Articles
Name | Author | |
---|---|---|
CASE STUDY: A new solution for fuel efficiency at Viva Aerobus | Paola Cavazos, Operations Engineering Manager – VIVA AEROBUS and François Chazelle, Head of Sales Support, Flight Efficiency, SITA FOR AIRCRAFT | View article |
CASE STUDY: FDM data key to easyJet’s flight efficiency | Taylor Bradbury, ETS Manager, easyJet | View article |
CASE STUDY: Flight efficiency at airBaltic: past, present, and future | Rihards Kārlis Eizentāls, Flight Operations Digital Solutions Manager, airBaltic | View article |
CASE STUDY: KLM implemented a new airports and obstacles database | René Dijkema, Flight operations Engineer, KLM and Bruno Ramioulle, Partner, ACFTPERFO | View article |
CASE STUDY: End to End digital document management leveraging Vistair’s DocuNet is transforming Vueling’s Flight Operations | Mar Albaladejo Mans, Flight ops projects, manuals and operational supervision manager and Xavier Merencio Espar, EFB administrator and Flight ops projects engineer, both at Vueling | View article |
CASE STUDY: Flight efficiency at airBaltic: past, present, and future
Author: Rihards Kārlis Eizentāls, Flight Operations Digital Solutions Manager, airBaltic
Subscribe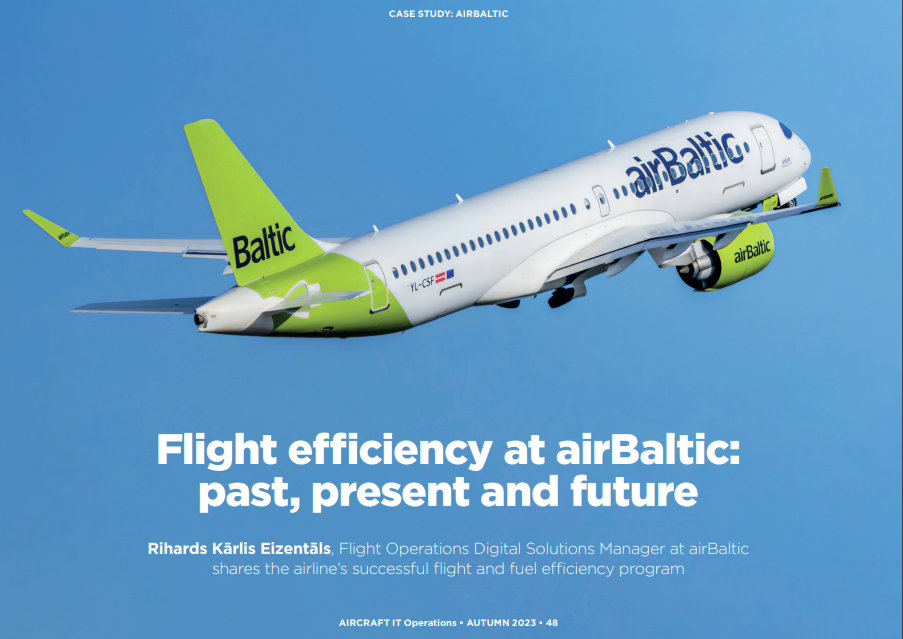
Rihards Kārlis Eizentāls, Flight Operations Digital Solutions Manager at airBaltic shares the airline’s successful flight and fuel efficiency program
As with any Case Study, it will help the readers to better understand what happened and what it achieved if they first understand something about the airline whose case is the subject of the study. So, here is a brief ‘tour’ around airBaltic.
AIR BALTIC
The airline was founded in 1995 and operates out of four hubs at Riga, Vilnius, Tallinn and Tampere (figure 1). Additionally, we also do ACMI operations for various European airlines.
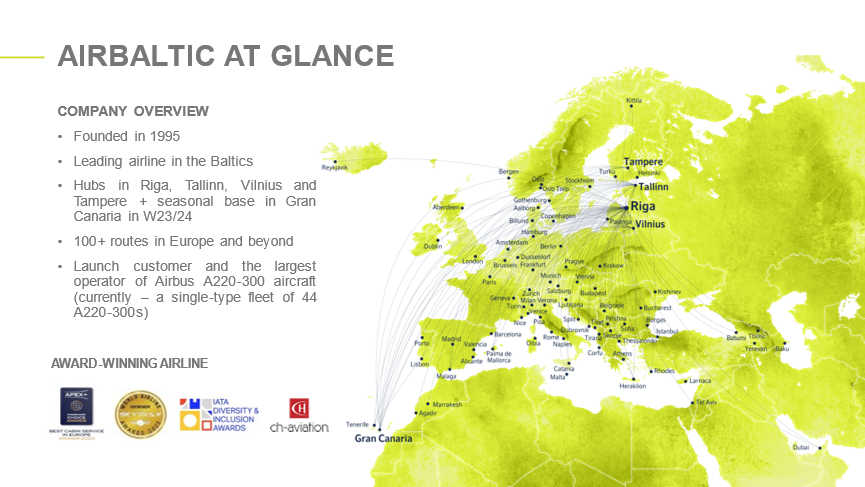
Figure 1
We perform flights on more than 100 routes from the Baltics to Europe and beyond, and are the launch customer of the Airbus A220-300 aircraft. With 44 aircraft of the type, we are also the largest operator at the time of writing. airBaltic’s fleet is also among the youngest aircraft fleets in Europe.
