Articles
Name | Author | |
---|---|---|
CASE STUDY: Blending legacy aircraft with digital technology at Lynden Air Cargo | Ethan Bradford, Vice President Technical Operations, Lynden Air Cargo | Jim Buckalew, CEO, AeroATeam | View article |
CASE STUDY: Ten years of ‘eLog’ operations at British Airways | Scott Falkiner, ELB Manager – Engineering, British Airways | View article |
CASE STUDY: An electronic log book for Blue Islands | Scott Dicken, Head of Maintenance, Blue Islands | View article |
CASE STUDY: A change for the better with documents at Spirit Airlines | Dan Cottrell, Senior Manager Fleet Asset Management, Spirit Airlines | Stephen Morrison, Sr. Manager of Aircraft Records and Records Compliance, Spirit Airlines | View article |
CASE STUDY: An electronic log book for Blue Islands
Author: Scott Dicken, Head of Maintenance, Blue Islands
Subscribe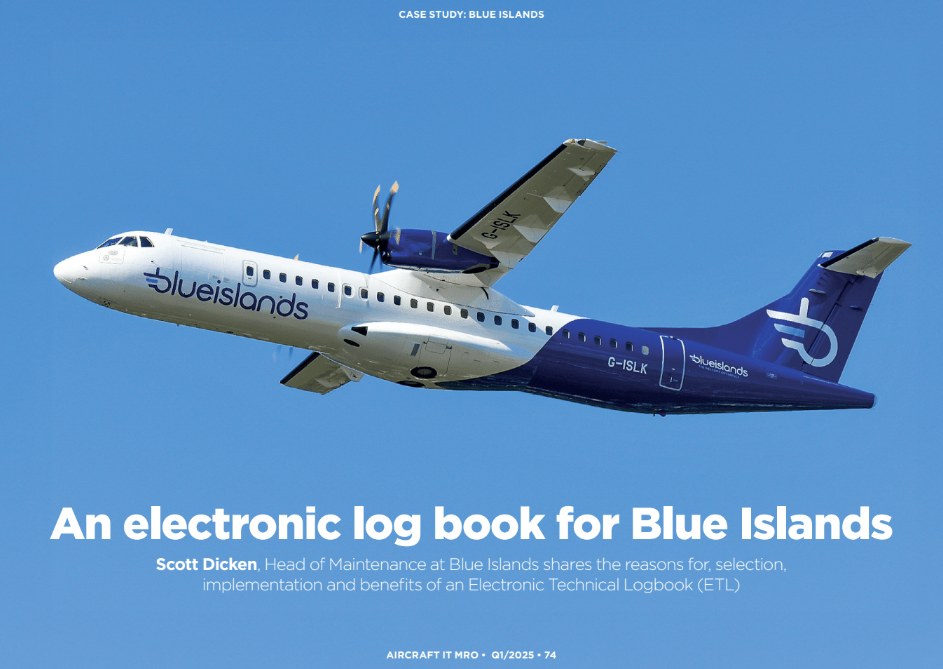
Scott Dicken, Head of Maintenance at Blue Islands shares the reasons for, selection, implementation and benefits of an Electronic Technical Logbook (ETL).
BLUE ISLANDS
Based in Jersey, Blue Islands operates ATRs. It’s a different operation compared to some larger airlines; we fly lots of sectors which are divided into three types: short-haul, medium-haul and long-haul. Our short-haul is Jersey to Guernsey (nine minutes flight time); medium-haul is Jersey to Southampton (30 minutes flight time); and long-haul is Jersey to Birmingham or Manchester (60 to 90 minutes flight time). The interesting thing with Blue Islands is that we fly a lot of sectors in a day. Compared to a long-haul carrier that might only fly two sectors in a 24-hour period, our aircraft can fly up to 18 sectors a day.
Although the origins of the airline go back to 1999 as you will see in figure 1, Blue Islands was launched in 2006 and has remained a proud independently owned and operated regional airline.
