Articles
Name | Author | |
---|---|---|
Case Study: MATMen – In-House Solution for Supply Chain Optimization | Petr Barton, Inventory Manager, Travel Service a.s. | View article |
Case Study: A digital future for Air Evac | Tammie Bethel, Records Specialist, Air Evac | View article |
Case Study: Achieving a Continuous Compliance Culture at Southwest Airlines | Don Tilden, Director of Central Publications, Southwest Airlines and John Zawlocki, Fleet Solution Manager, Flatirons Solutions | View article |
Case Study: A digital future for Air Evac
Author: Tammie Bethel, Records Specialist, Air Evac
SubscribeA digital future for Air Evac
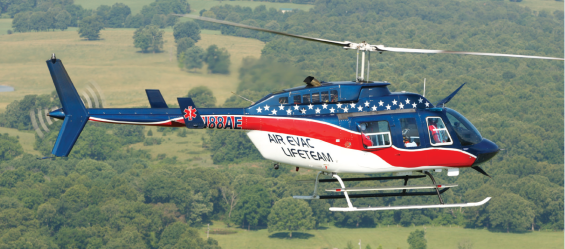
Tammie Bethel, Records Specialist, Air Evac shares a decade of growth propelled by NextGen M&E MRO IT
Air Evac is one of the largest Air Medical operators in the USA and is, in turn, part of a larger holding group, Air Medical Group Holdings (AMGH) based in Dallas, Texas with, collectively, nearly 300 aircraft. The Ramco solution has been implemented across the whole group, including Air Evac which accounts for more than 150 aircraft. This article, in six parts, shares key points from the journey that Air Evac has travelled with their IT solution during the last ten years: The Air Evac growth journey; HEMS industry challenges; Identifying business pain points and key needs; choosing the right technology partner; where Air Evac is today in terms of business benefit realization; and Air Evac’s digital mobile ecosystem strategy.
THE AIR EVAC GROWTH JOURNEY
Air Evac Lifeteam was established in 1985 by a group of citizens in West Plains, Missouri. The goal was to provide air medical transportation and ensure access to emergency health care facilities for their remote community in the Missouri Ozark region. Although air ambulances were primarily based in metropolitan areas at the time, the company founders believed that the people who needed air medical transport the most were those living in rural communities, often far away from a hospital or major trauma center. Today, Air Evac Lifeteam is the largest independently owned and operated membership-supported air ambulance service in the United States, with more than 125 bases across 15 states from which Air Evac flies more than 70,000 flying hours a year for 40,000 transports, also annually. It all drives more than 50,000 maintenance transactions each year inside the maintenance system. Air Evac first implemented a Ramco solution in 2007 with version 4.0, transitioning in 2014 to version 5.6 and currently using version 5.8.
HEMS INDUSTRY CHALLENGES
One challenge with which any operator will be familiar is regulations. But there are also a number of other challenges for a HEMS (Helicopter Emergency Medical Service) operator working across a large geographical area (figure 1).
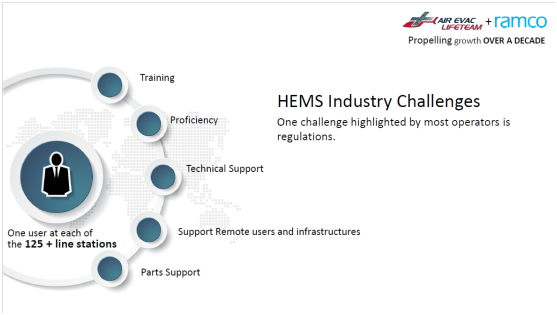
Figure 1
Training and proficiency are a clear challenge and can be considered together. As we’ve already mentioned, Air Evac has more than 125 bases in 15 states scattered across the country and usually more than 100 miles apart. There are a lot of mechanics who are working by themselves and, of course, it’s very important to maintain their levels of training: the Ramco solution used at Air Evac has the ability, to get training information to where it’s needed and keep people in the business up to date on changes.