Furthermore, airBaltic has won a number of international awards – 2023 APEX award for the Best Cabin Service in Europe, the Skytrax award for being the best airline in the region, and the IATA Diversity and Inclusion Team Award 2022, recognizing airBaltic’s efforts in increasing gender balance within the industry. Furthermore, ch-aviation has named the airBaltic’s single-type fleet of Airbus A220-300s among the youngest aircraft fleets in Europe for several years now.
FUEL MANAGEMENT IN THE PAST
The Fuel Efficiency program at airBaltic was established in 2009. The program introduced APM, APU Usage monitoring, single-engine taxi, AMBER (Arrival Modernization for Better Efficiency in Riga) arrivals and many more saving initiatives resulting in EUR 4.3m saved in the first year of Fuel Efficiency program being in place.
Although the Fuel Efficiency program was in place, the company still had challenges that needed to be solved to achieve the expected results. Prior to me joining the company in 2017, the airline faced a number of challenges relating to usage of fuel efficiency tools and instructions available and given to pilots:
- There were efficiency guidelines being provided to pilots, however, they sometimes were general and not fine-tuned to specific aircraft;
- There were non-customized statistical data and reports being provided to pilots but only at fleet level;
- Existing KPIs were not being enforced and new KPIs not being introduced at a sufficiently fast pace;
- There was no Feedback Loop in place;
- There was limited use of Fuel Efficiency Software inasmuch as we used the Honeywell solution but not to any significant degree and it was not available for pilots and dispatchers. It was just used by the back-office team to analyze flight data.
So, there was still room for a lot of improvements. (figure 2).
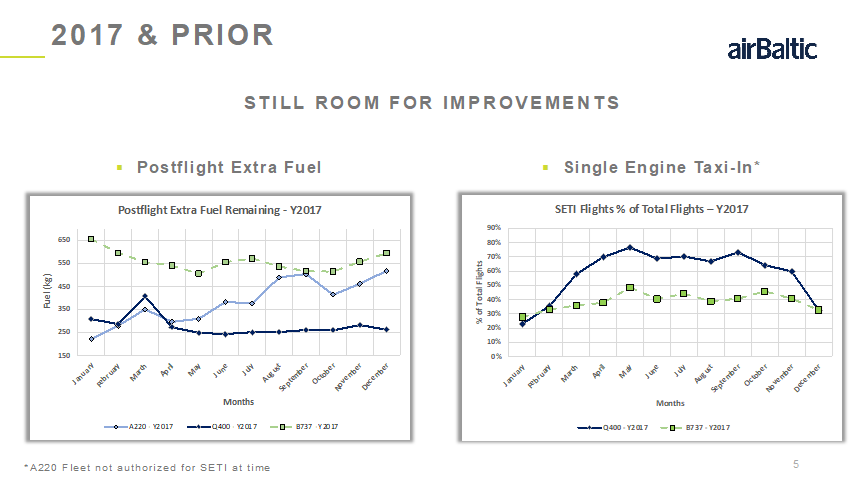
Figure 2
In figure 2, the statistics for 2017, show that pilots were not made aware of the possible savings and inputs required. The graphs were quite flat, and ‘extra fuel’ was even increasing on the A220 fleet. The same was true for single engine Taxi-in flights – at the time, the A220 was not authorized for that but, as you can see on the Boeing 737 fleet, it did not change with the season, it is always the same because there were only a small group of pilots that did it.
The same was true for Idle Reverse (figure 3).
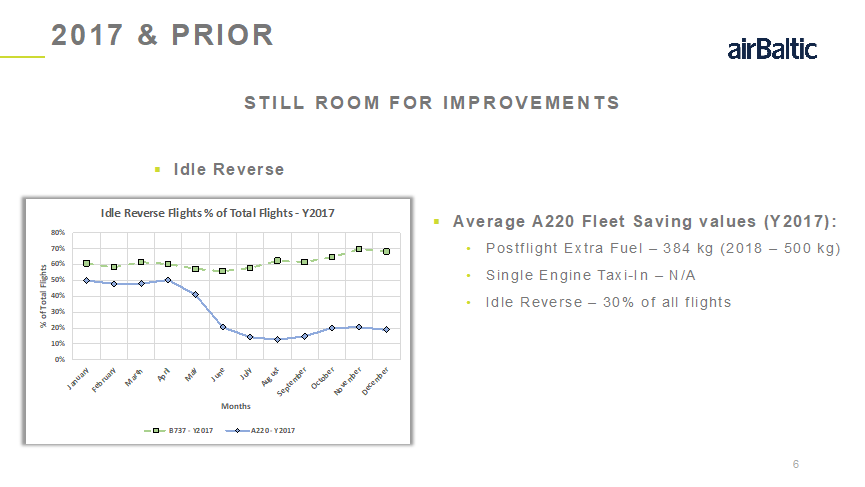
Figure 3
On the 737s, the result was good as it had been in use with airline for many years, but on the A220, it could have still been improved. There are, of course, times when idle reverse would not be appropriate – such as on a slippery runway in heavy rain. Also, you can see that the average value of post-flight extra fuel was 384kg but it increased in 2018 to 500kg.
