Articles
Name | Author | |
---|---|---|
CASE STUDY: Etihad Airways bring cockpit and cabin logs together | Masoud Al-Alawi, Manager Aircraft and Digital Operations, Etihad Airways | View article |
CASE STUDY: Digitalizing the warehouse at Finnair and DHL Supply Chain | Otto-Wilhelm Orumaa, Operations Excellence Manager, Finnair | View article |
CASE STUDY: A Better Documentation Solution for Cebu Pacific | Hazel B. Ocampo, Manager – Configuration Management – EFM at Cebu Pacific Air | View article |
CASE STUDY: Joramco’s new system offers a better way of working | Shakespear Nyamande, Vice President of Planning at Joramco | View article |
CASE STUDY: A Better Documentation Solution for Cebu Pacific
Author: Hazel B. Ocampo, Manager – Configuration Management – EFM at Cebu Pacific Air
Subscribe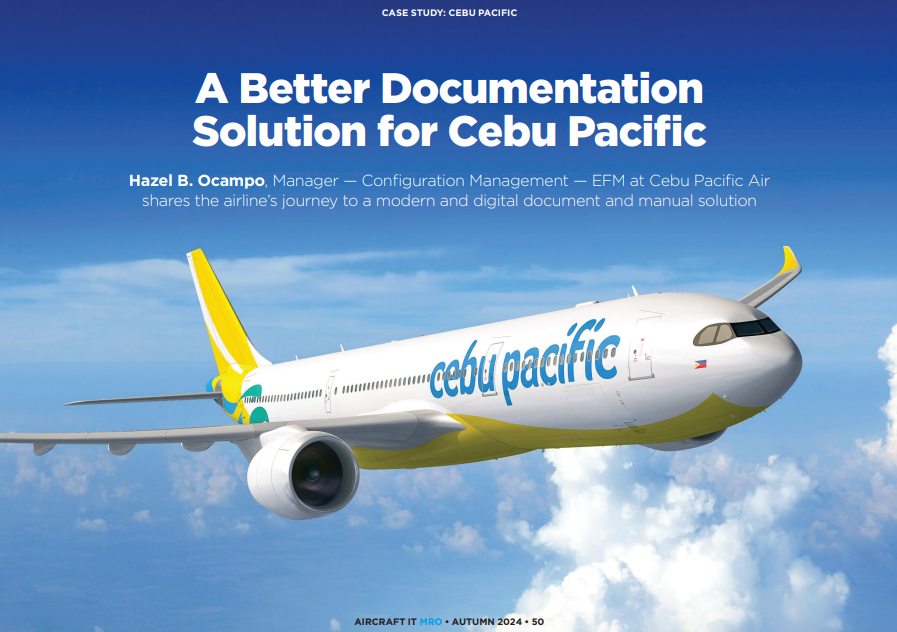
Hazel B. Ocampo, Manager – Configuration Management – EFM at Cebu Pacific Air shares the airline’s journey to a modern and digital document and manual solution
The value of a case study is that readers find out about a solution working in an airline environment. So before delving into the details of the solution, why it was needed, how it was selected, and what it has done for the airline, it’s always a good idea to find out something about the airline in question, in this case, Cebu Pacific.
CEBU PACIFIC
As the Philippines’ leading airline, Cebu Pacific, a low-cost carrier (LCC) founded in 1996, has one of the youngest fleets in the region and in the world with an average age of five to six years for 84 aircraft. Most of the fleet are Airbus A320 family and A330s, plus there are ATR 72-600 and ATR freighters in the fleet. The airline serves 13 international destinations across Asia and the Middle East as well as in Australia, plus 34 domestic destinations. There are seven hubs across the Philippines’ three main islands with the main one in Manilla. At Cebu Pacific we’re focused on sustainability and eco-friendly initiatives. In keeping with that, the airline took delivery of its first Airbus A330-900neo in December 2021 and there have been more deliveries since then with further deliveries scheduled: the plan is to have an all neo fleet by 2027.
Cebu Pacific does not carry out maintenance in-house; MRO and engineering are contracted to Aplus (Aviation Partnership Philippines), a sister company to Cebu Pacific. The 200 people in the Cebu Pacific engineering department are mainly technical services, component management and materials management. The department holds the contracts and the budgets for maintenance services from different vendors. The engineering department also includes configuration management, the technical records team, the planning team, logistics, engineering systems and safety standards. We ensure that Cebu Pacific meets all regulatory standards and requirements and is certified with IOSA.