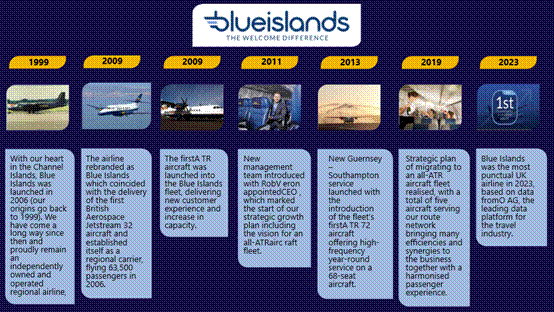
Figure 1
The airline was rebranded as Blue Islands in 2006, the same year as when the first British Aerospace Jetstream 32 was delivered; 63,500 passengers were flown in that first year. In 2009, the first ATR aircraft joined the fleet, delivering a new customer experience and increasing capacity. In 2011, a new management team led by Rob Veron, CEO, marked the start of the airline’s strategic growth plan, including the vision for an all-ATR fleet. With the introduction of the first ATR 72 aircraft, the Jersey to Southampton service was launched offering high frequency, year-round service on a 68-seat aircraft. By 2019 the fleet comprised five ATR aircraft and in 2023, was confirmed as the most punctual UK airline based on data from OAG, the leading data platform for the travel industry.
WHY AN ELECTRONIC TECHNICAL LOGBOOK?
The main reason was that we needed enhanced communication between the crew flying with the aircraft and the maintenance team on the ground, as well as greater compliance, greater accuracy and all the normal sorts of reasons, as you’ll see in figure 2.
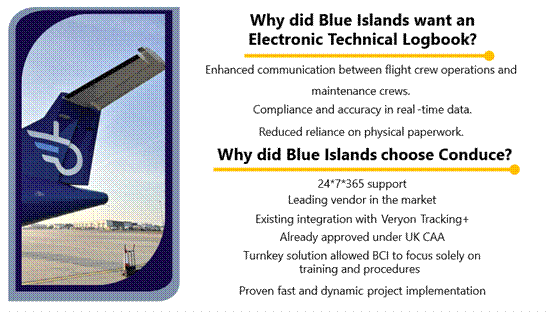
Figure 2
We needed to reduce reliance on physical paperwork which was often hard to read, incomplete, and late coming back into the MCC (Maintenance Control Center) or into the Flight Operations Office. Also, we wanted to ensure compliance and accuracy with real-time data. For those reasons, we decided to look at an electronic tech log (ETL). It can be more difficult for a small airline such as Blue Islands to make the business case for implementing an ETL, since a smaller fleet has less economy of scale. However, our board and CEO had the vision to see both the financial and the less tangible benefits from an ETL for a high intensity operation like Blue Islands.
CHOOSING CONDUCE
There were a number of contributing factors that led Blue Islands to choose the Conduce eTechLog8 solution, not least of which was the 24/7/365 support that is run pretty much like a 24-hour MCC would be run. Conduce are quite happy to take a call from the captain in the cockpit, or the engineer on the line to make sure they get immediate assistance and avoid any delay. In addition, the Conduce eTechLog8 was already integrated with Veryon Tracking Plus, and was already approved in the UK under the UK CAA (Civil Aviation Authority), as well as many other approvals around the world. Conduce also had the capability to organize a well-proven, fast, and dynamic project implementation, which was very welcome. Finally, Blue Islands liked the full turnkey approach Conduce offer, which allows the airline to focus on flying, training, and procedures and not become a software development company!
To emphasize the importance of that last point – Blue Islands is a small team. We don’t have lots of people from IT, Flight Operations or MCC that can just be put onto a project to support a particular piece of software. So, to have Conduce provide everything from the hardware and software to the hosting, data, comms support, was really valuable. It means that Conduce is a ‘one stop shop’ for all things ETL, which was, and continues to be, really convenient.
