Articles
Name | Author | |
---|---|---|
Case Study: Preparing to Implement an ETL / ELB at AeroLogic | Nils Oehlmann, Project Manager, AeroLogic | View article |
Long-term maintenance; who will secure the future? | James Elliott, Director of the MRO Product Line, IFS A&D | View article |
Case Study: Air Canada get an App for it | Keith Dugas, Manager of Excellence, Process & Technology, Air Canada | View article |
Case Study: The move to a Modern Maintenance Management System at Cape Air | Isaiah Herrick, IFS Maintenix Program Coordinator, Cape Air | View article |
Case Study: Air Canada get an App for it
Author: Keith Dugas, Manager of Excellence, Process & Technology, Air Canada
SubscribeAirline Case Study: Air Canada gets an App for it
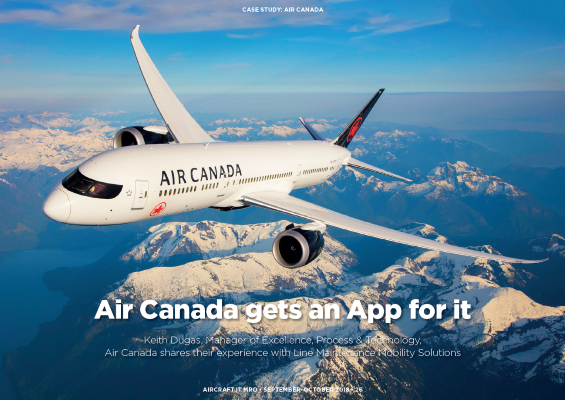
Keith Dugas, Manager of Excellence, Process & Technology, Air Canada shares their experience with Line Maintenance Mobility Solutions
To provide a little background on this article, let me explain my title and to what it refers. At Air Canada Maintenance, we started an Excellence 5.0 initiative which is our commitment to Air Canada becoming a 5-star maintenance organization. My responsibility within that organization is to help introduce technologies that will help us achieve that 5-star status. One of those enabling technologies is the Mobile Technician and that’s going to be the focus of this case study and article.
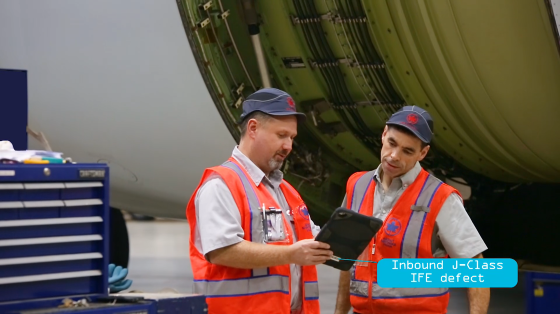
WHERE WE ARE PLANNING TO GO
Back in 2015, we knew that we had a long process ahead of us in trying to set this up. Trying to keep an organization of any decent size aligned to a common goal is a task in and of itself. So, about two years ago, we built a video to explain the path we planned to travel going forward. The video included what we were trying to achieve as it pertains to the connected aircraft and what we were trying to do within Air Canada and Air Canada Line Maintenance specifically. The video can be viewed below.
That video has been viewed throughout Air Canada Maintenance’s organization and it helps ensure that we maintain alignment to this program and to our common goal: to make sure that every new process introduced into our line maintenance environment will tie back into the connected aircraft and pit crew mentality that we’re trying to achieve.
As you will have seen, the video starts with Captain Jason Brown and sets out to show where Air Canada will be when we have reached the end state of the connected aircraft that is currently planned for maintenance. The electronic aircraft defect log in the flight deck will be the last stage, but the reason that the video runs from the technology implementation backwards is because we’re de-risking the different regulatory aspects of what it is to become a fully electronic and paperless organization. Like some other airlines with this issue, Air Canada is a relatively old airline with more than 80 years of history, which means more than 80 years of paper processes in our flight decks since inception. So, in order to transform all of a sudden or overnight, to a fully digital operation would have definitely incurred a lot of risk.
