Articles
Name | Author | |
---|---|---|
White Paper: A more efficient maintenance data standard | Iryna Khomenko, Manager, Operational Efficiency, IATA TechOps | View article |
White Paper: A lifelong digital maintenance record for aviation assets Part 1 | Karl Steeves, CEO, TrustFlight and Jack Hsu, Senior Manager, Boeing Vancouver | View article |
Case Study: All change for the better at Mexicana MRO | Enrique Guido, CFO, Mexicana MRO Services | View article |
Case Study: Increasing engine on wing time at Neos Air | Ivan Albini, CAMO Postholder at Neos Air and Ville Santaniemi, Senior Partner at QOCO Systems | View article |
Case Study: All change for the better at Mexicana MRO
Author: Enrique Guido, CFO, Mexicana MRO Services
SubscribeEnrique Guido, CFO, Mexicana MRO Services shares the experience of finding and implementing a new MRO IT solution from EmpowerMX
This is the story of how the leading Latin American third-party MRO business realized that a new MRO IT solution was needed, selected the right one and implemented it. However, before we launch into the substance of this case study, it will be useful to understand about the subject business, Mexicana MRO Services.
MEXICANA MRO
Mexicana MRO Services used to be Mexicana MRO Airlines’ Maintenance facility. Mexicana, based in Mexico City’s Airport, was the largest and most experienced airline in Latin America. Its MRO facility was the fourth most experienced in the world, Mexicana having created a maintenance facility in 1921 to Services its fleet. Following some corporate changes, and as a result of a successful spin-off, Mexicana MRO Servicess was created as an Independent Business Unit and transitioned from the division of an airline to a stand-alone MRO in 2015. In 2019, Emilio Otero was asked to take over as CEO and began to transform the organization to what it is today; a thriving company providing world-class maintenance and cargo conversion Servicess to the aviation sector. Mexicana MRO Services is the only MRO in the region with 18 different certifications from regulatory authorities around the world, the USA’s FAA and Europe’s EASA to name but two. Also important is that Mexicana MRO Services is certified by Airbus as an Official Airbus Maintenance Facility.
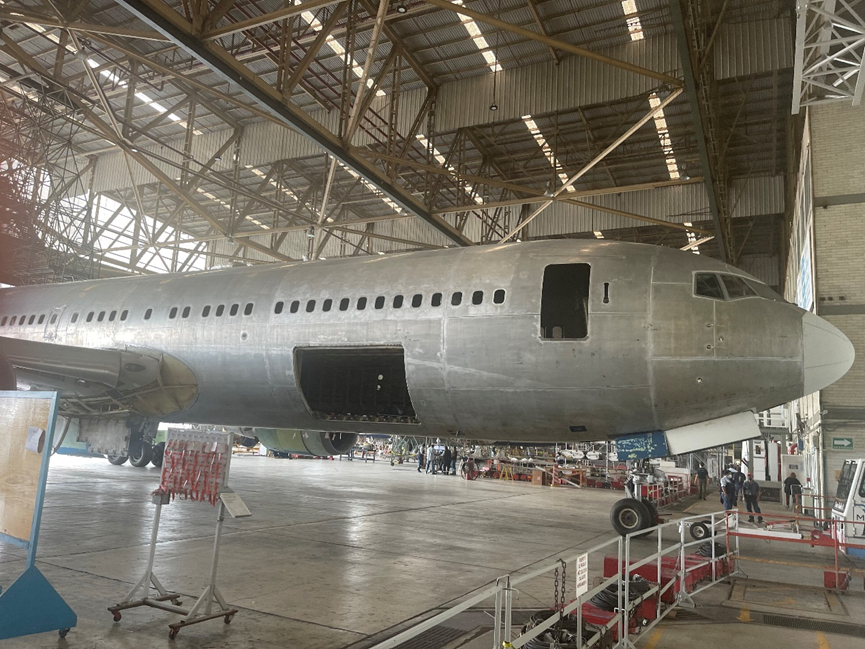
There are seven production lines in two hangars completing around sixty Servicess each year. Additionally, there is line maintenance delivering overnight Servicess for more than twenty aircraft a night. The business can handle a mix of wide bodies and narrow bodies, currently 50/50, including the A320 family, 737 family and 767 as well as A330. Since 2017, two of the lines have been working on passenger to freighter conversions, in association with IAI of Israel.
