Articles
Name | Author | |
---|---|---|
WHITE PAPER: New Technology Focus – Extending Digital Twins to Digital Financial Twins | Sriram Haran, CEO; Varun Prakash Anbumani, Senior Solution Architect and Vamsi Krishna, Data Scientist, all at KeepFlying | View article |
CASE STUDY: An ERP system that has grown with Airbus New Zealand | Peter Buscke, Production Engineer, Airbus New Zealand shares Airbus’s experience with Ramco in New Zealand | View article |
CASE STUDY: A digital game-changer for JAL Engineering Co. | Atsushi Kita, Senior Director, Maintenance Planning Group, JAL Engineering Co. | View article |
CASE STUDY: An ERP system that has grown with Airbus New Zealand
Author: Peter Buscke, Production Engineer, Airbus New Zealand shares Airbus’s experience with Ramco in New Zealand
Subscribe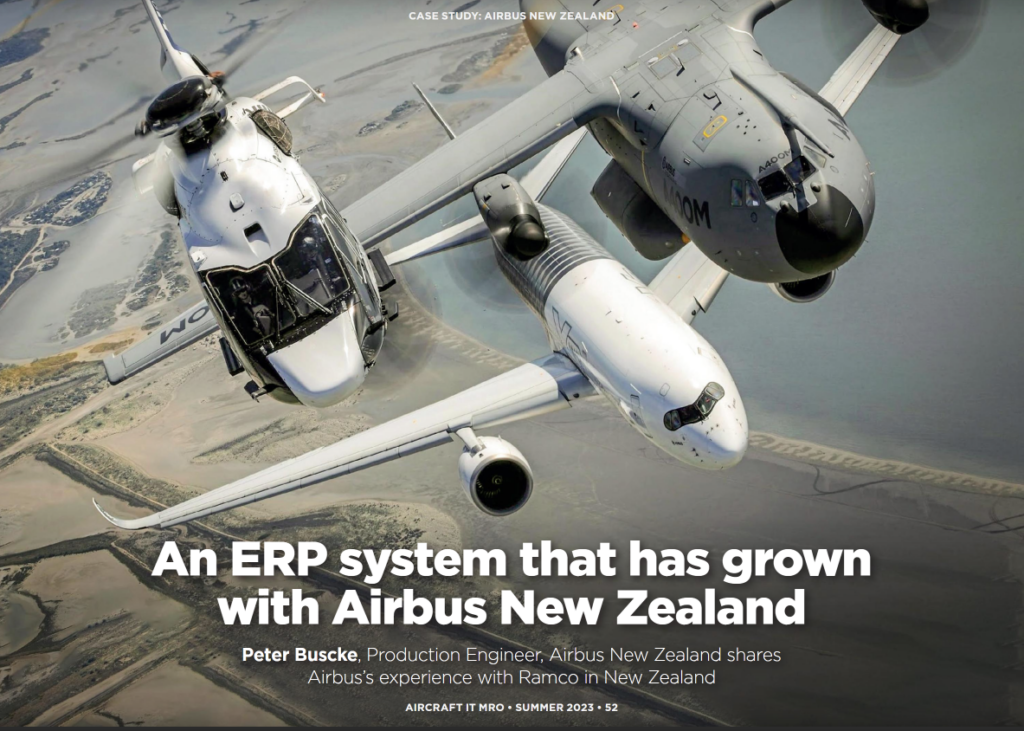
Peter Buscke, Production Engineer, Airbus New Zealand shares Airbus’s experience with Ramco in New Zealand.
Before we delve into the case study here, I’ll share with readers some information about Airbus and Airbus New Zealand.
AIRBUS NEW ZEALAND
Airbus New Zealand is part of Airbus global, an international aerospace pioneer with some pretty high expectations and ambitions, including to be produce the first zero-emissions commercial aircraft which they aim to achieve by 2035. The ZEROe concept is for an aircraft powered by hydrogen. As part of this project, Air New Zealand has partnered with Airbus. With over 125,000 employees and, as the largest aeronautics and space company in Europe and a worldwide leader, Airbus is at the forefront of the aviation industry.
Divided into three divisions Airbus includes: Airbus Defence and Space, Airbus Helicopters (the world’s number one helicopter manufacturer) and, of course, Airbus Commercial. Across Australia and New Zealand, Airbus Australia, our immediate Airbus division, operates 15 locations with 1,400 employees. Most of our work is in serving the defense forces in both countries, and supporting over ten aircraft fleets in the Australian Defence Force and New Zealand Defence Force as well as Airbus Commercial Helicopter sales within the region. We also provide a range of component MRO services to customers in the region including large aircraft engine and propeller overhaul and aircraft strip and paint.
