Articles
Name | Author | |
---|---|---|
CASE STUDY: Smartwings journey to a more effective digital supply chain | Petr Barton, Head of Logistics & Stores, Smartwings | View article |
CASE STUDY: Cargolux & TRAX eMOBILITY Q&A Part 2 | Stephane Kastler, Director of Maintenance & Production, Cargolux | View article |
WHITE PAPER: Technologies for a promising future | Rob Mather, Vice President, Aerospace and Defence Industries, IFS | View article |
CASE STUDY: Rolls-Royce and QOCO; working together for PLM | Nick Ward, Head of Product Management for Digital Services, Civil Aerospace at Rolls-Royce | View article |
CASE STUDY: Cargolux & TRAX eMOBILITY Q&A Part 2
Author: Stephane Kastler, Director of Maintenance & Production, Cargolux
SubscribeStephane Kastler, Director of Maintenance & Production, Cargolux, demonstrates the Shop Control Application and how the application works in the MRO environment.
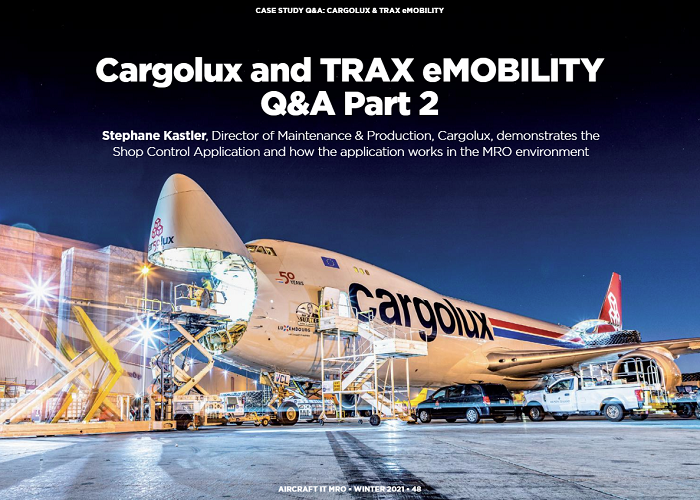
In the first part of this article Stephane explained to AircraftIT how the Shop Control Application came about, what factors were germane to it and how it was implemented in Cargolux. In Part 2, he goes through a demonstration of the Shop Control Application for readers to learn how the application works in the MRO environment.
What you see in the video is our Shop Control application and what is specifically in front of you right now this is what we call the backlog of parts. We are now controlling the induction of parts into the shop, so we don’t just send everything to the shop because the shop would become congested on that. We have a backlog area where the parts are coming in and waiting for the right time to be released to the shop.
It’s almost identical to software for hospital emergency room management, where you come in as a patient and you’re going to be reviewed by a nurse who will classify you as a serious case or normal case. According to this you’re going to be moved to the doctor’s office or waiting room, as opposed to the process we had before would have sent every patient straight to the doctor’s office. Obviously, that wouldn’t work. The doctor needs to focus on their job and see the right patient at the right time.
What you see here is this backlog area where the parts are waiting to get assigned to a repair order. What we have done with Trax here is very efficient because the parts are not classified by the time they came in or by the time they are waiting here, they are just classified by their priority and that priority is compiled here.
It’s a calculation that we put together with TRAX, based on the utilization of that part, the number of parts that we have currently in stock, the number of parts we have currently in repair, and when these parts are going to make it or not, or whether they’re going to have to be on hold for a reason. Based on that, the system is constantly calculating what is the next part that should be put into the shop, from top to bottom.
The page is quite intuitive. You see your part and where you currently stand with your stock. You see these parts in red, they are currently standing at zero stock, so we know we have an immediate problem with these parts.
If the parts are in stock, we are able to immediately see where they are and what are the quantities. This is a very easy way to get information and then you are able to see what is happening for the parts which are currently in repair: e.g., are they on hold? do I have some open requirements for that part? did somebody order that part? and when is that part needed?
This is what this page is showing, so it’s a very useful tool for the shop control planner. That’s what Cargolux is putting in place right now, we will have a shop control center with shop control planners in there and the shop control planner will use that list and say, “look; my shop can take one more part and that’s the right part to send them right now”.
