live date but when the legacy software was turned off there were unexpected issues with some reporting that was dependent on data from the legacy system. This meant that the teams had to step back and re-group to see who was doing what with legacy data. There were some work-around things that had to be done which were fine to get the migration done. The ‘Enabling output and decision making’ stage was well underway at the time of writing. ‘Bridging the gap’ is the part that FedEx Express is really excited about, more of which later.
The foundational stage was about making sure that the planners can continue to do their job and expand functionality (the environment set-up); data migration had to be done, loading a lot of data, and there had to be a training program. At the start, it was all Aerros data going into FedEx Express system with no flow the other way.
With the legacy system a simplistic method of maintenance event planning was employed. When there is a maintenance event that’s about to fall due, there is also the next event that will come due of the same type, everything between those two events gets pulled into that workscope. This was obviously not the best way to do it because there is a tendency to pull things into maintenance events that don’t belong there while not looking at the materials requirements or all of the other issues that go with it.
Integrations and streamlining data flows
Once the foundational efforts had been completed and the planning team had been set-up so that they could at least continue doing their jobs, and while we began to really work on integrations, we began to streamline data flows (figure 4).
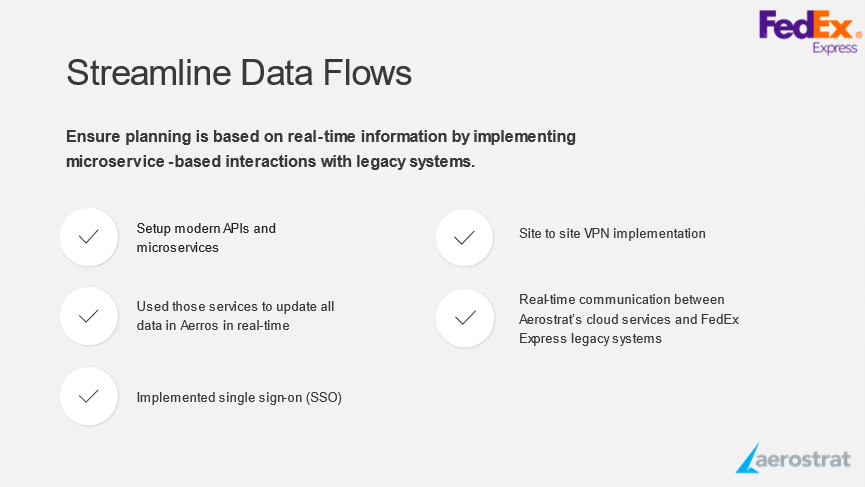
Figure 4
This was a very technical, behind the scenes effort that required a large number of development hours. It began with Aerostrat looking at both systems and, as they were legacy systems, there were no APIs (Application Programming Interfaces) available plus, albeit that Aerros uses a service-based architecture and has over 700 out of the box APIs, none of them was compatible with FedEx Express’s system. Initially, Aerostrat needed to meet with FedEx IT on multiple occasions, then created a plan for both sides to build their own microservices so, that way, both systems could talk. The benefit of this and something that really sets apart the integrations at FedEx Express is that Aerostrat created real-time integrations so that, the moment an aircraft lands that updates in the Aerros system just as it would in FedEx’s internal system. Similarly, the moment a schedule is published, and the five-year plan is available to all stakeholders, it’s possible to update all the necessary data in FedEx’s current legacy systems. So, Aerostrat created a real-time communication but the challenge here was that, while Aerostrat’s Aerros was in the Cloud, the systems at FedEx were all Intranet and locally hosted on FedEx Express’s data centers. In order to talk to them, Aerostrat had to build side-to-side VPN implementations to tunnel through the firewalls and communicate with them in real-time. The other piece for Aerostrat was that they also had to implement SSO using Azure B to C to build the authentication systems both for users, so that every stakeholder at FedEx Express could log-in, but also to securely authenticate with both the VPN and the microservices that had been implemented. By doing all of this, Aerostrat set up an ability and function in conjunction with the foundational side to set up the next phases of the project.