THE DECISION TO IMPLEMENT A NEW MRO IT SOLUTION
At Mexicana MRO Services we consider it a fundamental part of our strategy and a pillar of our philosophy to maintain constant communications with the customer and provide state-of-the-art Customer Services. We are constantly looking for ways to work more efficiently and better ways to improve our processes.
Originally, Mexicana MRO had developed an MRO IT solution in-house but we realized that it was not up to the best standards in the sector and didn’t allow us to realize the efficiencies that we wanted. We wanted to improve our internal processes and to be able to offer customers Servicess of the latest quality. That was why we were looking for new MRO IT solutions. In pursuit of that, a number of solutions were considered and evaluated against Mexicana MRO Services’s corporate objectives which were, to drive operational efficiencies, attain the highest accepted standard, increase productivity (a key focus) and provide a better overall Services to customers. We wanted flexibility and a comprehensive solution for each operational model.
SELECTION, IMPLEMENTATION AND TRAINING
After analyzing several alternative Software Solutions in the aviation maintenance IT market and after careful evaluation we chose EmpowerMX because it matched all of our corporate objectives. EmpowerMX is a product designed by aviation maintenance professionals who support the technological solution with many years of experience: our interests were aligned and it would help Mexicana MRO Services to further improve its offer to customers. EmpowerMX’s solution offered us real-time communication between managers, finance and customers: customer Services is a key priority at Mexicana MRO Services and it has always been our philosophy that customers should feel that we are being transparent through every stage of an aircraft’s maintenance process in our facilities. We found all of this in the solution from EmpowerMX which has been designed for aviation maintenance; to drive operational efficiencies while maintaining the highest safety standards, and increasing productivity while providing a better overall Services to customers. It brings flexibility and comprehensiveness to each operational module.
EmpowerMX has provided the Technological Solution to consolidate Mexicana MRO Services’s place among the best-recognized MROs worldwide. We share the focus on Customer Services and, by using the new software, we will be able to improve the utilization of our workforce as well as provide real-time visibility to operators, management and customers. Additionally senior management will be able to view, in real-time, summaries of each invoice and work schedules.
For implementation, EmpowerMX configured the solution to work in accordance with industry best practices and with the customer’s way of doing business. For Mexicana MRO, implementation was broken down to a number of phases including:
- Initial preparations – data set-up;
- Configuration of the solution in accordance with Mexicana MRO’s goals and introducing proven industry best practices;
- Testing the configured design;
- Training for the user population;
- Go-live, supported by EmpowerMX;
- Expansion and deployment of additional features and enhancements.
The system went live on 25 February 2022 with the first job using the new solution being a C Check on a Boeing 767-300 freighter aircraft. Then, the go-live was rolled out throughout the facility and the organization – hangar and line maintenance – bay by bay, line by line, in order to minimize disruption and to better manage risk. After the go-live, EmpowerMX provided on-site support while the users learnt their way around the new ways of doing things. Once all of that had been established and approved, a training program was set-up to train the trainers across the organization to ensure that there is a strong group of people familiar with the system.
CHALLENGES ENCOUNTERED ON THE PROJECT
Training was a challenge where we had to prepare and create training courses to train the workforce across the organization in the new software. The solution is used by technicians, planners and commercial. In conjunction with EmpowerMX we have been able to train the workforce effectively by using our in-house training center and have trained the trainers in every part of the business who are presently training our operational workforce and who offered support during the implementation.