Another challenge is that of technical support. Air Evac has a Control Center manned 24/7 because there are mechanics out at the bases, often alone. If they have technology issues, something with which they need help, they can call into the headquarters to get the information they need, get help finding it and move tasks forward. Support for remote users and infrastructures are a further challenge along with parts support; getting information out to people who need it in order to give them the ability to get parts ordered fast in the system: create orders which are sent out as quickly as possible. Another desk manned 24/7 is the AOG desk to deal with aircraft on ground situations. So, if something is needed very quickly, the mechanic can call that desk and, as soon as they put in the MR (Material Request) for that part, the AOG desk can start looking through the system to see what it has and what is needed, identify in the system the nearest one to the station that needs it and get it transported to them in order to keep the aircraft in the air.
IDENTIFYING BUSINESS PAIN POINTS AND KEY NEEDS
Engineering orders
As any reader will understand, with aircraft there’s always going to be a lot of ADs (Airworthiness Directives), CEBs (Commercial Engine Bulletins) and ASBs (Advisory Service Bulletins) being issued. Air Evac also issues a lot of Maintenance Information Letters (MILs) on its own fleet, things that need to be done with aircraft. We use a part of the Ramco system called Engineering Orders which we implemented a couple of years ago. It’s a great time saver that allows users to go in, create the EO (Engineering Order) for the task and, once the task is started, there’s no need to leave the screen: the user just names the task and decides whether it’s for a component or an aircraft from where the system takes the user right in to what the task is effective to. So, for instance, if it’s effective to an aircraft, there is the option to pull it in by model (right now Air Evac has three models: the Bell 206, the Bell 407 and Airbus Helicopters’ 350s) or by ‘multi’, i.e. the fleet. Once that has been pulled in the user can search the component number, the part number or aircraft model and there is a tab to mark whether the task is effective for that model. Once that has been done, the user can go to the next screen that allows the user to set the schedule for that task without having to go into a different system; and it can be date based or flight hours based. The user simply sets their times and gets the task running. A lot of ADs in Air Evac will include multiple tasks so, still on the same screen, a further task can be created in addition to the one already running. Tasks can be recurring or one-off or sequential, i.e. when one is complete the next one can start. It’s also possible to pull parts in, decide whether they are serial based or whether they should be in the parts program or aircraft program. Still not leaving the screen, the next step can be to initialize the schedules, set it up to be running on those parts or those aircraft. The system makes it easy: once the screen is open, the user can export it, fill in the times, bring it back in and release it to all the fleet simultaneously with the further ability to then check that everything is running correctly.
The other thing that was a compliance problem for Air Evac was being able to pull information up and look at it. There was a compliance status report in the Engineering Orders and that was being used a lot for MIL’s (Maintenance Information Letters) by internal staff. If management wants to know what’s going on with a particular project running on an EO on an aircraft, all they need to do is go to the compliance screen and enter the EO number which offers the option of looking for what’s pending or what’s closed. That information can be pulled into an exported Excel sheet to be sent to management who can use it for whatever data work they want. In short, what the users sees is exactly what is running and using one screen offers time savings as opposed to having to move to several areas.
Enhancement of Inventory Management
Air Evac finds this useful because it helps decrease turn time which leads to an increased number of turns while reducing the inventory for LRUs (line replaceable units). When an aircraft is out for maintenance, as soon as the maintenance controller removes a part that is automatically transferred to Air Evac’s ‘unserviceable’ warehouse until the next morning when the repair people come in and pull their reports that show them everything that was on the aircraft’s maintenance form – every discrepancy, every component removal. They then see what parts are available at the RMOs (Regional Maintenance Office’s) to be sent back. Those parts used to sit there for two to three weeks while Air Evac was waiting for paperwork to be submitted from the RMOs to say what parts had been removed. Now, it’s an automatic function, it’s seen the next morning and a repair order can be raised and emailed to the RMO so that the parts can be shipped out that same day which gets them to the repair facility for their overhauls with faster inspections before being returned to Air Evac and put back in the system. That has reduced the number of major components that have to be held in stock because the circulation of parts through the repair system is so much faster to get the stock back in which has reduced the number of line replaceable units that Air Evac needs to keep in stock.
Facility Objects
Up until about a year ago, Air Evac was manually tracking all calibrated tools held in the field which made it difficult to keep up with what was out there and when they were due back in for a yearly calibration. In our new system is a capability called ‘Facility Objects’ which allows users to track all of their tools and helmets because they have a 12 month inspection that is required. All of those are tracked through the system which gives the user visibility across the company of what is held at each location. Each location has their own warehouse for their tools and their helmets. So, at any time, across the company it’s possible to see what is held at each warehouse, when it’s due and how many haven’t been completed. That has allowed us to cut down on mis-calibrations, we no longer have the FAA coming in and pointing out that we have a tool out of calibration. Air Evac knows a month or so ahead of the time for recalibration and notifies the bases to make sure that their tools are in as well as send them a new one before the old one has to go out. This has made tool management so much easier.