Enabling output and decision making
Key to realizing the objectives that FedEx Express is looking at is syncing FedEx Express’s data to the existing legacy systems (figure 5).
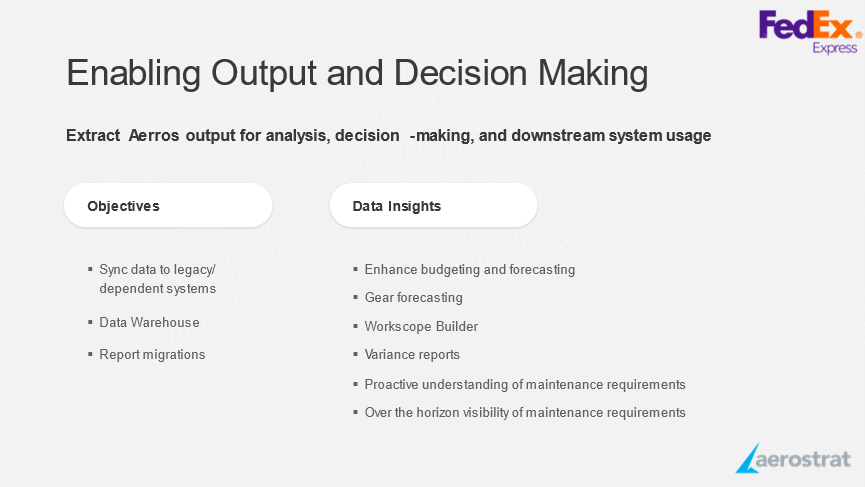
Figure 5
One the major challenges over many years had been that it was always so hard to get data for FedEx’s data warehouse from legacy systems because there had to be someone who could write code to build a report either as an Excel spreadsheet or a printed report. Now, with the new data warehouse, FedEx Express has the ability in real time to make daily updates to the system, extract data and report migration. So, looking to the future, phase three and beyond, is not just the ability to forecast the next scheduled event but, putting in aircraft utilizations, specifications, hours and cycles – date driven things. FedEx Express will be able to project out events into the future and is looking to use that to forecast for multi-year budgeting, allocations such as landing gear forecasts. As an example, FedEx Express took delivery of its Boeing 777 fleet fairly close together with the first fifteen aircraft all arriving within a year and now, the airline is getting into landing gear changes. However, you can’t have fifteen landing gear changes in the triple seven fleet occur within fifteen months because there’s not enough gear available in the supply chain to support that and you can’t have all the aircraft grounded. So, a way had to be figured out to meter those first gear changes and then going forward into the future.
The Work Scope Builder/Planner in the part of Aerros that was being worked with at the time of writing, meant taking the two basic system in which the Workscope Planners work, but within those two systems are multiple screens and tabs. FedEx Express was then in the process of pulling all that into the Aerros product so the Workscope planner is within the one software piece and then that information is sent out to the various systems including FedEx Express’s main forecasting system of record (Workbench) and the Production Control System which manages the work packages that go to the worksites.
Following the completion of that build, the airline moved into training and testing so that it could all go live in Spring of 2023. There were a couple of issues that arose with the go-live including that the purchasing Material Planning organization had been running independently a Landing gear overhaul report that the Aerros implementation team was unaware of. When the old system was turned off, that also turned off their report. But Aerostrat dealt with that and the old legacy system has now been properly turned off. Now, FedEx Express has the ability to generate over-the-horizon views which is also a part of the new system that the airline really likes.
Bridging the gap
Unifying the planning process is an important objective and one of the things that has been discussed at FedEx Express is integrating the materials systems and to have the materials system talking to the planning system and forecasting the engineering authoring document system so that all of these things can be pulled together (figure 6).