Covid-19 negatively affected the entire world and especially the aviation sector. The year 2020 was devastating as most airlines grounded their fleets as a result of travel restrictions and almost zero demand. In contrast, 2021 was a great year as most airlines began their ramp ups and required additional maintenance capacity to get fleets back in the air as soon as possible. Mexicana MRO Services benefited from this ramp up and we witnessed a shift in customers origins, migrating from a majority of customers coming from Latin America to where we are now with more than 55% of customers coming from the US and Western Europe.
The important thing with challenges is to be prepared. In order to guarantee access for the solution through the LAN and Wi-Fi network, as well as a solution that suits the working environment, we had to get the necessary devices in time for the implementation. Prior to having the system working, we made a plan in order to support ongoing projects where we had to be careful that every project could be managed on both old and new systems during the implementation. That was a challenge because everybody involved had to be conscious that they had to work with both systems for a while. But results at the time of writing suggest that implementation will take less time than expected, being achieved in six months starting in February 2022 and completing in July.
WORKING WITH THE NEW SOLUTION
One of the main characteristics of the Solution is the way all the modules are integrated allowing for a direct connection between the multiple areas participating in the maintenance, repair and Passenger-To-Freighter conversion processes. The processes include planning, execution, stores, supply chain, quality assurance and mobile interaction with the MRO customers.
The system allows:
- A significant improvement in the efficiency of all operations as it helps to quickly resolve risk factors through a better understanding of real-time maintenance execution and historical data;
- Having accurate visibility of all costs a quick and continuous way;
- Having remote interaction with customers, while offering them a real-time picture of the progress of their Services.
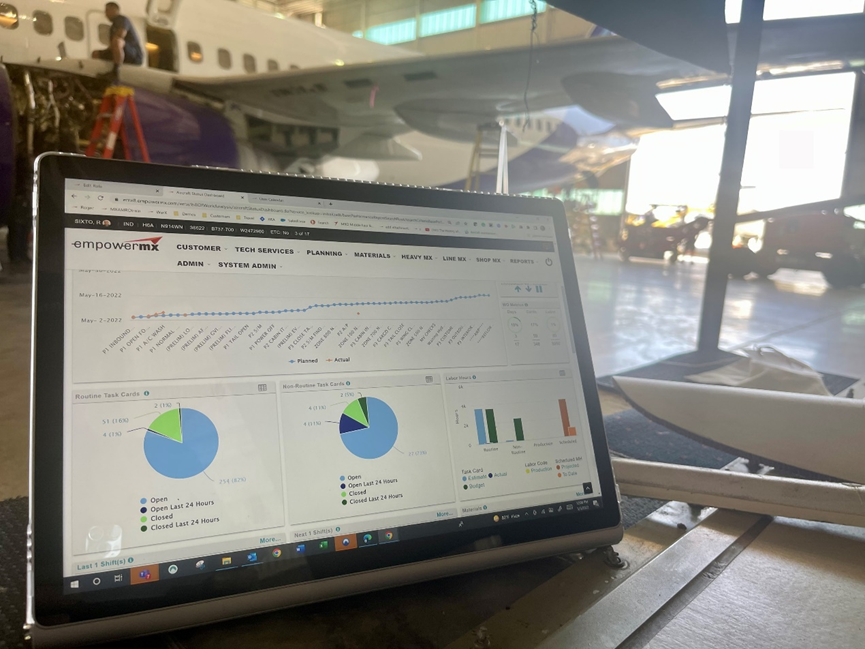
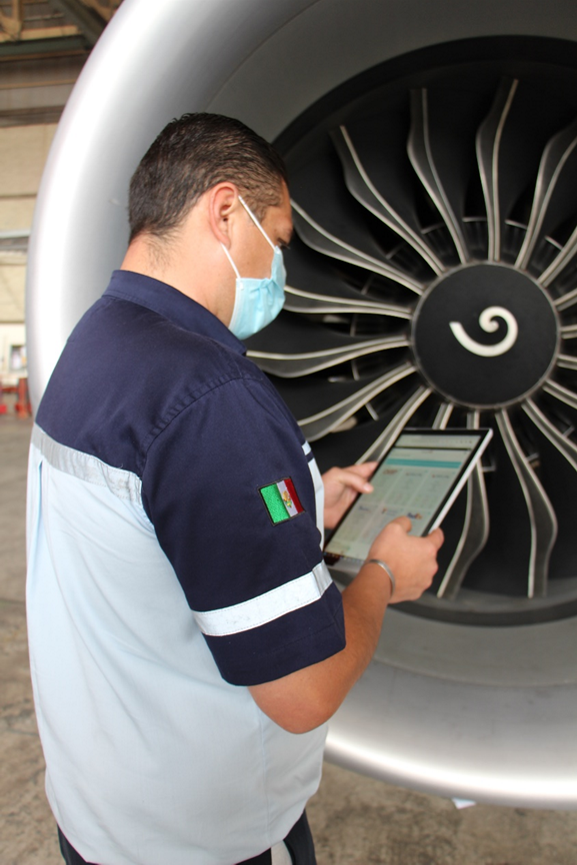