We included a manual aspect to it as well, in case the planner needs to make a manual interaction when he finds that a part which is not presented to him as high priority is now actually high priority (this happens a lot). Somebody comes from planning and says “hey, watch out, I need that part for a certain check” the shop control planner is going to be able to go there and move that part to the fast lane and put a note on it. You see that my planner has already done that, the part is required for Friday.
That’s going to be an immediate reminder for the planner that this is actually the next part I need to send to the shop. When the part is sent to the shop, then we are moving to the other tab of the application which is the work list. Here we are looking at the due lists or let’s say the work list of the shop or what should be being worked on by the shop at the moment.
That’s going to be an immediate reminder for the planner that this is actually the next part I need to send to the shop. When the part is sent to the shop, then we are moving to the other tab of the application which is the work list. Here we are looking at the due lists or let’s say the work list of the shop or what currently should be worked on by the shop at the moment.
What is very interesting there is that, with TRAX, we designed what we call the ‘buffer consumption’, which is a percentage incrementing with the time that the part is spending in the shop and it’s telling us the percentage of time. It shows the amount of time this part has spent in the shop compared to the TAT (Turn Around Time) that you want to have, so it’s based on your TAT and based on your due date.
You see the percentages are increasing now, you see that it displays red, and it is a very high percentage. Why? Because we are in the test database and the data gets overdue there.
When the part is just released into the shop and let’s say you have 15 days turnaround time, plus you are on the first day of that TAT, then your part is going to be displaying green. As the part is progressing along in the shop it’s going to move to yellow, then to red, and if it’s overdue it’s going to be staying red. That provides a uniform priority system.
Everybody has the same priority across the whole organization. That part is at a certain percent of buffer consumption and that defines the priority. When that part is moving to another shop it will go within the list of that shop and the shop will have to do that part according to the global priority level. This was a huge problem for us in the past because we did not have a means to indicate a global priority.
Essentially it was down to all individual shops to negotiate priorities. You know how this goes — you are from the wheel and Brake Shop and you go to the Paint shop and ask “can you do a couple of parts for me today?” But then the Sheet Metal shop lead is doing the same thing Then you have these discussions which are never ending and which take a lot of time. But this is no longer the case with the new system because now we assign a global priority to each of the parts and it’s the same for everybody and it’s controlled by our shop control center.
I mentioned that we have a lot of AOG parts, so we have a specific category for that. That’s what you see on the first line here. When the part is AOG it displays full red and shows up in front for everybody to see. So that’s a clear sign that everybody needs to stop what they are doing and get on with that part because it is immediately required to get an airplane back in the air. This is going to be displayed prominently for everybody. The page is going to be displayed on screens in the shops pretty soon here at Cargolux.
We’re going to have big screens with that page displayed so if you get an AOG part, even before the part is coming physically to your shop you know you have something that you need to work on, on a very urgent basis.
I got a little ahead of myself here, so on that work list you see your part, you see the specifics of the work order, you see all the specifics of that part; then you can see what the priority of that part is, when that part was inducted, when that part is required, what’s the remaining duration, and what’s the buffer consumption. This buffer consumption is shown on the KPIs on the right there which you will see shortly.
When we look at the overall buffer consumption in the shop, we can see the current health status of the shop.
If our shop is green, that probably tells me that the shop could manage to do a few more parts now. If the shop is yellow, it is the average condition which should be the norm or shall we say the cruise speed of the shop. If the shop is in the red (and right now it is because you are viewing the test database) everything is overdue. But if the shop is in the red, that tells me that the shop is not going to deliver all the parts on time, so that’s a big indicator for management.
Management is basically looking at the buffer consumption and can manage the shop from day to day accordingly. If the buffer consumption is increasing, then that tells me that something is not being delivering as quickly as expected in that shop and that is a very simple indicator which is basically free from any other data. We don’t need to put man hours into that, we don’t need to put fancy data into that, it’s just a due date, a consumption due date and we are able to see how that shop is doing.
I moved back to the production database in order to show you the shop indicators. These shop indicators on the right are the critical indicators we figured for our own operation.
We are integrated to the airline, so our mission is to make sure that we fly our planes as much as possible and as safely as possible.
