Articles
Name | Author | |
---|---|---|
CASE STUDY: Blending legacy aircraft with digital technology at Lynden Air Cargo | Ethan Bradford, Vice President Technical Operations, Lynden Air Cargo | Jim Buckalew, CEO, AeroATeam | View article |
CASE STUDY: Ten years of ‘eLog’ operations at British Airways | Scott Falkiner, ELB Manager – Engineering, British Airways | View article |
CASE STUDY: An electronic log book for Blue Islands | Scott Dicken, Head of Maintenance, Blue Islands | View article |
CASE STUDY: A change for the better with documents at Spirit Airlines | Dan Cottrell, Senior Manager Fleet Asset Management, Spirit Airlines | Stephen Morrison, Sr. Manager of Aircraft Records and Records Compliance, Spirit Airlines | View article |
CASE STUDY: Blending legacy aircraft with digital technology at Lynden Air Cargo
Author: Ethan Bradford, Vice President Technical Operations, Lynden Air Cargo | Jim Buckalew, CEO, AeroATeam
Subscribe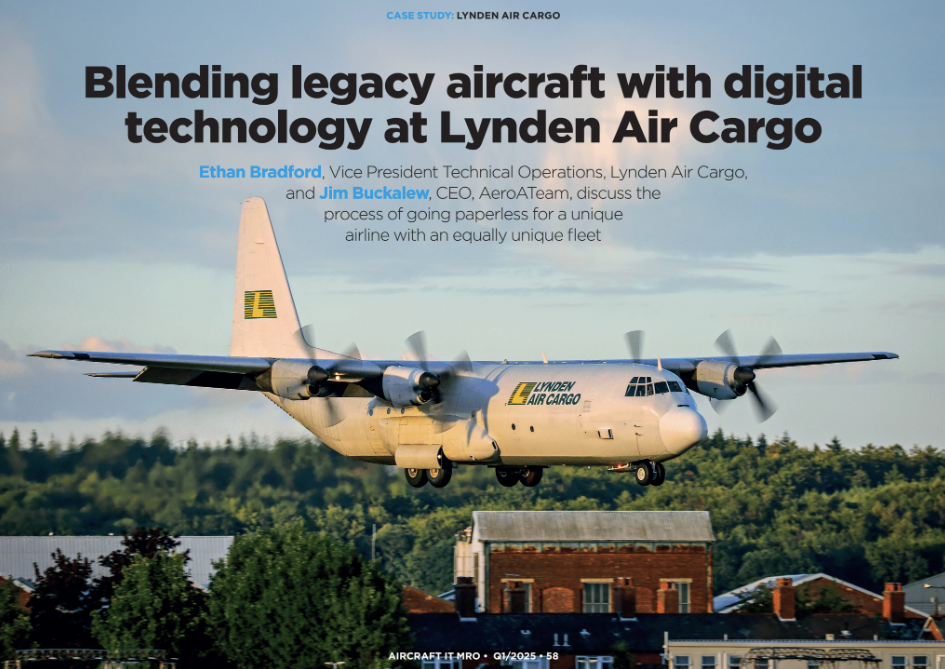
A conversational case study where Ethan Bradford, Vice President Technical Operations, Lynden Air Cargo and Jim Buckalew – CEO, AeroATeam discuss the process of going paperless for a unique airline with an equally unique fleet.
LYNDEN AIR CARGO
Since 2000 our company has operated the world’s largest fleet of civilian C-130 Hercules aircraft, the L-382. Lynden Air Cargo operates in some of the world’s most remote and challenging environments, spanning from Antarctica to the jungles of Papua New Guinea, providing humanitarian aid in Africa, supporting disaster relief efforts, and serving mining and oil sites in the High Arctic. We operate a wide range of operations but Lynden Air Cargo is not a scheduled service and, with a legacy airplane that doesn’t have digital data, we need to be self-sufficient to operate anywhere in the world, particularly in remote, austere locations where we have no connectivity. Having used a paper-based system for a long time, we now want to move ahead to support customers around the world, providing disaster relief, AOG engine moves aerial delivery or whatever services they require. We want to be able to serve our customers better with better digital tools. Our key objective, having been a TRAX user since 2000, is to upgrade to eMRO and eMobility to truly go paperless. It’s not an easy task but we will utilize mobile devices and connectivity with back-end systems to achieve that.
Jim Buckalew
AEROATEAM
AeroATeam has been working with Lyndon and has been working with airlines and with integration partners for five years. But although we put the AeroATeam together five years ago, team members have been working together for decades. We are a team of more than 40 airline experienced professionals focusing not only on technical operations but also on Flight Operations and Technology. Essentially, we are the bench in this case, with Ethan and Lyndon Air Cargo, and we all augment the support as needed in these types of projects. We have a full suite of technology available for software as a service (SaaS) and we do hosting, but most of all, we apply our experience as airline professionals in these types of projects.