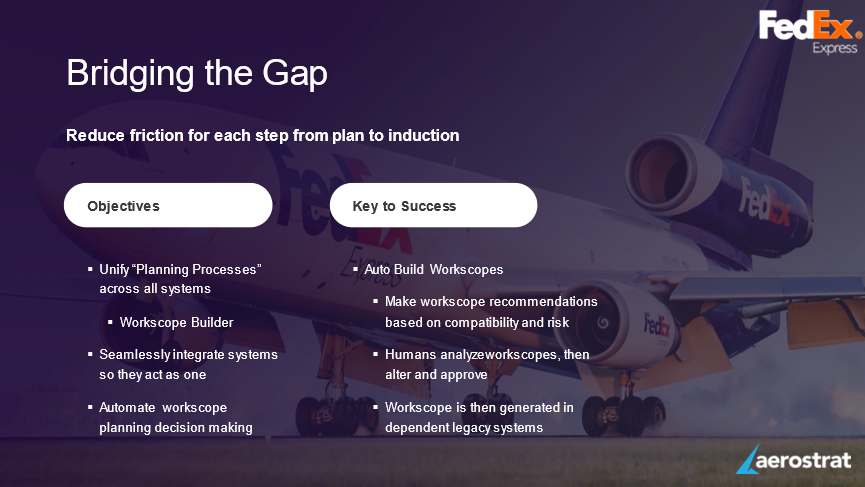
Figure 6
The Work Skill/Scope builder, which FedEx Express finds really exciting, is taking the process that s being done now, and beginning to automate that. So, one scheduled maintenance event is and a new event starts, the forecast is a B Check or a C Check and the plan is for Aerros to query the old forecasting system and begin to bring things in as it builds Work Scopes in advance with the idea being that, by the time that the aircraft is ready, two weeks to 45 days prior to induction, the planner would review what Aerros has suggested, either agree or disagree, and makes changes. Along with that, FedEx Express has to make sure that the right work is scheduled at the right event. For example, you wouldn’t want a pylon removal to be done during a 24-hour check; that needs to be planned well ahead.
of the FedEx Express Maintenance Planning & Scheduling organization who have been involved in this at various levels of planning, using a Safety Risk Assessment (SRA) methodology, developed a Technical Risk Assessment with considerations such as, ‘does the aircraft require tanks to be opened’, ‘flight control surface removals’, then developed a severity listing of it so that when Aerros is enquiring what to put where, there’ll be some intelligence built-in to allow it to assign the right task to the right type of event. That’s also something which FedEx Express is looking forward to having.
LOOKING TO THE FUTURE
Looking even further ahead, FedEx Express is looking at simulation software, multi-year planning windows, even life-cycle planning. Also under consideration is a capacity and demand system for the whole maintenance system, how that could be built? So far, they’ve come up with simulation software because once there’s a basic forecast for the next C Check cycle, that be built our, requirements changed to allow for more or less aircraft, flying.
With that, let’s take a look at the Aerros system and what it will look like when the FedEx Express project is complete (figure 7).
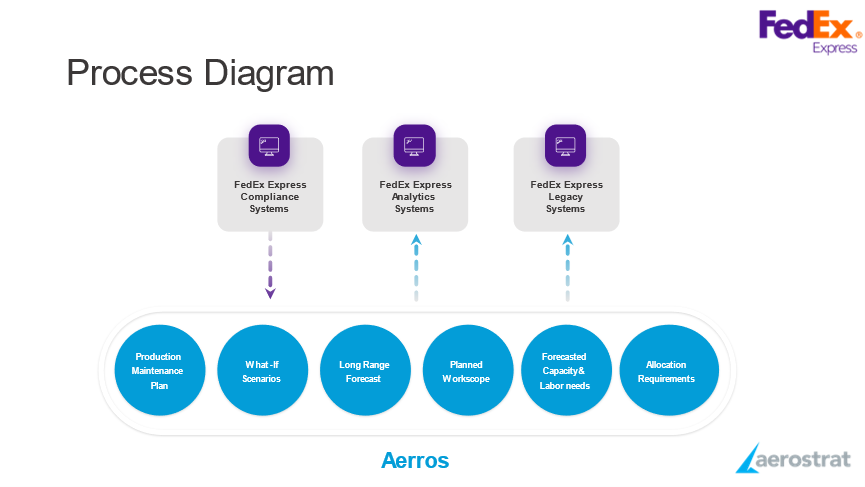
Figure 7
Currently, Aerros is importing data from FedEx Express’s legacy compliance system to help the long-range planning team build their heavy maintenance plans; using this data to feed the long-range forecast, to set up their scenarios and, once those decisions have been made, publishing to all stakeholders. Further than that, the airline is also using the data to build their Work Scopes for which purpose, Aerostrat is building a customized Work Scope Building tool. The users will also take that data and feed it into other FedEx systems.