FUEL MANAGEMENT IN THE PRESENT
Shortly after joining airBaltic, I arranged a meeting with the chief pilots of all fleets, and we discussed the steps that would need to be taken in order to improve the fuel management situation. For that, we set goals and made changes to achieve improved results.
We defined clear flight efficiency goals, including 75% or more pilot adherence to fuel-saving initiatives and that post-flight extra fuel should be less than 300kg on A220 and Boeing 737s and less on the Q400 fleet.
Efficiency guidelines and training began to be provided to pilots at every opportunity and new pilots joining the company were also given efficiency training on their first day with airBaltic.
We created customized and individual statistical data reports provided to each of the pilots, plus KPIs were being enforced and new KPIs were being introduced. Similar reports and dashboards were created for dispatchers. We were careful to ensure two-way communication, including meeting with pilots to talk about efficiency, and setting up dedicated channels such as email and other methods. Part of this was for us to explain the importance of fuel efficiency software, with which they would not only be producing savings for the company but the savings made during the flight could be used for an emergency. It was also a benefit for pilots do their job even better.
In 2019, we revised the existing pilot reports, which had first been released in 2018 (figure 4).
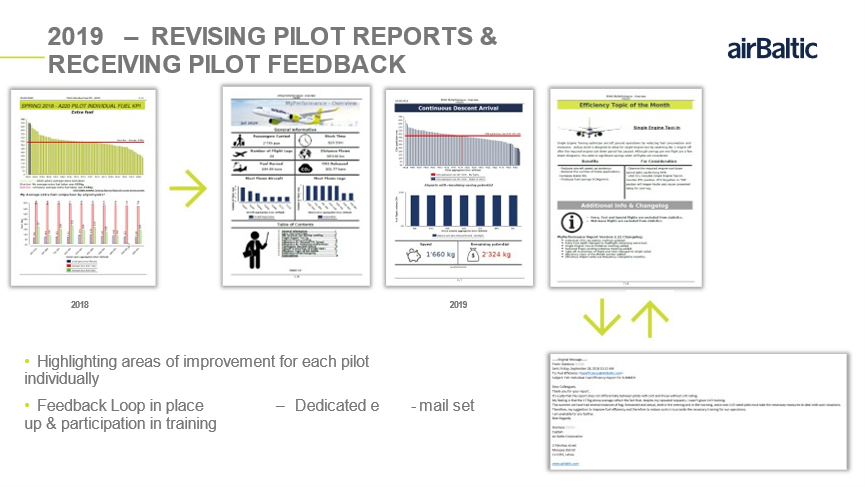
Figure 4
On the left, you can see the old report, which showed pilots their own position compared to others in terms of post-flight extra fuel. Here we have a graph, which shows extra fuel taken and used, and the statistical contingency fuel on that flight. We wanted to show pilots how much extra fuel they were taking but were not using in order for us to drive the change.
Furthermore, to make the pilots more interested in the topics, we did some research on colors to use and data that might be interesting to pilots – such as numbers of passengers carried, distance flown, and more. These were the new reports introduced in 2019 (see above) with a table of contents and with every page focusing on an initiative. Every month, at the end of the report, we added the efficiency topic of the month, explained the importance of this and, by using the communications channels that we had established (see above), we received feedback from pilots about matters like procedures and training reports. This led us to make a lot of adjustments. In the first email we received, a pilot said that he was missing the target in the category because of reduced visibility operations, which was why he was taking extra fuel. So, we were able then to address that with training.
Our next step was working with Honeywell to refine the statistical contingency fuel statistics (figure 5).
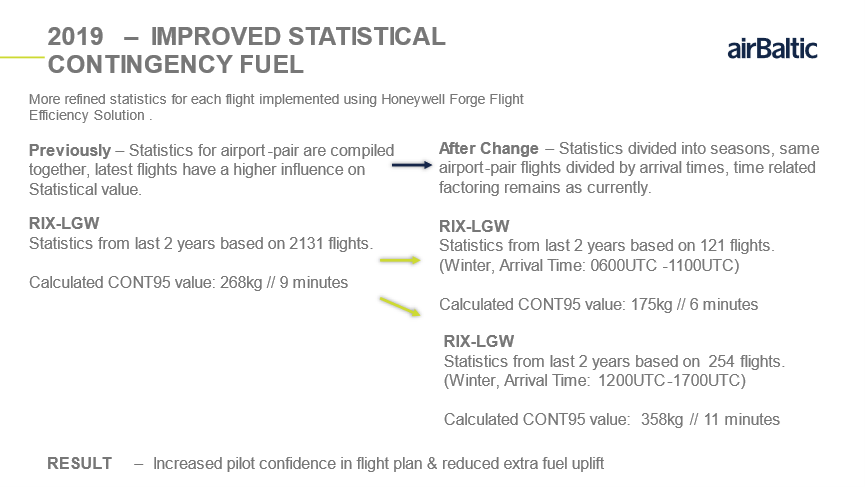
Figure 5
Previously, we had compiled statistics for airport pairs with the latest flights having a greater influence on statistical value. In the example, we had put together all the Riga-London Gatwick statistics with no differentiation according to arrival times or season. As a result, we got a value, which was inadequate – insufficient for one flight, inefficient for the other. Using Honeywell Flight Efficiency System, we were able to add additional parameters that improve the calculation for each flight by taking into account seasons and arrival times. The changes were made, resulting in improved flight plan reliability and efficiency. The change increased pilot confidence in the flight plan and reduced the levels of extra fuel uplift. It is important that pilots have confidence in the data given to them.