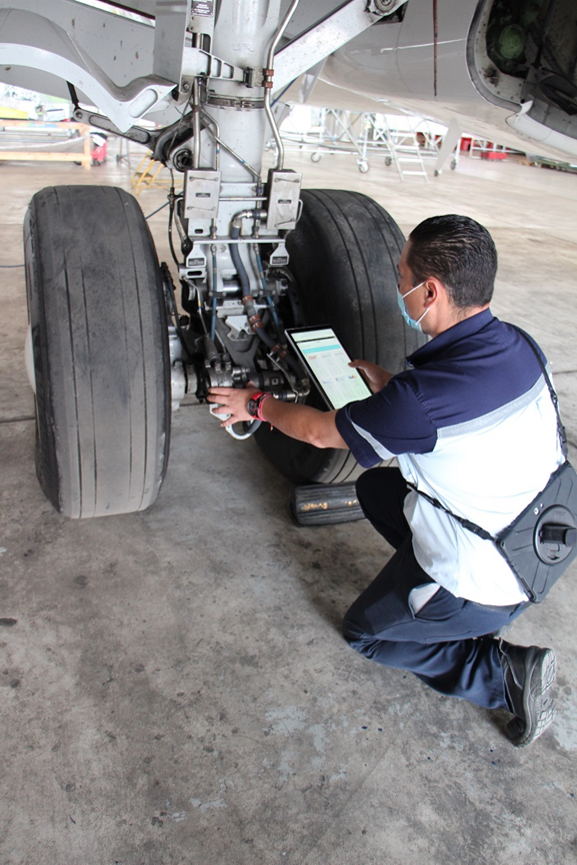
Mexicana MRO has moved away from multiple data silos to an integrated solution. We are no longer making decisions today based on yesterday’s data. All areas of the business are now interacting with each other in real-time. These include materials planning, technical procurement, shipping, receiving, and stores. The system also simplifies interactions with customers’ technical representatives. There is an automated workflow based on approval hierarchies. We can very easily monitor changes of status via notifications and now have total visibility of all parts requests, either coming from the hangar and shops or, also, requisitions for restock. The system allows tracking of orders via airway bills connected to the courier’s website. Materials can be traced through Customs, Initial Receiving, Inspection, binning and/or direct dispatch to Production. The extensive use of mobile bar code reading expedites the process.
We had to help some customers who were not familiar with the tool in the transition from the old to the new system but both the regulator and customers have accepted the new solution and Mexicana MRO is working with all customers with the aim to get every project onto the new solution.
The first Services performed with the new solution was a C check on a Boeing 767-300 Freighter at the end of February 2022 and that was a success.
APPROVAL FROM THE REGULATORS AND INTERNALLY
At the time of writing, the process of gaining approvals was still underway for electronic signatures but that has not hindered Mexicana MRO in using the system and benefitting from the extra efficiencies from using the new solution. The goal is to go fully electronic but there is a process that has to be gone through, Mexicana MRO has to demonstrate the business case for the change and then get the approval. In Mexico, that will be a simple process because EmpowerMX systems and electronic signatures are already approved for other MROs in the country. The other big regulator for Mexicana MRO, since they work on a lot of US registered aircraft, will be the FAA which will not be a problem either because some of Mexicana MRO’s customers such as Delta, also use EmpowerMX, making the FAA very familiar with the system.
