Articles
Name | Author | |
---|---|---|
What IT can do: The OEM perspective | Henrik Ollus, Customer Success Manager, QOCO Systems | View article |
Case Study: A lifelong digital maintenance record for aviation assets, Part 2 | Karl Steeves, CEO, TrustFlight | View article |
Case Study: Digital Transformation at Etihad Airways Technical | Eric Bogner, Manager Strategic Partnership and Performance, Etihad Airways and Arish Sayed, Manager Projects – Technical, Etihad Airways | View article |
Case Study: Enter Air’s post-pandemic upgrades are supported by a flexible MRO IT solution | Konrad Dymowski, Enter Air | View article |
Case Study: A lifelong digital maintenance record for aviation assets, Part 2
Author: Karl Steeves, CEO, TrustFlight
Subscribe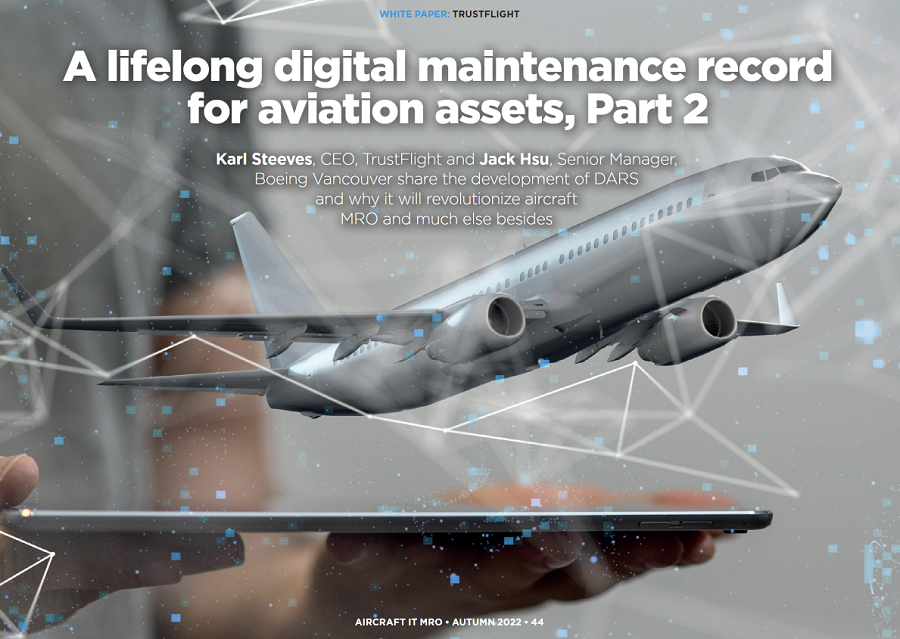
Karl Steeves, CEO, TrustFlight completes the story of development of DARS and why it will revolutionize aircraft MRO and much else besides.
In the Summer 2022 issue of Aircraft IT MRO, we looked at why DARS (Digital Aircraft Records System) was needed, who is involved in its development and what they each bring to the project. In part two, we’ll look at what DARS is, how it will work what will be its impact on the industry and how it can be implemented.
DARS (DIGITAL AVIATION RECORD SYSTEM)
There are two main components to DARS. One is more back-end infrastructure to support integrations between systems. In order to facilitate the transfer of data from an MRO which has one system where they’re tracking maintenance data versus an airline that has a different system, DARS facilitates the integration between those systems but also providing automation in terms of the audit and verification of that data. So, in a paper world, someone would have to go through and manually audit and check to make sure that the right items such as Service Bulletins (SBs) and Airworthiness Directives (ADs) have been complied with, DARS builds in technology to be able to automate a lot of that verification. That’s all part of the back-end infrastructure, the plumbing for the industry that will allow the data to flow between different systems: it’s not that exciting from an end-user perspective as it’s all hidden technology that users don’t see.
From a user perspective, the partners are also developing what they call digital workflow applications that sit on top of DARS. The ambition, ultimately is to have many different software companies and providers being able to build applications on top of DARS and the collaborators have started that with building the Digital Engine Log which will be used for managing engines. The initial focus within DARS will be on engines because they represent a mini-airframe in this context with the same technical challenges, the same number of stakeholders that need to be involved but engines are bit more manageable in terms of component numbers and complexity compared to an airframe. The program can then be scaled up. The Digital Engine Log is essentially a tool that will be used to manage engines within airlines and leasing companies to provide a lot of the ongoing quality and compliance information and automation to make sure that that engine continues to comply with SBs and ADs that have arisen for that model: what it will also do is make the onboarding and offboarding of those engines a lot easier than it has been. At the moment, for an airline that buys or leases a new engine, there is usually one to two weeks of work to get that engine onboarded into the system; all of the component data has to be uploaded with the current status of those components and current status of any modifications on the engine; it all has to come into the system and then all of the data has to be quality checked. DARS will reduce the onboarding time from one to two weeks to less than a day; a real saving because usually the airline is still paying for the engine in that time but cannot use it until it’s in the system in order for the airline to ensure full control of it from a maintenance perspective (figure 1).
