Articles
Name | Author | |
---|---|---|
Column: How I see IT | Allan Bachan, VP, Managing Director, MRO Operations, ICF | Kyle Tuberson, Chief Technology Officer, Public Sector, ICF | View article |
What IT can do | Henrik Ollus, Customer Success Manager, QOCO Systems | View article |
A new MRO IT solution for AISG’s multiple locations | Alejandro Bravo, Sr. VP Production Control & COO, AISG | View article |
Planning for a digital future | James Angus, Commercial Director of the Integrated Vehicle Health Management (IVHM) Centre at Cranfield University and John Maggiore is a senior aerospace leader, executive consultant, and digital transformation expert at Cranfield University IVHM Centre. | View article |
HAECO embarks on an MRO IT upgrade | Teresa Cheung, Assistant General Manager, Centre of Excellence & Cathay Operations, Line Maintenance and Christine Yung, Leader of the AMOS Competence Excellence team, HAECO Hong Kong | View article |
ATR steps-up to a modern MRO IT solution | Patrick Massicot, Head of Airframe & MRO Services, ATR | View article |
ATR steps-up to a modern MRO IT solution
Author: Patrick Massicot, Head of Airframe & MRO Services, ATR
SubscribePatrick Massicot, Head of Airframe & MRO Services, ATR shares a great experience of ATR’s implementation of a new MRO software solution
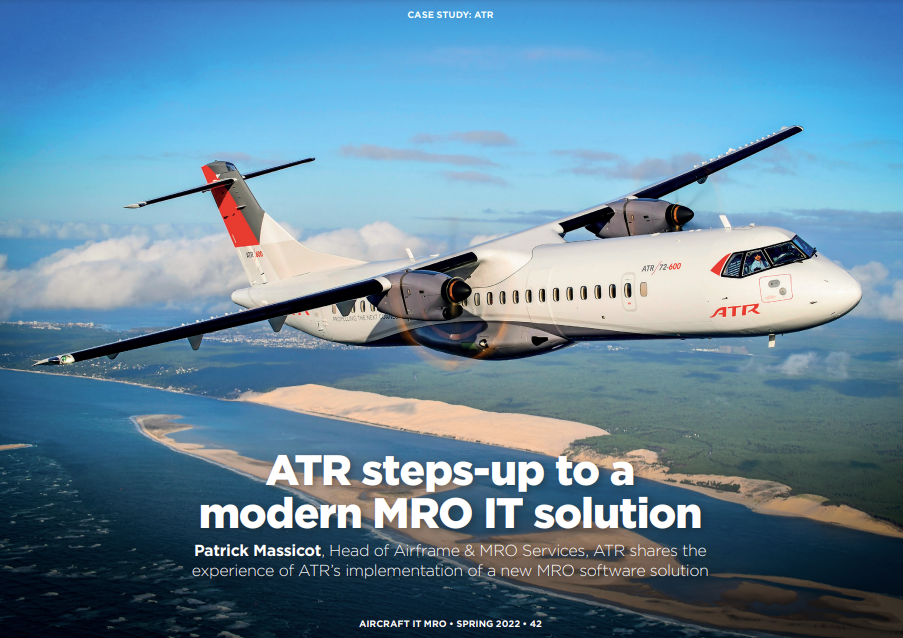
It’s always good to be able to share, with colleagues, information about common workplace issues. In that spirit this article will endeavor to share with readers how ATR came to decide on the need for a new MRO software solution, how we selected the right partner for our business, the implementation and what ATR has gained from the new solution. But first, let me tell you something about ATR, the business whose experience forms the basis for this white paper.
ATR
ATR, is not only a renowned aircraft manufacturer serving roughly 200 operators on a worldwide basis, but is also a major support and service provider. The range of services covers spares and tools, either on a spot basis or under a PBH (power by the hour) scheme, retrofit solutions, extended training services and airframe maintenance and CAMO services on a worldwide basis. To support our airframe maintenance which is mainly oriented to perform damaged aircraft repair and is also called Working Party and CAMO services, ATR has run its own maintenance facility in Toulouse area since June 2017 under a very standard MRO model.
As both a manufacturer and an MRO for ATR aircraft we deal mainly with damaged aircraft needing major repairs and we have highly skilled structural engineers interfacing with the engineering department; this is the core activity. But there are some customers who prefer their ATR aircraft maintenance to by carried out by ATR, including scheduled maintenance and SB (Service Bulletin) and STC (Supplemental Type Certificate) related work. The split is something like 80% major repairs with 20% of standard or scheduled maintenance.
THE CHALLENGES
The first thing to consider with any change such as this one is to ask why do it and, in that context, there were a number of issues in the business that led us to decide that ATR needed to investigate a new MRO Solution?