In New Zealand, the original business was Safe Air which was purchased by Airbus from Air New Zealand in 2015 and offers maintenance, repair and overhaul (MRO) capability for military and civil airframes and engines. These include types operated by the New Zealand Defence Force, such as the C-130H and P-3K Orion and SH2G Seasprite. Airbus New Zealand employs 250 people, including skilled technicians and engineers, at sites in Blenheim, Auckland, Ohakea and Whenuapai. Due to New Zealand’s geography, the country is well suited for helicopter operations especially in the South Island.
Our operations in New Zealand are divided across four areas at the moment. There is Whenuapai which is located on a military base on the upper North Island and serving the Royal New Zealand Defence Force; there is Ardmore which looks after commercial helicopter sales and has, in the past two years, enjoyed record sales in the New Zealand area; there is Ohakea which is also engaged with defense force support including a T6 Trainer operation; and finally, there is Blenheim which delivers MRO support for the New Zealand Defence Force as well as covering a lot of engine overhaul and aircraft deep level maintenance of the force’s helicopters. Our future programs look towards us being a continuing strategic partner with the New Zealand Defence Force
In Ohakea, as already mentioned, we have a program looking after the T6 Texan training fleet. Back in 2014, we had the opportunity to put in a bid for flight training for the New Zealand Defence Force, partnering, at the time, with Beechcraft, which is now Textron Aviation, to supply aircraft through-life support for RNZAF flight training. The ERP systems in use at Ohakea area divided into SAP, which looks after financial and materials overview while we use Ramco for a lot of the maintenance flight logs, maintenance scheduling, maintenance recording, and materials and aircraft configuration.
Unfortunately, this means we are doing some double entry of data which isn’t great. We have been offered the IRIS program by Ramco that can automate data transfer between our two ERP systems but our internal governance is preventing this from occurring for the time being. One of the great features when we were going through our journey to using Ramco 5.7 to support the T6 program, was that Ramco provided all the training and set-up the RNZAF staff with view access to the Ramco on cloud system.
RAMCO JOURNEY
Much of our appreciation of Ramco has been built on a long relationship that we have enjoyed with them.
Safe Air and the t-6 program
Our journey with Ramco started in 2006 with version 4 at Safe Air. At the time, most of our work was MRO related or held at Blenheim so we needed a solution that best fitted our needs. That solution was evaluated as Ramco. We stayed with the version 4 solution until 2020 when we had to migrate out of the system. As already mentioned, in 2014, the then Safe Air won a bid for the flight training program at Ohakea. As part of that program, we had to implement a new ERP system and decided on Ramco version 5.7 which provided us with everything that we required. Implementation entailed an initial program load, update of spares, upload of aircraft configuration, initial training and the building of maintenance schedules. In 2019-20, we added technical documentation capture, evolved packaged maintenance with multiple options of orders, tasks, subtasks and packages, and evolved aircraft configuration records to utilize more sub-subcomponents.
Figure 1 gives a representation of the initial modules, highlighted in orange, that were installed for Airbus NZ (Ohakea).
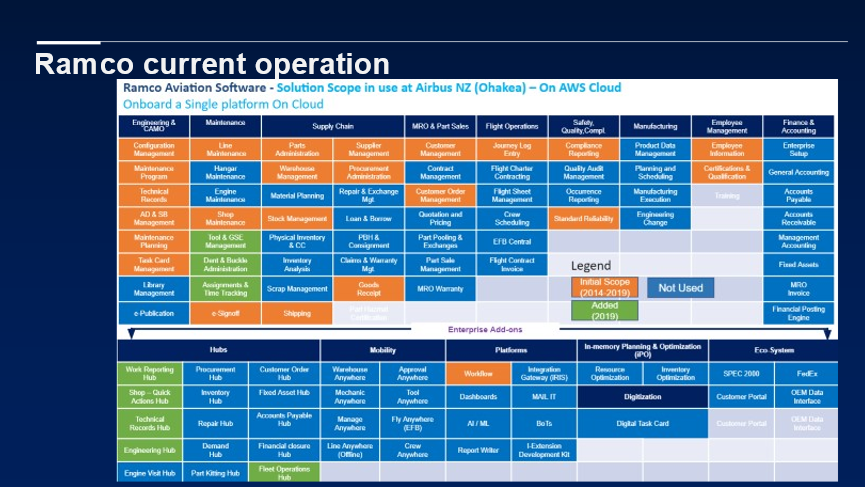
Figure1
The ones highlighted in green are the modules that were added later.