HOW DOCUMENTATION WAS HANDLED BEFORE FLYDOCS
Before flydocs, our maintenance records were largely paper-based using simple Office Suite programs, such as Excel, with manual inputting of data. Documents were scanned into PDFs, arranged and indexed manually in folders, and saved on CDs. One hundred thousand documents (on average) for each aircraft were managed in that labour intensive manner with lengthy processes, and inefficiencies. A major pain point was that, whenever we needed information about an aircraft, maybe for lease return, audit or evaluation, we had to search each folder manually to access the records (logbooks, certificates, work packages, Airworthiness Review Certificates, Engineering Orders, Work Orders, etc). We were also paying for data storage and document imaging fees. Lastly, in the event of incomplete information or missing documents during lease returns, some personnel had to physically search for a required document, which sometimes took days. If the relevant document could not be found, the components in question would have to be recertified.
THE BUSINESS CASE FOR IMPLEMENTING FLYDOCS
The business case was viewed in the context of Cebu Pacific’s drive to become world class in maintenance and engineering; to further strengthen its core, efficiently manage key results and streamline processes to achieve objectives through digitization. Any documentation system selected would have to meet our requirements for several features:
- OCR and search capability;
- Quick and easy uploading;
- Secure data storage backed up regularly;
- Unlimited storage space;
- Be able to accommodate various file types (PDFs, images, Microsoft files, etc.);
- Allow adding remarks and annotations to pages;
- Document review/audit trail with user authorizations/privileges;
- Be able to identify and list current records vs expected DFPs (Dirty Finger Prints);
- Be able to identify DFPs with discrepancies;
- Have an AMOS interface;
- 24/7 customer support;
- Be able to grant third party access to CEB (Cebu Pacific Air) documents;
- End of lease transition capabilities;
- Time-efficient ‘back to birth’ records, build and audit, and documents retrieval;
- Paperless transaction within EFM (Engineering and Fleet Management), auditor and lessor (even in large files);
- Reduced effort during lease return and remarketing projects.
For Cebu Pacific, the cost savings and efficiency increases resulting from using flydocs greatly outweighed the implementation costs.
We were looking for a system that could easily retrieve records.
Our internal folder usually had limitations; we used CDs to serve as the back-up. We regularly requested additional space for a given folder or the creation of another folder (please see folder below). Eventually, we ended up of checking our budget for an additional server, our own iCloud subscription or a system like flydocs. Before, if the document needed to be saved in a network drive, and the file name being looked for wasn’t written on there, a manual review of all the individual documents in that folder was required. We needed a system with which we could easily build the records for re-delivery and, at the same time, a structure that enabled all airline departments to retrieve the data they required, even if the individual seeking the data is not in the records department. The system selected was flydocs.
IMPLEMENTATION AND LESSONS LEARNED
Prior to the commencement of the project, a plan for implementation was created and followed. This involved uploading key components, certificates and search functionality before Go-Live in March 2021. We then rolled out further document uploads, current status, functionality, complete in-house and OEM publications, assigning workflows and finally templates with e-signature which has been ongoing since the end of 2023.
Event | Remarks |
CEB Components Certificates Uploading by Techstore | Started Jan 21 2021 through FSCC (Flydocs Server Control Centre) |
SEARCH Tab to all Engineering Section | February 8 2021 |
Go Live Flydocs | March 15, 2021 |
Long term Contracted MRO flydocs Implementation | Uploading of complied documents using FSCC |
MRO Station hub in Philippines Flydocs Implementation | April 5-7 2021 WP/DFP through FSCC or Scan at Source Email Process |
Current Status List | Manually updated by the team and usually performed six months prior to Aircraft induction and to End of Lease. |
flydocs Documentation Management | Cebu Pacific Technical Library completed the migration of in-house publication and OEM Publication in flydocs on 27th May 2021. |
Assigning and De-assigning Workflow | Activated last 27 May 2022. This will help to manage WP in AMOS and flydocs |
Airworthiness Review Center | Established last 20 December 2022 for the consolidation of documents required for aircraft Certificate of Airworthiness renewal. |
Template with e-signature | Ongoing; this started 28 December 2023. |
We learned lessons from our earlier implementation of AMOS, where we handled everything – including data migration – within the EFM department. When it came to implementing flydocs, we decided to get one representative from each of the project teams; the engineering system, Records and the IT, and focus on AMOS-flydocs system interface, process flow, and testing with the guidance of flydocs Onboarding Manager. The data migration to Digital Records Management was contracted out to flydocs to save time and manpower. This included proper tagging of the documents (C-Checks, Line Maintenance, logbooks etc.) and included five aircraft current status list build-ups.