There’s also a facility called ‘Objects Due Report’ that can be pulled up: Air Evac does that about one month ahead of time for the tools to notify everybody of what is coming due, when it’s due and where it needs to go. This same report will be pulled every month for helmets so the mechanics can coordinate with the pilots and crew members to get the helmet inspections done on time.
Records storage
Another pain point was records storage and the new solution provides the ability to electronically store records. This has allowed Air Evac more visibility anywhere in the company, at any location to see records. Mechanics now have the ability to go into the system and find things that they need. Because Air Evac is across 15 states, it’s not as if they can just go down to the records room and see what there is. They can go into the system and open aircraft maintenance records, component records, repair orders, quotes, goods receipts… any paper records are put into the system so that users no longer have to go to the filing cabinet and dig back through as much as two or three years’ of paperwork to find parts.
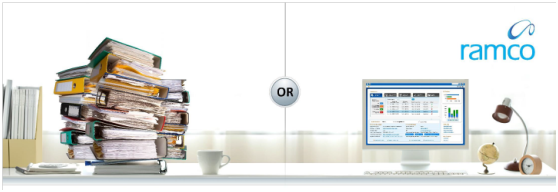
That’s being used for the facility objects: we upload every calibration paper that’s returned on a calibrated tool; we also upload every helmet inspection form. A recent implementation has been the employee training information in the HMRS section of Ramco (the employee information section), for every mechanic and pilot Air Evac has their licenses uploaded, details of any factory training they have received, their IAs (Inspection Authorizations) are uploaded and their A&Ps (Airframe and Powerplant) are uploaded so management has access to all their licenses with one click: it’s possible to call up a report with license information and everything needed on mechanics and pilots. This has taken away a lot of paperwork such as with component records: every time a component comes in, we upload every piece of paperwork for each individual component so we can go back to the last overhaul and have that information to hand.
CHOOSING THE RIGHT TECHNOLOGY PARTNER
One of the things that we like about Ramco is the security of having to log in. We also like how the solution has the ability to create roles, i.e. we can limit the role of, say, a filed mechanic to just the projects and items that he needs to do in the system. So, when he opens his screen, he has only his few areas that he needs to go into and work in and, because the content to which he has access is linked to his role, when he needs information, he doesn’t need to scroll through reams of information that he doesn’t require in order to reach the information that he does require.
A particular plus point for Air Evac is that the solution we have chosen is fully integrated: maintenance, purchasing, inventory, facility objects, and repair tracking… it’s all together. So, whenever maintenance order is raised, the order is immediately available to Purchasing on their screens; the order gets sent, vendors confirm and, as soon as the item is delivered, it appears in inventory facilities in a fast moving process which has enabled Air Evac to keep a tighter track of the inventory as well.
Another reason for our choice is the Enhanced Reporting capability which we call our decision works and which is very popular in Air Evac because it’s an area where users can create their own reports as opposed to having to pass that job to a technical person or two to get it done. With this solution, users can go into the system, take a report and make it fit for their purposes using just the information that they want to extract from the system. Ramco still gets asked to make reports when we’re looking for something a little more complex. One of the reports that Air Evac uses a lot is ‘Aircraft Status: Time Remaining’.
Because the Ramco solution uses web based access, it’s accessible from anywhere there is a computer which enables users to manage from where they are located; work, home, etc. That’s important in a business spread across fifteen states. Air Evac also appreciated the improved tracking and controls that enables maintenance to be managed from anywhere, offers better tracking of upcoming maintenance events and schedules across the fleet. Looking at our Aircraft Status: Time Remaining report (see above), mechanics can pull up that report and can plan for the next group coming in. We used to take aircraft out quite a bit for maintenance but, because of our enhanced reporting we’re now down to sending them to the major locations for every 300 hours flying time; otherwise, the only time they leave base is for an emergency or for a very short time out of service. That has allowed us to work out the best times to bring aircraft in in small groups while keeping the fleet flying.
Finally, the solution that we now use at Air Evac is expandable to match business growth so that, as Air Evac has grown, the solution has grown with us.