2021 Version 5.9
In 2021 we undertook an upgrade of the system. One of the mistakes that we had made previously was that we didn’t take a lot of the upgrades that were offered and so, when we got to 2021, some problems were becoming apparent with stability. We also had identified some expanded uses for which we needed appropriate updates, plus we needed some extra modules added.
We added a Work Execution Hub which enabled us to have a good visualization of all the maintenance requirements for the aircraft; gave us a very good overview and meant not having to switch between different screens to do a lot of the work, which improved our workflow. Fleet Operation Hub (figure 2) was another module that was added which has a very good display of aircraft availability.
We also updated our certificate of release which involved us in adding another certificate to the list.
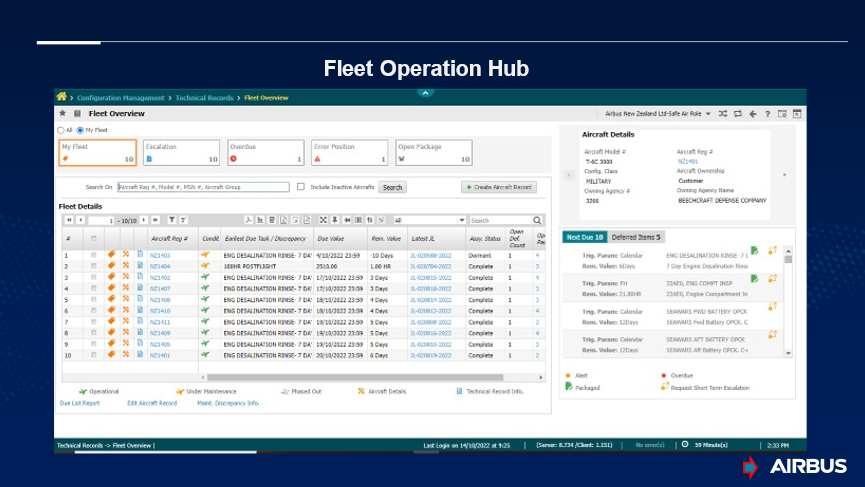
Figure 2
One of the big problems that the Fleet Manager faced was having to regularly report to the RNZAF to show them what the aircraft availability was like and Fleet Operation Hub greatly simplified that. There’s a traffic light system that tells us exactly which aircraft are available. If any maintenance occurs, we end up with a change on that traffic light system.
Component Control and Configuration Control is done through the Component Records (figure 3) and is an easy display to show what outstanding components there are being changed: it has good visibility and was a great support for the planner in understanding what the configuration state of the aircraft was like when the aircraft was departing the maintenance check.
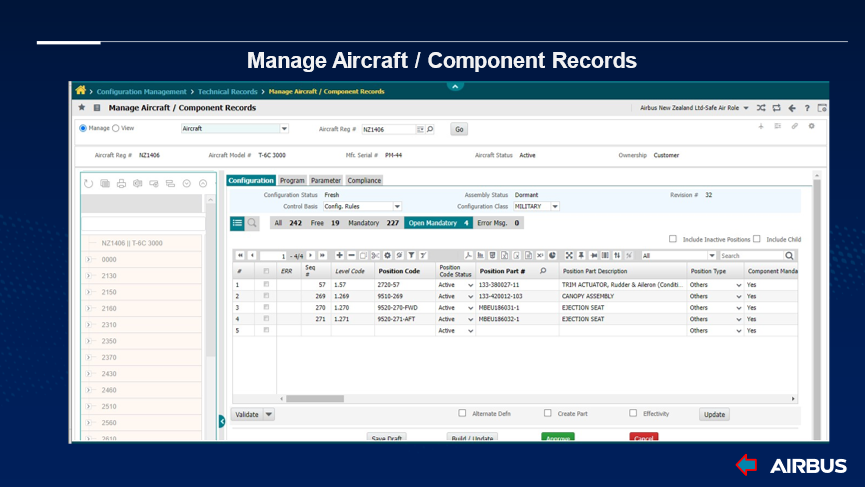
Figure 3
Facilities management was another tool that was added. Prior to this, facilities management, tools and calibration, etc. was being done on a spreadsheet which was not vey good. We needed to link in tools that were being used on the job to be able to understand where the tooling was used, especially if there was an out-of-calibration alert. Having the ability to effectively manage our tooling from a maintenance perspective and tooling use was a big step forward.