To support the ATR Working Party organization, which activity has been steadily growing during the last few years, and to build a robust CAMO department, formally established in 2017, a transformation plan was launched few years back. The transformation was contemplating extended training plan of the team, significant industrial investments, and IT tools deployment. The purpose of this last topic was to strengthen our processes and information approach while standardizing flows of information, sharing and securing data. As a significant portion of the team already ran some MIS (Maintenance Information System) in the companies they were previously working for, an IT mindset was already in place.
ATR then launched a formal RFP (Request for Proposal) to evaluate and qualify different MIS solutions with very stringent requirements about 24/7 availability, full Web compatible architecture, ease of training and deployment, as well as data upload capabilities on top of standard features.
THE SELECTION PROCESS
Through the RFP period, not only the features proposed by the MIS, overall architecture and pricing conditions and model were evaluated but also that the potential supplier should understand the customer’s mindset and had the ability to properly understand our planning and resources constraints. Whereas several suppliers proposed a heavy, long and costly project management approach, ADSoftware offered a very agile service and proposed workshops based on real data upload and real case studies to evaluate the package. This was successfully conducted in a couple of days based on a set of data (XLS spreadsheets) provided by ATR. The cost of the overall package (license, training, data upload, features enhancement) was also an obvious contributor to the final decision to go with ADSoftware.
IMPLEMENTATION
The RFP specified some features, architecture (Web was a must have), and the agility to run workshops as well as data upload, a case study and training. Deployment planning was proposed and shared with ADSoftware to organize the required training plan. The plan agreed was made up of theoretical training sessions, data uploads (which were qualified) and then a switch to a run mode with on-site assistance of ADSoftware team.
The full solution, meaning all modules, has been contracted and deployed throughout the project lifecycle. We started with the ‘easy piece’ which was the set-up of a dedicated tools inventory, including life limit control and standard procurement / material management features. Then training for our Planning and Production department started to secure good preparation and management of complex work packages. As our core activity is to repair heavily damaged aircraft, we can easily manage complex work packages including more than several hundred tasks.
Once the ‘core’ functions were deployed within the organization, we moved several steps forwards through different internal projects, supported by ADSoftware. This included deployment of the production module, to secure technical staff technical licenses and training management alongside assignment of our workforce to maintenance tasks (work orders) and recording of production time. Based on that, at least a weekly update is shared with our customers when their aircraft are undergoing repairs. The production module is also strengthened by the integration of ATR’s Quality Department which is responsible for technical staff licenses management and renewal, including for our few sub-contractors.
In addition, the MIS is also deployed within our CAMO organization. Specific developments have been made to ease the upload of information and data processed when ATR CAMO is doing an aircraft recovery or airworthiness review so that aircraft and component configuration, maintenance program, SB & AD will soon be managed in a more business-like manner.
On top of that, and as ATR also leases or sells what we call ME or Main Elements (engines, propellers, landing gear…), the airworthiness of these ME which are located in our different warehouses (Paris, Singapore, Miami) is currently supported by ADSoftware MIS in full integration with ATR’s Spares and Supply chain department.
The next step, that we are just starting, is to track our costs on three axes (production, spares and services) to ensure a proper cost control of any project and compare then to our initial commercial proposal and business case.
ADSOFTWARE AIRPACK: AIRTIME, AIRSTOCK AND COST MONITORING
[This space is where ADSoftware can enter a brief (c200 words) outline of Airpack and the modules that are in use at ATR. Also, if any screen shots are available, one or two that go with the text would be welcome.]
THE IMPACT OF COVID-19 ON THE PROJECT
From an ATR perspective, almost no impact from COVID as the core modules were already deployed and support was still available. ADsoftware was sometimes struggling with a few colleagues leaving the company, so some minor developments were delivered a little bit late, but nothing major nor impacting our activity.
OTHER AND MORE ROUTINE CHALLENGES
Having the whole team engaged with such a major project is key and this was quite easy at ATR as most of our colleagues already had some experience on different MIS. Then, ensuring a proper communication and understanding between ADSoftware and ATR could have been a challenge but we realized that you must make sure that each listens top the other and understands the challenges and projects to be achieved. So far overall cooperation is good.
TRAINING AND USER ACCEPTANCE
Training was organized per service starting with data upload or initialization when required. Theoretical training was then performed on a test database fed with real data. Once the team had been trained, the switch over to the production data base was made, what we called a run mode, with an ADSoftware trainer on site to secure a very smooth transition.