We put together a business case based around the facts that eTechLog8 customer airlines reap the benefits of sustainable digital operations for faster turnarounds, cleaner data, and greater fleet oversight as shown in figure 3.
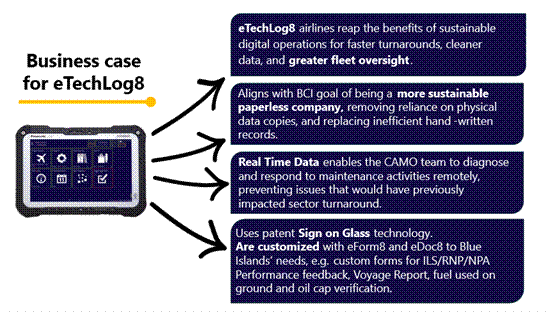
Figure 3
It also aligns with Blue Island’s goal of being a more sustainable, paperless company; removing reliance on physical data copies, and replacing inefficient hand-written records. eTechLog8 uses patented Sign on Glass technology so we also had confidence that the data we were collecting was legally signed for electronically. We realized if we could collect the correct data at source, then we could use it within the rest of the organization reliably and efficiently. Real-time data means that our CAMO department and MCC can respond to any crisis that might occur as well as being able to diagnose and respond to maintenance activities remotely, preventing issues that would have previously impacted sector turnaround. Our aircraft fly in very, very short sectors. Therefore, anything that was going wrong with an aircraft during the operational day was having a huge knock-on effect. Getting real time and accurate information provided a solid business case.
We also looked at the additional modules that are built into the Conduce product, including the forms designer (eForm8) and the document library (eDoc8), as well as a number of add-on modules that the Blue Islands team have adopted and used. To give some concrete examples, we used eForm8 to create custom forms for collecting data related to ILS/RNP/NPA (Instrument Landing System/Required Navigation Performance/Notice of Proposed Amendment) Performance feedback, Voyage Report, fuel used on ground and oil cap verification. And again, since we didn’t have a large IT team to develop custom features and functions, we were pleased to find that the eTechLog8 solution is fully customizable and configurable within the existing system. In fact, there wasn’t a single software code change required for the deployment of technology across Blue Islands.
CHALLENGES ENCOUNTERED
Whatever you do in whatever context, there are always challenges, whether you’re operating Airbus A380s, Boeing 777s or ATRs. One of the challenges we had with our ATRs is that they don’t have any on-board capability to charge the devices; no USB, no auxiliary power socket or anything of that nature. Happily, Conduce were able to supply us with a rugged device with the option for a second, additional battery. This doubled the battery life of each device. In addition, the batteries in the supplied rugged devices are fully removable, so we could rotate the batteries and charge them in the line office overnight – or whenever needed. This was also really useful in providing an opportunity to see if any batteries were damaged or anything of that nature.
Another potential challenge was that we were rolling out our maintenance control system at the same time as deploying the ETL, which gave us some concern about having too many projects running simultaneously and in parallel. However, the eTechLog was actually implemented relatively quickly, with a lot of support from Conduce. The good thing about an ETL is that we don’t necessarily have to worry about data migration. Open ADDs (Acceptable Deferred Defects) do need to be taken into consideration when transferring from paper to electronic, but there are not any mass data migrations and data validations to undertake. It’s just a case of setting the aircraft up at its current status. eTechLog8 being implemented relatively quickly suited Blue Islands’ business case because, as I’ve already mentioned, we’re a small dynamic airline and a lean organization.
The other challenge for Blue Islands is our incredibly short turnarounds. The ATR doesn’t have many passengers, compared to, say, an A380 so it only takes a few minutes for all the passengers to get off and for the next passengers to board, especially at Jersey where it’s only a two-minute walk across the apron to the airplane. It was invaluable for us to have a product that would enable the airline to reduce or avoid turnaround delays by having good information and good systems in place, but also being easy and fast to use. eTechLog8 allowed us to consistently optimize short turnarounds, by providing greater oversight of the fleet maintenance.