WHERE AIR EVAC IS TODAY IN TERMS OF BUSINESS BENEFIT REALIZATION
Multiple Operating Units
As we’ve already mentioned above, Air Evac Lifeteam is part of the larger AirMedical Holdings Group, AMG Edge with other group entities including Med-Trans, EagleMed and Reach Air Medical Services with a group total of nearly 300 aircraft. The whole group has one software package and one installation that can be modelled in each use case to serve multiple entities. In this group, the different entities work pretty much independently from an operating model perspective. So, modelling is a single installation using the concept of organizational units with the nuances for each of these entities retained in that model; at the same time the whole business needs to be able to view across these entities for things like inventory information which can be provided across the group. Also, if the holding group wants to roll up the finance across these entities, that can be done to achieve visibility whilst still retaining the nuances of each entity. Plus there is a reduced cost of ownership for the software when installed across a group such as this. Furthermore, when any new companies are acquired, the solution can be scaled horizontally and vertically to accommodate that additional entity.
One case where this has proved useful is where there might be an aircraft out of service or needing a major part. Group operating units can share views across all four companies and look at their stock of parts and components. Instead of simply going out and spending thousands or tens of thousands of dollars on a major part, operating units can see what stock their sister companies hold and work together to make exchanges which has proved a big cost saver.
Decrease in spare inventory
This has been very helpful with AOGs (aircraft on ground) allowing users to see what there is in inventory across the whole fleet so that the business does not need to keep such high value stock and has been able to reduce inventory values.
Technical records tracking
When a part comes in from repair, the first person to deal with it will be someone in inventory; so, as they bring it in, they look at the 8130s, check the times on the part when they come in and what maintenance programs it related to. But, before they release that part to the fleet they put it in ‘pending status’. The system then sends an email to the records department who conduct a deep dive on that part, double check the 8130 and the component maintenance program to make sure everything is running correctly, that the times look right, that nothing has been missed. They’ll then upload all the records. When Records says that everything is good, the record is verified and only then is the part or component released to the fleet. That function alone has saved group businesses a lot of down time. Before this was started, parts would be brought in because inventory people didn’t always know what they were looking for: we would go to put a part on and there wouldn’t be the correct paperwork or something would be missing or the part number would be wrong. So then we had to spend hours digging and searching in order to get the aircraft back into service. This new solution has allowed us to make sure that the parts we need are up and ready before it ever reaches the aircraft – a real time saver.
Maintenance cost reduction
The enhanced maintenance forecasting with improved inventory tracking is where the Aircraft Status: Time Remaining report comes in. Our RMM’s (Regional Maintenance Managers) run this which allows them to see what’s coming due on that aircraft which, in turn, has allowed Air Evac to calculate the exact time to bring those aircraft in for their big maintenance event, at 300 hours. It has also helped Air Evac to use timed parts a lot closer to their full life limit by running this report because it tells us how much the aircraft is flying and what its utilization time is. All that information can be used to work out; how long the aircraft has been flying so how much time is left on the part. If the aircraft is flying this many days a week, the maintenance planners know exactly when to bring it in and Air Evac is not losing as much time on the part as used to be the case which is also a big money saver.
Simplified budgeting
This follows on from the maintenance cost reductions because our budget team is able to pull up those same reports and plan for a year ahead to what will be due with respect to major components such as engines. That has, among other things, reduced the outlay on engines (an expensive component) because Air Evac is now able to push those right out until their specified time rather than taking them off the aircraft long before they’re due.
DIGITAL MOBILE ECOSYSTEM STRATEGY
Digital signatures
One key part of this is the digital signature which has already been tested at Air Evac where we are now in the final stages of implementing it. The system will use dual authentication to meet regulatory requirements. Ramco has worked with Air Evac on this to meet their very specific FAA requirements. The screen (figure 2) is what the mechanic would see the first time they use digital signature.