We staggered the implementation program, starting with our technical stores’ for uploading of component documents. After that, we involved Aplus, CEB main Line Maintenance MRO for the scanning of complied documents and uploading to flydocs based on the structures that flydocs recommended.
A future project on the horizon is working towards running Spec2500 interface which includes even further benefits around automating compliance processes, for example the auto export of compliances list from AMOS to flydocs with no manual intervention, and auto updates of component counters based on asset utilization. There will be no need to manually attach documents as flydocs will automatically link related/exact documents based on compliance metadata, helping to save time.
HOW flydocs WORKS AND ADDRESSES IDENTIFIED PAIN POINTS
The flydocs solution is designed to significantly improve the quality and structure of stored records via a secure, digital interface. Processes that were previously long and complex become much simpler through automation, a key piece of the puzzle for busy Technical Records teams who can focus on other high-importance tasks. The value of flydocs really becomes apparent when used long-term, as new, faster processes can become established and allow for efficiencies to be found across the entire asset lifecycle. Using flydocs is a great step for airlines looking to start their journey towards paperless, digitized operations.
Rather than searching each folder manually which previously had taken days, Digital Records Management allows for fast searching of documents through OCR and Metadata technology that recognizes keywords and phrases throughout. This alleviates a major challenge, as teams no longer spend vast amounts of time looking for a single record. URL links can be provided to anyone who needs access and there is easy visibility of current status. FLYsearch helps us to consolidate records required for re-delivery, while flydocs Reports helps us to monitor individual deliverables. Internal Excel listings can be uploaded in the MID (Manage Internal Documentation) module for common references, accessible to authorized users.
Among the solutions that we considered, flydocs came out on top for three main reasons. Firstly, the search functionality which means that, not only can users instantly search scanned records, but the automatic optical character recognition (OCR) technology allows users to electronically select and search characters, not just file names. Secondly, the automatic indexing and sorting of documents is really simple to use, including a drag and drop feature for PDFs. Finally, flydocs partnership with AMOS allows each MRO work package to be exported automatically from AMOS to flydocs.
Through structured, organized, and industry-formatted data within flydocs, we can easily monitor any missing documents and there is a faster retrieval of records. Multiple departments can use Digital Records Management as their source of truth, meaning that anybody who requires access to documentation can do so easily. flydocs have also been open to discussing our feedback and some modifications we suggested to enhance the functionality have already been included. With flydocs focus on creating robust, automated, and accessible digital records, it provides a solid foundation for areas like inspections and re-deliveries.
Did flydocs’ implementation require any process changes?
We needed to ensure our system of file naming was consistent while scanning to ensure it could be matched with our on-base records indexing. The good thing is that file names do not hugely matter because of the OCR technology can find a document by ‘reading’ its scanned qualities – similar to using Google. Now, we don’t need indexing for scanning.
We also had to first scan the work packages to follow the flydocs structure which was a change in our process but it’s doable as this was part of the MRO data preparation requirement. A great process change for efficiency was personnel from EFM department (technical services, planning, MCC) no longer need to send us an email to retrieve a complied document. Instead of exchanging emails with attachments, we now just supply them with access to flydocs and they can do their own search and they can do sharing through a URL link to everybody with or without access.
CHALLENGES ENCOUNTERED DURING IMPLEMENTATION
When we started using flydocs on the ‘A’ Check packages, there were a lot of work orders and initially some of them were not able to be automatically attached. We adjusted some of the metadata and sent some of our engineering work orders to flydocs, and a sample of dirty fingerprints from the different MROs used by Cebu Pacific. Having done so, everything has gone smoothly so far and the testing has produced the results that we expected. The implementation took just over 15 months starting in the third quarter of 2019, when the project was awarded clearance, and running to the go-live in February 2021.
We were keen to run training during implementation to bring other staff members into using flydocs, build user access rights and understand which processes were most important to bring in. As this started during the pandemic, flydocs provided short online training sessions and the support team are always there to help us with urgent queries. After that initial training, we were able to create manuals on how to use flydocs Digital Records Management.
For new users, the navigation of flydocs extensive features can appear challenging – particularly compared to an embedded process, no matter how inefficient this may be. However, once they have become familiar with the system, flydocs demonstrates efficiency, significantly improving the speed and ease of organizing and locating files.