As Airpack (the name of the MIS) is very close to other major MIS in terms of terminology and architecture, deployment was not difficult. Transition to a full new web interface definitively improves the overall perception and user-friendliness of the entire solution. Overall, the reaction of users was good with some specific attention to the deployment of the production module. It is no secret than setting up a major and integrated IT solution brings some constraints and forces you to potentially rethink your processes and some priorities but we did not face major challenges there. When the production module was deployed not only in our hangar but also on remote sites, our colleagues made some comments and recommendations to improve some transactions. This was translated into a document shared with ADSoftware and a new version was deployed encompassing these improvements.
ATR is still working closely with ADSoftware and, when there is the requirement for a new feature or an improvement to, say, the back-end, we are very quick to share that with ADSoftware and, if it is something that is chargeable, we might pay for it but, if not, it will be part of the IT life cycle plan; either way, ADSoftware is quick to provide updated solutions and versions. They are very agile in their reactions and that speed has a value of its own.
REGULATORY APPROVALS
Regulators were informed about the integration of our new MIS and recognized it as a source of major improvements. ATR being not only an OEM working under EASA approval but also with different foreign Authorities, we are very frequently audited and our OSAC (Organisme pour la Securite de l’Aviation Civile), the arm of the French regulatory body, mentioned our MIS as a very reliable and structural pillar of our maintenance organization.
The MIS was evaluated, from an architecture perspective, and qualified by our IT department. It was a requirement for us that MIS should be able to be run on any PC with absolutely no impact on stringent software configuration and IT safety rules, especially in our FAL (Final Assembly Line) hosted by Airbus and where ATR aircraft are manufactured. This was a seamless approval.
LESSONS LEARNED
So, what have been our take-aways from the whole process at ATR?
Maybe to take more time to think about the impact on internal processes. Also, a deeper evaluation of the users’ manuals (see below) and standard operating procedures is something which is worth evaluating as this supports good training, deployment and transfer of know-how between the MIS editor and the Customer. But, overall, for both ATR and ADSoftware, I don’t think that we made any big mistakes neither did we face any major challenges when deploying the solution whether that was related to data qualification and upload or to the initial curriculum training plan so I doubt we would change much at all if we had to do it again: what we did was quite efficient.
Maybe we should have given more thought to the quality of the users’ manual which could be improved. Because we had to take some time to re-define some standard internal operating procedures, where we were expecting to have state-of-the art users’ manuals. This is something that we should evaluate if we had to do it again and on which we should have spent more time.
If we were to offer any advice to another MRO considering a similar implementation, I’d say map your different data sources, qualify them to define which data is reliable or is worth being processed before you enter into the MIS journey. Inform your entire organization about potential impacts but, most important, inform them of the benefits that the company will gain from using an integrated MIS.
Make sure what you pay is in line with what you need. For ATR, there was really no need to have a consultant on site during six months to supervise our organization, processes and data and define an action plan. As we are a small but very agile MRO and CAMO organization, this was done internally by very key and committed people with very high skills.
BENEFITS GAINED
When a business deploys a major IT solution like an MRO information system, it’s really all about standardization of processes, methodology and data. The issue that we had before deploying this solution at ATR was that we were using very standard Excel spreadsheets that had been developed, run and customized by many different colleagues on different PCs: hence there was absolutely no integration of any kind of data as a result of which, it was not possible to share, say, a return on experience of data. That resulted in a loss of energy and a loss of value for the organization. It’s about making sure that everyone is sharing the same and qualified information using IT solutions and data and that everybody is going to run the application under the same standards, meaning that, at the end, there are standard processes throughout the organization. That, along with standard and secure data, is a key benefit of having these sorts of IT solutions in place. Definitively this is all about the standardization of process, methodology and secured data to avoid each individual having their own set of data and, potentially, method of work.
Having been running the new solution for two and half to three years now, where we are is very close to the plan that we made in terms of standard processes, organization and securing data; and the team has been positive about the deployment of this kind of solution. Also, thinking about the people who are fixing the aircraft, their job is to repair aircraft and undertake maintenance and not to be typing on keyboards. But actually, the way the solution is designed and the way we have organized the set-up of the ADSoftware solution in ATR is that most of the production people are, in the end, entering very few data on the MIS; so, as much as possible, we are recording real-time data when it comes to production. However, there are back-office people re-typing some data which we are manually inputting on work orders for example.
NEXT STEPS AND FUTURE PLANS
ATR has acquired the eDamage module that will be used by our Part 145, CAMO, Working Party representative and our colleagues in the FAL (Final Assembly Line). The purpose is to track from the very early stage any dent and buckle and trigger proper maintenance actions in a full end to end approach.
Also, we have started a small project team deploying a cost monitoring module because, the bottom line is that we are selling services so must be able to identify some benefit from that. Cost control is a key activity. Once everything has been set up in terms of supply chain, material management and production, the next consideration is the dollars or euros for which cost control is a key step that has to be addressed and tackled. So, that is what is currently being done and for which we have received a new cost control module which, at the time of writing, was being evaluated not only within my department but also in cooperation with the finance department. One of the main intended outcomes is to have financial reports and we have to be sure that those financial reports are providing accurate, readable and understandable data.