THE TIMELINE TO OUR GOAL
We started (Figure 1) in 2015 with getting project approval before moving on in 2016 to launch Surface tablets in our main warehouses. The reason we selected Surfaces was that, around 2015, a lot of airlines and a lot of developers had not yet chosen a specific platform for a mobile app. Air Canada was predominantly a Microsoft Windows based company and we knew we wanted mobility, but had yet to select a device of our own for our Aircraft Maintenance Engineers. However, we made the mistake of asking software developers to build device agnostic Apps. There are exceptions that are built intuitively but when a device agnostic App is built, the designer doesn’t always end up following any one of the three major standards – iOS, Android, or Windows. We asked for something device agnostic so that it could be put on any platform that we would choose later one, but again, the ease of access on something that is device agnostic isn’t always as good as something built natively for a specific device.
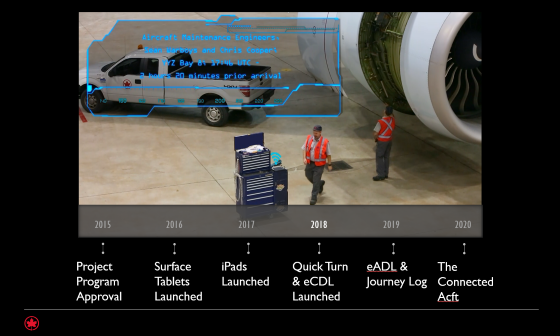
Figure 1
Notwithstanding all that, we launched Surface tablets for our warehouses, knowing that Trax had a platform built for Windows, and we started with that to gain traction on mobility. In 2017 we launched iPads to Air Canada Line Maintenance and, in 2018 we have launched the eMobility QuickTurn iOS App that is the focus of this case
HOW THE eMOBILITY QUICKTURN APP WORKS
One of the most integral parts of the video is where it shows technicians in the hangar undertaking an engine change, receiving the notification and having to go to change one of the IFE (In-Flight Entertainment) screens on an aircraft. We would not, of course, expect a technician to delay an engine change while he went to change an IFE screen; however, the point in the video is to demonstrate the ability that, once we’re fully connected and we have electronic logbooks at Air Canada, that when any defect is raised during a flight, it will connect through the aircrafts on board WiFi system, stream down to the ground and present a notification to a technician assigned to that location.
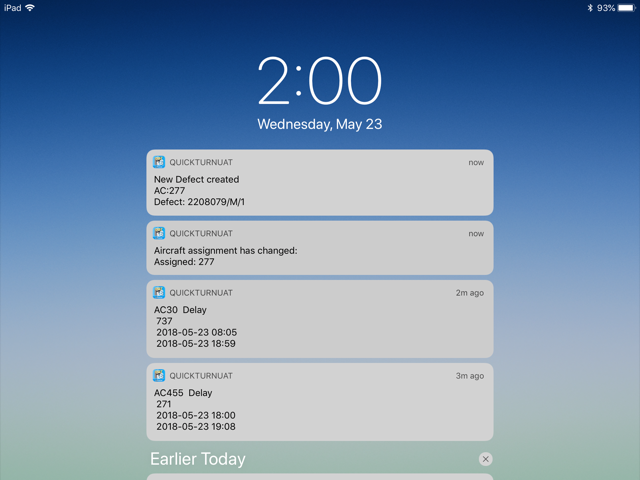
Defect notification
For example, right now this is our production region in version 2.0. Up at the top of the screen you can see YUL, Montreal, and the App is pulling in the entire flight schedule inbound to Montreal for the next 12 hours. It’s also generating a countdown to departure on the status column on the left and, if the user scrolls down, each bar represents its own flight, its own aircraft tail as well as, later on, displaying a countdown to Arrival. So, given that most events occur during the top of descent, an aircraft maintenance engineer will be able to calculate, based on the aircraft type and approximate altitude, that 45 – 25 minutes out they will have to start looking at the aircraft in the App to see whether there was anything reported during flight for which they might have been too busy to check the notification when it was sent.