Shop Hub was another screen that was added (figure 4).
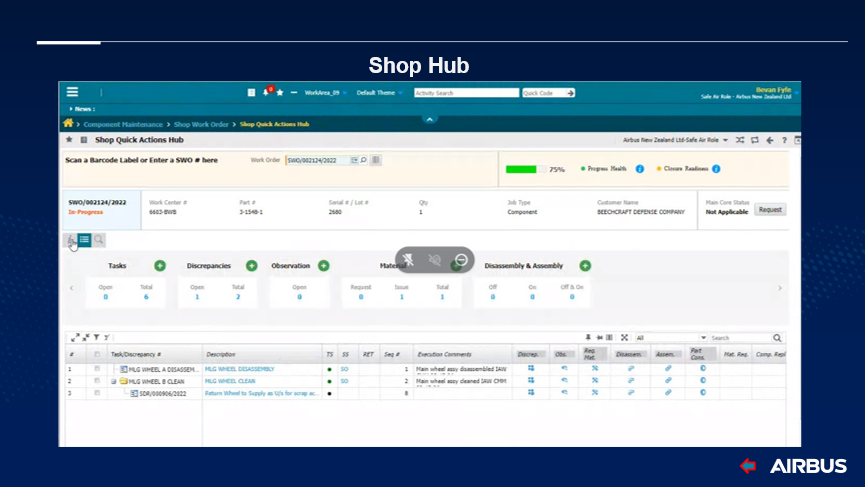
Figure 4
It enabled us to track a lot of the component work through the shops. If we remove a faulty component straight off the aircraft, we can send it straight into an ‘unserviceable’ warehouse where the option to send it straight on to the shopfloor for repair will appear and automatically creates an entry for us to carry out that maintenance.
Tech Records and Engineering Hub helped address one of the issues that we had early on which was that, with a lot of the engineering change requests, if there was something that we needed to defer maintenance wise, we were capturing a lot of that data just as a PDF in the system. That evolved later with the use of the Engineering Hub which had an actual workflow so that you could see the engineering requirement and then, of course, all of the workflow to see it signed-off. That was a big step forward for us.
Finally, the Dent & Buckle module. This was added at the RNZAF’s request. Early on and right up until recently, a lot of this work was being carried out with just marking all aircraft dents on graph paper.
Something else that Ramco did that worked out very well for us is that, during the system change, they enabled us to bring the RNZAF on as part of the journey, bring them into the system and give them access to views of what we were using so that they could see exactly what was going on the whole time.
AN OVERVIEW OF THE PROJECT AND THE FUTURE
We’re now at a point where we can evaluate how the whole program has gone. There were a number of pros that we have identified and appreciated as part of the project. These pros included weekly contact with our Ramco project manager and trainer, and an engaged workforce who were striving to learn how to do things better, plus the understanding that, while the basic system is easy to use, to excel, we needed to work on configuring the system.
The future we see as moving to implement Mechanic Anywhere and Touch Screens Apps which Ramco offers but we haven’t yet implemented. There’s also Authorisations Management. Furthermore, other Airbus sites in Australia are now looking to move from their current ERP systems where Ramco is one of the systems that they are considering.
IN CONCLUSION
In New Zealand, we are a small Airbus site at the bottom of the world with really big ERP capability that fits all our needs, that works well when it’s set up right and with a good understanding from both parties. Finally, future expansion is possible and very likely.
Contributor’s Details
Peter Buscke
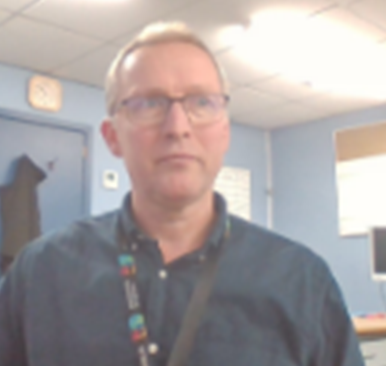
Starting in the Royal New Zealand Airforce, in 1998, Peter joined Safe Air Ltd, now Airbus NZ. Peter’s recent projects include SAP ERP implementation working on configuration testing and Data Migration. His current role is working as a Production Support Engineer carrying support work for the workshop floor engineers and planning team in the MRO environment. Peter also works as SAP support working on report development and ERP improvement and defect resolution.