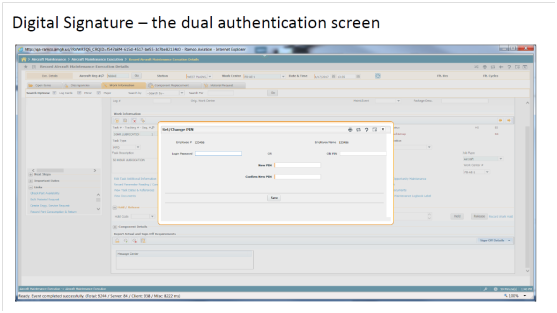
Figure 2
The digital signature will be set-up for the mechanics when they are brought into the system. As soon as they complete their next task, they’ll see this screen for the first time where they’ll put in their password before creating a new one and confirming it. They’ll then sign the task off with their employee number, their A&P license and a date. The reason that’s important is that at Air Evac’s RMOs there are thirty or so mechanics at one time. There might be five or six mechanics working on one aircraft. The FAA wants to know which mechanic did which task. Prior to digital signatures, the mechanics would manually sign off the tasks they completed on a printed out work order before scanning or manually uploading them. They will now add all employees that worked on a task in the Execution Comments in Ramco and one mechanic from the group will sign it off electronically in the system. This is going to eliminate the manual work order paperwork which will be a big time saver for the mechanics.
The other thing that digital signatures facilitate is that, if the inspector determines that the job needs to be looked at again or doesn’t agree with the discrepancy as written out, as soon as he registers that decision, it wipes the signature off so that the mechanic has to re-sign the task after the revised or additional work has been completed. Then, once again, the inspector will go into the system to re-sign it off. Once the inspector has signed it off, it’s completed as done and will also show the Inspector’s AMP number and his information just as it does the mechanic’s.
Mobile solutions Anywhere
At the time of writing, Air Evac was in the process of going live with Mechanic Anywhere and Warehouse Anywhere to be tested in the month following with end-user training scheduled. Mechanic Anywhere will allow users out in the field to work on an aircraft even where it has been landed away from any base (say in a field) as if they were in the engineering hangar. All it will need is the iPad in the aircraft for the mechanic to be able to use the system as if he were back at base. Warehouse anywhere was scheduled for implementation at the same time and will also allow users to undertake inventory transactions on mobile devices. So they’ll be able to take their mobile phone to undertake cycle counts from the floor, or the transfer of a part from the floor and see exactly what they have on the shelf. Air Evac also wants to implement barcoding on parts so that mechanics can take their phone, scan the parts, see how many of those parts are in their system or how many might be available from other systems and what other warehouses have that part.
Those are some of the things that we’ve recently implemented at Air Evac with digital signatures which had gone live in 2017 and in the future, we’re looking forward to get rid of the paper logbooks on the aircraft to go wholly electronic with those through the system.
Contributor’s Details
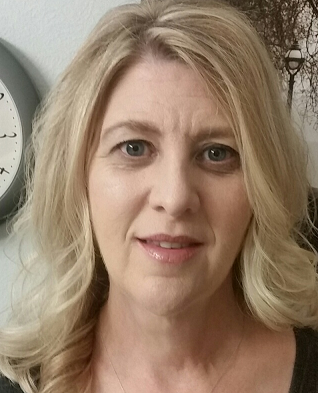
Tammie Bethel is a records specialist in the Maintenance Department at Air Evac Lifeteam’s corporate office. Prior to joining Air Evac Lifeteam in October 2007, Tammie and her husband, Gary, owned and operated a Radio Shack store. In Air Evac, Tammie creates and maintains the task for aircraft maintenance tracking in Ramco. She has helped implement the use of the EO’s for tracking of specific aircraft compliances and has also help implement the use of Facility Objects to track the tools and pilot helmets in Ramco.
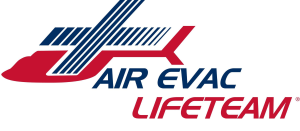
Air Evac currently operates helicopters at 131 bases, covering most of the central and southern states in the USA. While primarily a HEMS provider, they do operate 2 fixed-wing aircraft in Missouri and Kentucky. Today, Air Evac Lifeteam is the largest independently owned and operated membership-supported air ambulance service in the United States, and owns and operates around 140 Bell 206 L1+ Long Ranger helicopters and about a dozen Bell 407 helicopters.
Designed to be accessible on cloud and mobile, Ramco Aviation Software continues to add technological innovations with ‘Anywhere Apps’, redefining the power of Mobility, to significantly reduce transaction time both during AOG conditions and critical aircraft turnarounds. The software helps aviation companies ensure zero tolerance to error, with higher safety standards.
Comments (0)
There are currently no comments about this article.
To post a comment, please login or subscribe.