There are two pieces to this. One is a variety of different legacy systems, including the compliance system. The other one is the various analytics systems, including the data warehouse as well as the simulation systems. All of that Aerros data is being taken to provide the forecasts, the information and the actual plans that FedEx Express needs and then using that to update all the dependent systems that exist in the business today.
Looking forward, FedEx Express and Aerostrat want to continue to bridge the gap between long-range planning and production planning (figure 8).
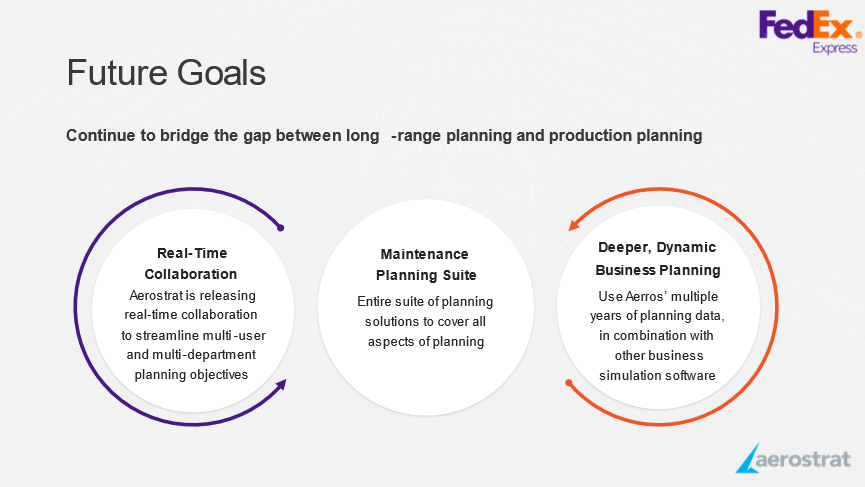
Figure 8
Aerostrat is working on two big endeavors with FedEx Express input. The first is a real-time collaboration tool within Aerros. It will be a huge advancement, especially for larger carriers such as FedEx because of what it will enable planners to do. With real-time collaboration, planners will be able to see what the others are doing live. So, for example, on a scenario, they’ll each be able to see, regardless of individual geographical locations, which event they’re editing – as they drag and drop events, update work scopes, etc. The other thing on which Aerostrat is working with FedEx’s input is a maintenance planning suite initially focusing on Heavy maintenance but to include a power plant planning tool and a line planning tool.
Finally, FedEx Express is working towards using the data to support deeper dynamic business planning covering things like maintenance allocation management, very important. The plan is also to make data available to other areas of the company such as finance because the data is in the information factory and is available for business planning, costing for the various levels and types of work scheduled for the year. Plus, the airline wants to know where are the traps, the over-the-horizon view. For instance, with the triple seven gear changes, if there was no way, other than intuitively, to know what was coming up, that wouldn’t be most efficient. If there is a tool that allows you to see that over-the-horizon view, then you can see where things might go wrong because one thing that maintenance planning is pretty good at is telling people that they have a problem and even when it will manifest itself; now, everybody can see what is happening and that there will be that problem at that time.
Ends…
Contributor’s Details
Roger Hutcinson II
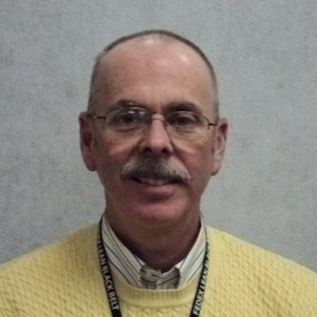
Roger started his career as a Helicopter Mechanic, he has worked as a Hangar Mechanic, a Logistic Support Analyst and in several managerial positions at FedEx Express, currently in Strategic Maintenance Planning. Roger holds an FAA Airframe & Powerplant and Private Pilot’s license. Roger has a BS in Aviation Management from Southern Illinois University and a MBA from Embry-Riddle Aeronautical University.