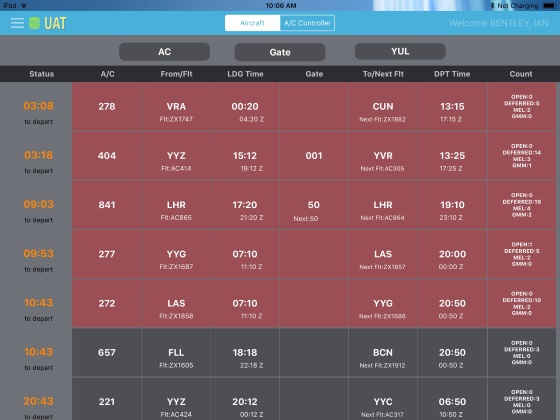
YUL Flights
Then they will select into the aircraft data and identify whatever additional issues need to be looked at. The App also identifies aircraft tail number (fin number in the USA), gives the flight it is arriving or arrived from, the landing time, the gate inbound and the next gate. It’s important to know the inbound gate but it’s also important for maintenance technicians to know the departure gate to identify if there will be a tow in between arrival and departure. The App gives the next station, the next flight that it’s going to, the departure time of that flight in local and in UTC and it gives a customizable count on defect statistics (e.g. defect status, MELs, etc.). One more thing, two different colors are used: gray identifies that there is nothing to be done on that aircraft prior to next flight. However, if an aircraft has an open defect or one set to expire, it will turn red. The same goes if there is a monitor on the aircraft where it has a repeat cycle of one, or greater that will expire today, then it will also identify itself in red; This is in an effort to ensure that Air Canada’s line maintenance technicians don’t have to scroll through an entire list to identify what they have to action, they just look into the ones that are red.
Another threshold that we set was that we don’t want to see all defects since the concept of the app is to turn aircraft quicker, for instance, we don’t need to see the defects that are deferred to a heavy check. So, Air Canada has elected to define the App to deliver all defects that have an expiration date from 0 to 120 days out.
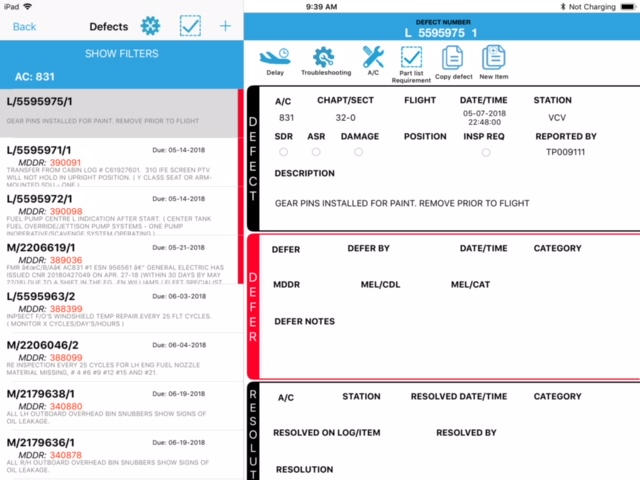
AC details and highlighted defects
One of the core things that we do at some of our bigger stations is that the system will assign specific technicians to specific tails. So, a technician or supervisor might assign him or herself to tail 691, 648 and 806. The App will then give the technician just their assigned list and it will give notifications just for that aircraft type. Plus, once anything does occur in flight, that assigned technician will get the notification for that fin. So, for example, some of the notifications that come in will just pop into the technician’s normal iOS messaging center where the notification comes up, they click on it and that takes them back into the App. But, let’s say they are in one of those stations where tails are assigned and, all of a sudden, something happens on the aircraft at the gate next to them, but they’re not assigned to it, and it’s not in their window, there’s another view called AC Controller, a toggle view which, when clicked on, has the ability to search for whatever particular tail it is that is affected. So, if we look at one of the 787s, it will bring the technician straight into that aircraft: whether or not they are assigned to it, the technician can still access the aircraft defects through the App and get all the information. It can be done in a controlled manner or can be used ad hoc for any aircraft type that a technician needs to address. Also, if nothing is assigned, the technician gets everything.