Airbus New Zealand
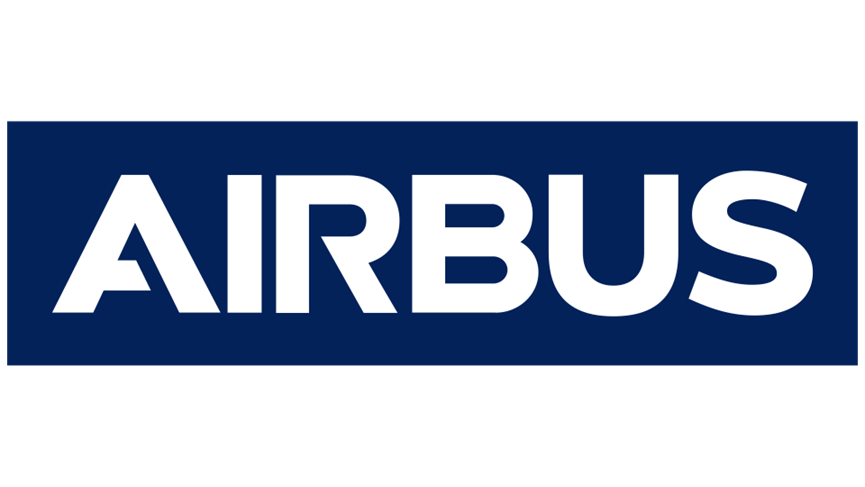
Airbus’s organisation in New Zealand reflects is another milestone for the business’s integrated services in the Pacific region supporting fixed and rotary wing aircraft in the defence and civil sectors. New Zealand is an important country for Airbus. The company’s MRO operations in the country are part of a regional services business in the Pacific that also includes facilities in Australia providing support for a wide range of helicopters and military fixed wing aircraft.
Ramco Aviation
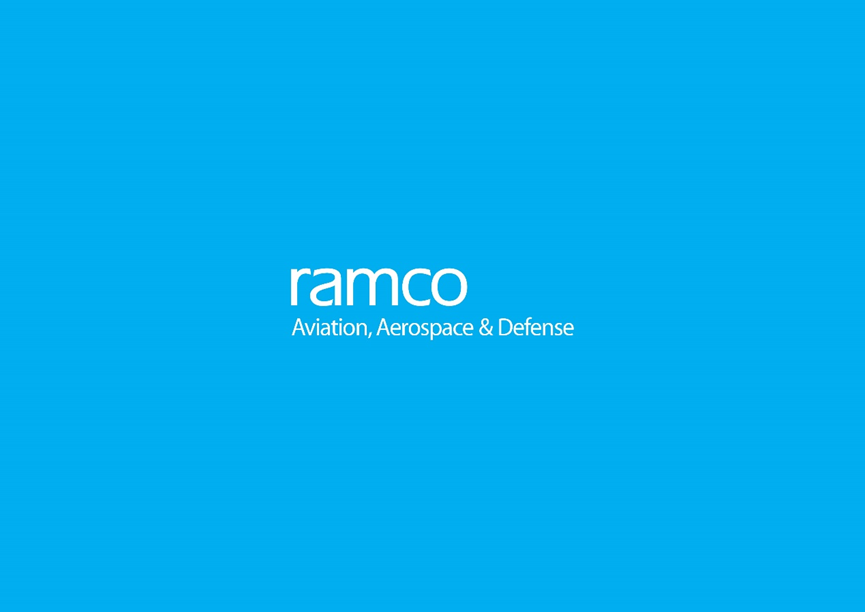
Ramco Aviation software is trusted by 24,000+ users to manage 4,000+ aircraft globally. With 90+ Aviation organizations onboard, Ramco is the solution of choice for top Airlines, 3rd party MROs, large Heli-Operators, leading Defense organizations, and major Urban Air Mobility companies around the world. Available on cloud, Ramco Aviation Suite provides accessibility with ‘Anywhere Apps’, significantly accelerating organizational efficiency and agility. Ramco is changing the paradigm of enterprise software with Artificial Intelligence based solutions, intelligent voice enabled user experience, and advanced features such as digital task cards, offline maintenance capability, conversational chatbots, HUBs and cognitive solutions
Comments (0)
There are currently no comments about this article.
To post a comment, please login or subscribe.