BENEFITS FROM HAVING IMPLEMENTED EMPOWERMX AND NEXT STEPS
During this first execution we were able to confirm the benefits we expected. We were able to experience and document the following results:
- Keeping clear visibility of work progress and emerging risks;
- Accurate tracking of consumed labor hours by the different skills;
- Tight control of all the materials consumed during the execution of the work package;
- Easy access to part interchangeability information;
- Alerts of when materials are ready for delivery, decreasing idle wait times;
- Access to all this information from mobile devices pairing technicians to all the information and resources required for them to perform the maintenance activities.
We are satisfactorily slightly ahead of schedule and should finish 100% implementation of EmpowerMX in Mexicana MRO Services by August this year. Having started using the solution with a C check of a Boeing 767-300F in late February 2022 (see above), we are now implementing the new software on passenger to freighters conversions. Hopefully by August we will be completing the implementation with the Line Maintenance products. The plan will be to extend use of the new solution to all future projects, not only heavy checks but also for line maintenance and for conversions. We will also be interfacing the new system with other company systems such as accounting and export control in order to achieve a complete communication with all systems in use at Mexicana MRO Systems.
We realize that, for the future, IT will be an increasingly important part of Mexicana MRO Service’s business model in order to match the best of industry standards and gain benefits for customers.
THE EMPOWERMX SUITE
What EmpowerMX Suite does is to digitally perform planning and execution activities for maintenance businesses. The suite is built from a base of being able to plan effectively and digitally, and monitor that planning as it goes through the execution process to make sure that what was planned to be done is being done and how effective that is when compared with other similar checks. When things are done digitally, it’s easy to compare whether one check is performing better than another similar check so that the process can be immediately and continually improved.
This is the principle that EmpowerMX has been guided by from when the first generation of the solution was released eighteen years ago, and it has continuously evolved since then. At the outset, there were no other digital solutions whereas there are now a growing number of solutions that are closer to being digital but have often not been developed from a digital starting point. Some solutions take what they have developed previously (usually a paper-based solution) and made it digital as opposed to building a native digital solution from the start. In fact, EmpowerMX has had, in the past, to do the reverse of a digital conversion; enabling people to work with paper from a digital solution.
The contract
The different phases which a project would go through would be to start with the contract, which becomes digitized. So, taking an MRO such as Mexicana MRO, for example, which has a third-party contract with an airline, that contract becomes digitized so that while the work is being performed, any activities in that process are constantly monitored against the contract. There is no requirement for somebody to check whether something has been done when it should be done or that it’s been done within the terms of the contract because all of that is monitored automatically.
The work pack
From the starting point of the digitized contract, the solution moves on to the work pack which is also fully digitized. That means that for every work pack there will be a start time and an end time, the resources required, material required; all of the information needed for that work pack to be monitored digitally.
Once that has been done, then all of the information in the work pack needs also to be digitized because we’re still not working is a fully digitized environment which means that any information on paper has to be digitized which can be done through XML or an intelligent PDF converter (converting a PDF document to a digitized format).
With all task information digitized it’s then necessary to make sure that all of the material information is digitized by linking it into other materials systems to acquire the digitized information. The same would also apply to the tool information. Everything in the process has to be fully digitized to make it work. That’s where it becomes quite complex making paper work in a digitized environment, but it is a process that EmpowerMX has been handling for the past fifteen years or more.
The work order
Once all that information is digitized then it’s possible to execute the work order, which is the execution part of the process. The EmpowerMX solution is able to monitor that to make sure that it’s been completed in line with the plan, Once the planning and monitoring aspects are established, one of the key elements of the system is the Status Report that monitors everything down to that level of detail: every task has a start and finish time, all required materials are included as is the required tooling and making sure that the work process is being carried out as smoothly as possible.