In 2020, airBaltic moved to an all A220 fleet earlier than expected. It enabled the airline to operate the most efficient aircraft available, and to benefit from the efficiency of only having to develop procedures for a single aircraft type. The A220 is built from scratch with engines that are more efficient, providing a number of benefits (figure 6).
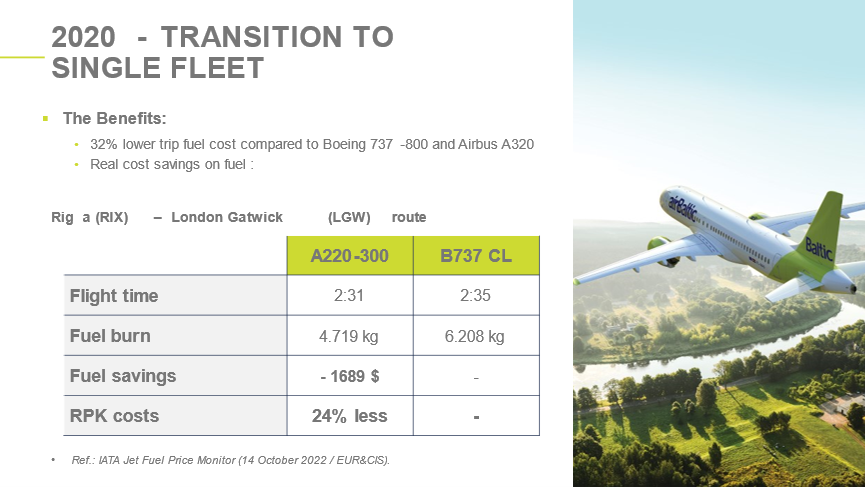
Figure 6
A220 trip fuel costs are 32% lower compared to Boeing 737-800 or Airbus A320. This change has allowed airBaltic to improve sustainability and move closer to our goals (figure 7).
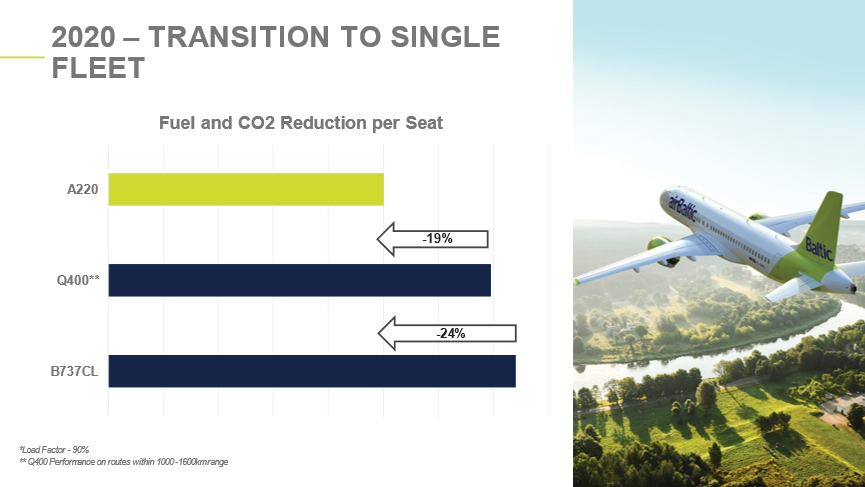
Figure 7
The figure shows a comparison with our previous fleets. As you can see, the A220 is more efficient than to the Q400 and the B737 classics that we operated previously.
The pandemic time meant reduced demand for training. As a result, we were able to utilize the A220 full-flight simulator for efficiency testing purposes (figure 8).
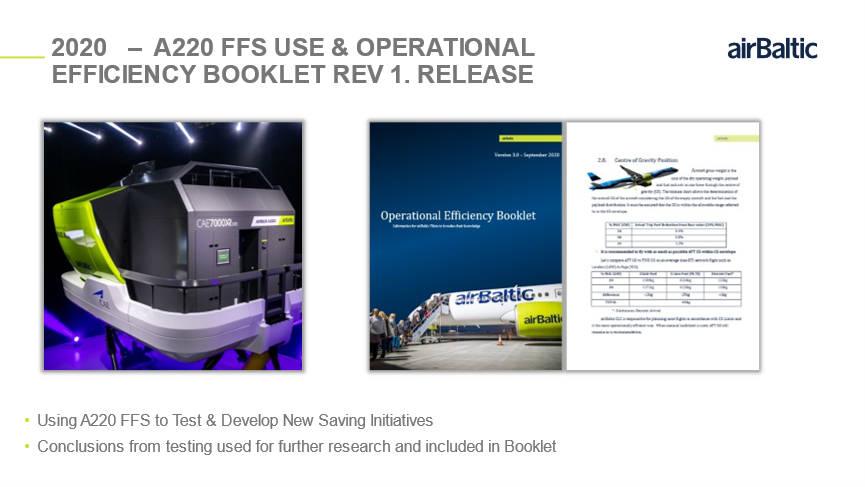
Figure 8
We used the simulator eight or ten times during that year to test various initiatives to see what would or would not work, how could we adapt them to the aircraft systems but with all the testing taking place in a safe and controlled environment. The knowledge gained enabled us to release our Operational Efficiency Booklet, which covers a number of topics. For example, in the figure is the impact of center of gravity; pilots can look at the data and it is explained to them plus, if they’re still not clear, they can contact us to further clarify it.