We need to have the parts returning to stock as soon as possible, as well, so these are the KPIs we chose. You see the buffer consumption, the on-time delivery (e.g., is the shop able to deliver on time what was requested at the beginning), what is the turnaround time of the shop, what is the throughput of the shop, and is the shop continuing to release parts into the system. All these KPIs are compiled using the last seven rolling days.
With the growth of our fleet and the increase in the numbers of components that we are repairing, it was very clear that we need to have a system which shows us an overall priority and progress tracking status on the parts that we are repairing. That is what the Shop Control app does for us.
The app is very interactive. As soon as you have a few days where you say, “I’m not aware” and one of my shops has its main machine broken down and no parts are being released, you know immediately that it will start showing on the KPIs.
Obviously, we’re going to be aware of the breakdown. But even if the shop lead would not make us aware of the breakdown, we can immediately identify that the shop has a problem. Then we have an overview of what parts are in the backlog, what parts are work in progress and what parts are on hold, so that we can review these parts and see if it’s getting out of control.
And the color of the arrows makes a difference. I’m looking at my pneumatic shop right now which has a workload surge which is shown by the KPIs. You can see the status of parts – ‘backlog’, ‘in progress’, ‘on hold’. They are all increasing to an extent that we just defined this as red. If it stays stable it would be a horizontal arrow and if it’s going down in the right direction, then it would be green.
Now I will show the main page which the shops are using. There are a couple of great features to this page.
First, I need to move back to the test database. There’s a couple of great, very easy to use features for the shops, and one of these options is to move parts around the organization.
We came from a system where we took the paperwork, and we brought it to the next shop and then maybe a week later you say, “Hey, where is that part? Is the part delayed at the other shop? Okay let me check with them”.
It’s quite difficult to keep track of all these parts, so now what we designed with TRAX is you simply click on the part, select that work order, and click ‘move to site’. Right at the bottom you select which shop you are sending that part to and that’s it. The part disappears from your own work list and it appears on the work list of the destination shop. It’s going to appear according to the priority list which we described, at the priority level which we described, so it’s very powerful.
The big users of this functionality are the NDT and Paint shops. The non-destructive inspection and paint shops don’t do parts on their own, they don’t have their own capability list, so they don’t repair parts themselves, but they do a lot of work for the other shops.
The paint shop paints parts for the other shops. The NDT shop inspects part for the other shops. So, this priority list is invaluable for them because they just keep on getting parts from all sites and need easily viewable information on the next priority.
When we move a part to another shop, when we click that ‘move to site’ button, we added a nice functionality that you go into the ‘travelers’ tab’. Right now, I’m in the pneumatic shop and you can see how I move two parts. I move one part to this site and one part to that site, then I can immediately see these parts in these travelers. I know that I’m responsible for these parts, but I have a clear view of which shops I have sent these parts to.
Obviously not all parts are just a straight fix. There’s a lot of parts nowadays in the MRO world that are stuck because you need an engineering repair for them. It takes a little bit of time or you need spare parts, and that spare part is not found in the market, or you must wait awhile to get that spare part, or you’re waiting on the customer.
Let’s say you’re waiting on the customer.
The customer has to give you an approval for the quote, so we did not want to keep these parts in the work list (at that stage when the shop is waiting for an external stakeholder) because the shop is not effectively doing anything to that part. When this is happening, we have another process in place where we select that part and put that work order on hold. An example is when we are waiting for parts or tools.
There are a few reasons that you can enter to move parts away from your shop work list but still have them visible in the ‘on hold’ tab where you have the parts which are stuck for an external reason. That way you will have an overview of these parts as well.
Going back to your list where you can see your part number, you can see your work order, you can see the description of your reason that part is stuck, and you see how much time since has passed since it was blocked.
That is useful for me as a manager, because if a part is blocked for one year I’m going to say “look, at some point we have to decide something.” Maybe that part is BER (beyond economic repair), or maybe that part needs to be replaced by a new part. So, we can see the incremental amount of time that part is on Hold.
If we are waiting on material, we immediately get that material information from the page as well. The information is not populated here now, but you can see the parts button. If you were waiting for material, you would get real-time information as to what you need and when is it arriving. You can manage your status and enter a reminder note. These two very simple processes of moving parts to another site and putting a part on hold when you really cannot work on it anymore are very beneficial for the organization because they add so much clarity to the whole operation.