Ethan Bradford
LYNDEN AIR CARGO
That’s very true. It’s very important, I think, that with any piece of software, it should be backed by experience that directly relates to your operation, as it operates. That experience is what Jim and the AeroATeam team bring; professionals with established airline experience. They’ve experienced different types and sizes of airline operations which gives us the ability to take the existing tools that we’re working towards with going to eMRO and eMobility and leverage those to our benefit, not copying any other airlines operation, because everybody’s different. Our operation is definitely unique, and their unique professionalism brings that experience to bear; that’s why we have this partnership, as they help us continue down this path.
BUILDING A BUSINESS CASE FOR CHANGE
Our vision is to become modern, with an integrated M&E system, and to be able to do this remotely with connectivity, you can’t move information without connectivity. We want to enable a paperless, or near paperless system, and improve our Tech Ops integration with our internal business processes and who we do business with, to get efficiency with our different systems. We’re going through a transformation. It’s been a while that we’ve been operating the TRAX paper-based system. In that time, we have taken on additional aircraft and, because ours is a legacy aircraft, a lot of people have worked with the Hercules over time, but a lot of them have retired, and we have new younger people coming in who want to embrace technology, want to go paperless. They already know how to pick up an iPad and use an app and we need to embrace that technology in our operations. In short, it’s time to be more efficient. In that and in the implementation of the TRAX system, we want to upgrade and to start establishing both the eMobility and eMRO in Microsoft Azure. We’ve been working with our corporate IT to do that, and Jim is helping us with that work to bring this Azure architecture to fully support the eMRO and eMobility applications into our environment.
Jim Buckalew
This case is a good example of how AeroATeam can give a business like Lynden industries, very large company logistics worldwide, and not just for the Air Cargo division. In this case, there is a fully Microsoft shop that really wanted to go to Azure. We not only had the AeroATeam, IT group, working with TRAX, but also with the Lynden IT to roll out eMRO in the Azure environment. It’s an example of the technology that we help bring the people together on.
Ethan Bradford
There were quite a lot of back-and-forth meetings with TRAX, because we’re a small operator. The business models were designed for larger airlines using eMRO and eMobility, but we were able to work through an arrangement that works for us as a smaller operator. We did look at software as a service but because of the nature of our operation, the uniqueness and the environment within which we work, we wanted to have it in house, to be able to support our own software and maintain it. So, the decision was made that, because our company is a Microsoft shop, we were going to establish the architecture for Azure and Terraform to load in eMRO and eMobility within our own environment.
With that, the integrated teams within Lynden Air Cargo tech ops, worked together with Lynden’s corporate IT (we’re a family of 20 companies but all separate) but it was a little bit difficult to get our Lynden IT department in the mother company, to be able to support it. It took a bit to work with them as a team plus we had to work with Jim and the AeroATeam with their expertise, and we had to work with experts at TRAX to help us design the architecture to support the two platforms. The other thing that we’ve done, as we worked through the business processes at Lynden Air Cargo to improve our use of TRAX, is we’ve been working with the A team, because they bring this airline experience where, because we’re a small infrastructure, it was difficult for us to take time out of the day. We’re a busy global operation: it’s 24/7 and, with messages arriving in the middle of night or an email you have to respond to, we don’t always get to stop.
To address that time issue, we had to break the project down to bite size pieces with an agile sprint approach where, where we would decide ahead of time with the AeroATeam that we would work on certain portions of process improvements and take out a day or half a day and make sure those people were available. We’d have Teams meetings, or they would sometimes come on site, face to face, and work with the individuals that were involved in that very specific task within the business process that we’re improving. That arrangement worked very well. We’re just not big enough to handle being down for a week and having to cut out ten people to be party to a process improvement; it was very important for us and the AeroATeam worked very well with that process.
Jim Buckalew
That highlights how we all have to stay flexible. Obviously, the airline operation is the first priority but breaking the process down to bite sized chunks enabled Lynden Air Cargo to make significant progress across the divisions. As we introduced best practices in engineering programs and planning, we had focused sprint sessions, remote and on site, for change management at pace as well as the technology. We have to adapt to the operator and our client, of course, but it both fulfilled their needs to continuously improve the technology in the organization and to make progress towards being in place for the next generation leap to a cloud-based solution with MRO and mobility.
Ethan Bradford
That sprint approach worked very well for Lynden Air Cargo and, with that, we’re hoping to get to our next stage. But what are the reasons, why are we changing?