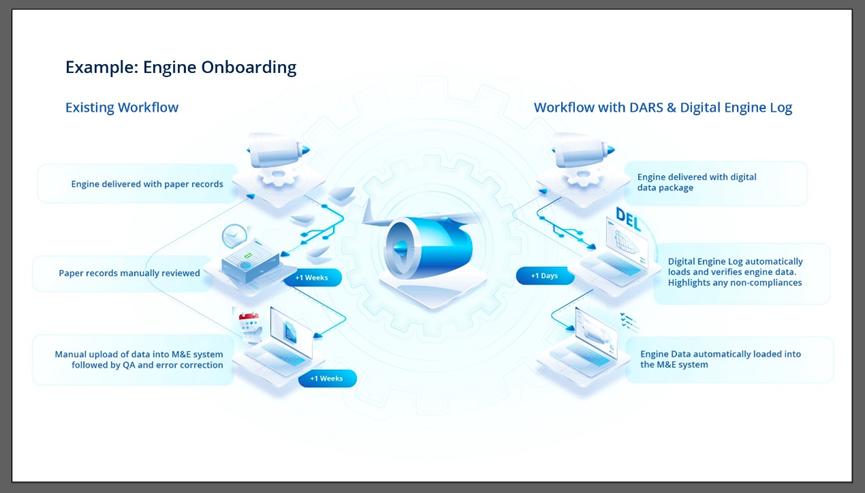
In a similar manner DARS will also speed-up the offboarding process. If an airline is selling or doing a lease return on an engine, there’s a huge amount of reporting that needs to be created to go back to the leasing company; but also, audit and verification on the compliance of that engine with lease and lease return terms. With DARS, that process will be automated.
This type of idea is one that people in the industry have been thinking about for a long time. TrustFlight commenced development on the project when they opened the Vancouver office in 2020. Part of what they applied for was called a Super-Cluster project, generally the Canadian Government is open to supporting projects like this, and so, from June 2021, the project got support from Canada’s Digital Technology Super-Cluster. That was also when the other partners got involved. Development of the systems is still underway with an intention by the beginning of next year, 2023, to have a launch customer for the Digital Engine Log and the underlying DARS system.
CHALLENGES FACED ALREADY AND ANTICIPATED
Between different systems, data is recorded and stored in quite different manners in different M&E and other systems being used; especially with organizations that are using generic ERP systems such as SAP which can create even bigger challenges on data standards because they’ll be whatever was decided when they implemented those systems. So, the project is having to deal with multiple systems, integrating those systems and figuring out how to get all the data to align and tie together. In the context where there might be a common component which was being managed in multiple different systems, having to tie all that together and make sense is a challenge, especially when there might be conflict between those systems. That’s certainly a big challenge but one that the project is spending a lot of time on and working through.
A large part of the solution is that, as the project team is getting more used to different systems and aligning everything into a common standard as well as leveraging some of the existing standards where they do exist. The ATA SPEC2500 and SPEC2000 standards are being used, but also other standards which aren’t so well developed. What’s also been interesting on the standards side is that a lot of the existing standards are built around replicating the paper way of doing things as opposed to being more forward looking and understanding what the benefits and opportunities that can be gained from having data stored digitally. For example, an Airworthiness Directive (AD) will have compliance information written into it which might be based on serial numbers so that all aircraft with the serial number will have to have the AD incorporated. Even things like that are not standardized today and computer programs have trouble working with different standards for the same thing. The DARS program is setting out, at that level, to align standards and design things for the future in order to be able to automate a lot of the processing of that data.
Another challenge is more cultural. As we’ve already said, the aviation industry is quite risk averse and is still at an early stage of digital transformation within the industry. So, trying to make sure that people understand the benefits and what can be gained from having new systems or better ways of doing things always comes up against a cultural barrier. Also, the industry is not that fast moving and a high turnover of staff in some businesses during COVID can mean that someone with whom there has been good progress on digital adoption either leaves or is replaced which slows things down.
Another obstacle has been that the industry often goes from feast to famine. One minute everything is going well and people are just making sure that aircraft are flying, day to day operations in which case it’s harder to get people to look long-term; then there is the scenario where, as in COVID when operations come to a complete halt, people get furloughed and no-one has the time or resources to be investing into long-term projects.