THE TIMELINE
As you’ll see in figure 4, the timeline started when the contract was signed in March 2023 and we started flying with the eTechLog8 in October of that same year.
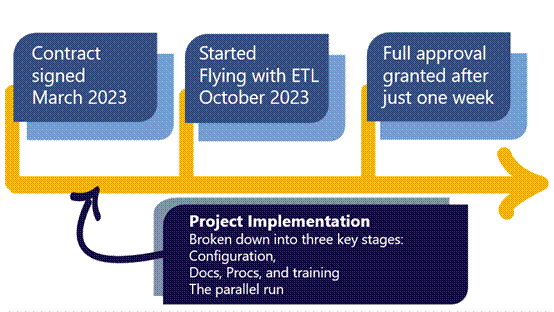
Figure 4
If we’re totally honest, not a great deal happened during the summer months, largely because we’re really busy flying over the summer season. The project was broken down into three key stages and we adhered to the KISS (Keep It Simple Stupid) principle which really worked well. In the configuration stage we focused on trying to make eTechLog8 reflect what’s happening in the real world. We didn’t want major software changes or major business process changes; we wanted to make the implementation as simple as possible for the crew, the engineers and all involved, because it does touch a lot of people within the organization. Once the configuration was fixed, which didn’t take very long, then it was a case of preparing the training materials; an interactive CBT (Computer Based Training) course for Engineers and Pilots, and lots of small group, hands-on sessions for everyone using the system. We then produced all the new documentation, new processes, new procedures, etc. Next was rolling out the training to crews and engineers, and then there was the parallel run which, with Blue Islands, lasted just one week, after which we were fully flying with eTechLog8 live on the aircraft.
We were very efficient with the parallel run and obtained UK CAA approval really quickly. This was largely to do with the number of sectors we were flying – often thirteen to fifteen sectors per day. This created a lot of flight data that we could use to demonstrate to the UK CAA that the system really works. During that parallel run period, it was really important to address any challenges. Things will go wrong in the first couple of days of a parallel run, but it was important to acknowledge them and to resolve them. We were able to show the CAA any errors that we identified and any data mismatches, and where we had tweaked the configuration or the procedure in response. But the speed of achieving approval is also a testament to the training and the willingness of our whole team to embrace change.
WHAT DID WE ACHIEVE
Having made the investment and installed the eTechLog8 in our aircraft, we were able to enjoy a number of benefits as shown in figure 5.
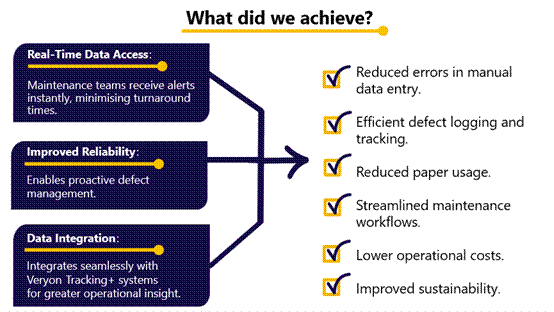
Figure 5
First, we now have real-time data access which means that every time an aircraft lands, it’s transmitting the data to Maintenance who also receive real-time alerts to any issues arising in flight that need to be addressed. That minimizes turnaround times. We get the OOOI times and any defect reports immediately into the back-office website, eCentral8, so we have real-time visibility of our aircraft.
eTechLog8 has also definitely improved reliability; having advance knowledge of what’s happening during the operational day has really helped us to plan overnight, when the aircraft are on the ground. We can deal with any defects that have arisen during the day, and we can provision and make the necessary resource available faster.
Integration is another key point, which in Blue Islands is mainly into the Veryon system. We don’t have ACARS enabled aircraft so can’t get the benefit of receiving data onto the device, but we no longer have to manually type information into the MRO system, saving time, reducing errors and freeing up our team to do other valuable work.