In 2021, one of the biggest projects undertaken by the airline was introducing RNP AR (Required Navigation Performance – Authorization Required) arrivals, as well as satellite-based navigation instead of ground-based. It enabled us to reduce distance and noise as well as to create further fuel savings and CO2 emissions reductions. Based on this, airBaltic, with the local air traffic services provider, created new procedures, and the airline trialed them before they were released to other operators flying into Riga (figure 9).
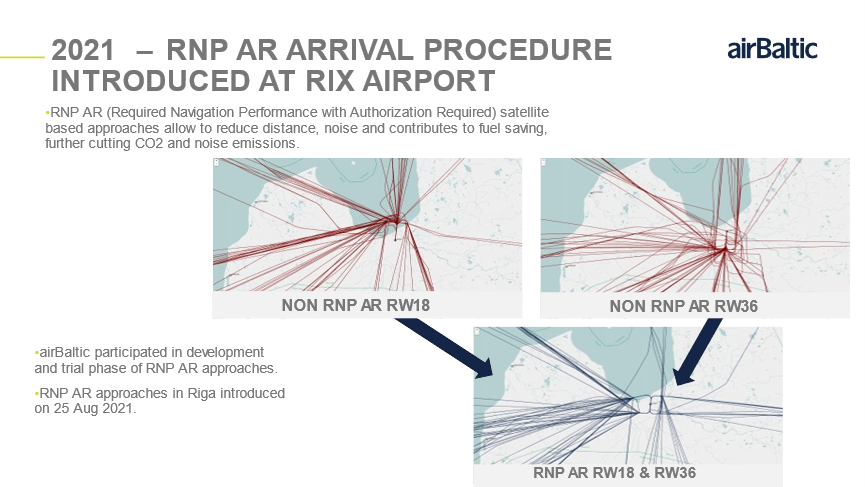
Figure 9
The top two maps show pre-RNP AR arrival routings for runways 18 and 36 and by vectoring aircraft around Riga in lengthy patterns, they were no good for fuel efficiency. With the new procedures (bottom graph), the aim was to reduce track miles with fuel efficiency savings as a result. Based on a data analysis that we undertook, each approach generated approximately 50kg in fuel savings from top of descent to landing. The direct impact is approximately 25 kg and using continuous descent and reduced distance adds additional 25kg to the savings. This also enables us to reduce CO2 plus the financial savings are substantial.
There has also been a positive impact with regard to noise levels with the RNP AR arrival procedures generating less noise around the airport. One thing not related to RNP AR is that we were initially researching capabilities to reduce acceleration altitudes to save some fuel but this research led to us increasing that altitude from 1500ft to 3000ft. It is not so much a flight efficiency improvement as a sustainability measure for communities living around the airport.
We used Honeywell GoDirect Flight Efficiency software to come to the conclusions.
We determined the savings achieved by using the entities list on the portal and analyzing the non-RNP AR and RNP-AR approach data in Power BI afterwards. We were trying to get the flights to match as closely as possible, so that meant including filters such as that top of descent should not be lower than FL280, because we noticed that, if it’s higher or at this level, the savings difference is negligible. We also applied a flaps position filter which equals to ‘FLAP 4’ setting or standard flaps to avoid saving differences created by different aircraft configurations. As a matter of fact, we do not track reduced flaps take-off and landing because we have a performance application, which selects the most optimal value based on external factors. But if we were to look at the data in Honeywell Forge, we would see that 95% of flights are using the most efficient flaps as it is already rooted in the pre-flight process.
Afterwards, we analyzed the data. An important thing to do is actually look at the data for many dates and data points, and you can see that the savings are quite consistent with various factors – such as weather impacting each day’s average fuel consumption (figure 10).