There’s also some additional functionality where a station can be changed giving the ability and flexibility to send Air Canada technicians on out-of-town assignments so it isn’t necessary for a technician to be limited to the view of only that station that they’re defined for but can select onto any other station assigned as well.
CONNECTIVITY, WORKING OFFLINE AND DELVING DEEPER INTO THE DEFECT
One of the core things we asked Trax to do was to make sure that we had full connectivity all the time, and that we don’t drop work when connectivity is lost. So thankfully, they built the App for us to be able to work in offline mode. One of the core reasons for this was that we operate the Boeing 787, which is basically a flying Faraday cage. Also, other aircraft can have poor connectivity in different areas but we didn’t want our technicians to lose the ability to have visibility of anything occurring on that aircraft or lose the ability to record anything in real-time. That’s why we made sure that they built in the capacity to work offline. While the App is in offline mode, it caches all the data and then, once there’s a connection available, it automatically uploads all the data. It’s really seamless and really straightforward.
There is also an option to go further into aircraft data and identify if there are any planned work orders schedules for the downtime. The App looks at the turns during the day and looks to see whether the planning department has planned any work orders to that aircraft for whatever event. The App gives the work order priority, the work order description and the scheduled start and end date. It also gives some additional KPIs and measurements; if the user clicks on the defect tab, it will retrieve a list of all the defects, and, if they select that, it will take the user into the defect list itself.
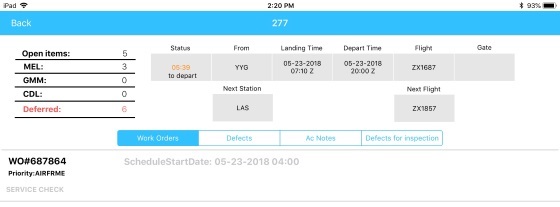
Check AC for WOs
Once the user selects into the aircraft they have the ability to create a new defect, by clicking a ‘+’ sign on the screen, they have the ability to select all the different features available to them in the list itself, upload a photo, type in the defect description or, just as easily, enable ‘dictation’ and read out loud that defect’s description, save it and, as soon as that record is saved, it automatically will, if connected, upload to Trax, Air Canada’s M&E solution. If, having created a defect, it is necessary to dispatch the aircraft, the technician can go into the App and defer that defect. If it was raised inbound to the technician and they did a one-time fix, they can then go in and resolve it.
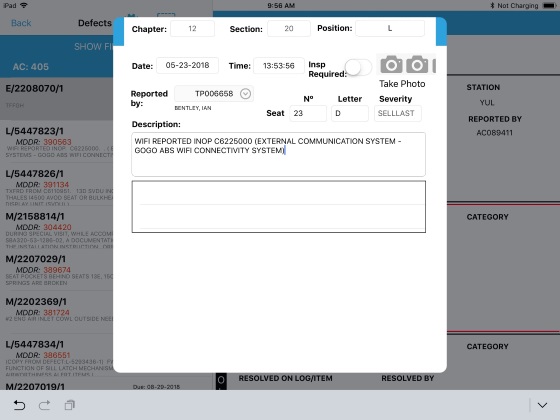
Create new defect
One of the core things that Air Canada technicians do when there is not enough time to resolve something is enter any trouble-shooting information and/or view historical trouble-shooting information. It’s also possible to record install and removals of components with the ability to take photos,
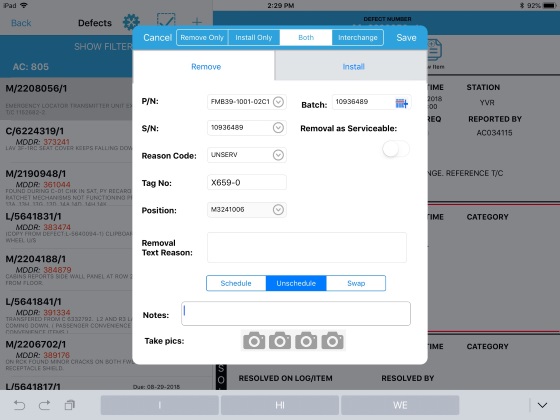
Install Remove components
AUTOMATION
We also wanted to automate as much as we could and take as much information as possible back in from the system; so, we’ve included the ability to scan our part labels that have a barcode, so the App will automatically input all the information to the part that is being installed or removed. Plus, there is the ability to add parts to a defect; so, whatever part might be required to fix the aircraft, the App will go into the Trax M&E system and identify whether that part is available or not: if it is available it gives the technician the ability to picklist the part which will automatically go to the warehouse for them to supply it: if not available, it gives the technician the immediate ability to create a requisition which will trigger our supply chain to supply the part.