WHAT AIRLINES WILL NEED TO MOVE TO DARS
These days, most IT infrastructure is in the Cloud and most offerings are software as a service (SaaS), of which DARS will be one. So, users are unlikely to encounter any needs for new equipment in order to access DARS. There are not that many drastic changes required to make the move to the new system. The project is not replacing existing systems; it is more about building tools that fit into the processes where those existing systems stop, often at the interfaces between different organizations. Say an engine is going out to a shop visit to get overhauled, the work scope might be produced in an existing M&E system but, in many cases still, that will be within a separate Excel file; then all the way to providing that to the external MRO and then receiving the package once that overhaul has been completed with that package coming in as paper, which someone will have to type into the M&E system. DARS will replace that part of the process which tends often to be made up of manual paperwork. In terms of implementing DARS, the main thing that needs to be done is building interfaces with the existing systems that the operators or MROs will have. After that, it’s largely process changes from the old manual ones to using the new tool. A big system like AMOS will touch a lot of parts of an organization so they would be naturally reluctant to make a dramatic transition.
THE IMPACT OF DARS ON MRO/M&E FUNCTIONS
Technical records will be impacted by the move to DARS; at the moment, many people are still dealing with paper records and the move to DARS will make that process a lot more efficient. Also, general functions will be improved in areas such as asset management of airframes and engines. The asset management department which is responsible for managing leases, for example, and the general condition of engines, will be using DARS and specifically the Digital Engine Log, to manage the engines as opposed to the using the combination of spreadsheets and other tools as they do today. More generally, planning and forecasting will change on the maintenance side of the business but even on the operations side as well because, when we’re talking about the onboarding and offboarding of engines, that changes a lot of how things are planned. The fact that there will a saving of a week or two weeks on both processes will have a significant impact because, for instance, it might become possible to get rid of one or two spare engines that are no longer needed when, across a large fleet, there might with DARS be enough spare capacity within the engine pool to reduce the spares inventory. Usually, a fleet with 50 engines in service will keep around a further ten percent of that number as spares. If those five spares can be cut to three, that will be a considerable saving.
Longer term, as more data insights to the system are gained, things like reliability will also be impacted and some other parts. In the short term, a lot of the impacts will be on the process side with reductions in on/offboarding times and also general visualization and understanding of the status of the engines. There is, built into the tool, a timeline which shows what stage the engine is at so that it can be tracked throughout.
IMMEDIATE AND LONGER-TERM BENEFITS OF DARS
The immediate impact of being able to speed up the on/offboarding of engines will benefit both sides. For an MRO, there is currently a lot of work for them to generate the package once they’ve completed, say, an overhaul on an engine; that takes time and can, in some cases, delay getting the engine out of the shop and back to the airline. DARS will help speed up that process as well as the onboarding into the airline when they receive it back.
We’ve already covered the benefit to the spares inventory plus, on the offboarding side, being able to more quickly complete a lease return. An issue that many airlines currently face is that they have legacy fleets which they need to sell or to return to the lessor. Often, a rate-limiting step is assembling the packages and doing the return: DARS will significantly speed that process as well as helping to provide more proactive guidance as to whether an asset is complying with the lease return conditions. Separately from the regulatory side of a lease, there will also be quite a few different lease return conditions in terms of how much time is remaining on an engine, component requirements, modifications, service bulletin requirements. With DARS it will be possible to automatically validate all that and provide a guide as to how long it’s going to take to make that engine compliant for a lease return. That will provide real saving on not prolonging a lease return which is often where an airline incurs the cost of paying excess lease fees after the engine has left revenue service but has not yet been returned to the lessor.
The other area of benefit is in compliance and the auditing of records to make sure that everything is correct. Many of the errors that occur are human errors; automation of processes will avoid that. In the longer term, the ability to utilize the data, having more of a whole life history for an engine or component will provide benefit in terms of higher reliability and availability for those components. What is surprising at the moment is that about sixty percent of maintenance costs come from unscheduled events. One of the longer-term goals with DARS is to reduce that sixty percent as far as possible.
For an MRO using DARS, they’ll be able to process more work in less time with the potential to realize greater profit. Also, for OEMs, assembling documentation for new engines and new aircraft is quite a difficult process as they have to assemble material such as reports and compliance statements from multiple different parts of the organization. That takes time and is not error free using current processes.