The Shop Control App gives us a way to decide when the part needs to be sent to the shop for repair, when is it needed and when it has been released. We can track in real time what is happening to that part and that’s extremely critical.
I don’t remember if I stated at the beginning that we handle and process 10,000 parts per year and that is increasing. This means that every day 40 parts are released. It means that, at the point we accept all the work orders and all the parts are going immediately to the shops, we have more than one thousand live work orders at a time. So, if you have more than a thousand work orders which are always open and which you need to manage, with this process we are able to triage the parts at the induction of the parts.
The work list shows only what you can work on with the right priority. You are putting the parts which you cannot work on anymore on hold and you are managing these parts in a separate workflow. All of these app functions reduce the working process in the shop and that’s the critical thing. The more you reduce the working process, the more you make life simple for the shops and for the people who are working on the parts. That is the name of the game, that’s what we are achieving here.
I’m glad to have had the opportunity to show readers the screens and please run the video as often as you wish. I hope that it has shown how the information is being used to help the organization at Cargolux to improve our performance.
I would just like to say a big thank you to TRAX. They took on the challenge of designing something new when we came up with the idea, when we came to them with the specifications. This was something which was a new project inside Cargolux. It was not clear whether we would succeed and come out with something that works. That took a lot of work from both sides and I really am grateful for that because we have a great tool that we’re going to be able to use in the future. And we’re going to be able to further develop that tool.
Contributor’s Details
Stephane Kastler
Stephane started his career at Cargolux in the engineering team as Structures Engineer, including as the airline’s representative at the Boeing plant, overseeing the technical acceptance and delivery of 747-8 Freighters for Cargolux. In 2015, Stephane was appointed Assistant Production Manager at Cargolux and then, in June 2017, Director Maintenance & Production. He holds a Master’s degree in Engineering and a Specialized Master’s in Aeronautical and aerospace structures.
Cargolux
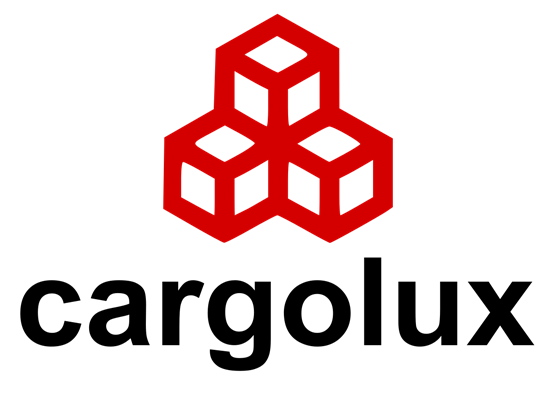
Cargolux is Europe’s biggest all-cargo airline with a fleet of modern Boeing 747-8 and 747-400 freighters offering an extensive product range, from every-day cargo to shipments that require attention, special treatment and expert handling. Innovative concepts and the constant drive for quality have earned Cargolux a number of awards, including the ‘Best All Cargo Airline’. Cargolux also offers third-party maintenance services at its modern two-bay maintenance hangar in Luxembourg specializing in 747 line and hangar maintenance up to and including C Checks.
TRAX
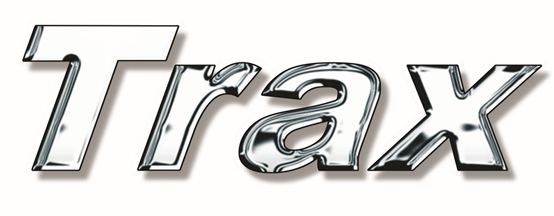
A global leader in the aviation industry for MRO ERP software, over 200 airlines and MROs using TRAX products. TRAX has the most advanced maintenance software solutions available for airlines and MROs worldwide with fleets consisting of all types of aircraft. eMRO is a completely integrated product, in addition, the eMobility suite offers a range of iOS apps to provide mobile accessibility. Gains can be substantial when using TRAX eMRO and eMobility, and ROI is quickly realized. TRAX develops software that works for customers.
Comments (0)
There are currently no comments about this article.
To post a comment, please login or subscribe.