Invoicing
The next stage is invoicing which, depending on the contract terms, can either be done as partial invoices or the system will capture all of the work that has been completed, so that no time is lost nor material that’s been added or any aspects: the whole extent of the contract is captured. There is no need for people to check that what was required has been done, it’s all completed in real time and digitally. One advantage of a digital contract is that, when invoicing, nothing is missed since humans are pretty much left out of the process. All through the process, the watchword is efficiency; through the flexibility and assignment of labor with all the information and data updated in real time, everybody involved has visibility of the process in real time and can plan against any potential risks either to the scheduled delivery time of the airplane or maybe some financial impact. Users of the solution report improved efficiency of between 15% and 30%.
That efficiency enables users to accumulate benefits such as departmental redundancy, no further need to store paper records.
Contributor’s Details
Enrique Guido
Mexicana MRO
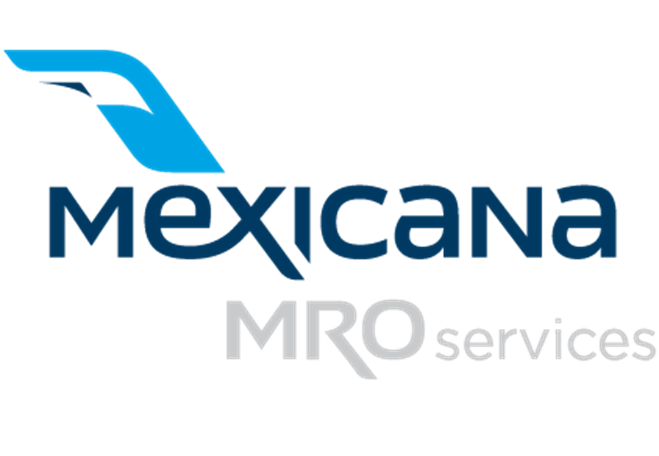
Mexicana MRO MRO Servicess offers Heavy Maintenance, Line Maintenance, Painting, Components Repair, Engineering and Training among other Servicess within the global aviation industry. Based in Mexico City International Airport, the company provides MRO and component support Servicess for Boeing 727, 737, 757, 767 as well as Fokker 100 and A320 aircraft. The company has workshops for repairs as well as for testing components, including avionics, seats and interiors, sheet metal, wheel and brakes, and aircraft weight and balance analysis.
EmpowerMX
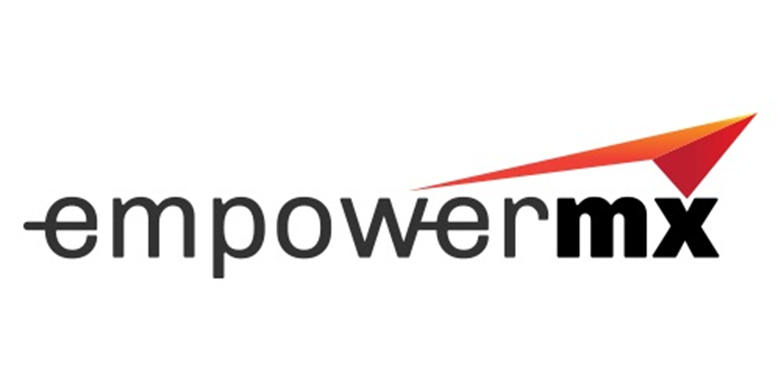
EmpowerMX is focused on equipping decision makers with reliable, real-time intelligence for minimizing maintenance turn times while maximizing airworthiness and profits. Airlines can jointly manage their outsourced and insourced activities like engineering reliability, QA and maintenance programs at the line, heavy and shop levels with an expected reduction in cycle times and increase in labor productivity on the magnitude of 16-30 percent. Third-party MROs can run their entire operation from bidding through contracting to invoicing.
Comments (0)
There are currently no comments about this article.
To post a comment, please login or subscribe.