We’re currently on version 12.5 of TRAX which is no longer supported. We can’t do patches; our Oracle database is an older version and we’d have to incur great expense to upgrade the Oracle database to the later version in order to go to the upgraded TRAX. As already mentioned, we’re currently in a paper-based process, and want to automate the processes in between the systems that we have within the company, whether that’s interfacing with flight operations or accounting or some of the other cargo movements and so forth, and bring all these pieces together. We want to bring everything into one platform where we can open up the database and open up the platform to be able to interface.
Going back to the sprint approach, we’re taking the same approach to the upgrade and we’re doing this in phases. Phase One is where we’re going to take the core functionality, upgrade to eMRO, and break that down into where our corporate IT is going to build the Azure architecture, the infrastructure and all the systems in place to support it. TRAX is going to come in and do the install and the data conversion. Along that data conversion process, we’re going to enlist the help of the AeroATeam in order to work with a number of data conversion pieces to ensure that that we have valid data in the new environment.
Once we get up and running, then we’re going to go through these business process improvements in the different departments; and then, once we’re settled in and stable in the eMRO cloud-based version of TRAX, we’ll move on to eMobility and bring that on. That’s really going to give us the true paperless piece, because now we can go full circle with the paper. We can push requirements out, from maintenance planning to the heavy maintenance check or the line personnel. They’ll be able to sign off the tasks on their iPad and return that electronically, back through the system and to aircraft records, where they’ll do a final audit, and site start that cycle over.
Jim Buckalew
The project plan in figure 1 highlights our approach in those phases
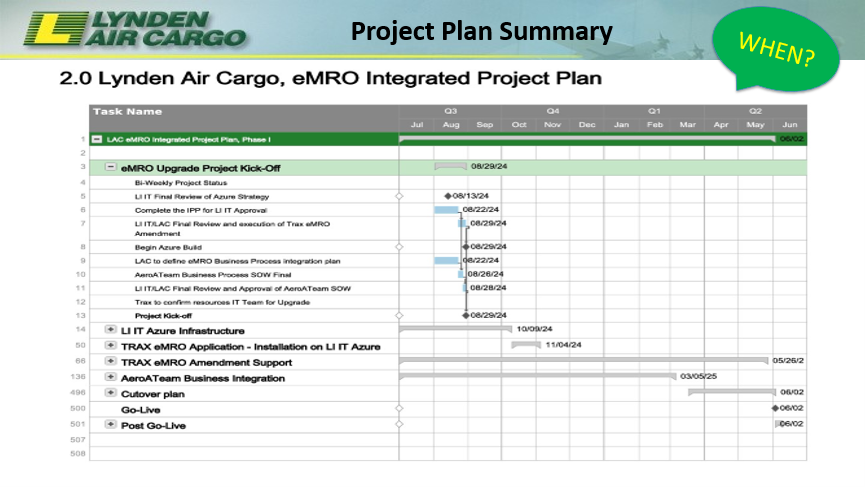
Figure 1
At the beginning, phase 1, we’re still working with the rollout of Azure and the new technology, block and tackle, compliance and support, and standing up the solution in the cloud. And then, in phase two, not only will eMobility give paperless processes, but it gives a data platform for advanced technology. We’ve heard some great things about AI, and we’re putting Lynden in a good place to really take advantage of the advanced technology.
Ethan Bradford
We’ve actually started the process of going paperless by creating electronic forms, using comply 365 for our distribution of manuals. We’ve reduced the amount of paper that we carry on the aircraft or distribute to mechanics. Like anything, it takes a lot to change people that like paper. They know how to find things with paper, but as soon as you take it away from them and show them the tool and show them how to search and find information, and if it helps them do their job better, you’re going to end up going paperless.
Jim Buckalew
We’ve already mentioned TRAX 12.5, which has been stable for 20 years, but with a lot of manual work that we’re now automating. Initially, the systems in the business were not integrated with the corporate systems that Ethan mentioned. And while being based in Anchorage, and having the great team and legacy that Lynden has, the team is ready for the next level of technology. That’s been an incredible engagement over the years with Lynden, the platform is now ready, and certainly the people are ready. And, as you know, with big projects, the technology sometimes comes easy, and the change management and the people are the harder part. We haven’t seen that at Lynden: it’s a great marriage of advanced technology coming together with the people.
Ethan Bradford
On that note, Lynden Air Cargo has been using TRAX for 24 years. Back then in 2000 there weren’t a lot of features or capabilities with technology or interfacing readily available along with the generation that we had, the older generation of people that have been maintaining our fleet. We now have the younger generation and they’re ready take the big step to digital and paperless. In the management of change, you can lead a horse to water but you can’t always make it drink. So, you have to go through the process. It takes a while for management of change.