Elliot Margul
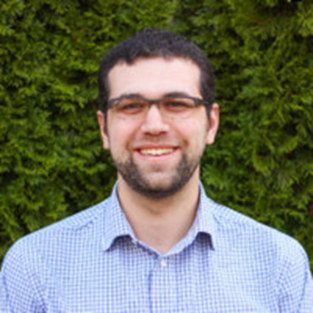
Elliot co-founded Aerostrat seven years ago. He began his career as a Reporting Analyst and later moved into Financial Planning & Analysis and founded Aerostrat to create modern planning and maintenance tools for Aerospace and Defense. Today, Elliot manages the business side of operations and develops Aerostrat’s product and corporate strategy. He has a BBA in Business from the University of Washington.
FedEx Express
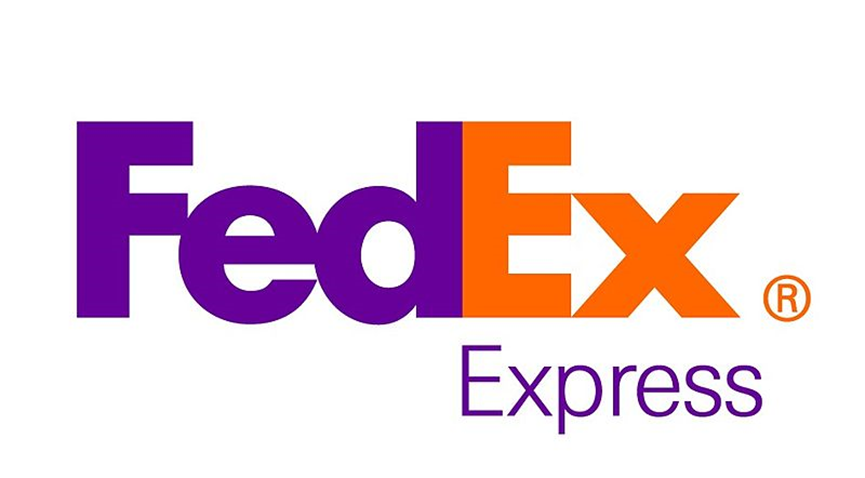
FedEx Express, a subsidiary of FedEx Corporation, is a major American cargo airline and one of the world’s largest airlines in terms of fleet size and freight tons flown, delivering to more than 375 destinations over 220 countries across six continents each day. There are a total of 13 air hubs in the company’s worldwide network. The fleet of 285 aircraft ranges from Cessna 408 SkyCourier up to Boeing 777 and Airbus A300 types.
Aerostrat
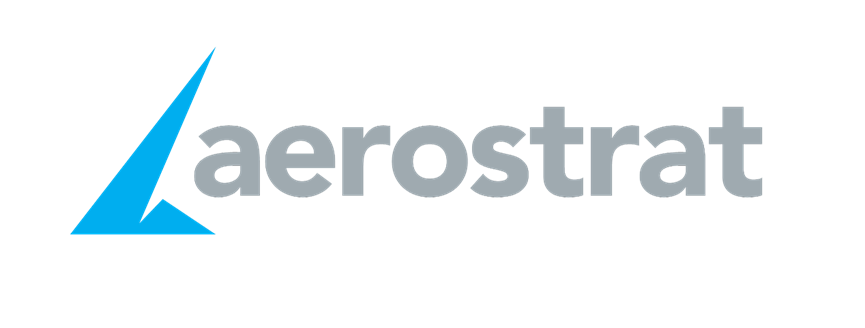
Aerostrat offers one product called Aerros, a program that manages an airline’s or MRO’s aircraft maintenance schedule and enables users to optimize the maintenance program by managing various maintenance and operational constraints; maximizing event yield, driving costs down, and enabling the organization to plan proactively, not reactively. Aerros provides excellent system stability and reliability with standard IT practices. It is also integration-ready and designed to work as an extension of a user’s existing information systems.
Comments (0)
There are currently no comments about this article.
To post a comment, please login or subscribe.