And then there are the normal things that can be achieved with any electronic tech log. For instance, we’re reducing errors and reducing paper with a much more streamlined maintenance workflow within the business. Everything just works so much better!
STATISTICS AND KEY TAKEWAWAYS
Since the go-live, we’d flown over 9000 sectors at the time of writing and, within that, we’ve recorded two and a half thousand maintenance activities. Some of those will just be standard maintenance activities on a turnaround, and some will be line defects that have been recorded and been fixed or deferred. The pilots and engineers alike are positive about the system and their feedback is that they find it intuitive to use. eTechLog8 has improved fleet oversight significantly. I know it’s only five airplanes at Blue Islands, but even five airplanes going wrong on a wet winter’s day is something to be avoided. The integration with Veryon Tracking+, mentioned above, has eliminated manual data entry from hand-written records and improved data confirmation and validation. Since they went live in October 2022, Blue Islands crew have actually called Conduce for support only nine times per one thousand sectors flown which, in itself, gives an idea of the reliability of the product.
In figure 6, you can see the support calls analyzed by type.
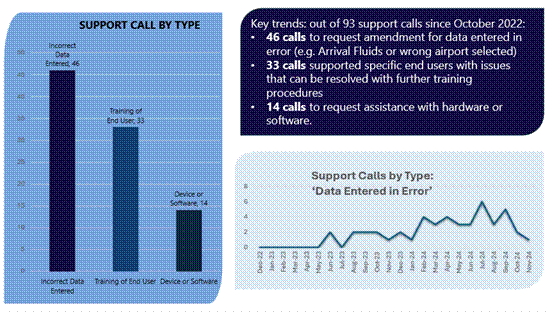
Figure 6
As mentioned earlier one of the things that attracted Blue Islands to the Conduce application was the level of support. If there’s anything wrong with the ecosystem related to the techlog, then it’s Conduce we call, whether it’s data, communications, the device, the software or whatever it might be. And you can see that the number of calls is pretty small compared to the number of sectors that we fly in a relatively short period of time.
WHAT’S NEXT FOR BLUE ISLANDS AND eTechLog8
Having implemented eTechLog8 in Blue Islands’ fleet, we want to take full advantage of the solution’s many capabilities, as you can see in figure 7, to do more than just replace the paper TechLog.
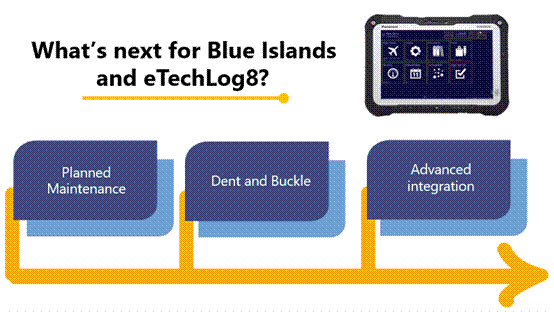
Figure 7
Planned maintenance is something we want to be able to undertake in the future. We’re not talking C-checks here on the eTechLog8 device but more what we would call, in the old-fashioned terminology, out of phase maintenance tasks. With an aircraft on the ground for a few hours, we might deliver a couple of work packages, some work cards to the device, and they’ll carry out actions on the device, and send the compliance straight back into Veryon Tracking+. We want to roll out the Dent & Buckle, get rid of the paper Dent & Buckle charts from the aircraft, and have that available on the device; and then we want to advance the integrations a bit more as well. All of these things are actually already available in eTechLog8 and Blue Islands is keen to take the steps to build on what we’ve achieved already and introduce additional functionalities in the business. We don’t have a huge project team to be able to do these things immediately, but we will gradually introduce them over time.
This has been our experience with eTechLog8 and we are very happy to be able to reach out to readers with that experience; especially those who are thinking about undertaking a similar implementation.
Comments (0)
There are currently no comments about this article.
To post a comment, please login or subscribe.