Jim Buckalew
One of the elements of the project is a Hercules analog fleet that’s been serving Lynden for many years going digital. We’re converting the maintenance program to digital test cards, and we’re absolutely going to leverage the technology and eMobility to roll that out to the front line as well.
Ethan Bradford
These are the different areas where we’re going to get the return on our investment; maintenance, control and planning and quality and technical efforts, really shifting our method. Paper has a certain process to go through in order to process it, and when you go fully paperless, that moves everything to the front of the line on the front end, and you end up being more efficient and able to do transactions in real time. But that process changes all these different departments and improvements.
For instance, we have parts movements all over the world, and we use a paper-based system in order to tell us where a part is moved from one place to another. But when you have the mechanics with an iPad at every place that they’re doing work on the airplane, you know that all that compliance of an inspection or a removal of a part, shipping a part, receiving a part, all those transactions are going to be captured and make us more efficient our operation.
We can communicate with our data center and determine whether there’s a requirement, an inspection, a change of part, a part coming, what the tracking number is, all that can be possible as long as you have a device to store it offline and that you can connect to the database that contains that information. One of the things that we’re doing on our fleet right now is we’re going through a major upgrade for avionics, and looking at installing Starlink for broadband connectivity because it’s very important in a remote, austere location where you have no local connectivity, to have that connectivity. So, you’ve got your device, you’ve got connectivity, and you got your software, your systems and your data that you connect to in real time. That you can support any operation anywhere in the world.
Jim Buckalew
Figure 2 is an example of how we married the sprints and the efforts with each of the disciplines of the AeroATeam people to advance change management.
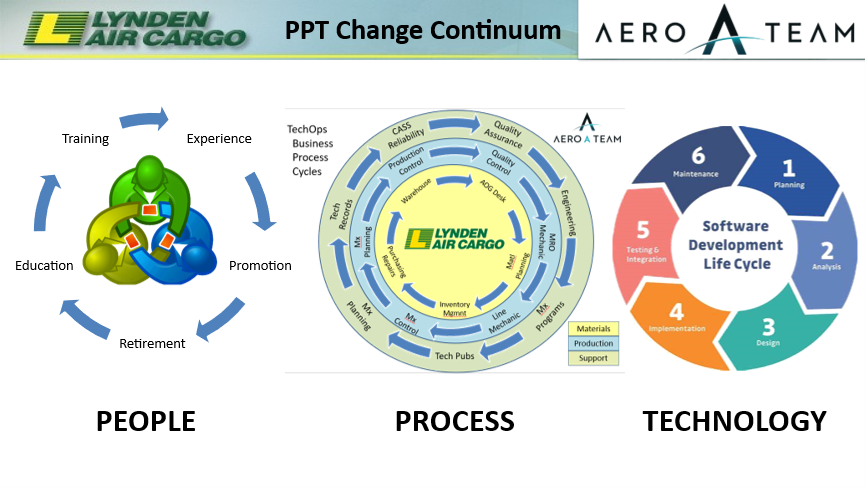
Figure 2
I mentioned that helping do the digital transformation puts Lynden, a fairly small operator but unique in its mission, in place for advanced technology. So, we’re happy to be working with them on applying some very specific use cases. This is what we like to do, to help airlines and apply this technology for very specific labor cost reduction such as asset utilization increasing the utilization on fleet maintenance, program optimization, material costs. Reducing material costs through some of this advanced technology is very focused. So that is our next step. And we are working with partners, integration partners. We’re becoming the integrators for the technology to the airline’s very specific use cases and real, tangible and measurable returns.
Ethan Bradford
It’s important, not only for us to go paperless but also to embrace technology. Artificial intelligence is obviously going to change the way the world operates: it’s like the Industrial Revolution but it’s the computer revolution. If we can mine the data, collect the data, the information, we can make it relevant. Lynden Air Cargo is preparing for the next phase of digital transformation – leveraging AI for predictive maintenance, intelligent troubleshooting, and data-driven decision-making. By mining decades of aircraft maintenance transactional data, internal communications, and maintenance documentation, AI can provide mechanics with real-time recommendations, enhancing efficiency and reducing downtime. Say we have to work on an aircraft. It’s not necessarily straight out of the maintenance manual. So, the knowledge base that comes with working on that aircraft and it’s hard to get those people that have that knowledge base. So, when you have the data of how the airplane was maintained over decades, and use AI to answer a troubleshooting question or what steps you should take to do a certain job. If you can have a conversation with the data and let it tell you the correct information to make the decision you will have a more efficient operation and be able to use people that have a skill set that may not be available today on older legacy aircraft that we have. It’s important that we embrace artificial intelligence.
Comments (0)
There are currently no comments about this article.
To post a comment, please login or subscribe.