REQUIREMENTS OF REGULATORS FOR DARS TO BE USED
In the short term, nothing is required for an airline or MRO to start to use the platform. In the longer term, the intent for the DARS platform is to be the sort of infrastructure which allows users to get away from paper records and that will involve the regulators because there will be a need to be able to recognize electronic sign-offs with maintenance records, which is the part on which Boeing is working.
Also getting more recognition of regulators within themselves: there’s a lot of work and inefficiency that gets generated at the moment when moving assets and components across jurisdictions. What a European country might have in terms of requirements might be different from what, say, Transport Canada requires; this is especially true when looking at modifications or changes that have happened to an aircraft or engine. Part of the difficulty with that is because the full history and timeline of a modification might not be known because it might be a surveyor or inspector in Canada has signed it off and said they’re happy with it but there might not be any supporting documentation for that. One intent with DARS is to be able to have that supporting documentation on the system but also to get the regulators to recognize that. So, if there is a regulator in one jurisdiction, they could look at a modification of change and see the background material and why this modification was accepted in another jurisdiction. Whereas today, it is often necessary to undo a modification or change in order to move an asset or component to a new jurisdiction.
Regulators themselves will also be set to benefit from the digital transformation enabled by DARS. Put simply, the role of the regulator is to maintain oversight of organizations within their remit and ensure they are complying with regulations. Today, this is mostly achieved by auditing: going into organizations and spot-checking records and processes to verify compliance. In organizations with manual and paper-based processes this is the only way to do it. However, DARS paves the way for what’s called continuous compliance. Already being rolled out in other regulated sectors such as healthcare and finance, continuous compliance involves using systems to constantly monitor data and automatically highlight non-compliances. This enables oversight to be achieved in a much more efficient manner, whilst also reducing the risk of non-compliances not being caught – a common event today as spot-checks are only carried out at a point-in-time, usually annually, and only targeting a small sample of records or processes.
NEXT STEPS
The major step will be the launch of the Digital Engine Log in 2023 and we’d hope to soon be able to confirm who the launch customer for that will be.
Longer term this is not just an initiative for TrustFlight or the other partners to do; it’s something that we’d want to be a cross-industry initiative with as many airlines, software companies, MROs and other industry stakeholders involved in building an ecosystem around DARS that will facilitate a lot of the transactions and management of maintenance data longer term.
Contributor’s Details
Karl Steeves
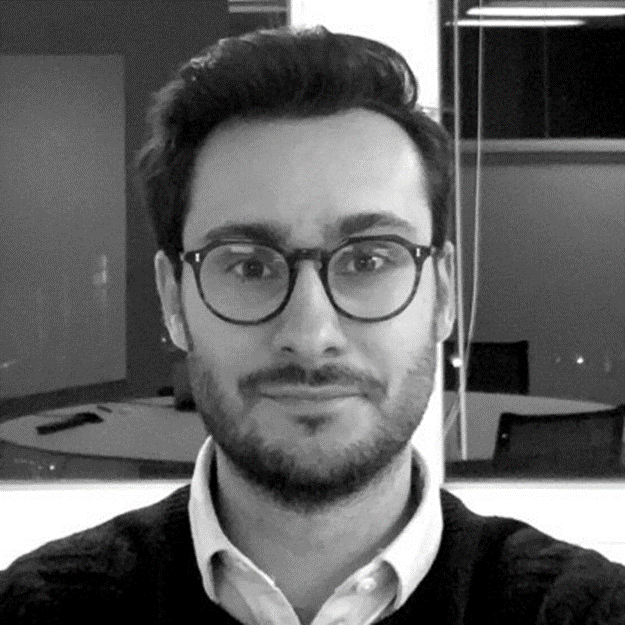
Karl is the CEO of TrustFlight. Graduating with a degree in Engineering from Imperial College London, Karl originally worked in creating safety-critical software systems for electric vehicles. He then went on to become a commercial pilot, and founded TrustFlight in 2017 with the aim of using software to improve some of the processes he experienced in operating and maintaining aircraft.
TrustFlight
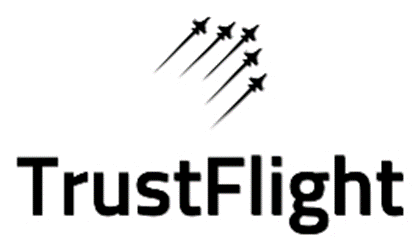
TrustFlight is a global provider of Digital Workflow Applications to the aviation industry including the class-leading Electronic Tech Log system and Operational Management system, Centrik. TrustFlight also provides innovative software-driven workflow support services helping aircraft operators and airlines to remove costly paperwork and associated errors, preserve aircraft value, increase efficiency and safety in aircraft operations.
Comments (0)
There are currently no comments about this article.
To post a comment, please login or subscribe.