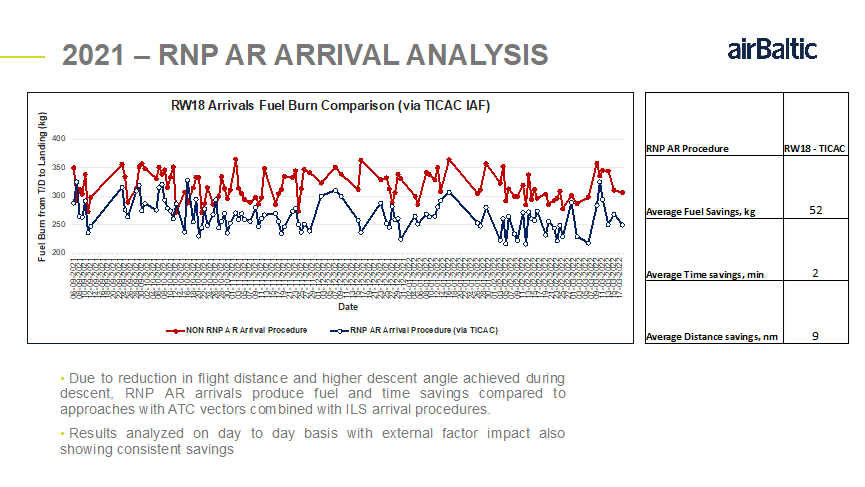
Figure 10
On the graph, the red line is for regular procedures leading to ILS (Instrument Landing System) while the blue line is for RNP AR with that initial specific approach fix. In addition to fuel savings, RNP AR also produced time savings of about two minutes per arrival.
PROGRESS SO FAR
At the time of writing, we were working on several projects to continue our fuel efficiency program (figure 11).
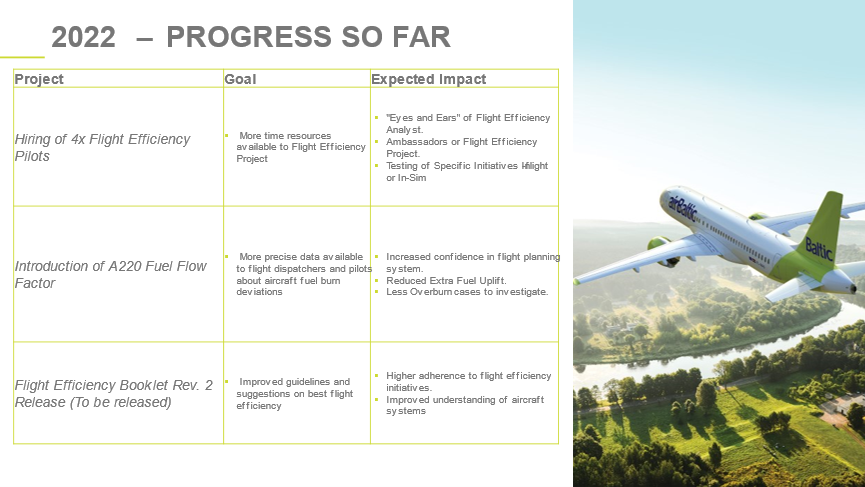
Figure 11
We added additional duties for four flight efficiency pilots because we needed more resources to work on the flight efficiency project. They are also the eyes and ears of flight efficiency analysts – what we cannot see in the data, they can tell us by contacting us, and that is really important. They are also ambassadors for flight efficiency.
The second project was introducing the A220 Fuel Flow Factor, which has meant more precise data being available to pilots and flight dispatchers to make them more aware of fuel burn deviations highlighting. This also led to fewer overburn cases to investigate, which reduced our workload.
Last but not least, was the Flight Efficiency booklet (see figure 8 and copy) issue 2, which we were planning to release and in which there had been further inputs by the flight efficiency pilots. We expected it to support higher levels of adherence to flight efficiency initiatives and encourage an improved understanding of the aircraft’s systems.
IMPROVED RESULTS
With all of the hard work already invested, we have seen an improvement in results (figure 12).
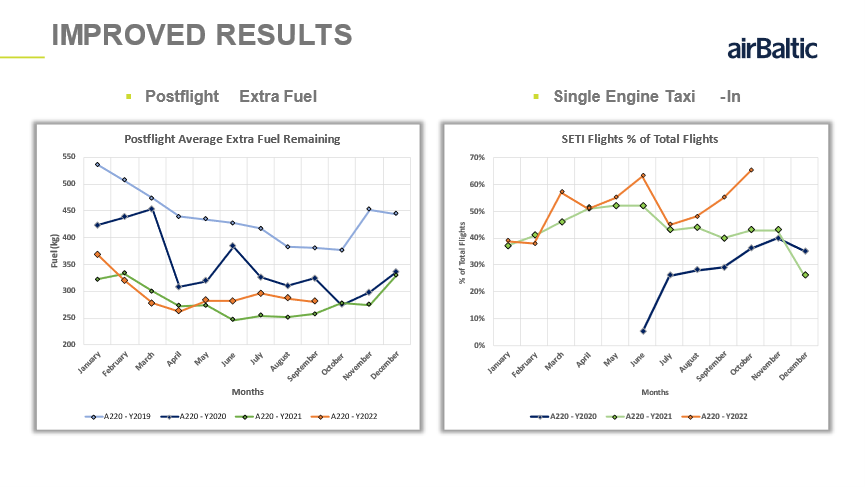
Figure 12
Here you can see the efficiencies that we have covered above, post-flight and single engine taxi-in, and levels of adherence to them. As we can see, in 2019, post-flight average extra fuel remaining was declining with further decline in 2020. In 2021 and 2022, you can see that airBaltic was meeting the goal of 300kg or less but there was an increase towards the end of 2021. That was because, after the pandemic, we appointed a lot of new pilots and there was line training for them when they needed more extra fuel. The same goes for single engine taxi-in numbers, which were improving – previously, adherence had been really low, whereas now it is constantly increasing. And it is the same again for idle-reverse flights (figure 13).