CHANGE MANAGEMENT
The teams generally were excited, but hesitant as they assumed that AMOS would provide them with the information they required. Users also still wanted to rely on the technical records team.
With the help of the management, our goal was to digitalize everything, and we did manage to convince affected personnel/groups. Having flydocs allows all users to have access to all the information related to the keyword they are searching; giving them broad information in their analyses. So far, aside from our internal processes we have not required any changes to our structure. Some teams do not need to access flydocs directly; if they’re in AMOS, they can get the data that they need, thanks to the platform’s integrations. For the regulatory authority, we submitted a letter for electronic records management and the associated procedure manual, aligning with local regulations and requirements.
A SUMMARY OF BENEFITS GAINED FROM IMPLEMENTING FLYDOCS
Cebu Pacific has embraced digital transformation by upgrading its documentation processes to enhance efficiency, ensure effective aircraft maintenance and operational processes, ultimately improving safety and service quality. Key upgrades in the Engineering Department include the implementation of an Engineering Computer System, Electronic Records System, RFID Lifevest System, AMOS Mobile, and an E-Technical Logbook. Additionally, Cebu Pacific is open to exploring ideas related to FlyCI and Life Asset Management.
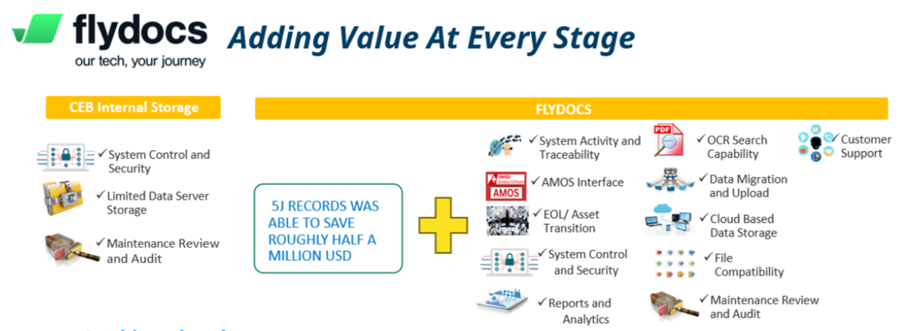
Benefits:
- Digital Documentation: Reduced paper-based processes, allowing for efficient storage, retrieval, sharing of aircraft documentation and providing easy access to review documents for correctness and completeness.
- Improved Maintenance Management: Streamlines maintenance forecast processes and automates document management tasks reducing downtime and administrative task.
- Real-Time Data Access: Provides access to up-to-date information on aircraft status, maintenance history, and parts availability, enhancing decision-making.
- Regulatory Compliance: Helps ensure compliance with aviation regulations by maintaining accurate records and documentation of maintenance activities.
- Integration: Can be integrated with other systems for comprehensive data management across various departments.
- Cost Reduction: Minimizes costs associated with physical document storage and management while enhancing productivity.
LESSONS LEARNED
So far, the plan to stagger the implementation of flydocs has worked well and while we still do call them from time to time for support., we continue with the same processes as before but now in flydocs. And, whenever in the future we implement new systems within Cebu Pacific, I recommend that we follow how we managed the flydocs project. It worked and all involved now have the skills required.
Since we first saw flydocs in 2017, it’s had lots of upgrades, and their ethos of continuous improvement means there are always new features in the pipeline. We had initially decided to wait a while before getting a new records documentation system, so when the time came, we looked into the market to see which system was best for our purposes and provided all our requirements, which was flydocs.
To summarize, flydocs has and can give us: the ability to share significant records with lessors through the delivery bible; automatic transfer of components documents from AMOS to flydocs; AMOS Mobile and eTechLog workorder transmission to flydocs; and storage of metadata instead of scanned documents.
Going forward, we are planning to contract out the upload of records to flydocs to the CEB contracted MRO for Base Maintenance Records and/or third party engineers to migrate the aircraft’s historical records into flydocs. It is very easy as we have the delivery docs files and the maintenance history file which are portable for third party use. We also use the redelivery binder internally to support our processes.
Now, we can measure how many work packages are still missing from the aircraft’s records and, for the end of lease, the time spent on collecting the records has already come down one third, from six months to four months due to easy retrieval. This has been our experience at Cebu Pacific and I hope that it proves useful information for any reader considering a similar project.
Comments (0)
There are currently no comments about this article.
To post a comment, please login or subscribe.