For the next step after that, which is running almost in parallel, ATR has acquired a new module, the eDamage module, the purpose of which is to use tablets to record remotely from close to or even on board the aircraft, minor damages, dent and buckle, which are sent electronically to the back office of the engineering department so that, from Toulouse, we can assess what is the extent of the damage on the airframe, and provide some repair solutions direct from the ATR head office.
This module will not only be used in Airframe & MRO Services to address major aircraft repairs but is also going to be deployed in the final assembly line for new aircraft. On new aircraft the dents and buckles are minor but they do happen and that is something that ATR needs to address to ensure that new aircraft delivered are one hundred percent perfect.
ATR is both an MRO and an OEM but the primary activity is to design and build aircraft. So, when we are proposing and implementing these types of solutions, we have to take into account different parts of the organization such as Quality and Production, which means it will probably take a few months to deploy everything, to buy equipment such as iPads, and to define all the parameters and technical information that we want to track and manage. It’s not a long-term but is a medium-term project which will take something like six months.
SUMMARY
The project was well managed by both parties, ATR and ADSoftware. It’s good that we are interacting more like partners, meaning that when, for instance, there are new features to be developed, at ATR, we are proactively proposing new developments which are shared with the user community. It means that we contribute to the ongoing evolution and improvement of the global solution. That is something that we were expecting from the ATR perspective but which is sometimes quite difficult to do with larger MIS editors because they have their own development plan which making it sometimes quite difficult to interact with that plan and to be part of it.
Contributor’s Details
Patrick Massicot:
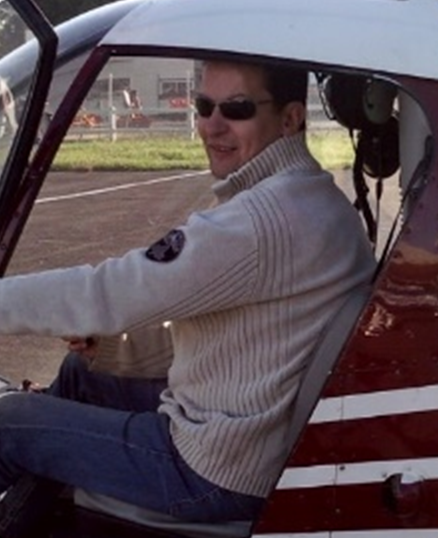
Patrick is a graduate aeronautical engineer with a more than 30 years’ experience in aviation and aircraft maintenance and operations, and more than two decades working with MRO, lessors, regulatory bodies, civilian and military operators, flying fixed and rotary wing aircraft. He gained a thorough knowledge of Maintenance Information Systems, as the Head of Sales & Marketing for a major supplier before joining ATR. Patrick now leads the Airframe & MRO Services business unit at ATR providing maintenance and CAMO support, and services to ATR internal and external customers worldwide.
ATR

ATR is the world’s number one aircraft manufacturer in regional aviation providing a new generation of turboprops up to 78 seats. Since 1981 we have built and delivered aircraft to over 200 airlines, in 100 countries. Our efficient aircraft have been designed and built around turboprop engines to burn less fuel and emit less CO2 than a similarly sized regional jet; access challenging terrains; and contribute to sustainable aviation.
ADSoftware
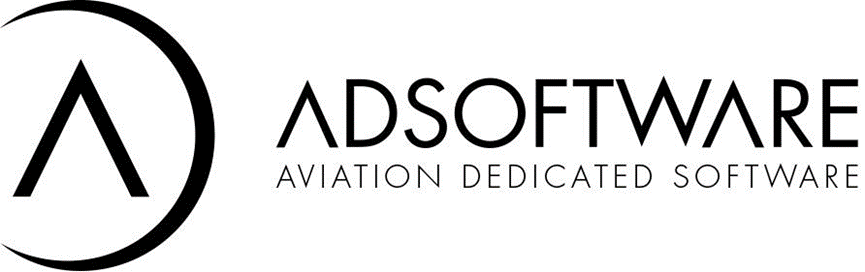
ADSoftware offers a fleet management system and logistic package called AIRPACK which meets the needs of aircraft and helicopters operators, as well as MRO and CAMO centers. It provides modular ERP solutions to more than 50 clients worldwide for fixed wing and helicopters maintenance. The strength of ADSoftware is the simplicity of its product. ADSoftware solutions incorporate aviation regulatory requirements with state-of-the-art IT tools plus innovative mobile and cloud solutions, recognized with several European awards.
Comments (0)
There are currently no comments about this article.
To post a comment, please login or subscribe.