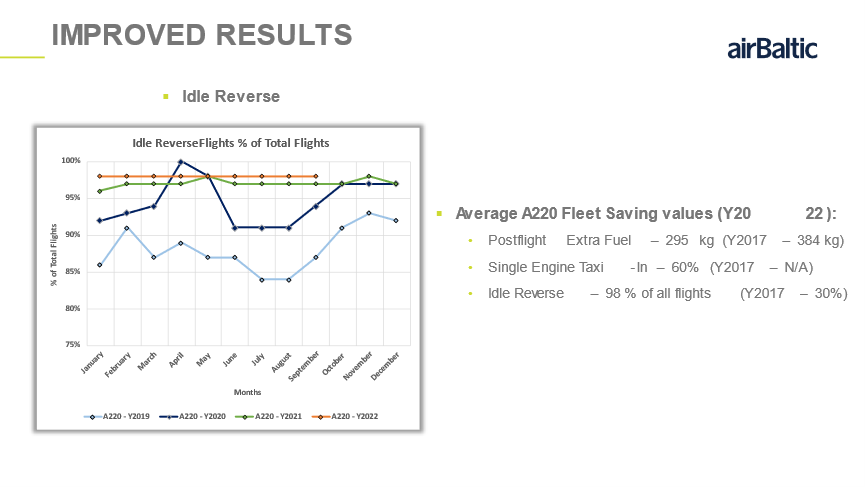
Figure 13
After making this a standard operating procedure (SOP), we have seen it used on 98 % of flights. That said, one important note is that we provide all this as guidance to pilots, it is not that they are expected to do it on every flight as per environment and conditions surrounding the flight.
WHAT THE FUTURE HOLDS
In the short term, we are looking forward to the introduction by Honeywell of Pilot Connect Mobile Application. As we have seen, the interactive experience will further drive efficiency results.
Moving on to mid-term, we are researching a concept called GPU to GPU with the idea that we can reduce APU use as much as possible. During the pandemic, we wanted to do the right thing and have the APU on as much as possible to maintain fresh air flow in the cabin. By doing the GPU to GPU project, first at our home base in Riga, we are trying to ensure that pilots do not use any APU at all and get connected to GPU right away to reduce fuel burn and emissions.
In the long-term, we continue to work on sustainable aviation practices, increasing SAF (Sustainable Aviation Fuel) uplift, and researching electric/hydrogen aircraft propulsion.
SUMMARY
Here are five key takeaways from my own experience as a fuel efficiency analyst.
- Ensure guidance
- Do not overcomplicate it because efficiency is only one of a pilot’s priorities;
- Based on this, you should adapt the information accordingly and, as a final measure, make efficiency part of SOPs, it should not be a side project.
- Use all the tools available
- A Full Flight Simulator is a great place to test theory in practice;
- Using Honeywell Forge we are able to fine-tune initiatives to adapt to real-world challenges
- Involve and work together with pilots
- You need to understand that the data does not always paint the full picture, which is why you need to have eyes and ears among the pilots.
- Do not stop or be discouraged
- We undertake a lot of case studies and work on this topic, and not every case study will lead to the implementation of a new efficiency initiative. Do not give up or stop trying.
- See the bigger picture
- It is not about fuel efficiency now; it is about flight efficiency. Sometimes flying at a non-optimal cost index for that specific flight could save the schedule and actually reduce the overall expenses and total fuel and CO2 emissions for the company.
This has been our journey to flight and fuel efficiency at airBaltic so far. We are pleased with these achievements so far and will continue to work towards out goals. This is not a one-off project – it is an important element in the good management of our business.
Contributor’s Details
Rihards Kārlis Eizentāls
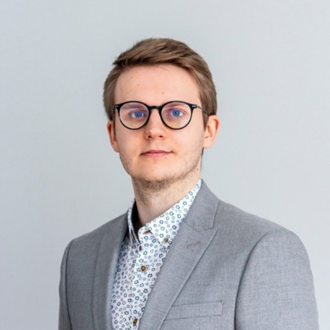
Rihards, who joined airBaltic in 2016 as Fuel Efficiency Analyst, has a proven track record of boosting flight efficiency through research, project implementation, and training. He is passionate about sustainability, with experience in analyzing sustainable aviation fuel usability and performing cost-benefit analysis for airline projects. As Flight Operations Digital Solutions Manager at airBaltic since 2021, Rihards is driven to achieve growth and development of the aviation sector with the use of new technologies and digitalization.