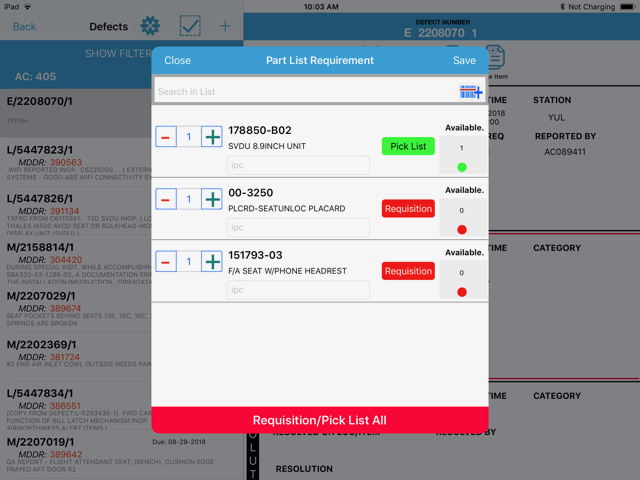
Parts availability
At Air Canada, there are still paper logs: so when we transfer defects from one paper log to the next, we wanted the ability to copy defects over. This has also been incorporated into the app. Also, when it’s necessary to create a new item, the user can click on a new item with the ability to create an ‘item 2’. The App automatically pre-populates all the information from item 1, creates it as defect item 2 and then the technician can just change whatever information is required in line 2.
SUMMARY
We have just covered the majority of the functionality in the QuickTurn App, one of the core tools that will help get Air Canada to become a 5-star line maintenance organization. It will allow us to not have to disembark the aircraft to go down to our ready rooms to do our transactions in our Trax M&E system because, with mobility, we’ll have it in our hands in real-time, right away, and not have to take any delays just to respond to a defect.
Contributor’s Details
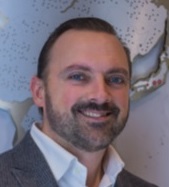
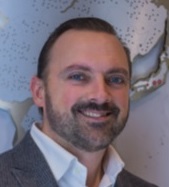
Keith Dugas
Keith has worked for Air Canada for 10 years, starting as an expediter on the AOG desk, then moving to operations manager for the AOG desk. Following that he was responsible as a business lead in supply chain to transition from Air Canada’s legacy maintenance system to Trax where after a successful deployment he became Manager of Continuous Improvement for Logistics and Operations. Today he is in the Excellence 5.0 team as Manager of Excellence, Process & Technology, leading several projects.
Air Canada
Air Canada is Canada’s flag carrier, and largest domestic and international airline serving more than 200 airports on six continents. It is among the 20 largest airlines in the world serving over 48 million customers each year with a fleet capacity of more than 390 aircraft, one of the youngest, most fuel efficient and environmentally friendly in the world. It includes, Boeing 737, 767, 777 and 787 types; Airbus A319, A320, A321 and A330; Embraer 175 and 190; and Bombardier CRJ, Q400 and Dash 8
Comments (0)
There are currently no comments about this article.
To post a comment, please login or subscribe.