airBaltic
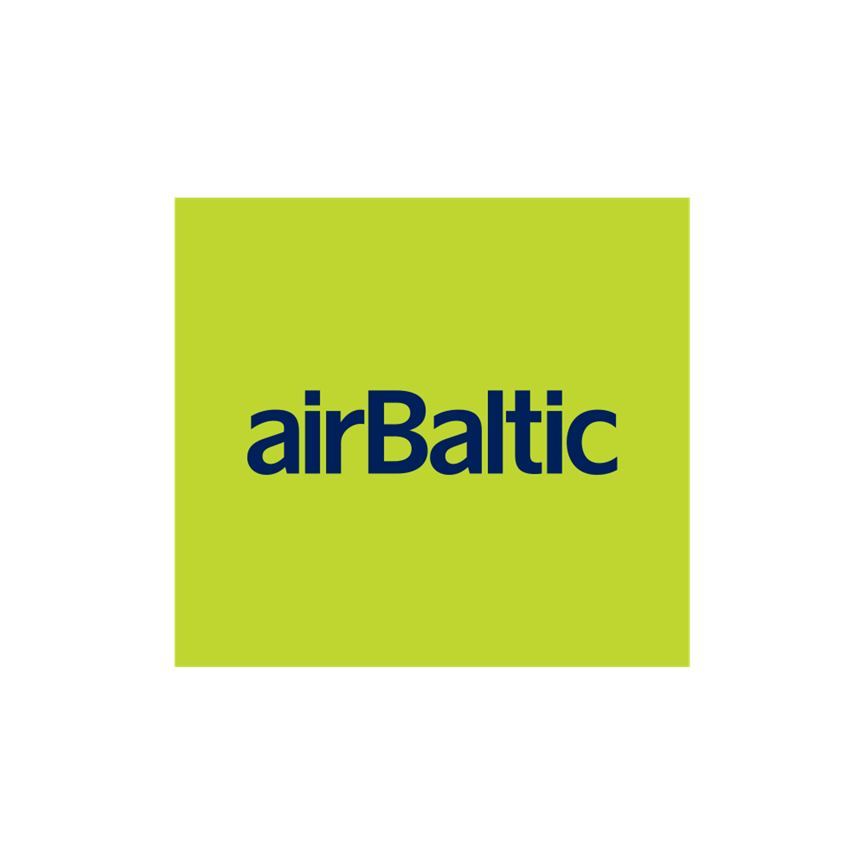
The Latvian national airline airBaltic offers connections to more than 70 destinations in Europe, the Middle East, North Africa and Caucasus region. Over the last 28 years, airBaltic has developed as a strong and internationally respected airline, which employs more than 2 400 employees. The airBaltic fleet consists of 44 Airbus A220-300 aircraft, making it one of the youngest fleets in Europe. The airline has received several international awards for excellence, innovative services and significant achievements. Skytrax has awarded airBaltic two years in a row as the best airline in its region. Additionally, in 2022, the International Air Transport Association (IATA) awarded airBaltic the Diversity and Inclusion Team Award. In 2023 the airline received the APEX Passenger Choice Award of Best Cabin Service in Europe.
Honeywell Aerospace
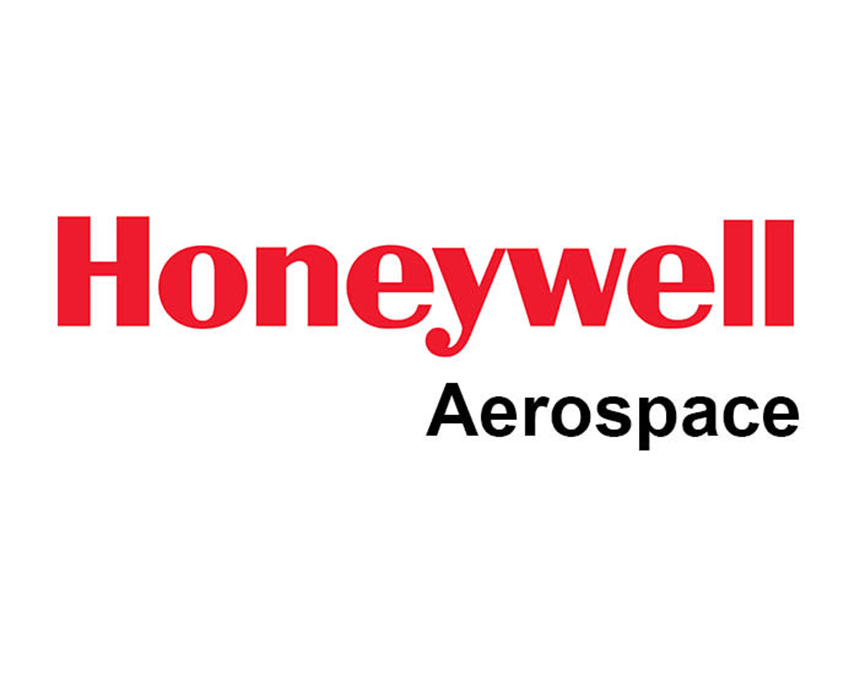
Honeywell Flight Efficiency is an advanced fuel efficiency and airline data analytics solution. More aircraft rely on Honeywell Flight Efficiency to improve flight efficiency and reduce carbon emissions than any other solution. The software connects stakeholders across the organization to provide a unified source of truth for all operations-related data. Honeywell’s advanced analytics help users to uncover the hidden potential. Even airlines with mature and sophisticated fuel-efficiency programs have unlocked significant additional savings by implementing Honeywell Flight Efficiency.
Comments (0)
There are currently no comments about this article.
To post a comment, please login or subscribe.